storage system: an economical entry-level solution
With the STOPA ECO storage system, KW automotive has created the basis for efficient sheet metal processing. The company supplies a laser cutting system that produces welded parts for high-end chassis from the compact storage system.
Stefan Weihbrecht, head of production at KW automotive GmbH, Fichtenberg (Baden-Württemberg), which was founded in 1995, holds a component in his hand. “We use the sheet metal panels that we buffer in the tower storage system to produce welded parts for chassis.” KW automotive, a global company with around 200 employees at five locations, has made a name for itself in the fields of car tuning and vehicle refinement. It supplies industrial customers and motor sports teams, primarily with a wide range of high-end chassis. In addition to chassis solutions, the company also manufactures patented gullwing conversion kits that are available for almost all common car models.
Need for speed
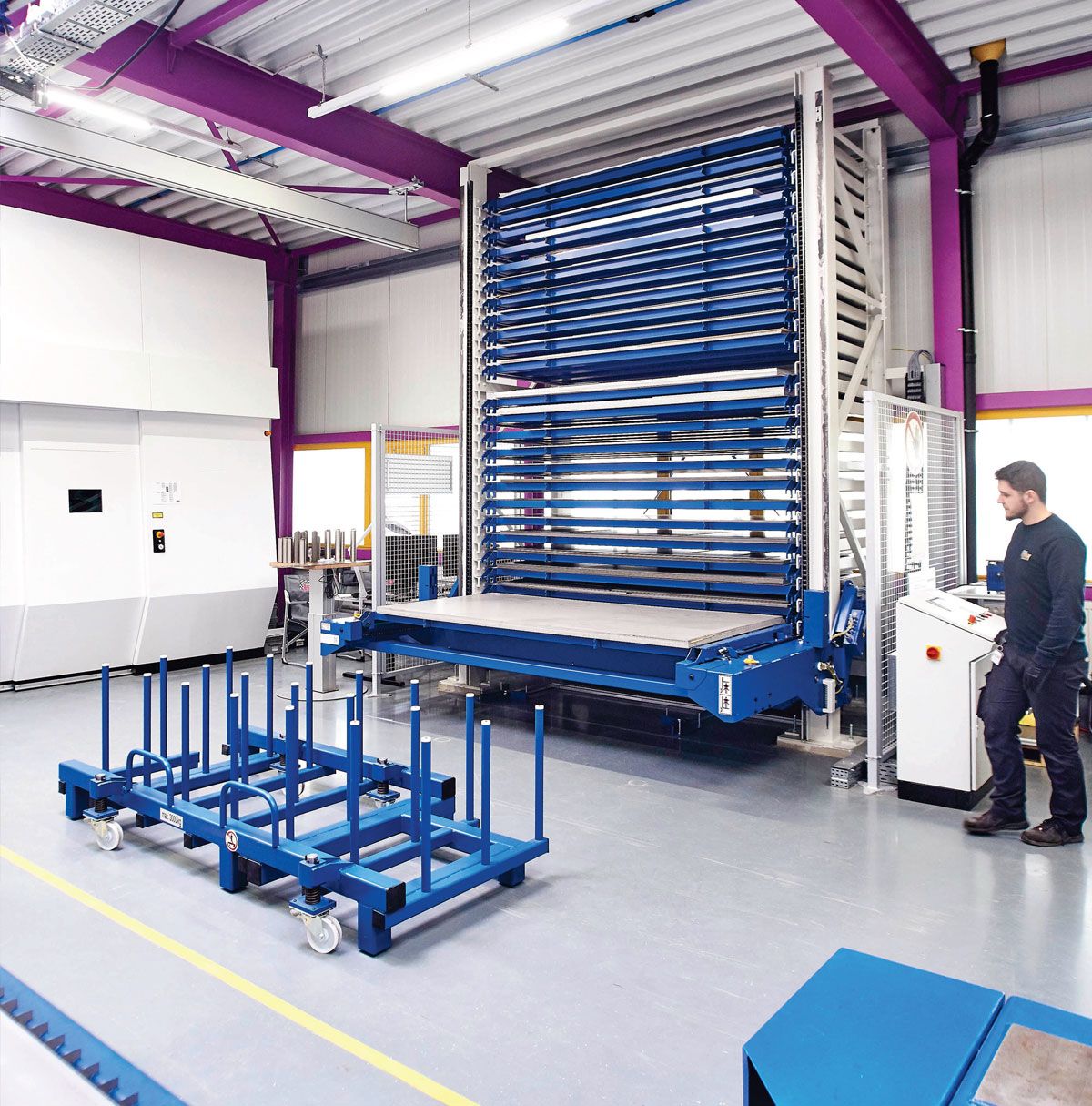
Axel Ausländer enters the start and finish coordinates at the central control panel to save a system pallet in advance.
