Efficiently connected
The sheet metal processing company Dreeskornfeld operates two STOPA UNIVERSAL automatic storage systems to store its extensive range of materials. One of the systems is designed for four sheet metal formats, including the maxi format XF. Since the storage systems are connected by a shuttle line running at a height of around five meters, each laser cutting system can be supplied from both systems.
Marcus Dreeskornfeld, managing partner of Heinz Dreeskornfeld GmbH & Co. KG, Bielefeld, which was founded in 1961, begins his tour of the production facilities at his new STOPA UNIVERSAL sheet metal storage system. “We were experiencing massive problems with regard to storage capacity for raw sheets, especially since we also buffer customer-owned material, which accounts for about 50 percent of our inventory. Since it was not possible to extend our old automatic storage system, we invested in a second system. Another decisive factor in this decision was that we are now working more and more with XF format sheets.”
The new automated storage system, which is around 83 meters long, seven meters high and six meters wide, went into operation in February 2015. Like the first system, it was supplied by STOPA Anlagenbau GmbH, Achern-Gamshurst. The large-scale storage systems are designed for extensive material ranges, economical use of space, direct access to raw materials, a controlled material flow, low-manpower processes and significantly reduced downtime. System pallets for small (KF), medium (MF) and large (GF) format sheets, as well as for the 2,000 x 4,000 millimeter maxi format (XF), serve as load carriers. By expanding to the XF format, for which the old warehouse was not designed, the family business is optimizing its processes. If Dreeskornfeld had decided to store the XF format in cantilever racks, the sheets would have bent considerably. Moreover, there would have been a risk of damage because forklifts would have had to transport the material to the processing machines. Apart from that, the concentration of all the sheets in the automatic storage system has the advantage of permanent stock control.
Storage systems precisely aligned with each other
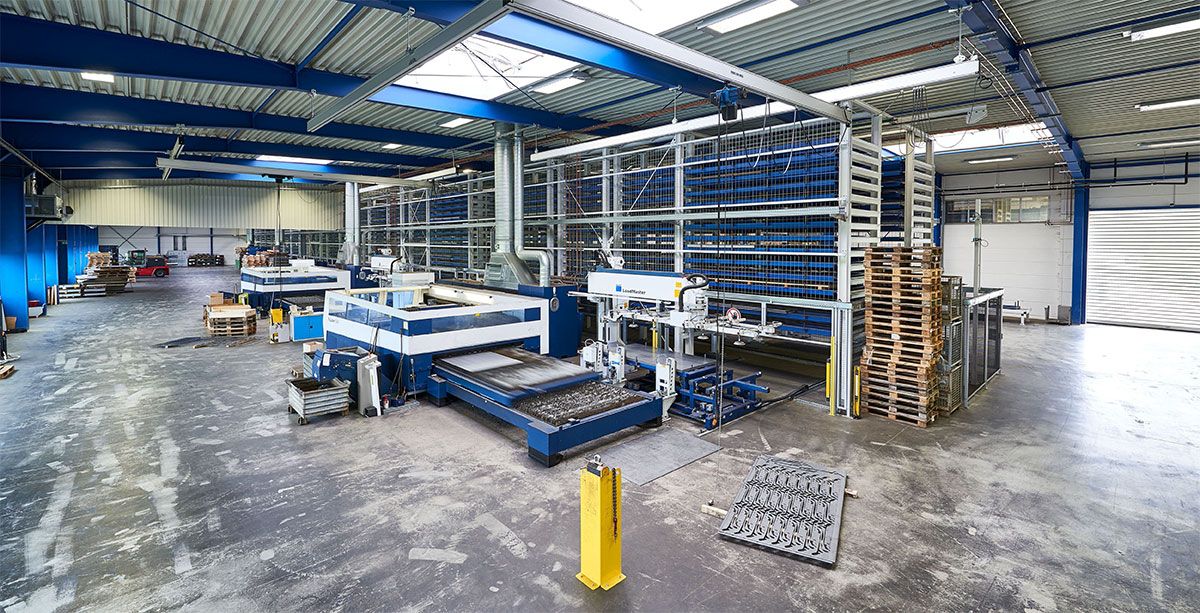
Dreeskornfeld has invested in a second automatic sheet metal storage system that is designed for four system pallet formats, including the maxi format XF.
