storage system brings productivity boost
By using a STOPA FLEX sheet metal storage system, Büchel Blech AG benefits from a high level of flexibility in material handling, as well as from cost and time savings. These advantages result in increased added value and ultimately in increased productivity.
Marco Büchel, managing director of Büchel Blech AG, Balzers in the Principality of Liechtenstein, which was founded in 1981, has taken a pioneering step towards increasing profitability by investing in the STOPA FLEX. “In the high-bay warehouse, we can stock enough sheet metal and cut the material ourselves at any time, without having to buy finished blanks.”
A calculation that works out, especially since the contract manufacturer is able to achieve cost reductions and time savings despite the expenses for the sheet metal storage system, the laser cutting system and the additional employees required. This is because he is now able to manufacture the components or semi-finished parts for his products in his own factory. This is a plus point that enables him to react immediately to market requirements, for example by answering enquiries promptly and making decisions at short notice. What’s more, the consistent quality of the material means that identical results of a consistently high quality can always be expected.
The storage system developed by STOPA Anlagenbau GmbH, Achern-Gamshurst, stands for efficient use of space, faster access to the sheets, more organization and careful handling of the material.
Furthermore, the storage system is a prerequisite for process-optimized production, in which flexible material provisioning of different sheet formats and sheet thicknesses is required.
Easy material handling
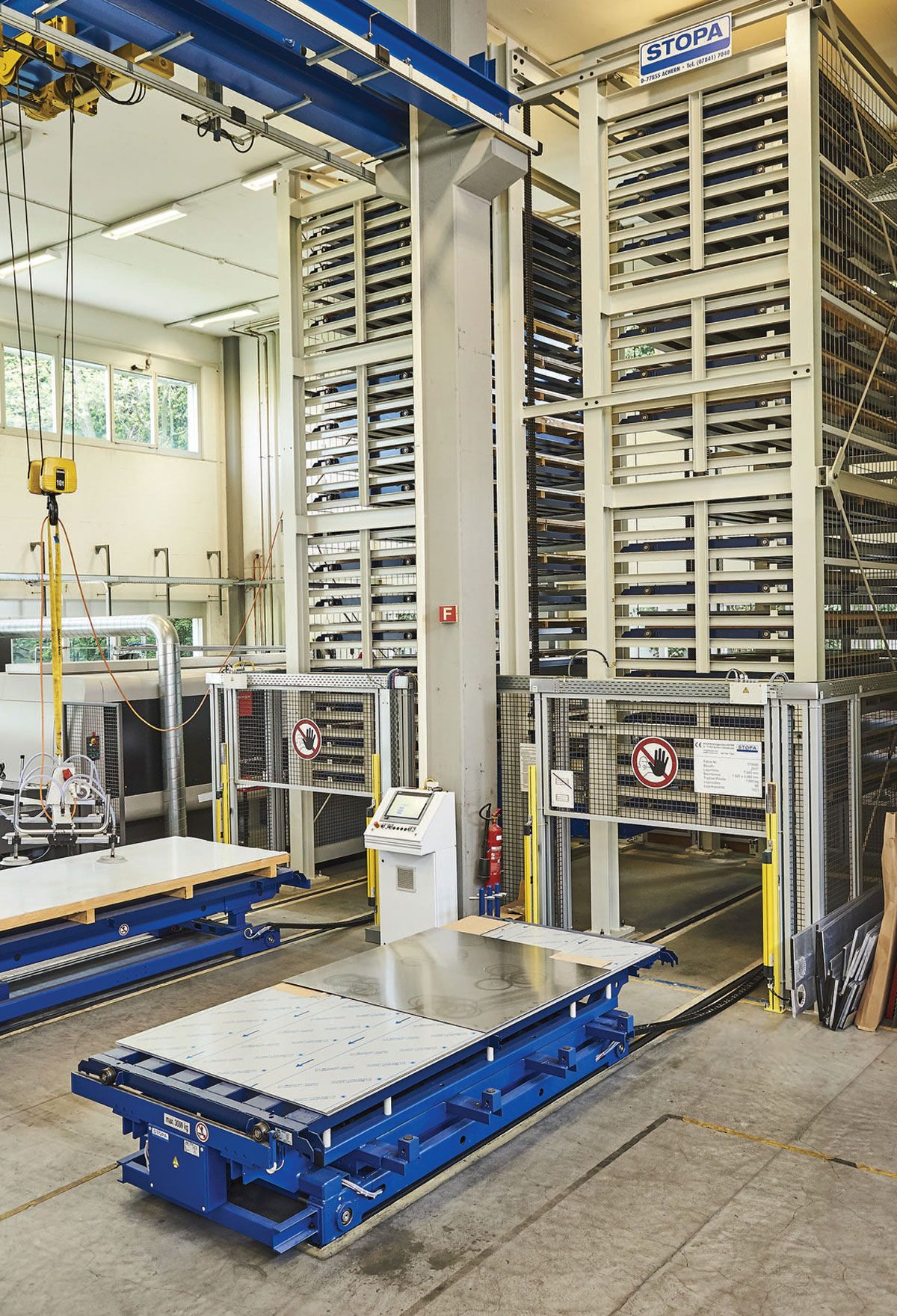
Büchel increases its flexibility by using a solution with two transport carts that store and retrieve at the same time
Marco Büchel observes how the laser cutting system is supplied from the sheet metal storage system. “What is important is that the material handling is simple, because this step takes more time than in mass production. With this in mind, we have invested in two transport carts that facilitate parallel processes and thus increase our flexibility. One example of this is the ability to store and retrieve material at the same time.”
Employees use manual transport carts to move the sheets to the laser cutter and to return the leftover sheets to the warehouse. To ensure that the same material in the same thickness is always on the 40 flat pallets of the system, each of which has a usable area of 1,525 x 3,050 millimeters, they put the leftovers back on the original load carriers. The material movements can be tracked by the operator’s ERP system, as the transport carts are numbered.
