Custom Tower Storage System
ATMOS MedizinTechnik has invested in a STOPA ECO tower storage system. The limited space available in the production hall was a particular challenge for the operator, as it meant that a very compact solution that deviated from the standard was required. This called for a form of customization that only STOPA was able to offer.
Walter Baschnagel, Head of Process Organization, IT and Quality Management at ATMOS MedizinTechnik GmbH & Co. KG, based in Lenzkirch in the Black Forest, stands in front of the STOPA TOWER Eco, a single-sided sheet metal storage tower equipped with a retrieval system. “Our floor plan has grown over time. This is one of the reasons why we have such limited space in our factory hall. The challenge for STOPA was to integrate an extremely compact sheet metal storage system in this space, in the corner of the hall and under a sloping roof. Without this solution, we would have had to knock down walls.” Ralf Bausch, Head of Mechanical Production, shows photos from the past. ”Before the system was installed, the sheets were stored upright between stands, where some of them were deformed. Furthermore, we had several storage locations, which meant a lot of transportation.”
Faster access to the sheets
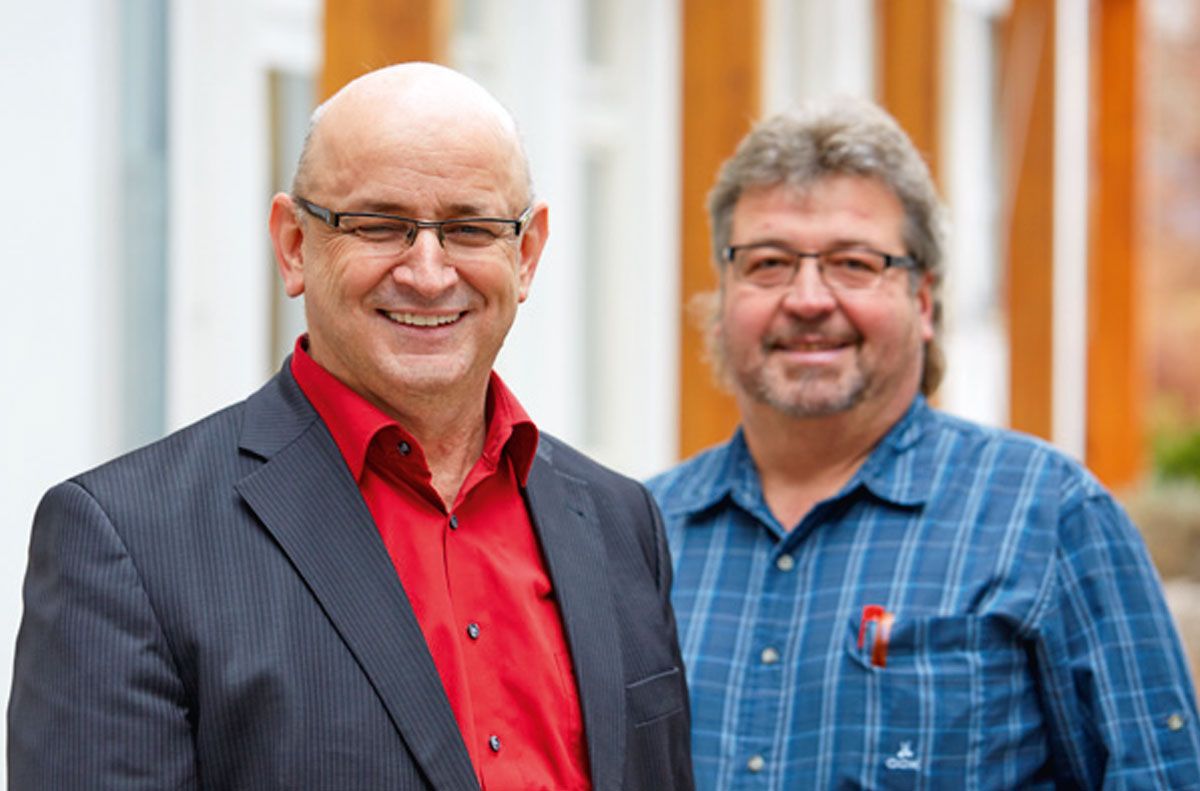
Walter Baschnagel, Head of Process Organization, IT and Quality Management (left), and Ralf Bausch, Head of the Mechanical Production Department, have a sheet metal storage system that is tailored to their limited space.