Marcus Dreeskornfeld stands between the two warehouses. “A particular challenge was the calibration of the second sheet metal storage system. STOPA had to align the storage system exactly with the first system, parallel and on the axis. In addition, a minimum height of 4.5 meters was required for the lower edge of the bridge so that forklifts could pass under the shuttle route. For this reason, no supports may be placed in the forklift path.” The sheet metal storage systems, which work with fixed storage, supply the laser cutting machines. The daily turnover of raw material is between 50 and 60 tons. The medium-sized company, which was originally founded as a turning shop, does not store any leftover sheets.
Marcus Dreeskornfeld has climbed onto the bridge that connects the warehouses. He points to the transport carriage that shuttles between the systems at a speed of 30 meters per minute. “This connection makes it possible to supply all our laser cutting systems with all the material qualities we process in the KF, MF and GF sheet formats, regardless of which warehouse they are in. The only thing to consider is a longer travel distance, so that the material has to be requested earlier. We only need the XF format in the new warehouse because only there are machines that can process this sheet size.”
Dreeskornfeld relies on a high level of vertical integration. Its range of services includes 2D laser technology and 2D laser punching technology, folding, welding, deburring and straightening. In addition, there are mechanical production steps, surface treatment, assembly, construction, as well as the areas of warehousing and logistics. Christine Dreeskornfeld, managing partner alongside her brother, shows product samples from her company. “We manufacture cladding, housings, containers and welded assemblies made of sheet steel, stainless steel and aluminum. We develop ideas for sheet metal together with our customers, who are mainly based in the region.” The company mainly manufactures small and large series for agricultural technology, mechanical and plant engineering, vehicle construction and, more recently, to a considerable extent for conveyor technology manufacturers.
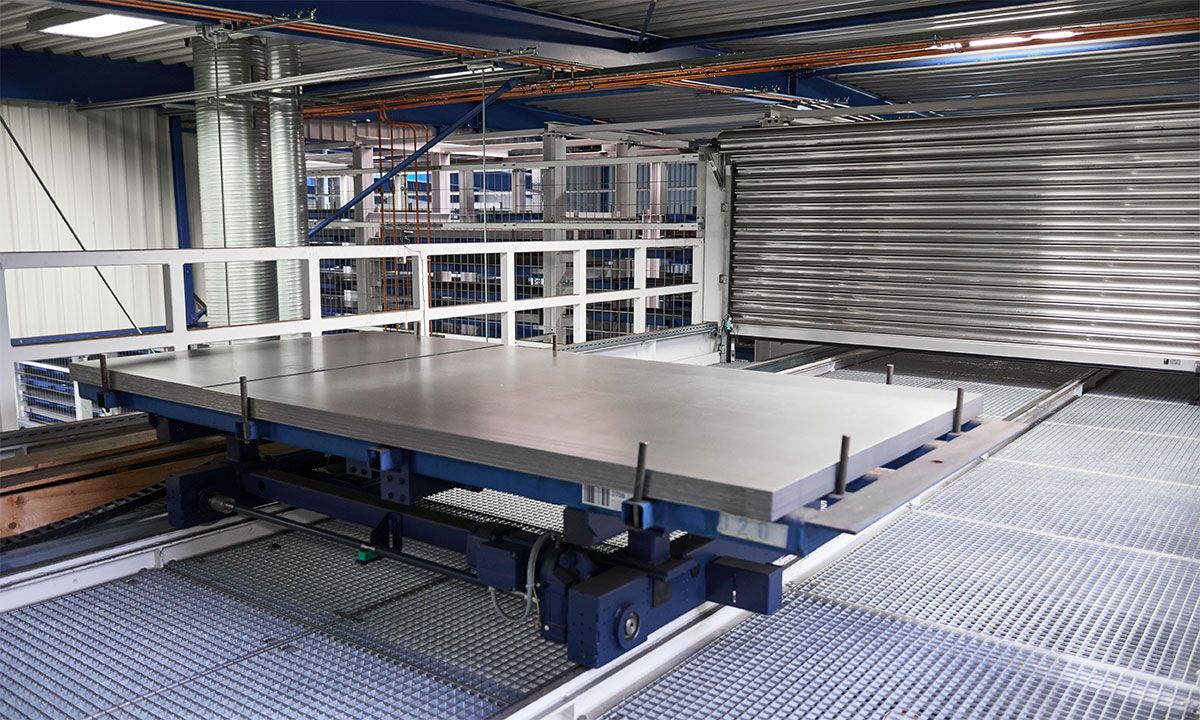
The shuttle line, which leads over a bridge, allows each laser cutting machine to be supplied from both storage systems.
