storage system “beats” cantilever arm
Florigo, a manufacturer of deep fryers and frying equipment, buffers its up to 6,000-millimeter-long raw sheet metal plates in two STOPA MONO storage towers. Previously, the operator relied on cantilever racks and floor storage. The advantages of the towers lie in the handling of the plates, which has become more ergonomic, safer, faster and thus more economical, as well as in better use of space.
In the production hall of Florigo Frying Equipment B.V. in Woerden, the Netherlands, you can see frying equipment on which employees are assembling the final components. Floor Goes, Technical Director at Florigo, runs his right hand over the structure of a deep fryer. “We place a lot of value on visually high-quality surfaces without joints or welds. This also applies to our large systems. That’s why we need sheets in the right dimensions and the right storage.”
With this in mind, Florigo invested in its first sheet metal storage tower in 2008, at the same time as moving into a new building. A STOPA MONO XF from STOPA Anlagenbau GmbH, Achern-Gamshurst, designed for the maximum format of 2,000 x 4,000 millimeters. Just one year later, the Dutch company had a STOPA MONO SF installed, a tower for special formats that allows them to store sheets up to 6,000 millimeters long in a compact and quickly accessible manner.
Higher storage density
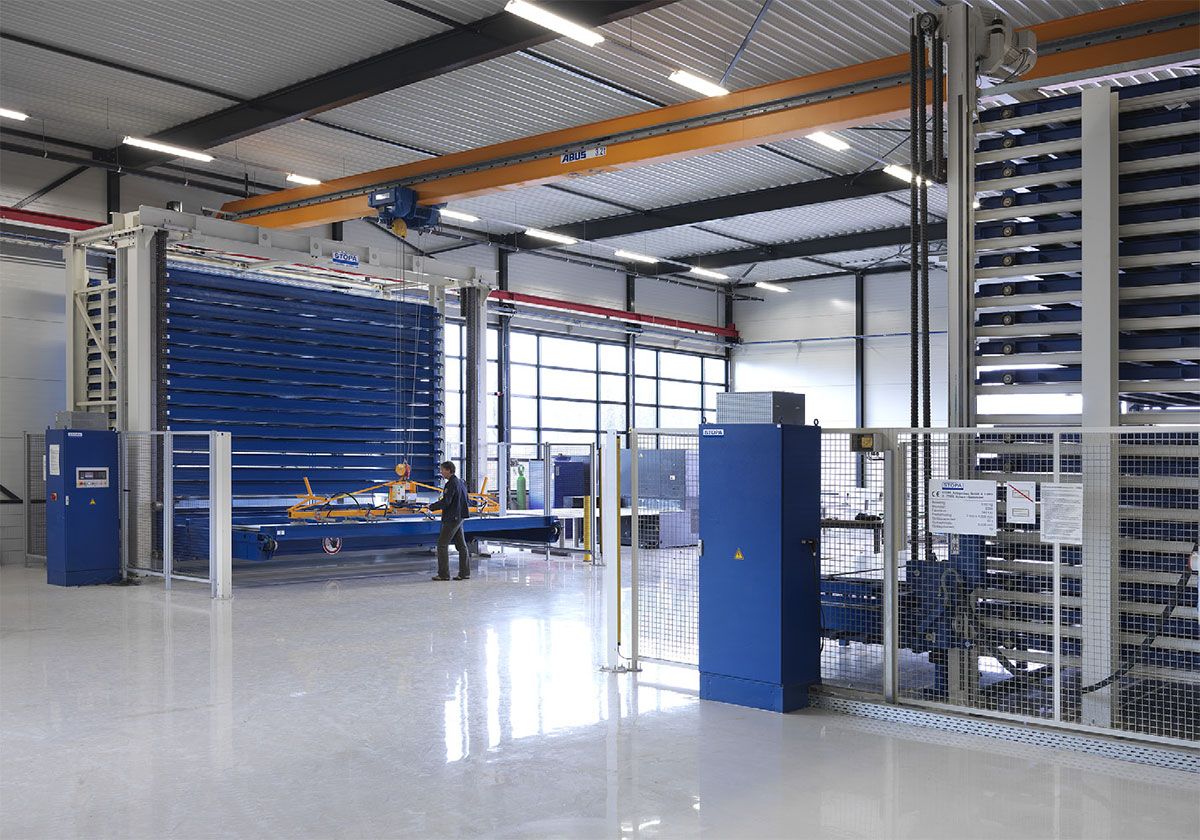
Florigo buffers its raw sheet metal in two STOPA MONO storage towers.