ATMOS chose to invest in a tower storage system from STOPA Anlagenbau GmbH, of Achern-Gamshurst, Germany. The system, which went into operation in October 2012, offers a cost-effective entry point to the automatic storage of flat goods thanks to its modular design. Designed for a payload of 1,200 kilograms per storage compartment and flat pallet, the STOPA ECO, which in this case is around four meters high and long and three meters wide, is suitable for companies that want to store a large number of materials in relatively small quantities. If there were no space restrictions, a system height of up to 6.4 meters would have been possible. In the shelf block, which is equipped with a fixed height grid and designed for a loading height of 60 millimeters per pallet, the operator achieves an optimal packing density and thus a high degree of space utilization. ATMOS had the two upper storage compartments set up for the larger loading height of 200 millimeters per pallet so that more material can be stored on a flat pallet. This corresponds to a doubling of the height grid, which means that, for example, more voluminous parts or sheets can also be stored on Euro pallets. The tower is loaded and unloaded on the long side using the stationary lifting beam that functions as a storage and retrieval unit. Bausch uses a flat pallet to demonstrate the processes. “We now have quick access to the sheets, better organization and, consequently, less time spent searching. Furthermore, there is hardly any material damage. Since the system is also located directly next to the punching machine, handling is very ergonomic.”
Company
ATMOS MedizinTechnik GmbH & Co. KG: Competence in medical air
ATMOS MedizinTechnik GmbH & Co. KG has its roots in the Kaiser Friedrich Apotheke, which was founded in Berlin in 1888. Thirty years after its founding, the pharmacy had become an oxygen center, which developed the first so-called suction, pressure and hot air apparatus for medical purposes in 1927. This was the beginning of ATMOS’ core competence. In 1942 the company, which has been trading under the name ATMOS since 1941, moved from Berlin to Freiburg im Breisgau.
Today ATMOS has its headquarters in Lenzkirch (Black Forest). With around 300 employees, the company is consistently expanding its expertise in innovative suction and drainage technologies for the operating and care sectors. It is also a leading global provider of ENT solutions and gynecology products, offering complete workplace solutions for the world market.
ATMOS has an annual turnover of around 14 million euros and sells its solutions globally through 13 subsidiaries and approximately 70 country representatives. ATMOS also supports its partners in the context of strategic alliances with special developments in the field of its core competence – medical suction and workflow optimization.
Ergonomic handling
The 18 materials stored in the STOPA ECO include aluminum, brass, stainless steel, sheet steel, materials for prototyping and plastic plates. The punching machine is manually supplied with sheets by its operator. First, the operator enters the number of the compartment of the flat pallet to be stored in the central control panel of the tower storage, which is equipped with an LCD display and a keypad, into the intuitive compact control system. The operator then confirms this command by pressing the button until the pallet has moved to the removal position. From the retrieved pallet, the employee effortlessly pulls the sheet onto the punching machine table. The advantages of ergonomic handling are particularly clear in view of the fact that ATMOS produces customized components in batch sizes of around five to 50 pieces and at the same time relies on a high level of vertical integration, which leads to frequent material changes. The operator places any remaining sheets back on the pallet, which he releases by pressing the corresponding button, whereupon it automatically returns to its storage compartment. Alternatively, the operator could have opted for the fully automatic control of the storage system that STOPA offers as an option.
