Redundant tower construction
In order to continue to offer high delivery quality and on-time delivery, GEBHARDT Fördertechnik has invested in a second tower storage system for sheet metal and in another laser cutting system. The storage system supplied by STOPA helps the company to avoid bottlenecks, which can never be completely ruled out with a large order volume.
GEBHARDT Fördertechnik GmbH, Sinsheim, uses the two STOPA sheet metal storage systems to demonstrate how compactly sheet metal can be stored in a relatively small area. Torsten Schumacher, Technical Plant Manager at the company, lists other advantages in addition to the economical use of space: “We have quick access to the sheets and there is no material lying around. We also benefit from lower handling costs and thus shorter throughput times.”
Furthermore, Schumacher reveals that the investment in the second TKL was not about expanding capacity. The trigger was the desire to be able to rule out a production stoppage if a fault should occur in the old warehouse or in the laser cutting system attached to it. This has not happened so far, but the redundancy provides even more security with regard to promised deadlines.
Compact storage system
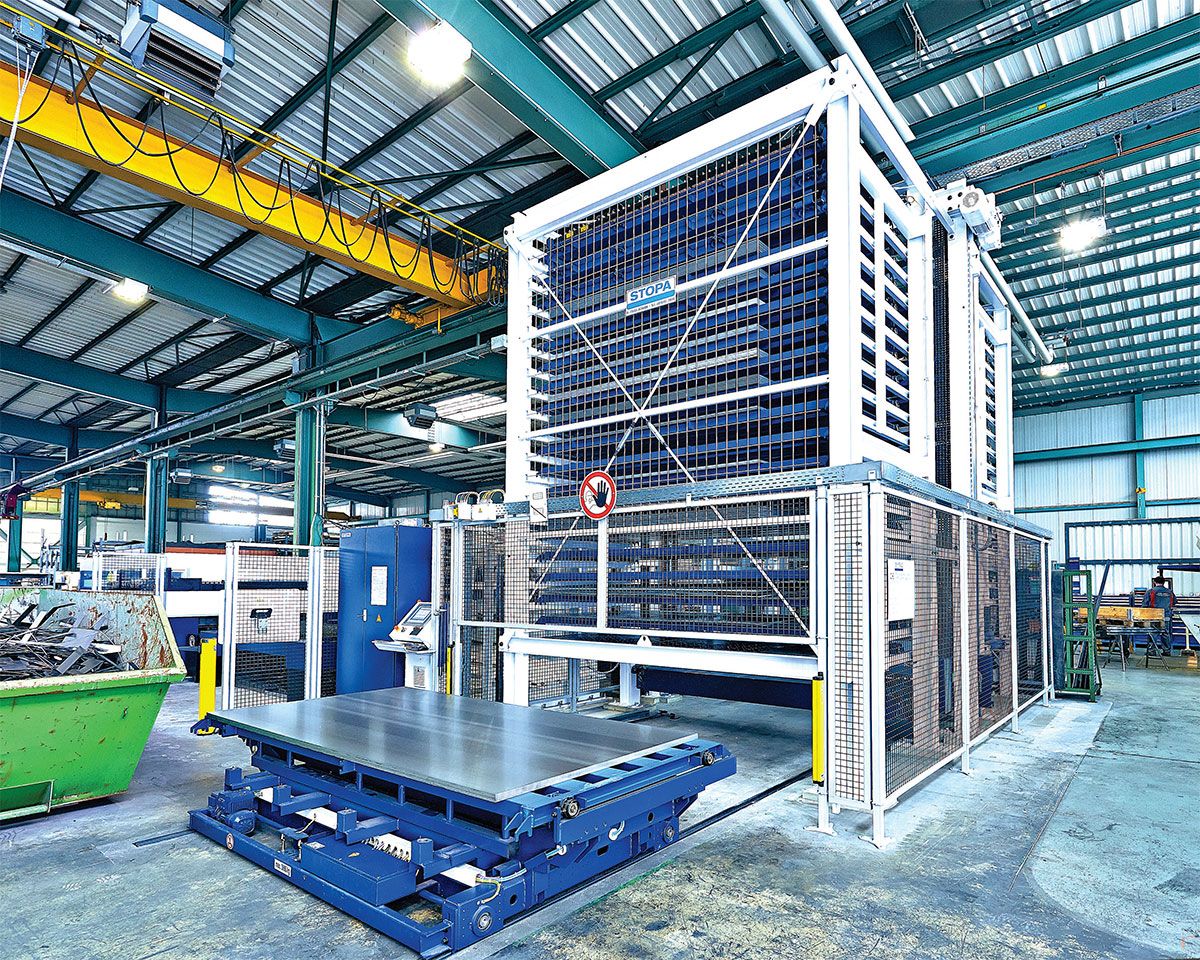
The two tower storage systems are a good example of how compactly sheet metal can be stored in a relatively small area
Schumacher goes to the incoming and outgoing goods station of the warehouse, which was supplied by STOPA Anlagenbau GmbH, Achern-Gamshurst. There, a forklift is just placing an unpacked sheet metal package on the storage stamps of the scissor lift table, which the station uses to store and retrieve material. “We use pluggable stops for a coordinate corner to be able to position the packages exactly, and a light barrier that checks whether we are keeping to the maximum loading height of 160 millimeters.”