Previously, Florigo stored the sheets in cantilever racks and removed them manually. Now, handling has become more ergonomic, safer, faster and therefore more economical. Ries Goes, Florigo’s financial director, watches as the load beam of the STOPA MONO SF removes a cassette and measures the time with his wristwatch. Then he nods in agreement. “Back then, it took us five to ten minutes to remove a sheet. Today, it takes just one minute.” The changeover has brought other advantages. Damage to the visible surfaces of the sheets, which was already rare before, now no longer occurs at all. In addition, the operator benefits from better use of space, because large sheets were scattered on the floor in the old building.
Floor Goes stops at the two storage towers to explain that the systems differ not only in terms of the size of the sheets. “In the STOPA MONO SF, we use cassettes as load carriers and therefore achieve an even higher storage density than with system pallets.” The reason for this is that the sheets are placed between the profile of the cassettes, which ensures the rigidity of the load carriers. In this respect, the number of sheets has no influence on the overall height of a cassette, as long as the sheets do not protrude beyond the profile. When using system pallets, on the other hand, the height of their profile must be added to that of the sheet stack. So, regardless of the loading height, pallets in a sheet metal warehouse have a wider distance between them than cassettes, resulting in more storage spaces in a cassette warehouse.
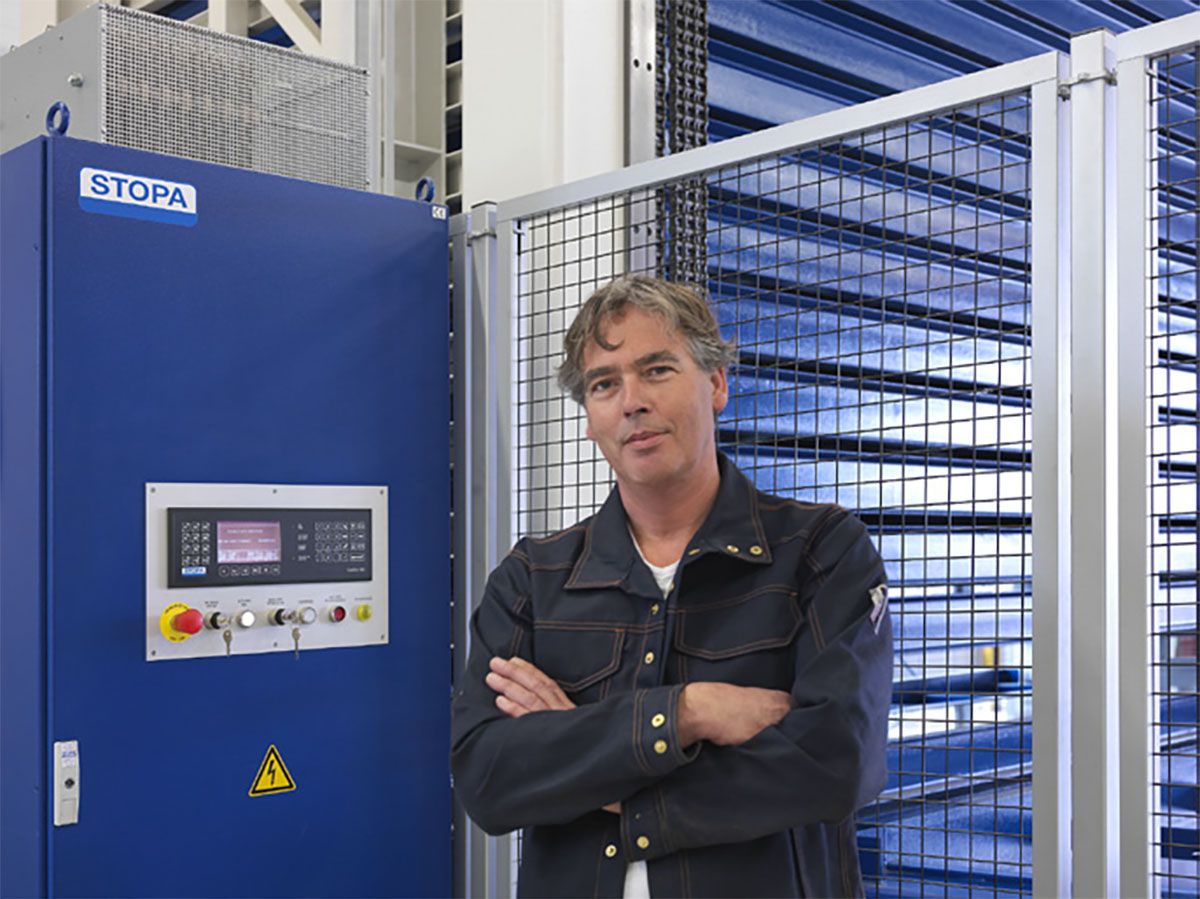
Floor Goes, Technical Director at Florigo, places great value on visually high-quality surfaces without joints and welds, and therefore requires sheets in the appropriate dimensions and the matching storage systems.