Baschnagel points to the STOPA ECO. “The 23 storage spaces are reserved for specific materials. However, we do not store any additional sheets until we have used up the sheets on the flat pallets. This is because the batches can vary.”
ATMOS MedizinTechnik has invested in a STOPA ECO tower storage system. The company cites the limited space available in its factory as a particular challenge, which meant that a very compact, non-standard solution was required. This called for a form of customization that only STOPA was able to offer.
Due to the limited space available in the ATMOS factory, a very compact, non-standard solution was required.
Walter Baschnagel, Head of Process Organization, IT and Quality Management (left), and Ralf Bausch, Head of Mechanical Production, have a sheet metal storage system that is tailored to their limited space.
“We have a high demand for customized products and we want to manufacture each product from a single batch if possible.”
Reliably designed
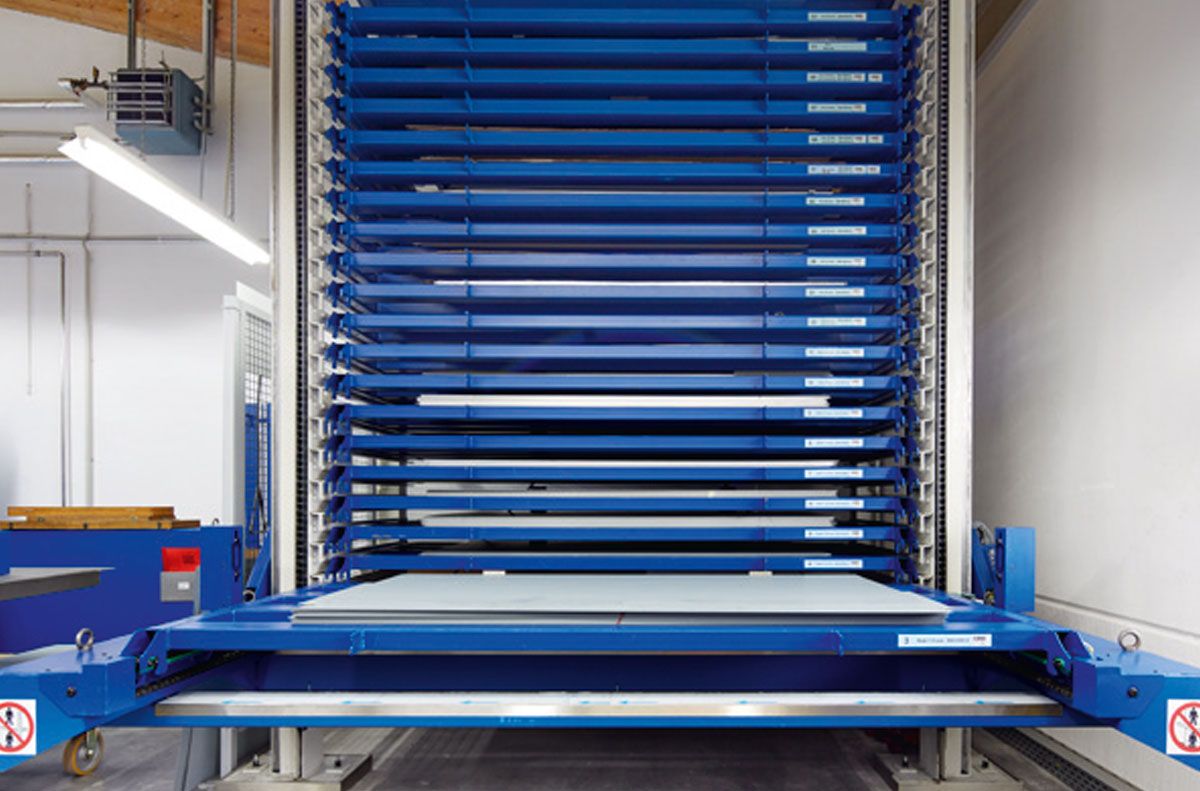
Due to the limited space in ATMOS’s workshop, a very compact, non-standard solution was required.