Speed is of the essence not only in the race, but also in the provision of sheet metal. The STOPA ECO, developed by STOPA Anlagenbau GmbH, Achern-Gamshurst, meets this production requirement by enabling fast access to raw sheet metal. The single-sided tower storage system with pull-out technology, which is around 4.5 meters high, 2.9 meters long and 3.6 meters wide at KW automotive, has other advantages too. These include space-saving storage of the sheets, minimal material damage and more organization, which means less time spent searching. In addition, the STOPA ECO, which is designed for a payload of 1,200 kilograms per compartment or system pallet, offers an affordable entry into the automatic storage of flat goods materials thanks to its modular concept.
Weihbrecht is standing in front of the tower storage system. “Since we only work with medium-sized sheets, we decided on a rack block with matching system pallets. We also chose a fixed height grid for the loading height of 60 millimeters because, based on our part geometry, this allows for optimal packing density.” On request, STOPA can also supply the tower storage system with a grid for a loading height of 200 millimeters. This would allow for higher loads or, for example, wooden pallets to be stored. The STOPA ECO at KW automotive is equipped with 26 storage spaces. The system pallets consist of a self-supporting frame construction with longitudinal beams and slide rails. They also have a usable pallet surface of up to 1,250 x 2,500 millimeters and a maximum loading height of 60 millimeters, which is controlled by a laser.
Due to the fixed-position storage, each pallet is assigned a specific place in the rack block, whose longitudinal connections and diagonal stiffeners, in conjunction with a rear push-through protection, ensure a stable steel construction system. The stationary lifting traverse is equipped with a pull-and-push device and a fail-safe monitoring of all functions. The height positioning is performed by an absolute and load-independent digital distance measuring system.
Highlights of the solution
- Fast access to raw sheets
- Optimal packing density
- Space-saving storage
- Less time spent searching
- Minimized material damage
Semi-automatic processes
The task of the STOPA TOWER Eco, which operates in a single-shift operation at KW automotive, is to keep sheets ready for the TRUMPF TruMatic L 2530 laser cutting machine installed opposite the warehouse. The system operator, Axel Ausländer, uses a crane to lift the delivered sheet metal packages onto the fixed storage stamps of the storage platform, between which the lifting or load crossbeam of the tower storage system has deposited a system pallet. If there is no empty pallet available, he places the material as an additional load on a pallet that already contains the same material. The operator finds the system easy to use. He selects the storage location and has the load carrier stored by entering the start and target coordinates at the central system control panel. When he releases pallets, they return to their compartment.
All storage and retrieval operations are semi-automatic as long as the employee keeps pressing the confirmation button. KW automotive has not yet required the optional automatic operation offered by STOPA, which would enable individual orders to be processed automatically after the start and destination coordinates have been entered.
The material stored in the tower storage system consists of steel and stainless steel.
The company also buffers aluminum sheets there. The material thicknesses vary between one and 15 millimeters. Inventory management is handled by the operator’s ERP system, which has a total production and usable area of 23,000 square meters at its headquarters in Fichtenberg.
Axel Ausländer is standing at the control panel of the programmed compact control system (PLC), which is equipped with an LCD display and a touchscreen user interface, and is monitoring the position of the sheets with regard to occupational safety. This is an additional control. Because the sheets are stored in a defined manner and can be picked up and delivered safely, the safety offered by the tower storage system is significantly higher than that of manual handling. He triggers material retrieval by entering the number of the compartment from which the pallet is to be moved to the retrieval position. If the retrieval involves one of the two lowest storage compartments, the storage platform can be moved when empty. The operator lifts the sheets from the load beam of the tower storage system using the crane and transfers them to the laser cutting system in a single step. He always stores any leftover sheets.