Company
Florigo: The recipe for golden-yellow French fries
Florigo Frying Equipment B.V., Woerden (Netherlands), is a leading manufacturer of deep fryers and frying systems. According to the company, these are ‘the recipe for golden-yellow French fries’. Technological innovations are constantly being incorporated into the growing range of products offered by the company, which employs 25 people. Florigo acquires customers in the fast food, snack and cafeteria industries, as well as among fish restaurants and other catering establishments. The deep-frying equipment meets the highest Dutch testing requirements in terms of efficiency and safety. In addition, Florigo pays attention to low energy consumption when developing new products. The family business, which was founded in 1951 by Floris Goes Senior, is now managed by his sons Floor, Ries and Ad Goes. The brothers produce around 140 fryers and deep-frying systems each year, which they sell primarily in the Netherlands, as well as in Belgium, England and Ireland. However, they also have customers in Germany, Greece and Spain, as well as worldwide through English representatives.
Handling long and short trays
The STOPA MONO SF from Florigo is equipped with 18 special format cassettes. The load carriers ensure safe storage thanks to the rollers mounted on the front and the inclined support of the storage locations. The tower, which STOPA has designed for heights of up to ten meters, is around 5.6 meters high, 7.6 meters long and 5.7 meters wide at Florigo. The maximum permissible payload per cassette is 5,000 kilograms, and the loading height, which is monitored by a light barrier, is 90 millimeters. Both towers contain rust-free steel with a brushed surface up to four millimeters thick, normal steel up to five millimeters thick, and aluminum sheets up to three millimeters thick. The company works with fixed storage and manual storage organization, without recording the quantities.
A manually operated gantry crane is currently using a vacuum suction gripper to transport a six-meter-long sheet to the STOPA MONO SF and place it in the cassette in front of it. Floor Goes: “We use the crane to store and retrieve sheets that are over two and a half meters long, as well as for transportation from the goods-in area to the towers and from there to the processing machines. For smaller formats, which are stored and retrieved by two operators, there are mobile plate tables.”
Florigo only manually transfers the plates at the special format storage tower, where the operator does not use a storage platform with storage stamps. Before a forklift delivers a sheet metal package, metal blocks are placed under the very stable and robust two-mast load crossbeam, which is equipped with a low-maintenance pulling and pushing device and can reach a speed of up to twelve meters per minute when lifting and six meters per minute when moving the forks. The crossbeam then lowers a cassette until the upper edges of the trestles are above the crossbeams of the cassette. Once the forklift has deposited the sheets, the crossbeam lifts the cassette, complete with sheet package, from the trestles. The forklift holds longer packages at an ergonomic height directly in front of the load crossbeam. Two employees pick up the sheets individually and stack them in the cassette.