The STOPA ECO rack block, with its longitudinal connections and diagonal bracing, forms a compact and secure steel construction system. It is equipped with bolted pallet supports that have a push-through safety device on the rear side. STOPA has designed the 23 flat pallets of the storage system for a usable pallet area of max. 1,250 x 2,500 millimeters and thus for medium-format sheets.
The lifting gear of the stationary lifting crossbeam works with low-wear and low-maintenance roller chains, while the pulling and pushing device works with a roller chain that is equipped with pushers. An absolute and load-independent digital position-sensing system is used for height positioning. The lifting crossbeam, which is equipped with a loading height control and whose functions are reliably monitored by the control system, can reach speeds of up to eight meters per minute when lifting and four meters per minute when pulling.
Less physical labor
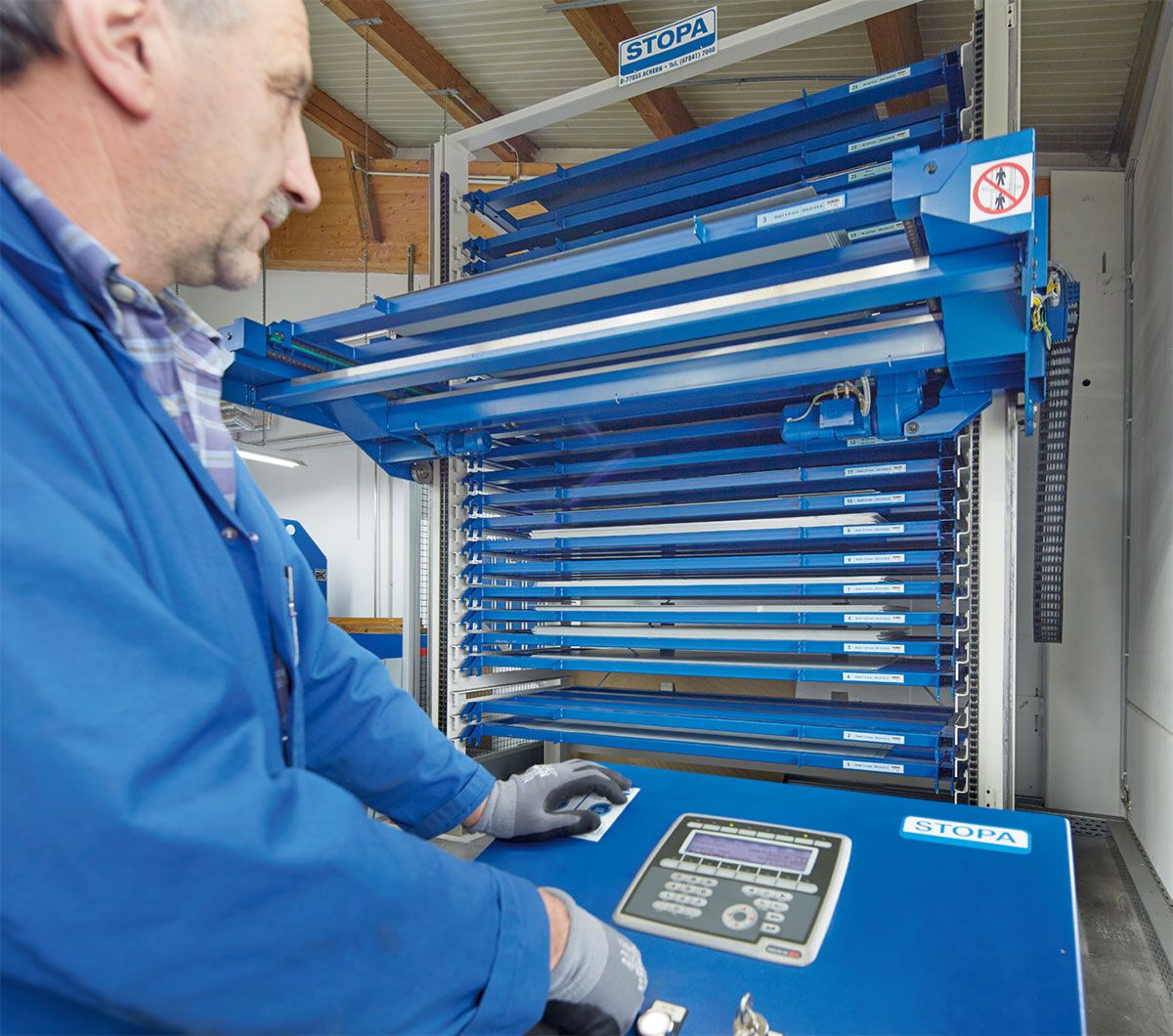
ATMOS now has quick access to the sheets, better organization and, consequently, less time spent searching.