Highlights der Lösung
- The new STOPA UNIVERSAL automatic storage system at Dreeskornfeld is designed for four system pallet formats, including the maxi format XF.
- All four formats can be stored via the goods-in station.
- Since a transport carriage connects the old and new sheet metal storage systems via a shuttle line, it is possible to supply all processing machines with sheet metal in KF, MF and GF formats from both systems.
One station for four sheet metal formats
One highlight of the new STOPA UNIVERSAL large-scale warehouse, which has 725 storage spaces, is its goods-in station, which can be used to store all four formats. STOPA, which specializes in customer-specific solutions, has developed a concept with a stationary scissor lift table. This is equipped with storage stamps that move in and out together depending on the format, as well as a chain conveyor. The conveyor has support tracks for the system pallets, which are arranged according to the sheet metal formats. A special feature is that the station is equipped with vertically movable sheet metal stops, which STOPA has installed on the long and short sides of the formats. Marcus Dreeskornfeld watches as the stops mounted above the scissor lift table move down. “Thanks to our software-controlled processes, the stops that would otherwise have to be inserted manually are no longer needed. Instead, a coordinate corner is automatically formed that is matched to the respective sheet size, and the forklift driver aligns the sheet stack with this corner when storing it, thus positioning it exactly. When the desired position is reached, this is confirmed by an optical display.”
The company, which is certified according to DIN EN ISO 9001 and 14001, employs around 100 people. It produces in three shifts, five days a week, and also on Saturdays if necessary. The STOPA UNIVERSAL warehouses supply twelve laser cutting machines. The manufacturer has automatically connected six machines to the new warehouse with the help of handling equipment, which is designed for a connection capacity of nine machines. Three systems are connected to the old system in the same way. Marcus Dreeskornfeld goes to the warehouse in the neighboring hall, which started operation in 1998 and was modernized in 2010 by a retrofit. “We do not supply the other three systems directly from the system, but by forklift. For this purpose, STOPA has installed a goods issue and goods receipt station in the first warehouse. Since these two stations are equipped with transfer points for the three sheet formats stored here, on-time delivery to the manually connected processing machines is also guaranteed.”
Increased system runtimes
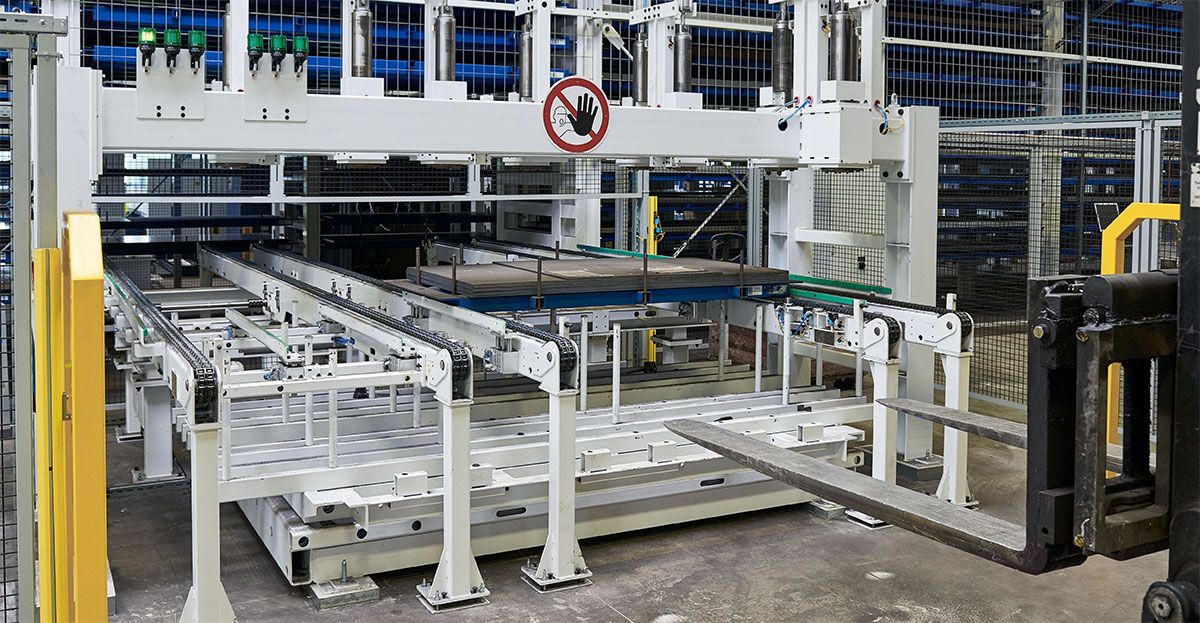
A highlight of the STOPA UNIVERSAL high-bay warehouse installed at Dreeskornfeld is its incoming goods station, which can be used to store all four sheet formats.