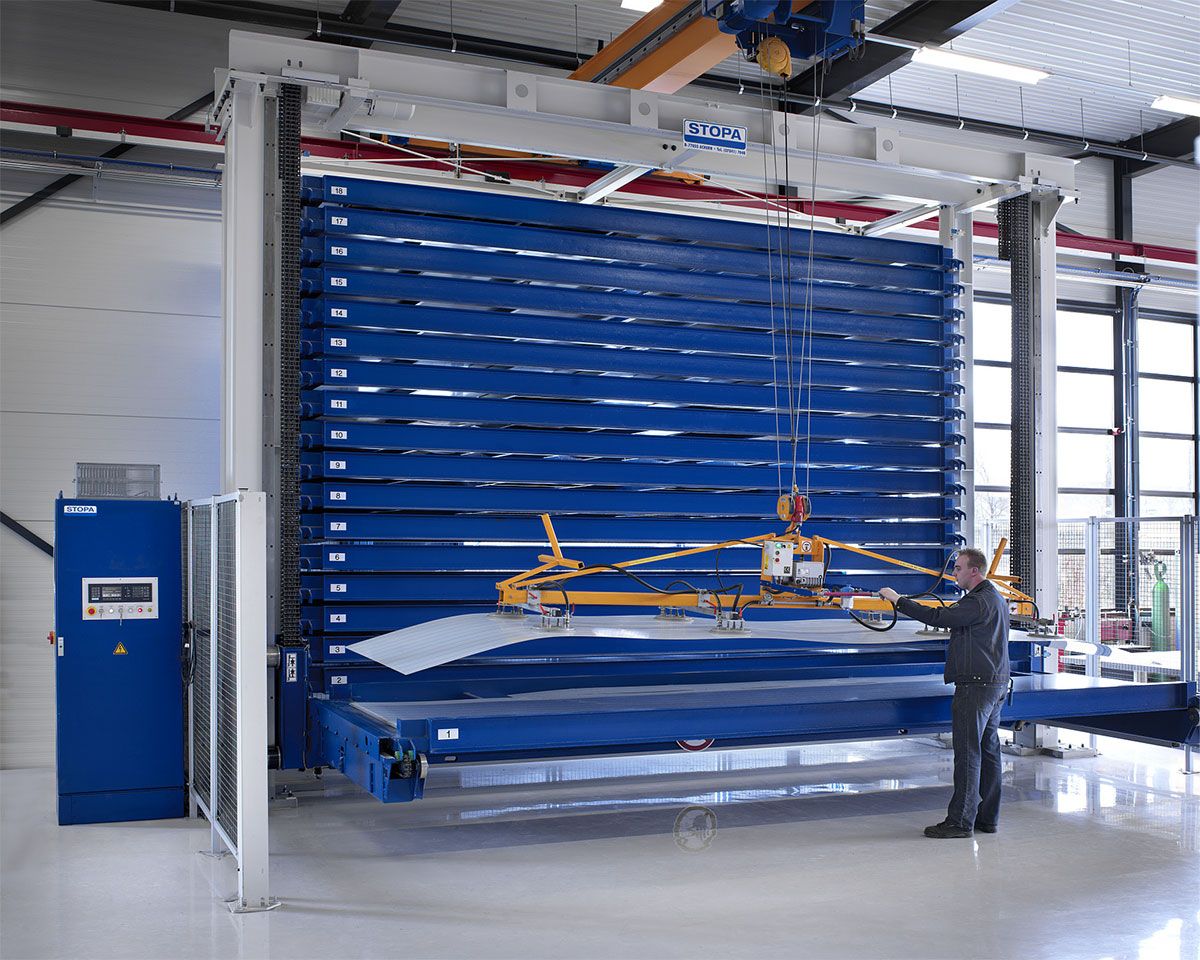
The use of sheet metal storage towers has made handling the sheets more ergonomic, safer, faster and therefore more economical.
Real-time soft PLC as new control system for STOPA sheet metal storage
Controlled by a real-time soft PLC integrated into an industrial PC. It replaces the old control system, which the manufacturer no longer offers. While the PLC controls the system components of the storage system, the PC displays the system status. The system is also operated via the PC and easy-to-understand function keys. The status of the load traverse can be read at any time in plain text on the 12-inch TFT display of the ergonomic control panel. Additional comfort is provided by more extensive diagnostic options and the remote maintenance software PC Anywhere, which allows quick error analysis and service via modem. Furthermore, the control system can be connected online to a higher-level computer system. Further advantages of the control changeover are the conversion to bus components. In addition, there is now a uniform user interface for all storage systems, except for the STOPA TOWER Eco. Furthermore, the control system also performs safety tasks and supports the new concept of “modular from small to large”.