The contract manufacturer, whose broad range of services extends from design to laser cutting, folding, deburring, welding, rounding, blasting and vibratory grinding, as well as clean room and assembly work, relies on STOPA WMS 4.0 as its warehouse management software. The WMS fulfills all the functions required to operate a high-bay warehouse with fixed bin allocation, including administration and automatic control. The WMS can be customized with regard to the range of functions, as well as the table and language display. In addition, the system offers further highlights, with batch tracking being particularly noteworthy. A Microsoft SQLServer Express database is used to manage and secure the data by default.
Marco Büchel, whose company generates an annual turnover of around four million Swiss francs, has clear ideas about the sheet metal warehouse in which he stores large and medium-sized sheets. “One of the main reasons for our decision was that STOPA was the only manufacturer to offer two front-end stations as standard. The other companies we approached would have had to build special solutions.”
The stations are a scissor lift table and a transport cart with a fixed height. Büchel uses the scissor lift table, which is equipped with storage stamps and pluggable stops for a common coordinate corner, as a goods receipt and goods issue. The transport cart, which, like the scissor lift table, is equipped with a pneumatic pallet locking device, is used for outgoing goods. Light barriers check whether the system is maintaining the permissible loading height.
The compact tower storage system enables the operator, who handles 60 tons of chrome steel and aluminum as well as 20 tons of special steel annually, to achieve an ideal ratio between storage capacity and space requirements. In addition, he benefits from high cost-effectiveness. In order to make optimal use of the system height, Büchel decided on two pallet loading heights. Material that he processes in large quantities is stored in the lower storage area with a maximum loading height of 275 millimeters. He also stores material directly from the truck there without having to repack it, which means that an unpacking table is unnecessary. The remaining pallets are designed for a loading height of 90 millimeters.
The system components of the STOPA FLEX, which is used in a single shift, are controlled by a real-time soft PLC that is integrated into an industrial PC. The PC, which is equipped with a touchscreen, operates the system and displays its status. This includes, for example, the graphical visualization of the warehouse and the double-mast storage and retrieval machine, as well as permanent status displays in plain text.
Marco Büchel leans against the ergonomic operating terminal of the tower storage system. “The system is easy to use. In addition to this terminal, STOPA has installed four more in our offices. If we initiate retrieval orders via the WMS, a light flashes in the warehouse as soon as the material is available. We do not use the function to pre-program travel orders. If necessary, we enter the orders individually.”
