Two storage and retrieval machines in one aisle
The agricultural machinery manufacturer AGROSTROJ has increased its handling capacity and storage capacity in a forward-looking manner by adding a fourth STOPA sheet metal storage system, in whose aisle two storage and retrieval machines operate. The system’s loading stations also work efficiently, with their turntables providing the sheets in a space-saving manner, so that a larger number of laser cutting machines can be connected.
Miloš Křenek, engineering director of AGROSTROJ Pelhřimov, a.s., Pelhřimov (Czech Republic), which was founded in 1896, presents a film about the use of combine harvesters and other harvesting machines. “These so-called in-house products account for around ten percent of our turnover. The majority of the parts that we manufacture and export (98 percent) are components for international cooperation partners.” These include other manufacturers of agricultural technology, but also companies that build trucks, buses, mobile cranes, forklift trucks, construction and road-building machinery, as well as wind turbines.
Increasing material handling
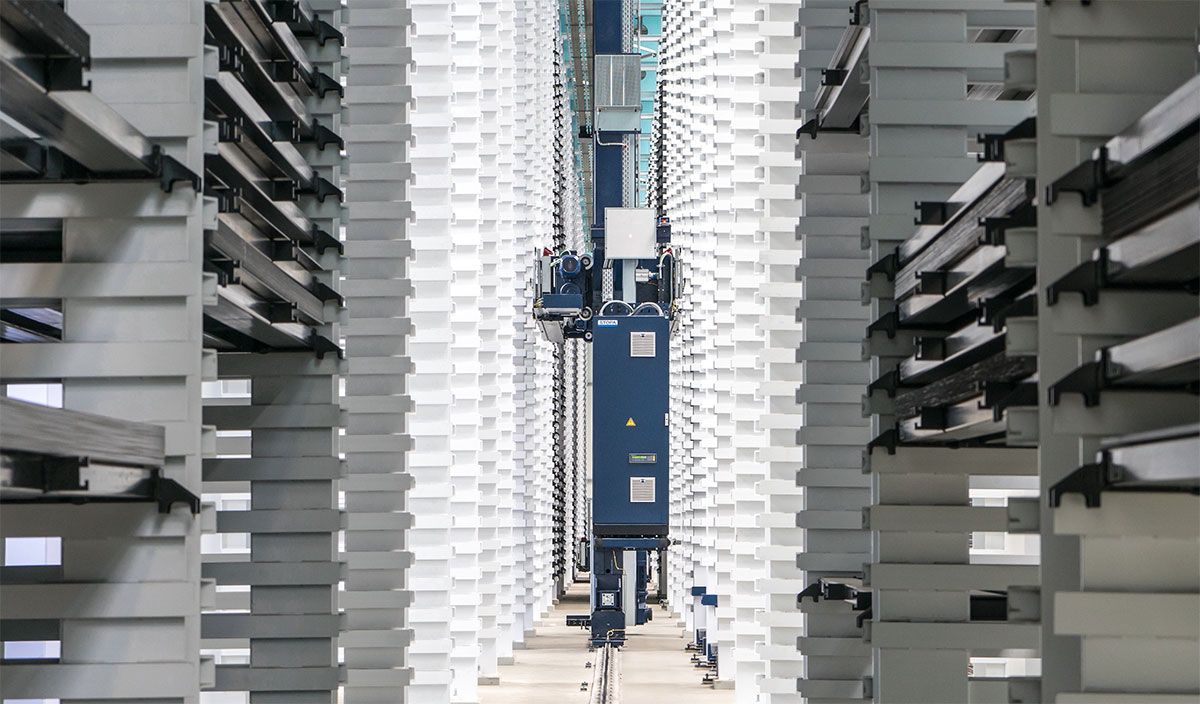
STOPA makes a significant contribution to performance with its concept of two storage and retrieval machines that run in one aisle of the warehouse at the same time
During a tour of the production halls, four automatic sheet metal storage systems stand out, all of which come from STOPA Anlagenbau GmbH, Achern-Gamshurst. Křenek stops in front of the STOPA COMPACT II, an automatic storage system of the latest generation. “We invested in this fourth storage system to expand our storage capacity and increase material handling from around 50,000 to 80,000 to 90,000 tons per year.”
The manufacturer makes a significant contribution to performance with the concept of two storage and retrieval machines (SRMs) that run in one aisle of the warehouse at the same time. This solution also stands for greater flexibility and process reliability. The SRMs process their orders independently of each other. Both storage and retrieval machines can access almost all 2,606 storage locations of the STOPA COMPACT II, which is around 108 meters long, 11 meters high and 5.5 meters wide. The outer 55 storage blocks, which are arranged in two rows, are the exception, as only one of the storage and retrieval machines can reach them at each end of the aisle. The high performance is also due to the speeds of the storage and retrieval machines, which can travel 150 meters per minute, pull 20 meters and lift 23 meters.