A mix of manual and automatic processes
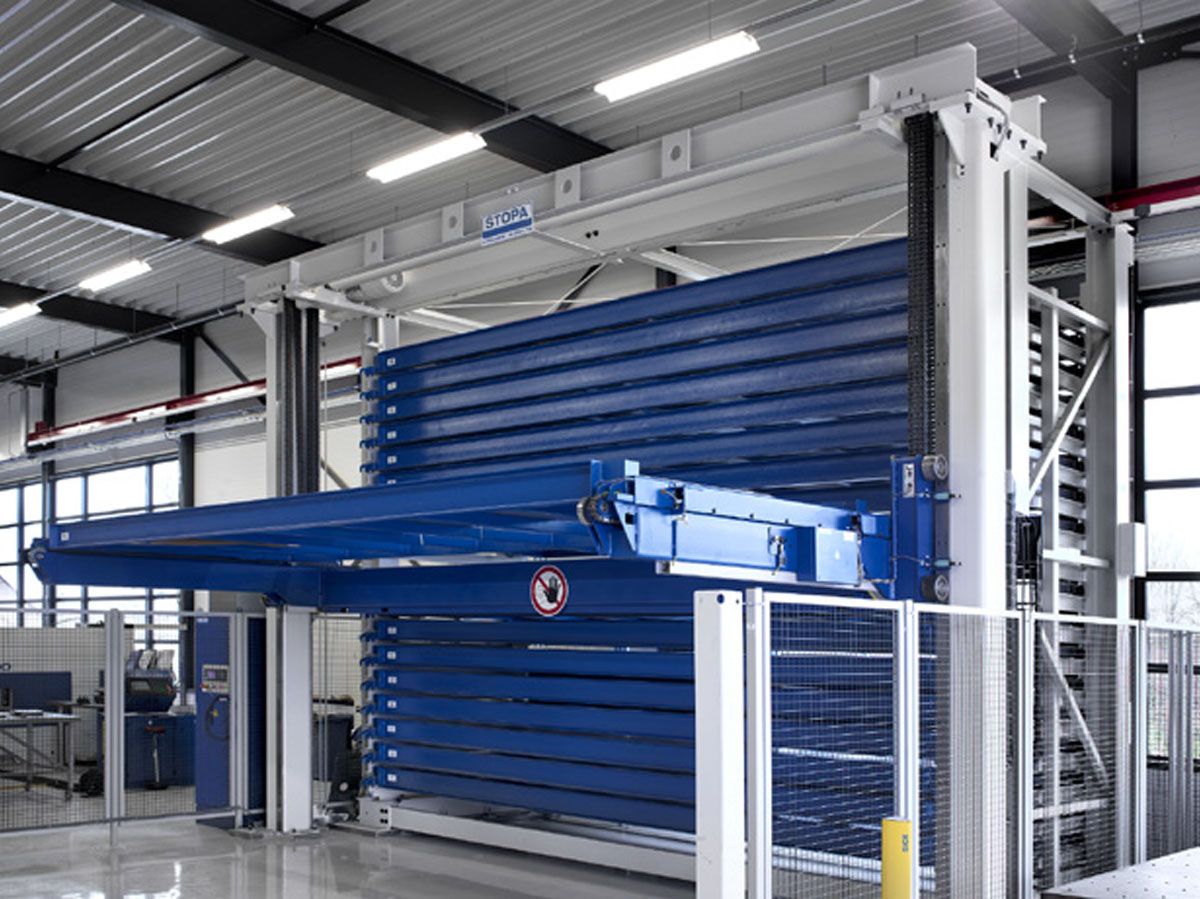
The STOPA MONO SF can hold sheet metal plates in special formats up to 6,000 millimeters long.
On the other hand, the STOPA MONO XF is used to place entire containers on a storage platform that has fixed-height storage stamps. The tower’s load crossbeam, which previously lowered a system pallet with its longitudinal beams between the stamps, lifts the sheet metal stack. The tower is about 5.5 meters high and long, and 5.1 meters wide. Each of its 19 flat pallets can hold a payload of 3,000 kilograms. After loading, the operator releases the load carrier, which then automatically returns to its compartment. Optionally, the pallets can be equipped with stops that make loading easier and serve as a shifting protection.
