Generational change in the sheet-metal storage system
By investing in a STOPA COMPACT automatic storage system, mks Metallbau Schreiber has brought about a new generation of sheet metal storage. Compared to the previous system, the new, more compact system offers more storage space and a modern control system. This ensures inventory security, organization, fast processes and high availability.
Christel Schreiber, managing director of mks Metallbau Schreiber GmbH, Wolfschlugen, points to the aisle in which the shelf operating device moves. “The difference to the old sheet metal storage system is already noticeable by the two-row shelf blocks. The system installed in 1992 had fewer blocks, which were also in a row. We changed because certain spare parts for the control system were becoming increasingly difficult to obtain and because of the capacity bottlenecks that had recently arisen.«
The old system, which had 82 storage locations, had reached its limits due to increased material and handling volumes. In some cases, sheets of metal were even lying on the floor. Today, the warehouse has 199 spaces, not counting the stations. STOPA Anlagenbau GmbH, Achern-Gamshurst, has managed to more than double the number of spaces with the same storage height and only about 50 percent additional space. The reasons for this efficient use of space are a narrower compartment division, a lower lower approach dimension and an optimized design of the shelf operating device. In addition, the STOPA COMPACT works with multiple loading heights. In the old system, the storage spaces were designed for one height.
Weighing provides greater inventory security
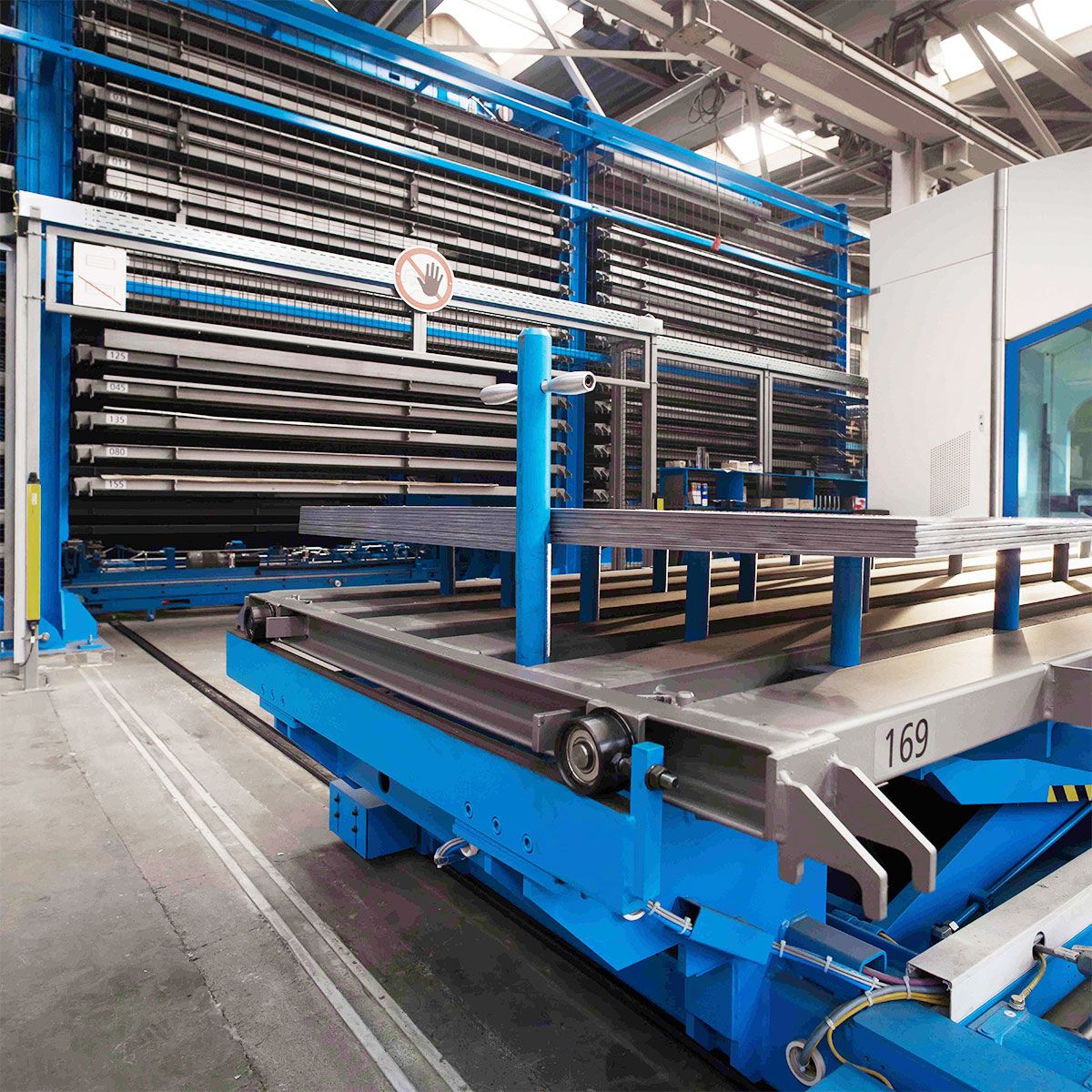
The scissor lift table picks up the sheet metal package on its stamping plates and lowers it onto a system pallet with the help of the stamps
An employee moves the stamping plates of the unpacking table, on which mks Metallbau Schreiber unloads sheet metal packages, and adjusts their position to the wooden pallets of the freight forwarder. A forklift truck then inserts its forks between the stamps, lifts the package and transports it to Station 1 of the warehouse. The operator also supplies a guillotine shear via this station, which is primarily used for incoming goods. “Here we place the sheet metal packages on the scissor lift table, which is also equipped with storage stamps,” explains Christel Schreiber. “We use pluggable stops to create a coordinate corner where the sheets can be aligned exactly.” The operator at the control panel enters important material properties and then presses the release button. The scissor lift table then lowers the sheet package onto a system pallet using the stamps and moves into the transfer position for the storage and retrieval unit.
The STOPA COMPACT automatic storage system at mks consists of ten double-row storage blocks. The system is a good 21 meters long, around five and a half meters wide and high, and it works with loading heights of 90 and 275 millimeters. Of its 199 storage spaces, the operator only uses 180 to store medium-sized (1,250 x 2,500 millimeters) and small-sized (1,000 x 2,000 millimeters) sheets in addition to the large format (1,500 x 3,000 millimeters) that is used primarily. It was essential to reduce the number of spaces because the load