GEBHARDT Fördertechnik has assigned fixed storage locations and article numbers to most types of sheet metal. The warehouse management computer shows the system operator where there is space for incoming or outgoing goods. The company mainly stores sheet metal in thicknesses of one to 20 millimeters. The materials it processes are steel sheet, aluminum and stainless steel. The warehouse also contains stainless steel sheets coated with film that are reserved for specific customers.
The TKL consists of two storage blocks. Their compact and secure steel construction is based on a shelf frame with longitudinal connections and diagonal reinforcements. The tower storage is about 5.8 meters high, 4.7 meters long and 6.3 meters wide. It is by no means at its limits, especially since it is available in heights of up to 20 meters.
Torsten Schumacher walks to the back of the sheet metal storage system, which can be seen from there, to explain its functions. “The two-mast load crossbeam, which moves in the Zaxis, stores and retrieves the flat pallets that serve as load carriers.” To do this, it uses a pull-and-push technology with roller chains and carriers that can be extended on both sides. For lifting, the crossbeam is equipped with a low-wear and low-maintenance chain hoist that has specially pre-stretched roller chains and a synchronizing shaft. The precise positioning of the very stable and robust lifting crossbeam is based on an absolutely and load-independent digital position measuring system that makes it unnecessary to approach a reference point. The traverse can reach speeds of up to twelve meters per minute when lifting and six meters per minute when pulling. All functions are monitored reliably. STOPA also scores points for its modular concept, which allows for expansion at any time, for example by connecting additional machines.
To keep the system’s 30 flat pallets in position on their inclined supports, self-supporting support rollers are mounted on the front side. The rollers are equipped with lifetime lubricated roller bearings that ensure long, low-maintenance operation. The load capacity of the pallets of 3,000 kilograms is designed for the large format (1,525 x 3,050 millimeters) and medium format sheets (1,250 x 2,500 millimeters) used by the customer. When storing and retrieving sheets or semi-finished products, bottom plates are used as required.
In addition to the flat pallets, GEBHARDT Fördertechnik uses six large-format laser auxiliary pallets on which sheet metal can be cut. For this purpose, STOPA has supplied holders for centering the auxiliary pallets, the centering devices themselves and two-part bottom plates. This means that the operator can buffer the laser auxiliary pallets that are not currently in use in the TKL. Of the 36 storage locations, 30 are designed for a loading height of 130 millimeters and six for a loading height of 160 millimeters.