Floor Goes lends a hand when an employee wants to place a larger piece of scrap metal on a pallet. “By storing scrap metal in the towers, we are increasing the storage density even further. At the same time, we are reducing waste. This is an important point in view of the expensive stainless steel material.” If a cassette or pallet intended for storage is almost empty, the operator places the new material at the bottom and processes the sheets that have been in stock for longer first. If Florigo did not use the FIFO (first-in/first-out) method, the plastic film used to protect the sheets would be difficult to remove later. In addition, old sheets would be likely to become scratched over time.
The operator of the STOPA MONO SF looks at a list to see which cassette he has to remove the requested sheet from. Then he releases the process at the control panel. The load crossbeam is positioned at the storage compartment via an absolute encoder, which makes it unnecessary to approach a reference point, pulls out the cassette and lowers it to an ergonomic removal height. Ad Goes, General Director at Florigo, says: “The control system displays all the input steps to the operator in plain text and allows the tower to be stored and retrieved at the push of a button. We can store up to ten retrieval orders.” The company uses a freely programmable control system for which STOPA offers a warehouse management system that automatically provides an optimal overview of the warehouse. Error diagnostics are possible using queries and detailed messages in plain text.
Floor Goes looks around his production area with satisfaction. The storage towers, each consisting of a compact block and braced lengthwise and diagonally, allow for a high utilization of space and only take up a small portion of the valuable production area. “Our decision to go with the STOPA MONO sheet metal storage system was the right one. There is no more sheet metal lying on the floor where it could disrupt the production processes. All the sheets are stored in the towers, and we work more efficiently.«
A future-proof solution
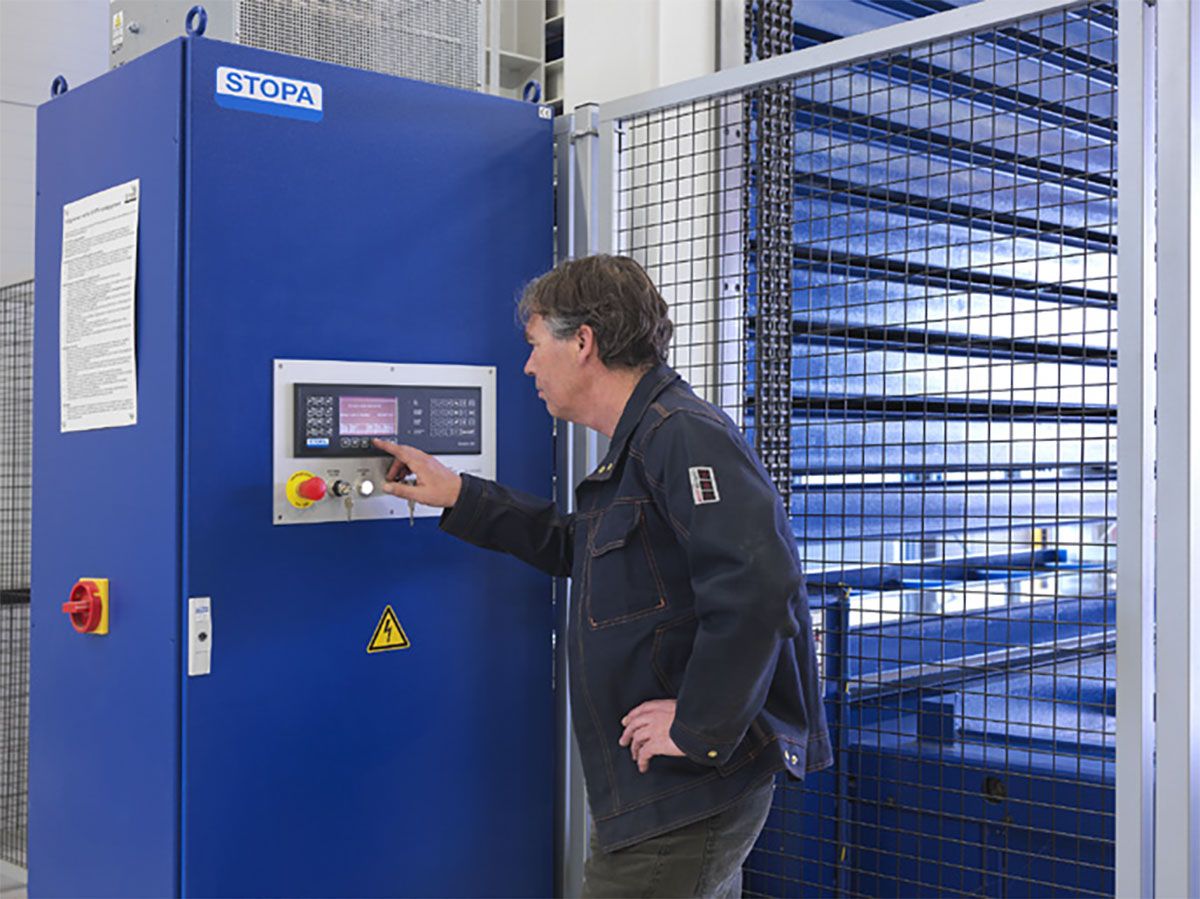
The control system displays all the input steps in plain text, allows the tower to be stored and retrieved at the push of a button, and can store up to ten retrieval orders.