The bottom line for the operator is higher productivity. The two-mast storage and retrieval machine in the new warehouse, which is equipped with a three-part telescopic fork that can be extended on both sides for the four formats, also contributes to this. It reaches speeds of 150 meters per minute when driving, 23 meters when lifting and 25 meters when moving the fork. To avoid collisions during storage, the stacker crane, which has two loading heights, automatically checks the loading height of the storage locations above and below the selected storage location.
In view of the efficient solution, Marcus Dreeskornfeld draws a positive conclusion regarding the cooperation with STOPA. “By investing in the second automatic warehouse, we were able to increase the running times of the systems. In addition, we have a constant overview of the material stocks, which also means that there are no more incorrect bookings. On top of that, we benefit from less forklift traffic, high availability and from having underpinned our reputation as a center of excellence for sheet metal.«
Author: Jürgen Warmbol
Sales Contact Person
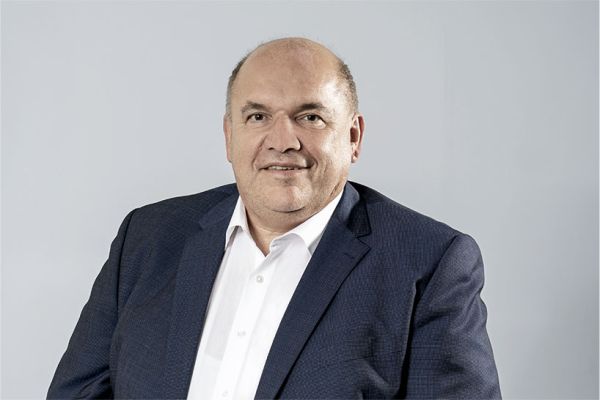
Holger Dehmelt
Sales Engineer Warehouse Technology
STOPA Anlagenbau GmbH
Industriestr. 12
77855 Achern-Gamshurst
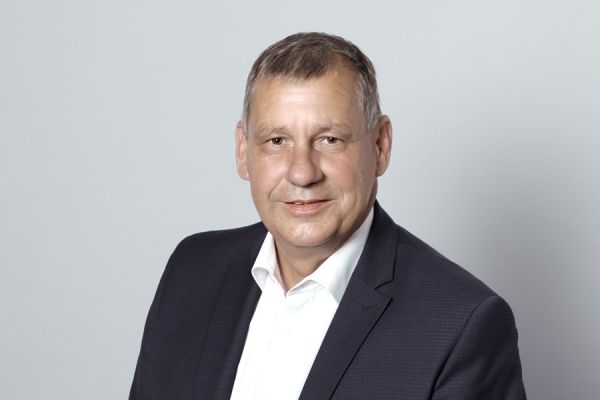
Rolf Eckhardt
Sales Engineer Warehouse Technology
STOPA Anlagenbau GmbH
Industriestr. 12
77855 Achern-Gamshurst
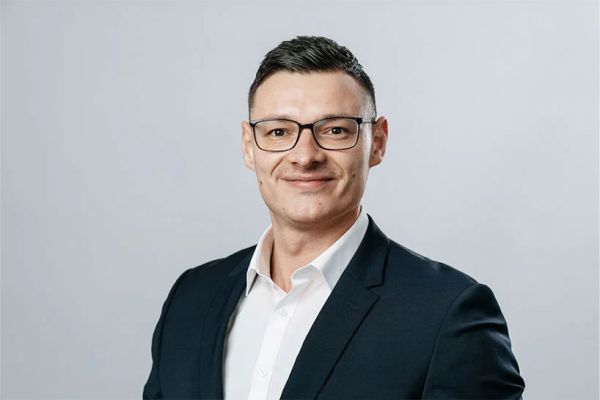
Andreas Pahl
Sales Engineer Warehouse Technology
STOPA Anlagenbau GmbH
Industriestr. 12
77855 Achern-Gamshurst