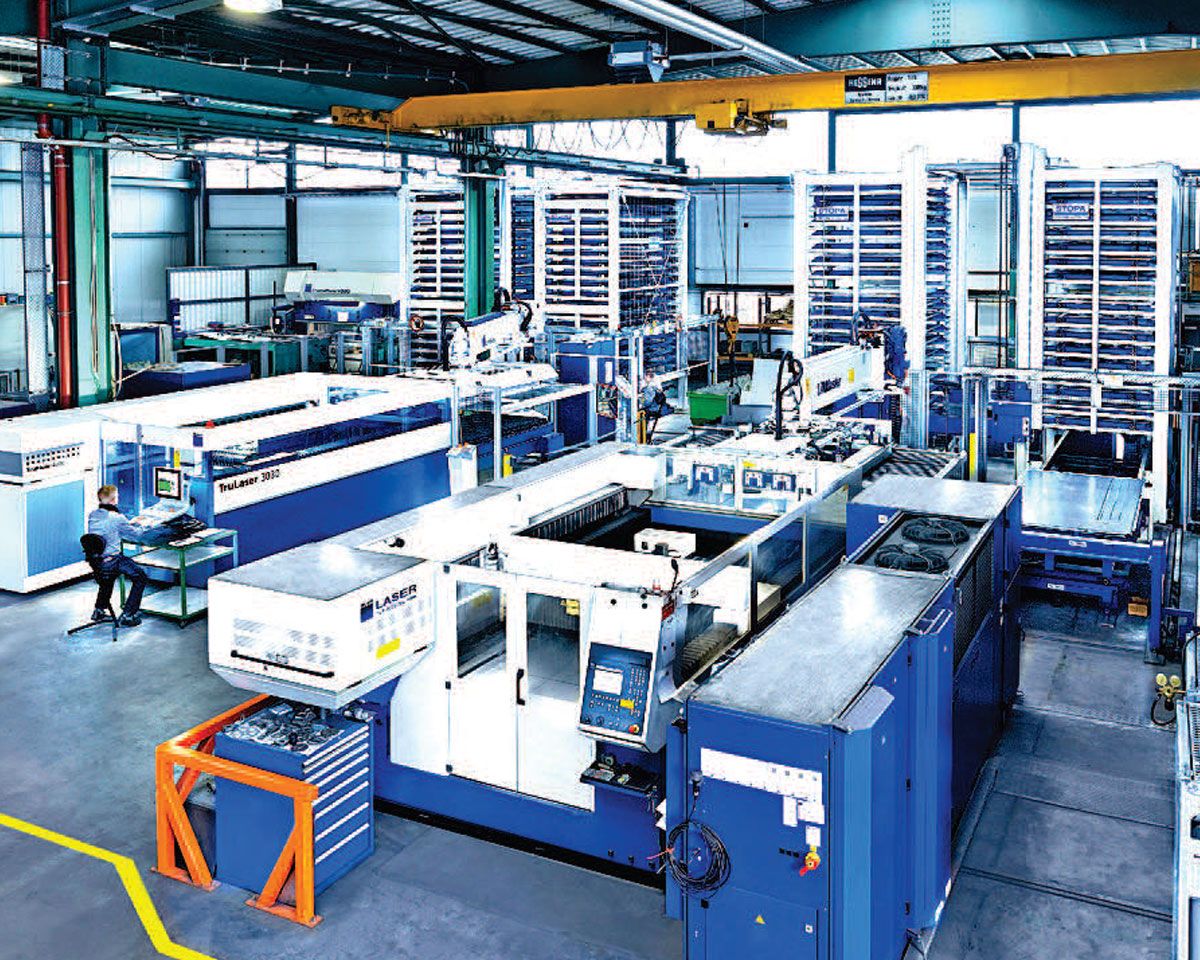
The front loading and unloading station of the storage system is equipped with an upper and lower carriage and the automatic loading and unloading device LiftMaster
Optimized laser cutting
A TRUMPF TruLaser 3030 flatbed laser machine is connected to the front loading and unloading station. The system, which receives its orders from the work preparation department, retrieves the required sheets from the towers. In the warehouse office, Schumacher asks an operator to use the computer to nest components on a sheet of metal. “Thanks to his proximity to the system and the warehouse and the resulting overview, the operator can also nest standard stock parts on a sheet that cannot be completely filled with order parts. This means that we are able to process sheets in a single pass with optimized cutting.”
The double station is equipped with an upper and lower carriage at a fixed height and with the automatic loading and unloading device LiftMaster. The lower carriage, which serves as a loading carriage and on which the last sheet is automatically recognized, has a loading height of 130 millimeters. The laser cutting system processes the orders around the clock, one after the other. In the third shift, it runs unmanned. Schumacher points to the upper carriage, on which the LiftMaster places a residual sheet. “Thanks to its gantry design, this carriage moves above the lower carriage in a space-saving manner.” The upper carriage is designed for a maximum loading height of 160 millimeters, which is monitored by a loading height control. The operator also has the option of moving the stations in the approval mode using the control panel.
Automation components lock the pallets pneumatically on the transport carriages of the double station and on the scissor lift table of the incoming and outgoing goods station. The scissor lift table is also equipped with a pneumatic carriage lock.
At night, GEBHARDT Fördertechnik returns semi-finished and finished parts, as well as scrap metal, to the TKL. During the day, semi-finished and finished parts are immediately transported to the goods-out station of the sheet metal warehouse, where they are picked onto pallets. The factory processes 90 percent of the semi-finished parts and buffers them in a rack for this purpose.