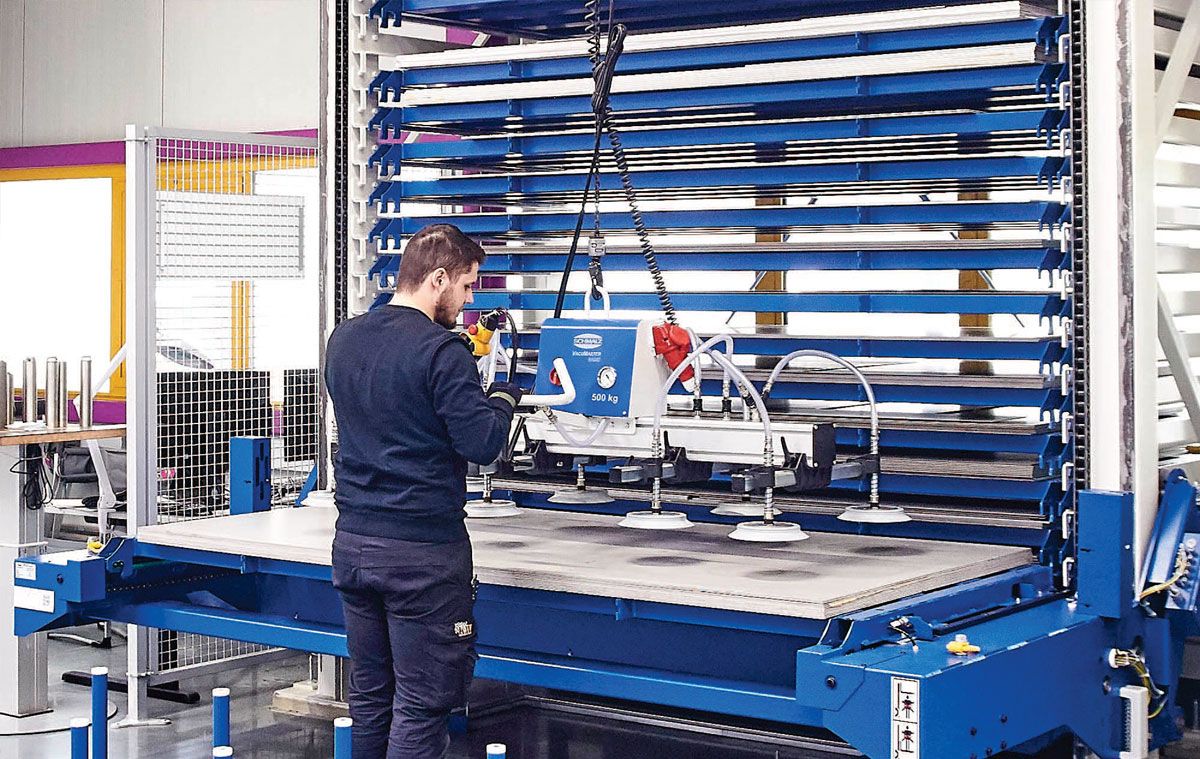
Since the tower storage system could buffer material for other processing machines in view of its capacity, KW automotive has invested in the future
With sheet metal into the future

Speed is of the essence when it comes to providing sheets
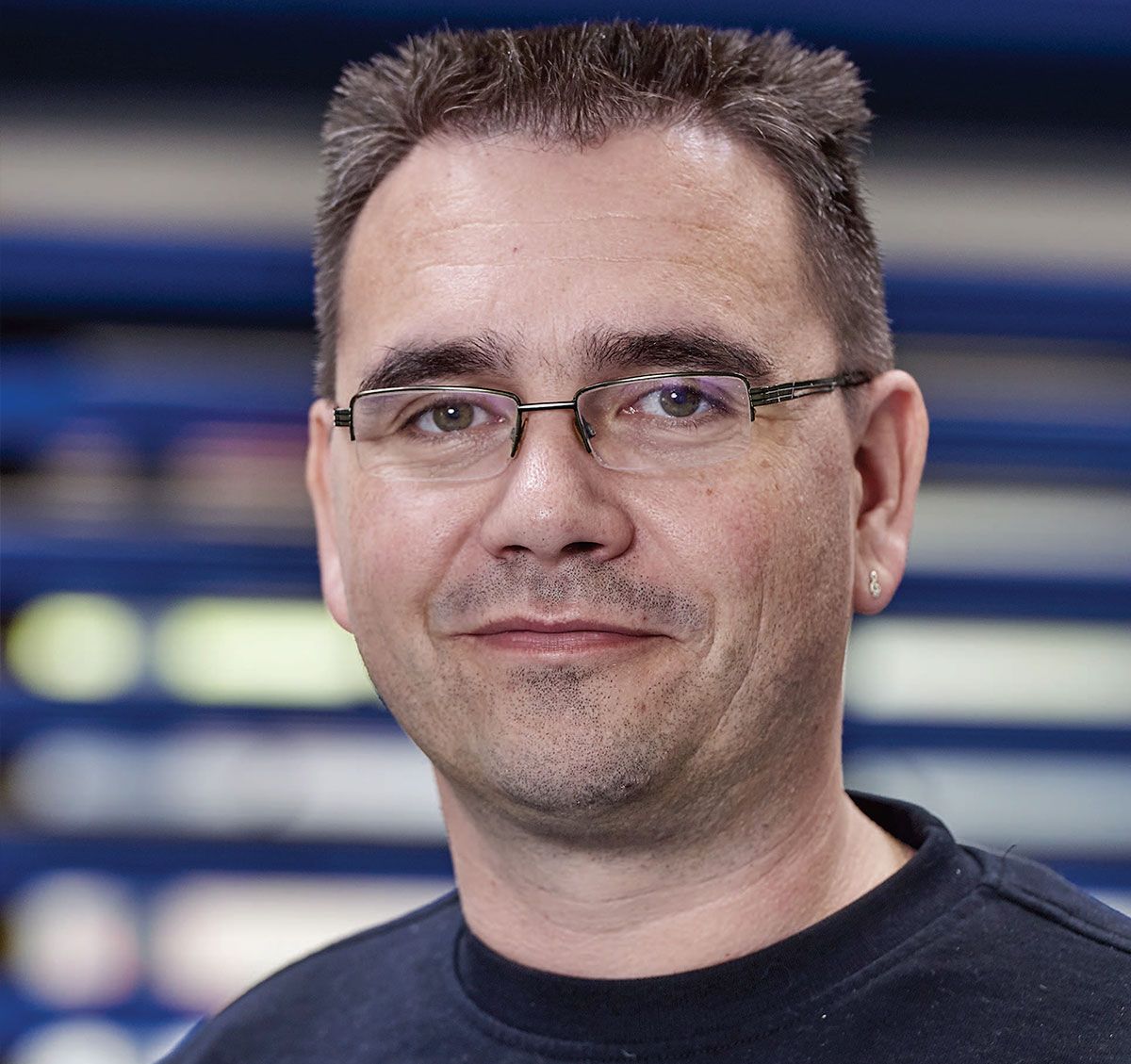
Stefan Weihbrecht, Head of Production at KW automotive GmbH
The commissioning of the STOPA TOWER Eco at KW automotive at the beginning of 2019, which has an availability of almost 100 percent, marked the start of sheet metal processing. Weihbrecht is satisfied. “Since the tower