carriers are designed for a maximum material weight of 3,000 kilograms and therefore for sheet stacks that exceed the standard compartment height for smaller formats. To ensure that the medium and small-format sheets can be placed in a corner of the system pallets at the coordinate corner with a full payload, STOPA has made the load carriers more stable at mks. This prevents the greater deflection that would otherwise occur due to the uneven load distribution. Self-supporting support rollers mounted on the front side simplify the handling of the flat pallets, of which 180 run in the system.
Christel Schreiber watches the shelf-operating device as it picks up the system pallet with the sheet metal package. “Unlike our previous solution, STOPA has integrated a weighing unit into the load crossbeam that automatically records the weight of the load carrier, including the material, when it is stored and retrieved.” The information flows to the warehouse management system, which manages the stocks and thereby observes the specified minimum stock. In this way, the operator benefits from a high level of inventory security and the option of a permanent inventory. On top of that, the investment results in more order and occupational safety, as well as faster processes. And hardly any sheets are damaged anymore.
The shelf-operating device in a stable and robust two-mast design, which is equipped with a telescopic pulling and pushing device on both sides and a low-wear and low-maintenance chain hoist, stores the load carrier dynamically (chaotically) in the next free compartment. During the journey between the shelf blocks, a digital distance measuring system ensures exact longitudinal positioning. A further digital distance measuring system, which works absolutely and independently of the load, ensures precise height positioning and thus makes it unnecessary to approach a reference point. Data flows contactlessly and without wear via a light barrier to the shelf operating device. Energy is conducted through an overhead conductor rail, which also ensures low-wear and low-noise operation. To avoid collisions during storage, the storage and retrieval unit automatically checks the permissible loading height of the storage locations above and below the selected location. The storage and retrieval unit can travel at speeds of up to 100 meters per minute, 23 meters per minute when lifting and 20 meters per minute when pulling or pushing.
The employee at station 2 of the warehouse, which the STOPA COMPACT system uses to supply a TRUMPF TruLaser 3030 laser cutting machine with sheets, enters the number of the desired pallet or search criteria, which may include the thickness, width, length, quality, surface or article number of the material. The control system then lists all the corresponding load carriers. At this station, which is connected to the machine via an interface, a transport carriage moves at a fixed height. A spreading magnet aligns the sheets for the automatic loading device, whereby the control system observes the maximum loading height of 160 millimeters. Christel Schreiber watches as the pallet changer of the laser cutting machine exchanges the new sheet for the processed one. “When we store leftover sheets, the operator enters their size so that the inventory is secure.”