Křenek unfolds a drawing showing the new warehouse and six laser cutting machines. “Since the warehouse has to supply ten machines with sheet metal plates in the final expansion stage, STOPA has proposed the use of two storage and retrieval machines. This solution has almost doubled the performance of the system. In addition, redundancy has been created so that the associated machines can process their orders without downtime.” The warehouse thus fully meets the requirements of the operator, who will connect only TRUMPF high-end flatbed lasers with high axis speed and positioning dynamics and therefore wants to avoid unproductive waiting times.
Highlights of the solution
- With a fourth STOPA sheet metal storage system, in whose aisle two storage and retrieval machines run, AGROSTROJ has sustainably increased its handling capacity and storage capacity.
- A larger number of laser cutting machines can be connected thanks to the turntables on the transport trolleys at the loading stations, which provide the sheets in a space-saving manner.
- At the same time, the operator benefits from greater flexibility and process reliability.
- In addition, redundancy has been created so that the connected machines can process their orders without downtime.
More process reliability
The STOPA COMPACT II, a further development of the STOPA COMPACT, which has proven itself in many applications, offers even better space utilization and an even greater number of storage locations for the same storage volume compared to its predecessor. In addition, AGROSTROJ benefits from greater process reliability and minimal wear. This is due, among other things, to the fact that the metal sheets cannot slip due to the smoother running of the flat pallets. If the company, which is certified according to ISO 9001:2008 and ISO 14001:2004, employs more than 2,000 people and produces on an area of 210,000 square meters, wants to further increase its process reliability, it can adjust the speed and acceleration values individually or material-specifically.
The system’s intelligent energy management offers significant economic advantages. For example, regenerative energy that is generated when the crossbeam is lowered can be used directly for the drive motor by means of an intermediate circuit coupling. To save even more energy, the manufacturer uses a more compact crossbeam and two powerful, lightweight gear motors instead of a heavy drive motor, which reduces the overall weight by about half a ton. Furthermore, the STOPA COMPACT II enables more productive cycles per shift due to its significantly shorter weighing time. In addition, there is less maintenance required, resulting in higher availability.
Space-saving rotation
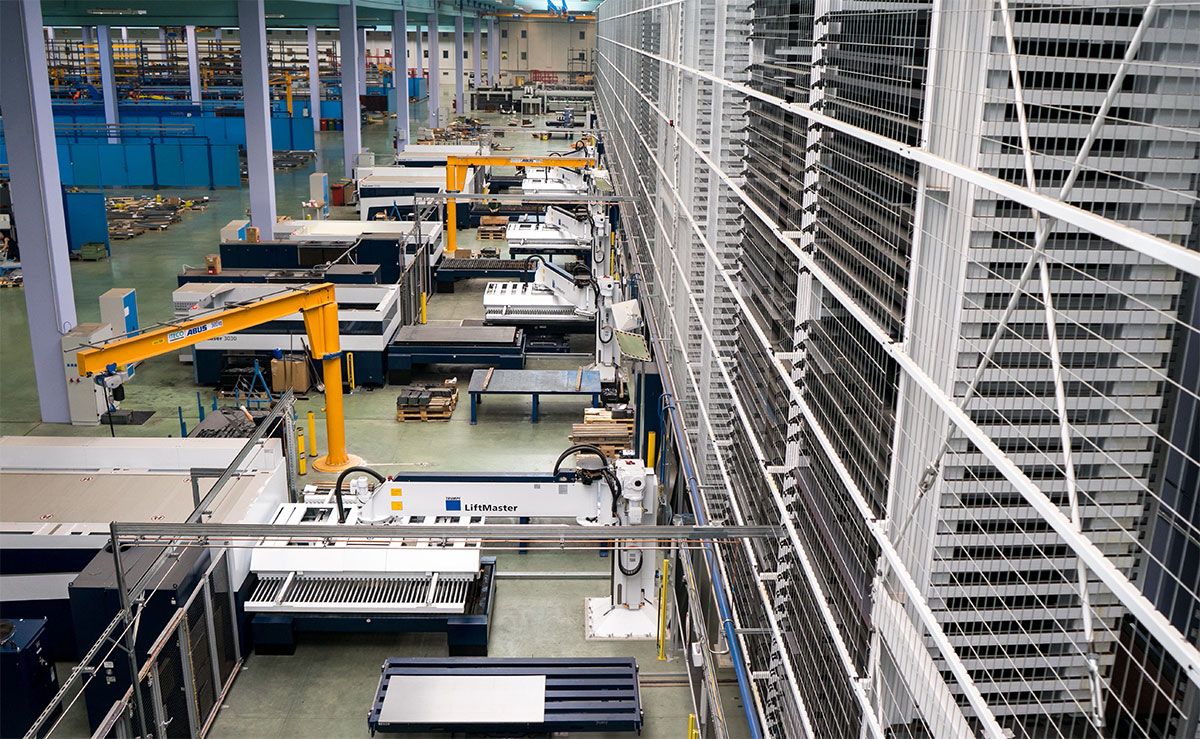
The turntables of the loading stations provide the sheets in a space-saving manner, so that a larger number of laser cutting machines can be connected
Křenek uses his tablet PC to show products from companies that purchase sheet metal components from AGROSTROJ. “The automated storage system also indirectly supplies the production facilities of our cooperation partners via our laser cutting systems. Because these customers sometimes want to be supplied just-in-time or just-in-sequence, their satisfaction depends not least on the performance of the storage system.”