storage system could buffer material for other processing machines, we have invested in the future.”
Author: Jürgen Warmbol
Sales Contact Person
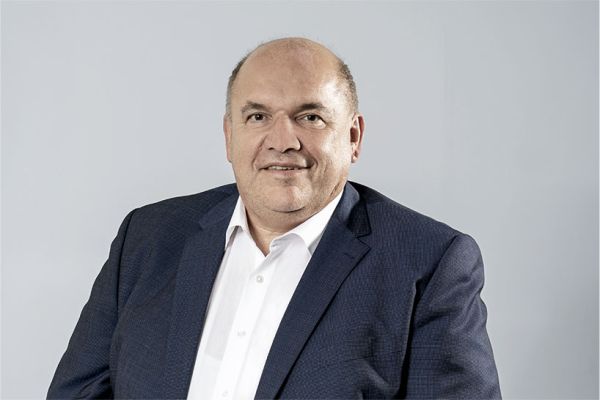
Holger Dehmelt
Sales Engineer Warehouse Technology
STOPA Anlagenbau GmbH
Industriestr. 12
77855 Achern-Gamshurst
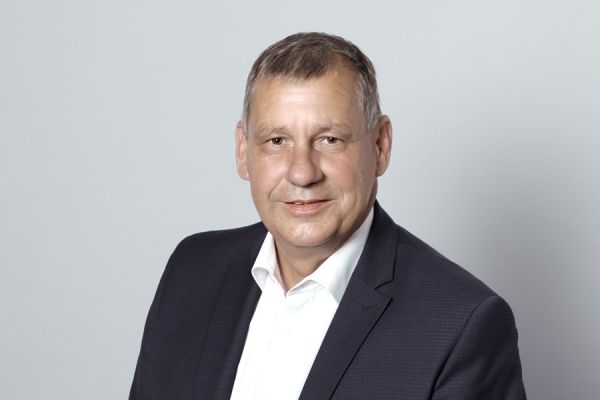
Rolf Eckhardt
Sales Engineer Warehouse Technology
STOPA Anlagenbau GmbH
Industriestr. 12
77855 Achern-Gamshurst
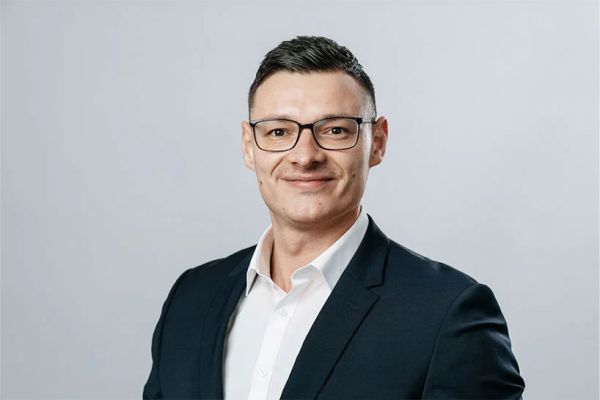
Andreas Pahl
Sales Engineer Warehouse Technology
STOPA Anlagenbau GmbH
Industriestr. 12
77855 Achern-Gamshurst