Easy to operate
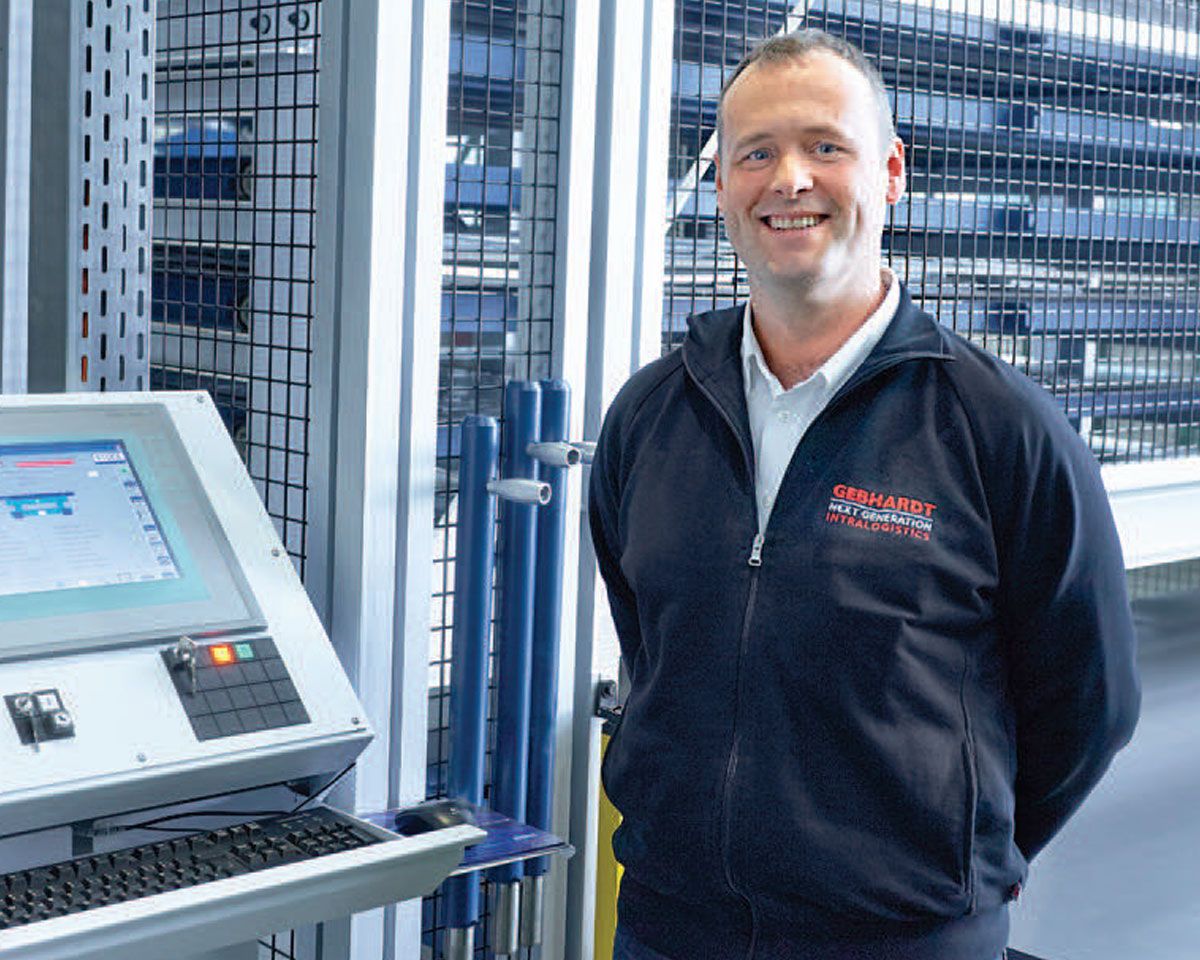
Torsten Schumacher, Technical Plant Manager at GEBHARDT Fördertechnik
A real-time soft PLC integrated into an industrial PC controls the system components of the warehouse and communicates with the warehouse management computer TRUMPF TC-Cell, which in turn is connected via interfaces to the laser cutting system and the operator’s ERP system. The industrial PC is used to operate and display the system status. If a hard disk should fail, a RAID system (Redundant Array of Independent Disks) backs up the data and thus ensures the availability of the entire system. With an uninterruptible power supply (UPS), STOPA prevents a power failure, for example as a result of a thunderstorm. The UPS switches off the PC in a targeted manner, thus also preventing data and program losses.