The TRUMPF laser cutting system is automatically connected to the sheet metal storage system via a transport cart and a loading unit
High data security
A real-time soft PLC integrated into an industrial PC controls the system components and communicates with the warehouse management computer. The work preparation department has access to the warehouse management system, from which it retrieves stock. The operator uses the industrial PC to operate and display the system statuses. If a hard disk should ever fail, the integrated RAID system (Redundant Array of Independent Disks) will back up the data. Because the warehouse can continue to operate, the availability of the entire system is guaranteed. With an uninterruptible power supply (UPS), STOPA also prevents the problems of a power outage, for example, caused by a thunderstorm. The UPS switches off the PC in a targeted manner, thus also preventing data and program loss.
“The sheet metal storage system is easy and convenient to use.” Christel Schreiber types commands into the ergonomic and clearly laid-out control panel. The 12-inch TFT display first shows the status of the storage and retrieval machine in plain text, followed by a graphical representation of the storage and retrieval machine and the storage blocks. “The software also shows free, occupied and blocked compartments, as well as empty and loaded pallets, including their loading height.” In the event of a fault, STOPA’s remote maintenance software PC Anywhere enables it to access the control system via modem in order to analyze and rectify the error from its own location.
Prepared for growth
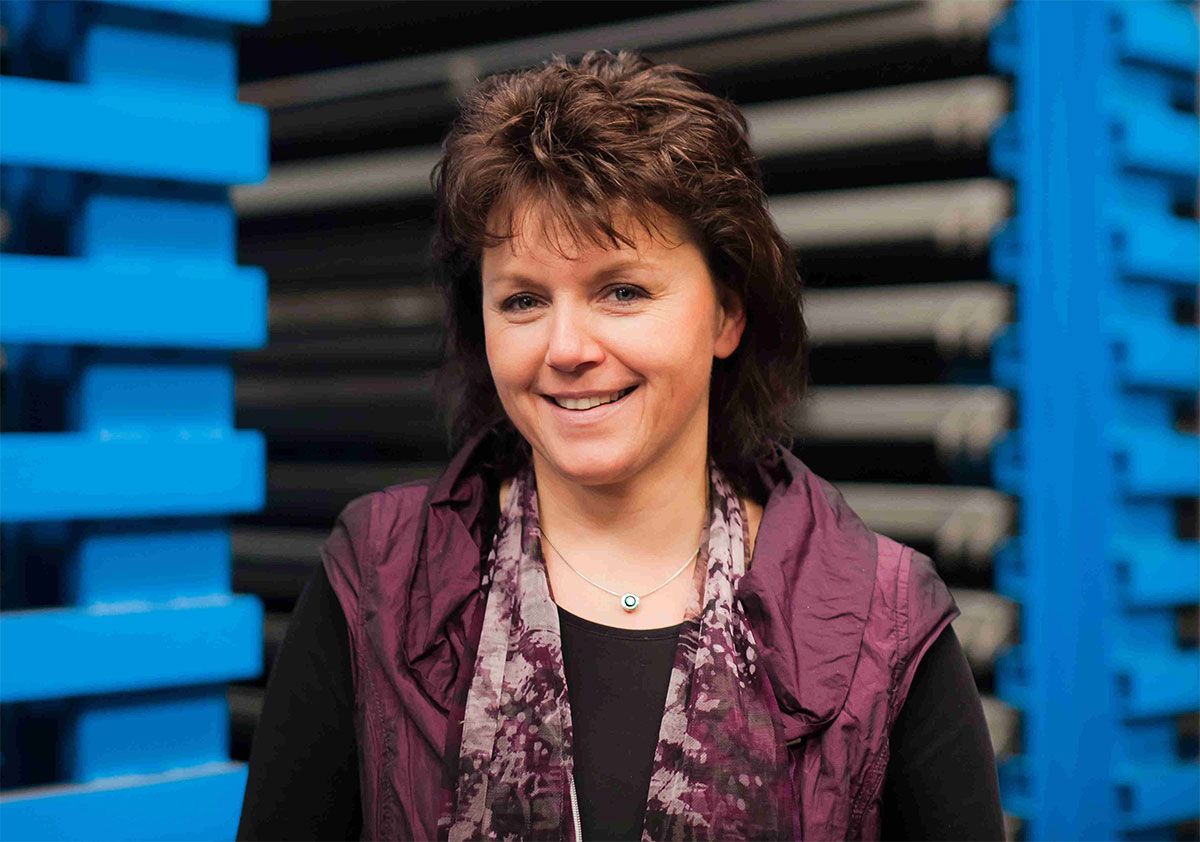
Christel Schreiber, Managing Director of mks Metallbau Schreiber GmbH
STOPA’s services also included the dismantling of the existing warehouse and a three-day training course for the operators of the system. Schreiber uses examples from the production process to explain what is made from the sheet metal. “Here you can see that we supply many production stations from the warehouse, as we rely on a high level of availability. That is why we decided to go with a system from STOPA again, especially since we were very satisfied with the old one for 20 years.”