Highlights of the solution
- Büchel benefits from a high level of flexibility in material handling, as well as from cost and time savings.
- Increasing added value results in an increase in productivity.
- The sheet metal storage system can hold enough sheets to allow Büchel to cut the material itself at any time, without having to buy finished blanks.
- The operator can respond immediately to market demands.
A coherent package of services
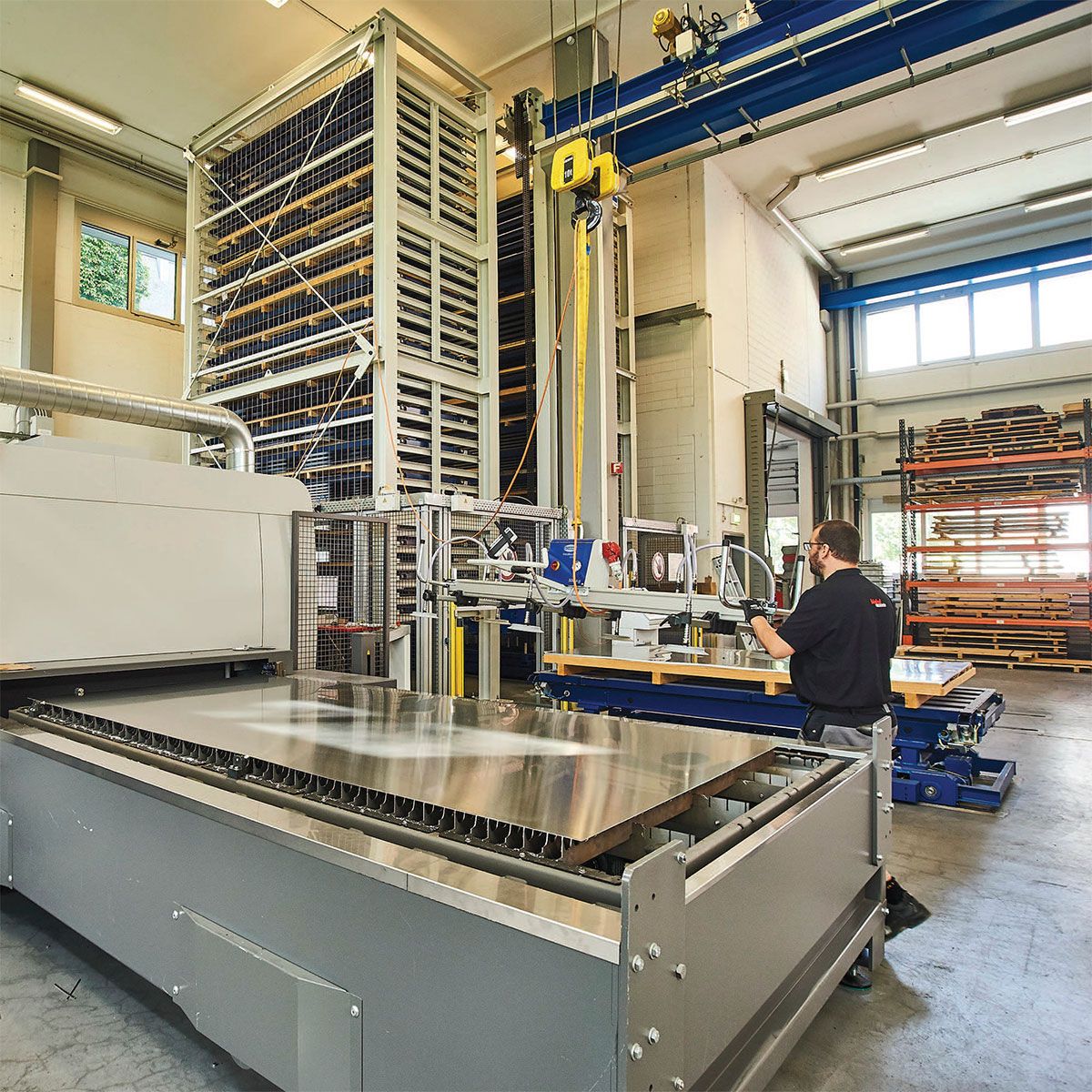
By choosing the STOPA FLEX, Büchel has taken a pioneering step towards increasing efficiency
The STOPA FLEX, which is around eight meters high, 4.7 meters long and 6.3 meters wide, started operation as planned in September 2017. Büchel, which manufactures customized individual parts, series and assemblies, had asked several suppliers, of which it included three in the shortlist. A considerable challenge was that the relocation of the ISO 9002-certified company to the current building was planned to take place in parallel with the completion of the warehouse. Against this background, the decision in favor of STOPA also depended on the firm commitment to the desired commissioning date. If the manufacturer had not been able to meet the deadline, Büchel’s production, which mainly supplies the semiconductor industry, plant construction for semiconductor coatings and vaporization, as well as the automotive industry and other industrial sectors, would have come to a standstill. STOPA even had to reschedule and reduce the loading capacity of the pallets from a maximum of three tons to one and a half tons, as the foundation of the hall had already been completed.