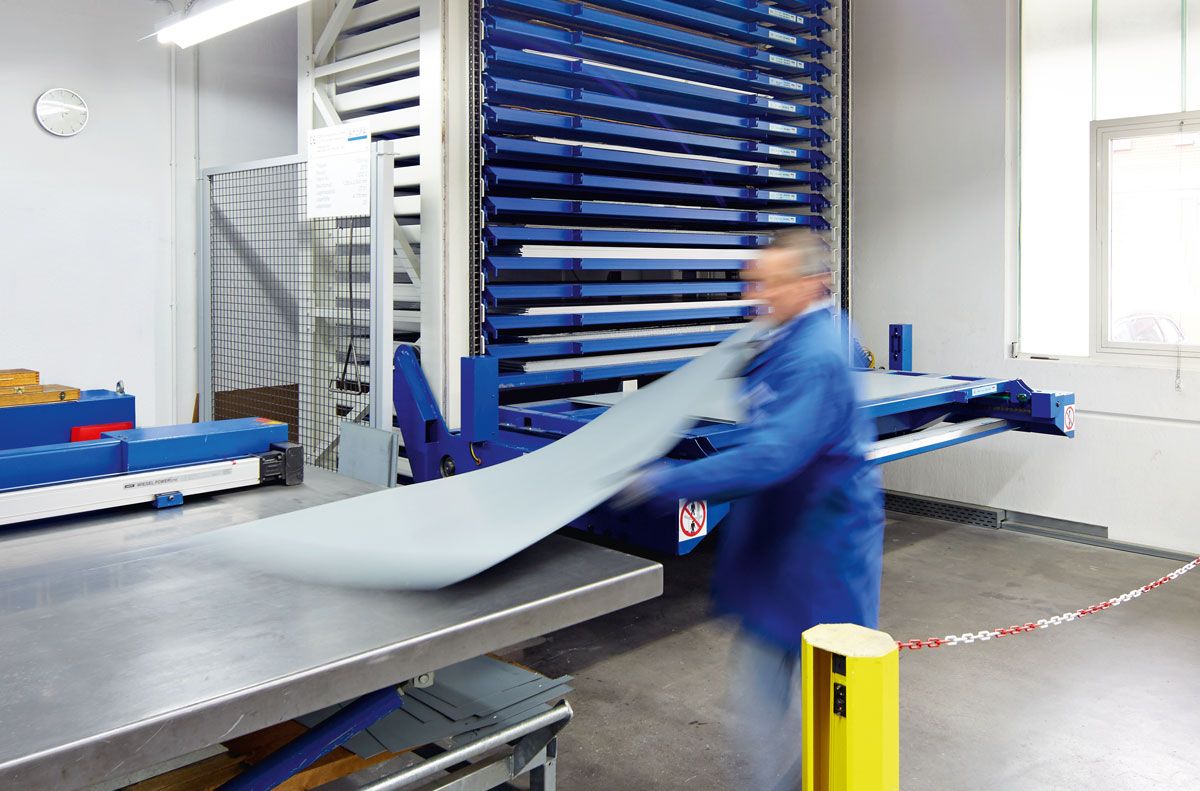
The fact that the tower storage system is located right next to the punching machine makes the handling very ergonomic.