One challenge was to automatically connect ten laser cutting machines, which, including their handling equipment, require a large floor space, to the two-shift system. As a result, the manufacturer presented a compact, space-saving solution in which the transport trolleys of the loading stations are equipped with turning devices. Křenek explains how it works on site. “Since the sheets are turned 90 degrees to the warehouse, we were able to place the machines closer together and – based on the length of the warehouse – save about four meters per laser cutting machine. With the standard setup, there would not have been enough space for the desired ten machines, but only for six.”
High availability
The real-time soft PLC integrated into an industrial PC of the easy-to-operate STOPA COMPACT II, which is equipped for three loading heights of a maximum of 90, 275 and 1,015 millimeters, communicates with the TRUMPF Tru-Tops Fab module Storage via an interface developed by STOPA. This software manages all inventories and controls the material flow of the production.
Since STOPA has equipped the control system with a RAID system, the storage operation can continue even if a hard disk fails. This is an advantage that increases the availability of the entire system. If the power fails, for example due to a thunderstorm, the panel PC is still supplied with power for up to five minutes. If the fault is rectified within this time, the PC continues to run without interruption. Otherwise, an uninterruptible power supply (UPS) will shut down the PC in a controlled manner. This ensures that the current system data is backed up and that data and program losses are avoided. In addition, the manufacturer offers a remote diagnosis service via its TelePresence portal, which can be used to directly eliminate faults in the system control.
A long history
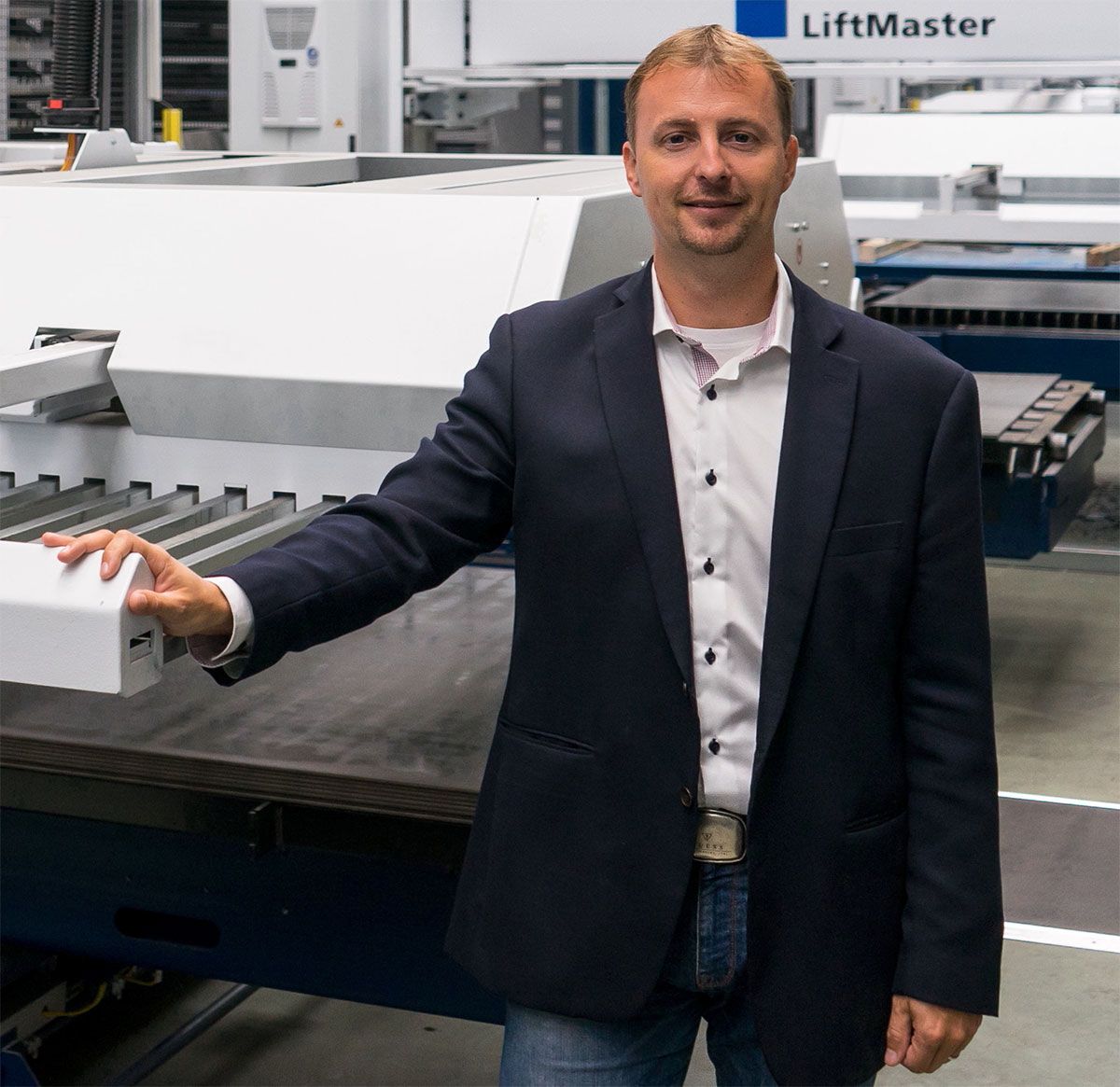
Miloš Křenek, Engineering Director at AGROSTROJ
AGROSTROJ and STOPA can look back on a long history of cooperation. Křenek holds up an old offer. “The contact was made through the recommendation of one of our customers, who also uses a STOPA sheet metal storage system. We invested in our first STOPA COMPACT in 2006. The three other automatic storage systems went into operation in 2007, 2012 and 2014. We chose STOPA again because the manufacturer’s storage systems are so reliable that we have had almost no problems with them over the years.”
Author: Jürgen Warmbol
Sales Contact Person
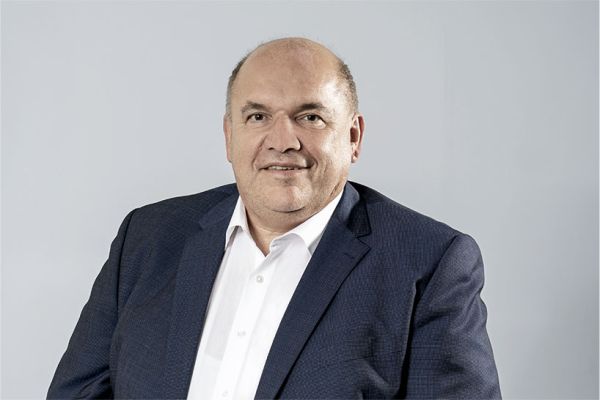
Holger Dehmelt
Sales Engineer Warehouse Technology
STOPA Anlagenbau GmbH
Industriestr. 12
77855 Achern-Gamshurst
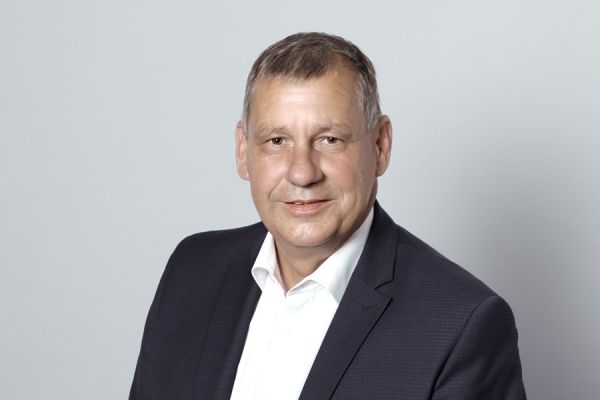
Rolf Eckhardt
Sales Engineer Warehouse Technology
STOPA Anlagenbau GmbH
Industriestr. 12
77855 Achern-Gamshurst
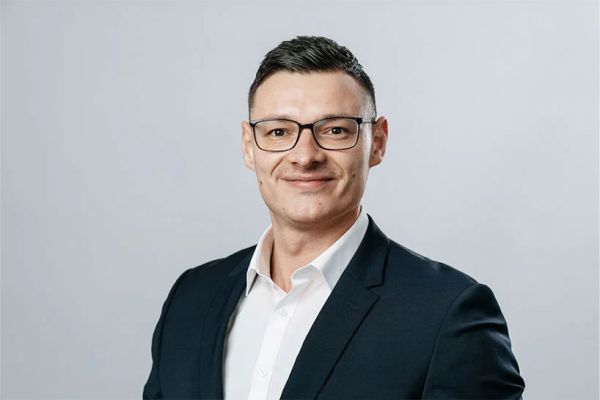
Andreas Pahl
Sales Engineer Warehouse Technology
STOPA Anlagenbau GmbH
Industriestr. 12
77855 Achern-Gamshurst