Andreas Lamberth is observing the processes on the STOPA COMPACT II, which was launched in mid-2015. “The decision to go with such a solution was predetermined by the desired level of automation. In view of our experience with the TKL, which runs with high availability, we also decided on STOPA when selecting the large-scale storage system.” Another factor in favor of STOPA was that no interface problems between the storage system and the processing machines were to be expected. This is an important point, especially since the system works unmanned with automatic material changes on Friday evenings.
Peter Lamberth leans back in his chair at the main control panel of the STOPA COMPACT II. “Everything works wonderfully. The automatic storage system is future-proof, because there is space for almost 50 more pallets and an additional machine can be connected. In addition, three-shift operation is possible. On top of that, we can continue to use our old tower storage system.”
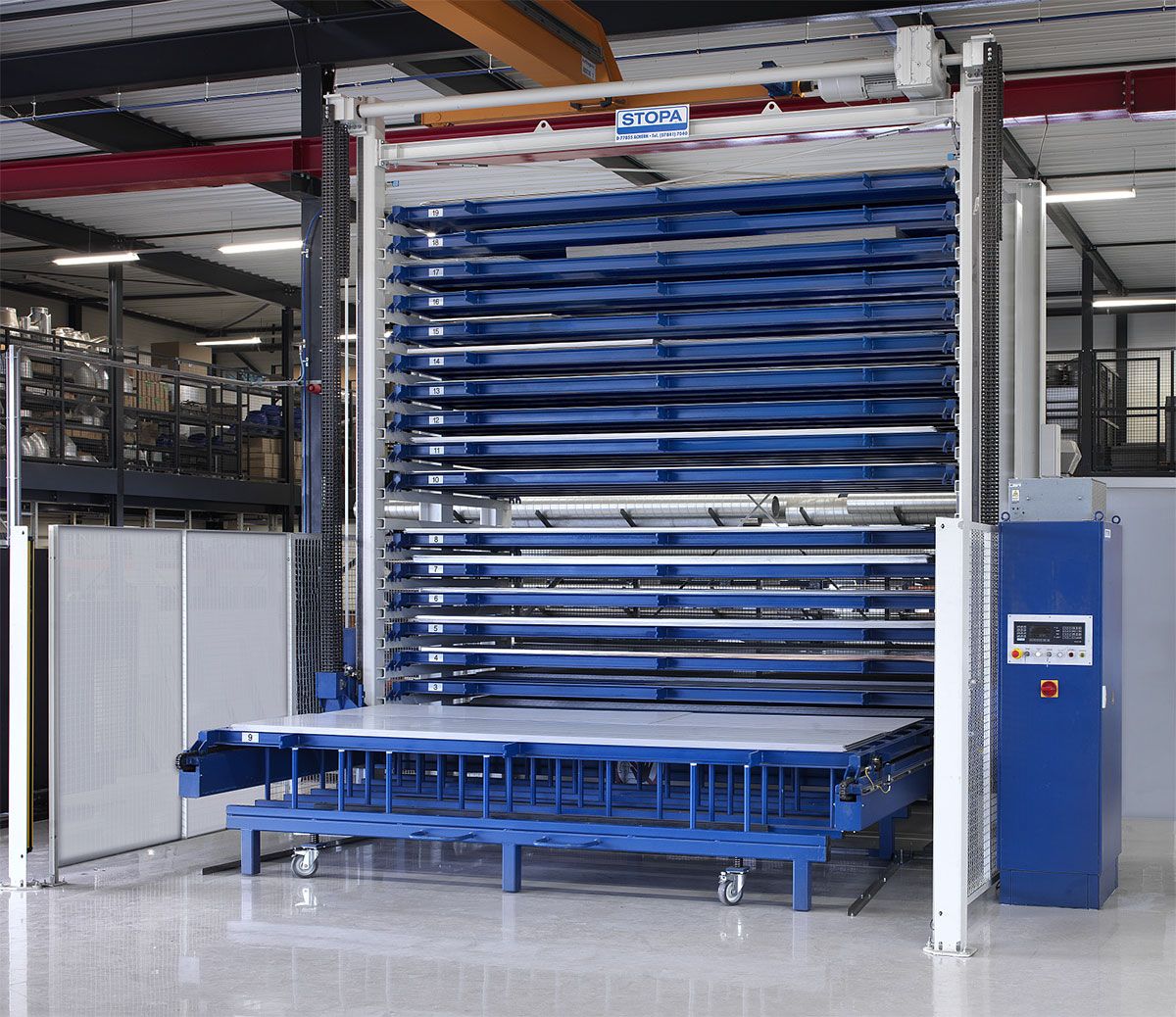
Before investing in the STOPA MONO storage towers, Florigo needed five to ten minutes to remove a sheet. Today, it takes just one minute.