Ralf Gerber, Technical Manager at STOPA, points to the tight space in which his company has installed the tower storage system with millimeter precision. “Due to the spatial constraints, which were caused by the building structure, the previously installed laser cutting system and a crane rail under the hall roof, the construction of the storage system, which is designed as a double block, was a challenge. Our fitters solved the problem with the help of a crawler vehicle equipped with a crane.” Marco Büchel, who expects a payback period of five years, looks back on the decision-making process with satisfaction. ”We see the increase in productivity, which is based on our increasing added value, as a major advantage of the investment. I would also like to emphasize the high level of consulting expertise of STOPA, which made us feel secure in our decision. All the points that needed to be clarified before the contract was awarded were clearly addressed and adhered to. Apart from that, the STOPA FLEX is a proven storage system. This was confirmed to us by the operator of a reference system that we visited.”
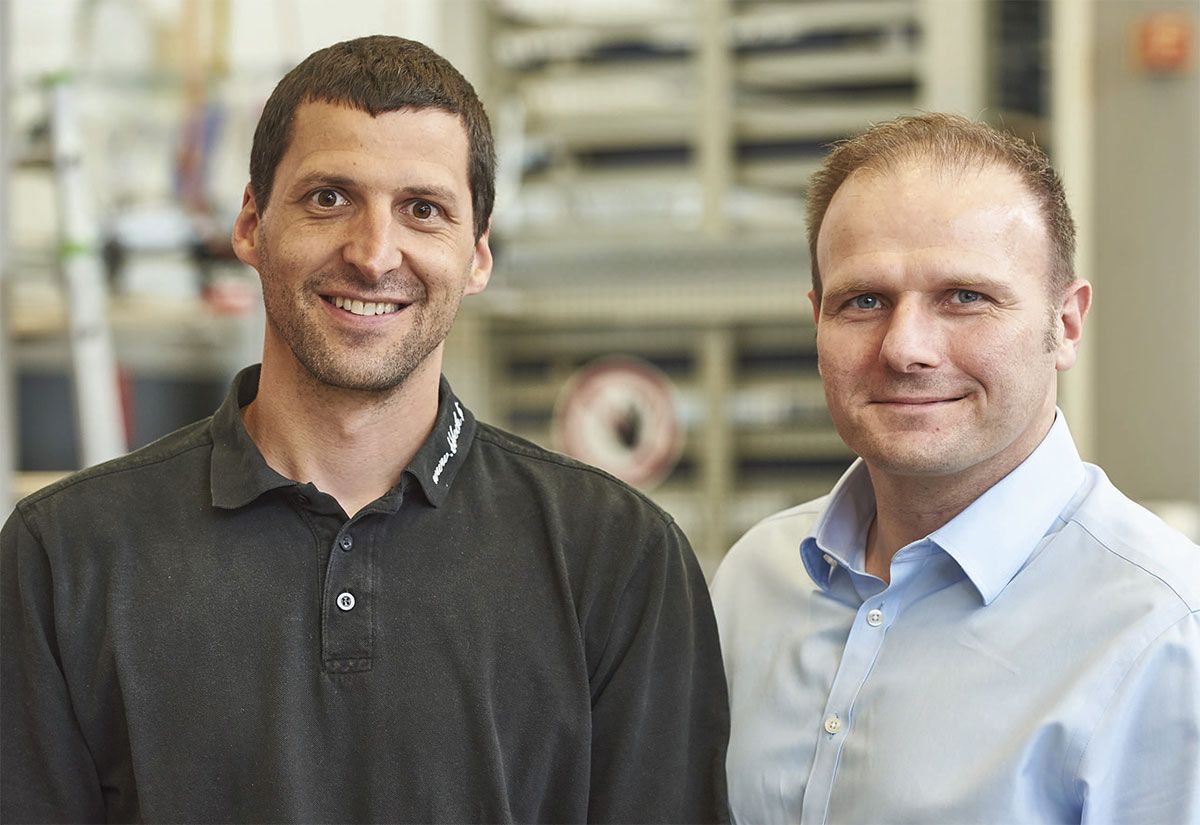
Marco Büchel, Managing Director of Büchel Blech AG (left), and Ralf Gerber, Technical Director at STOPA, see the main advantage of the investment in increased productivity
Author: Jürgen Warmbol
Sales Contact Person
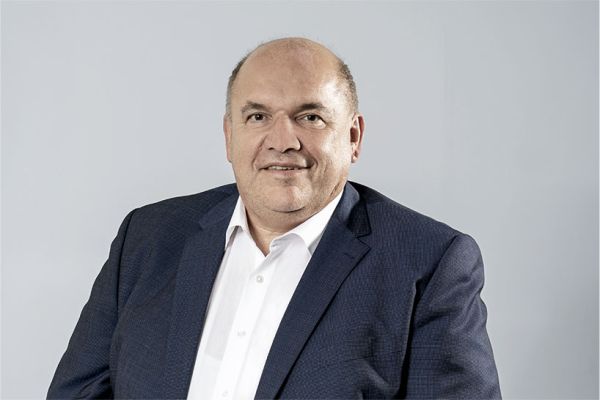
Holger Dehmelt
Sales Engineer Warehouse Technology
STOPA Anlagenbau GmbH
Industriestr. 12
77855 Achern-Gamshurst
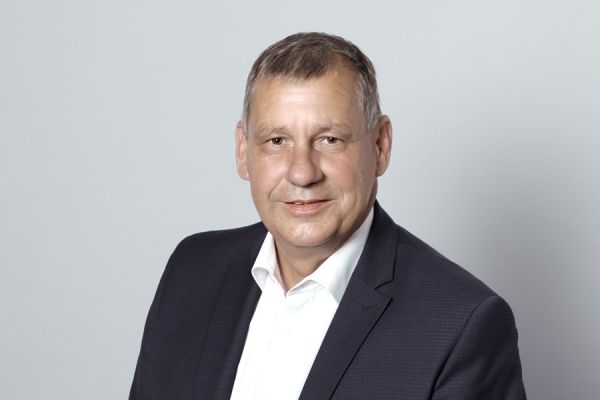
Rolf Eckhardt
Sales Engineer Warehouse Technology
STOPA Anlagenbau GmbH
Industriestr. 12
77855 Achern-Gamshurst
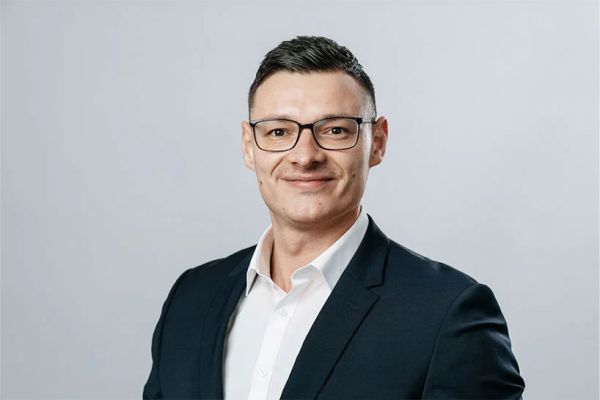
Andreas Pahl
Sales Engineer Warehouse Technology
STOPA Anlagenbau GmbH
Industriestr. 12
77855 Achern-Gamshurst