The STOPA COMPACT automated storage system, which works in two shifts, started operation in February 2012. Christel Schreiber points to the area next to the right narrow side of the system. “We can extend the storage system in this direction. This is an advantage that equips us for further growth.” The system itself also contributes to this, as it can be expanded due to its modularity.
Author: Jürgen Warmbol
Sales Contact Person
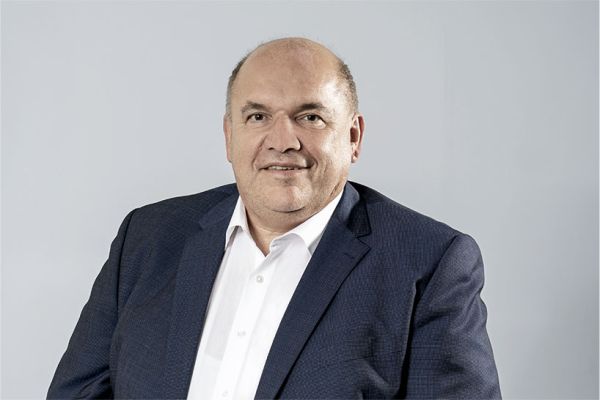
Holger Dehmelt
Sales Engineer Warehouse Technology
STOPA Anlagenbau GmbH
Industriestr. 12
77855 Achern-Gamshurst
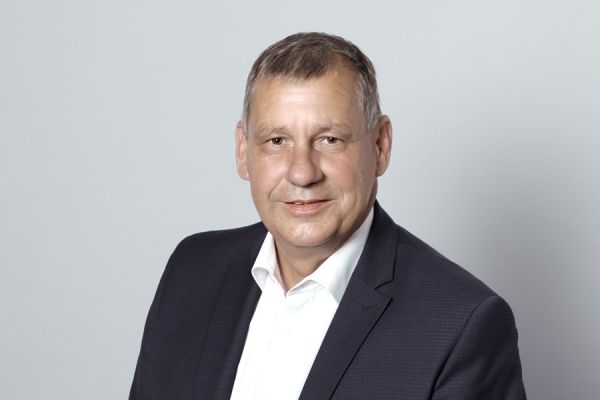
Rolf Eckhardt
Sales Engineer Warehouse Technology
STOPA Anlagenbau GmbH
Industriestr. 12
77855 Achern-Gamshurst
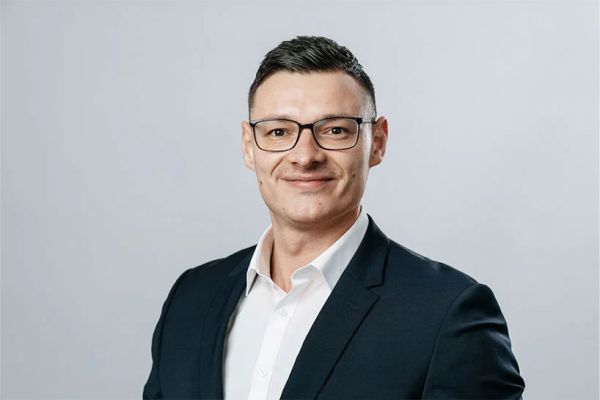
Andreas Pahl
Sales Engineer Warehouse Technology
STOPA Anlagenbau GmbH
Industriestr. 12
77855 Achern-Gamshurst