ATMOS uses the STOPA ECO in a single shift. The system achieves an availability of almost 100 percent and handles around two tons of material per month. The operator expects a payback period of four years. “However, the decisive factor for the investment was a sustainable reduction in physical labor”, emphasizes Baschnagel. “Our plant operators benefit from this, and they can also achieve more in the same time. We became aware of sheet metal storage systems at a trade fair. We later spoke to a number of companies and ultimately chose STOPA because this company was the most flexible and offered a solution that was precisely tailored to our limited space. Other manufacturers did not want to or could not offer this form of customization.”
Autor: Jürgen Warmbol
Sales Contact Person
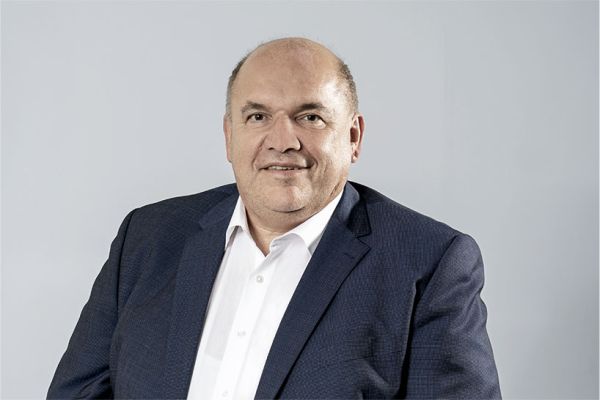
Holger Dehmelt
Sales Engineer Warehouse Technology
STOPA Anlagenbau GmbH
Industriestr. 12
77855 Achern-Gamshurst
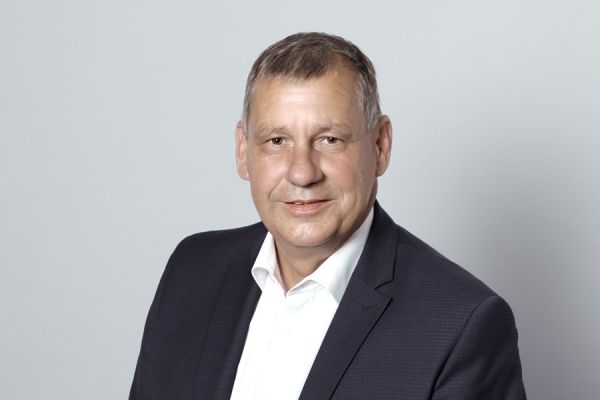
Rolf Eckhardt
Sales Engineer Warehouse Technology
STOPA Anlagenbau GmbH
Industriestr. 12
77855 Achern-Gamshurst
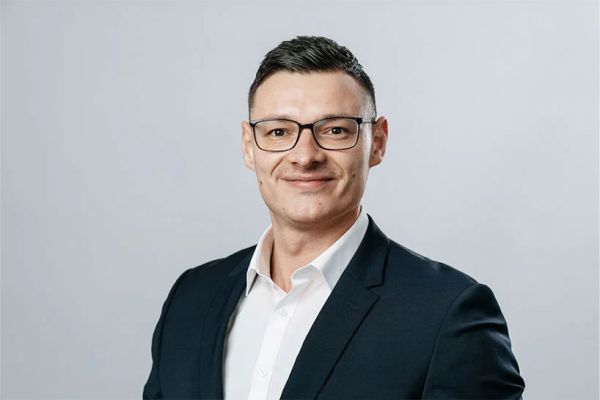
Andreas Pahl
Sales Engineer Warehouse Technology
STOPA Anlagenbau GmbH
Industriestr. 12
77855 Achern-Gamshurst