Torsten Schumacher demonstrates how easy and convenient it is to use the TKL at the ergonomically designed system control panel, into which the industrial PC with its 12-inch TFT display has been built. “You can visualize the warehouse and the storage and retrieval machine graphically and have the status displayed in plain text at all times. In addition, all messages and transport orders are logged.” Furthermore, the control system is equipped with a diagnostic function and an operating hours counter. In the event of a fault, STOPA is able to access the control system via modem and analyze and rectify the error from its own location.
Investment pays off
The scope of services provided by STOPA Anlagenbau GmbH, with whom GEBHARDT Fördertechnik has been working for 30 years, included the assembly of the storage blocks, the installation of the storage and retrieval machine and all safety equipment, as well as the overall commissioning, including the system control, in February 2013. In addition, STOPA commissioned the cell server software on site, provided first-level telephone support, trained the operators for a day in Sinsheim and then accompanied production for five days.
The new TKL is equivalent to its older counterpart from 2001. Torsten Schumacher is leafing through an evaluation. “The availability of our new sheet metal storage system has been 100 percent so far, and that of the old one was almost 100 percent. So far, we have had no reason to switch to the second storage system for redundancy reasons. However, the investment still pays off. Because we can now process several items of an order in parallel and high order volumes faster.”
Author: Jürgen Warmbol
Sales Contact Person
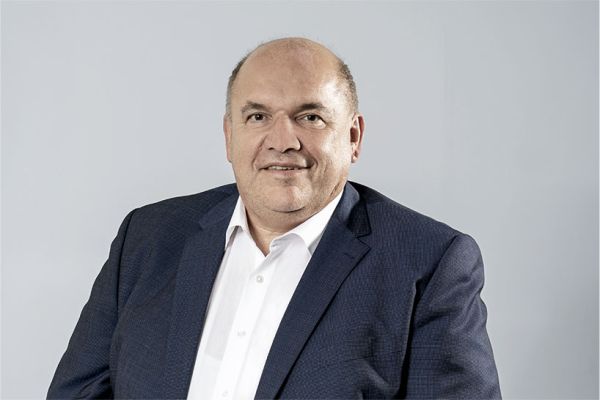
Holger Dehmelt
Sales Engineer Warehouse Technology
STOPA Anlagenbau GmbH
Industriestr. 12
77855 Achern-Gamshurst
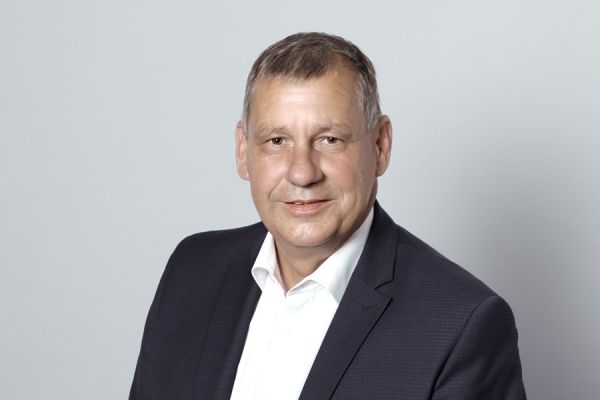
Rolf Eckhardt
Sales Engineer Warehouse Technology
STOPA Anlagenbau GmbH
Industriestr. 12
77855 Achern-Gamshurst
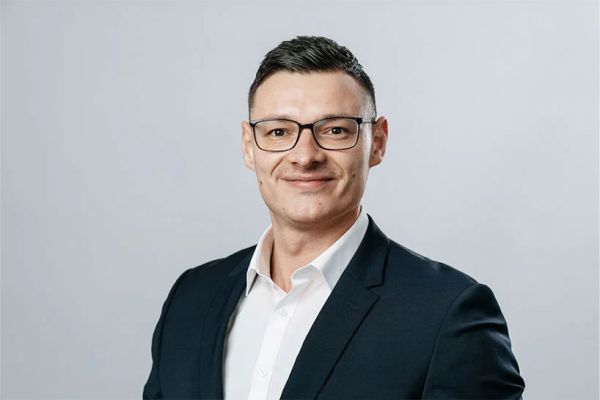
Andreas Pahl
Sales Engineer Warehouse Technology
STOPA Anlagenbau GmbH
Industriestr. 12
77855 Achern-Gamshurst