Author: Jürgen Warmbol
Sales Contact Person
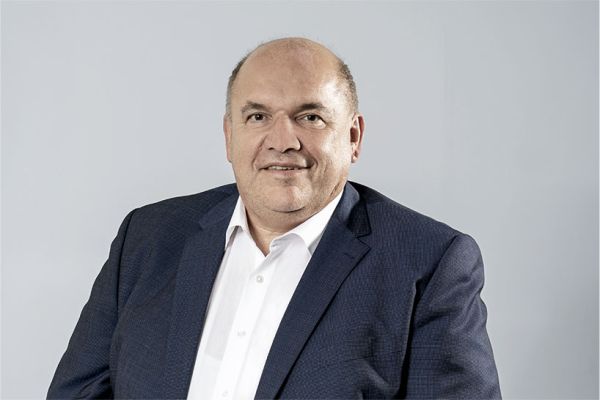
Holger Dehmelt
Sales Engineer Warehouse Technology
STOPA Anlagenbau GmbH
Industriestr. 12
77855 Achern-Gamshurst
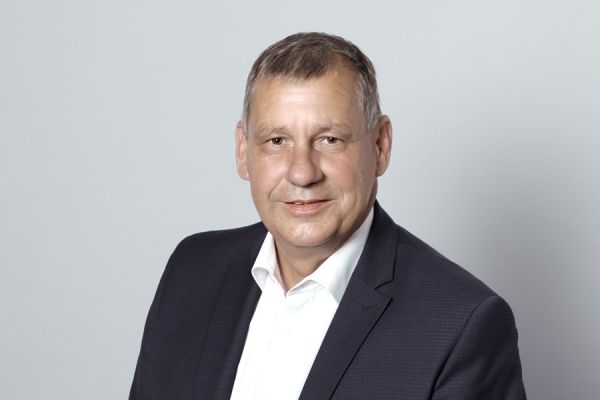
Rolf Eckhardt
Sales Engineer Warehouse Technology
STOPA Anlagenbau GmbH
Industriestr. 12
77855 Achern-Gamshurst
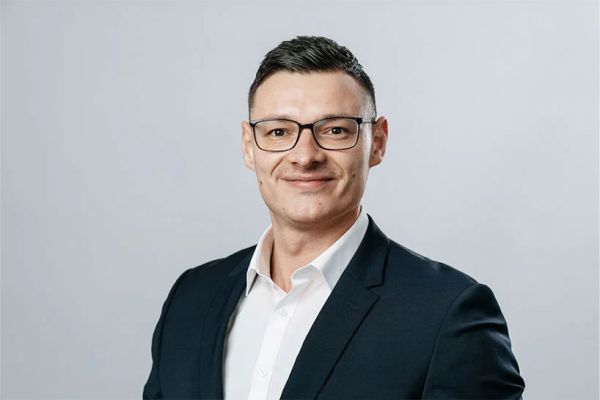
Andreas Pahl
Sales Engineer Warehouse Technology
STOPA Anlagenbau GmbH
Industriestr. 12
77855 Achern-Gamshurst