Double the performance
By using two storage and retrieval machines, RIKA Blechkomponenten GmbH has increased the performance of its STOPA COMPACT II automatic storage system and at the same time created redundancy. In addition, the operator benefits from greater flexibility and process reliability, as well as from unmanned and semi-unmanned shifts at night and at weekends.
Visitors to the sheet metal warehouse of RIKA Blechkomponenten GmbH in Micheldorf (Upper Austria) are presented with an unusual sight, as two storage and retrieval machines operate in one aisle. Each controlled by its own PLC, they are able to process their orders independently of each other. Both RBGs can serve practically all 1,072 storage locations in the system, which is approximately 73 meters long, 6.5 meters high and 5.5 meters wide. The only exceptions are the outer 38 storage blocks, which are arranged in two rows and can only be reached by one of the RBGs at each end of the aisle.
High availability and time savings during setup
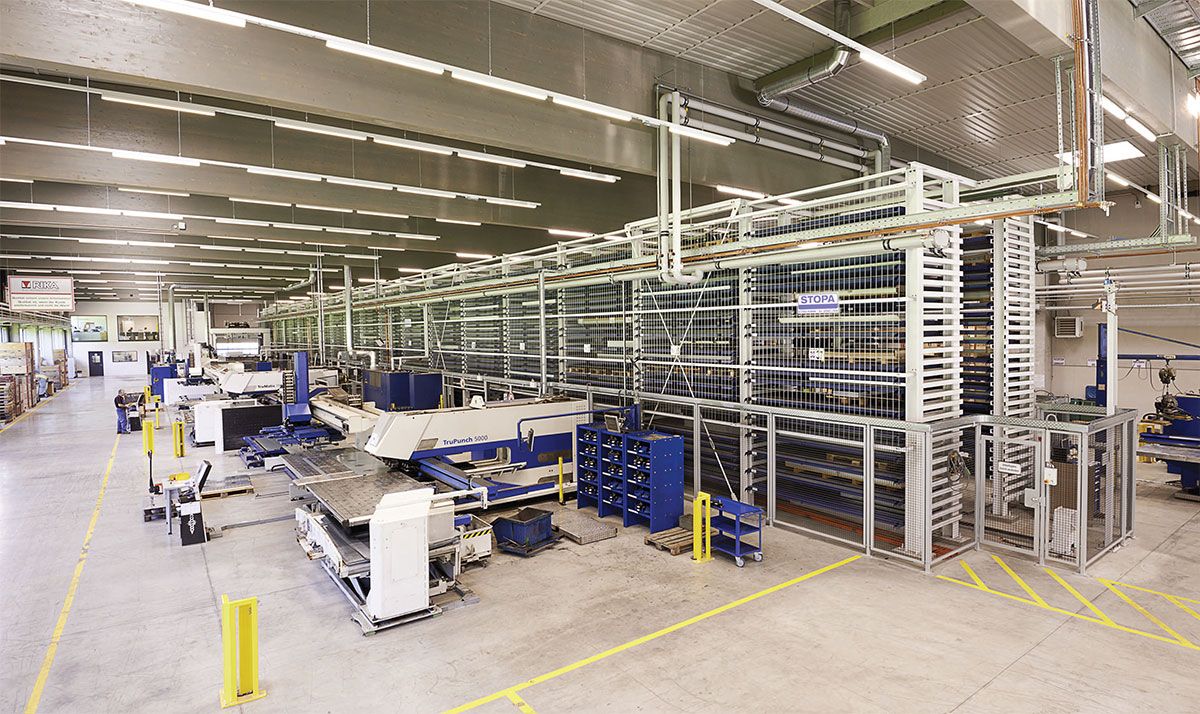
By investing in a STOPA COMPACT II sheet metal storage system, RIKA also benefits from greater flexibility and process reliability, as well as from unmanned and semi-unmanned shifts at night and on weekends
Reinhard Trippacher, head of purchasing at the company, stands in front of the automatic storage system supplied by STOPA Anlagenbau GmbH, Achern-Gamshurst, which is currently well stocked with sheet metal weighing a total of 820 tons. The system control is currently instructing an RBG to move to a peripheral position so that the second one has free access. “We chose the solution with two RBGs mainly because of the almost doubled performance and the reliability. We need the significantly higher performance in the provision of material, especially in the day shift, but the very high availability around the clock, because we already work in three shifts due to our order volume.” At night, during the low-manpower shifts, and at weekends, when the sheet metal production runs unmanned, the on-call service also benefits from the availability. To further ensure the availability of the system, RIKA has concluded a maintenance contract. It includes a teleservice for the system control via remote diagnosis via the STOPA TelePresence Portal.
Heinz Kohlbauer, head of cutting at RIKA, points to a sheet metal package lying on a transport trolley. “Here you can see that the use of the storage system – compared to the previous forklift traffic – means that hardly any material is damaged and safety is increased at the same time. What’s more, we now need significantly less time to set up because the machines connected to the storage system automatically request the sheets.” The operator returns residual sheets, semi-finished products and residual grids to the system, with the exception of three systems from which he removes the parts manually.
Highlights of the solution
- Increased performance
- Redundancy created
- More flexibility
- Higher process reliability
- Well-thought-out energy management
Sophisticated energy management
The new STOPA COMPACT II offers more pallet spaces than its predecessor for the same storage volume, as two storage compartments are usually gained for each rack block due to reduced upper and lower approach dimensions.
Another highlight of the STOPA COMPACT II is its sophisticated energy management system, which enables energy to be saved. For example, regenerative energy that is generated when the crossbeam is lowered can be used directly for the drive motor via an intermediate circuit coupling. This process requires intelligent drive control and is particularly effective when several drives of the stacker crane are in use at the same time. RIKA also uses the optional option of feeding the regenerative energy back into the power supply system, which would otherwise be lost because braking resistors would convert it into heat loss.
The fact that STOPA now uses a more compact crossbeam and two powerful, lightweight gear motors instead of a heavy drive motor, thereby reducing the overall weight by around half a ton, also contributes to energy savings.
Trippacher opens a file on his laptop. “The energy management of the storage system is in line with our thinking in terms of resource conservation. That’s why we also paid attention to low energy consumption when planning the hall. For example, universal cooling interfaces cooled by well water eliminate the need for normal electric cooling units, which means that we save 800,000 kilowatt hours of electricity a year and emit 770 tons less CO2. On top of that, we have our fixed costs under control.«
Variable acceleration
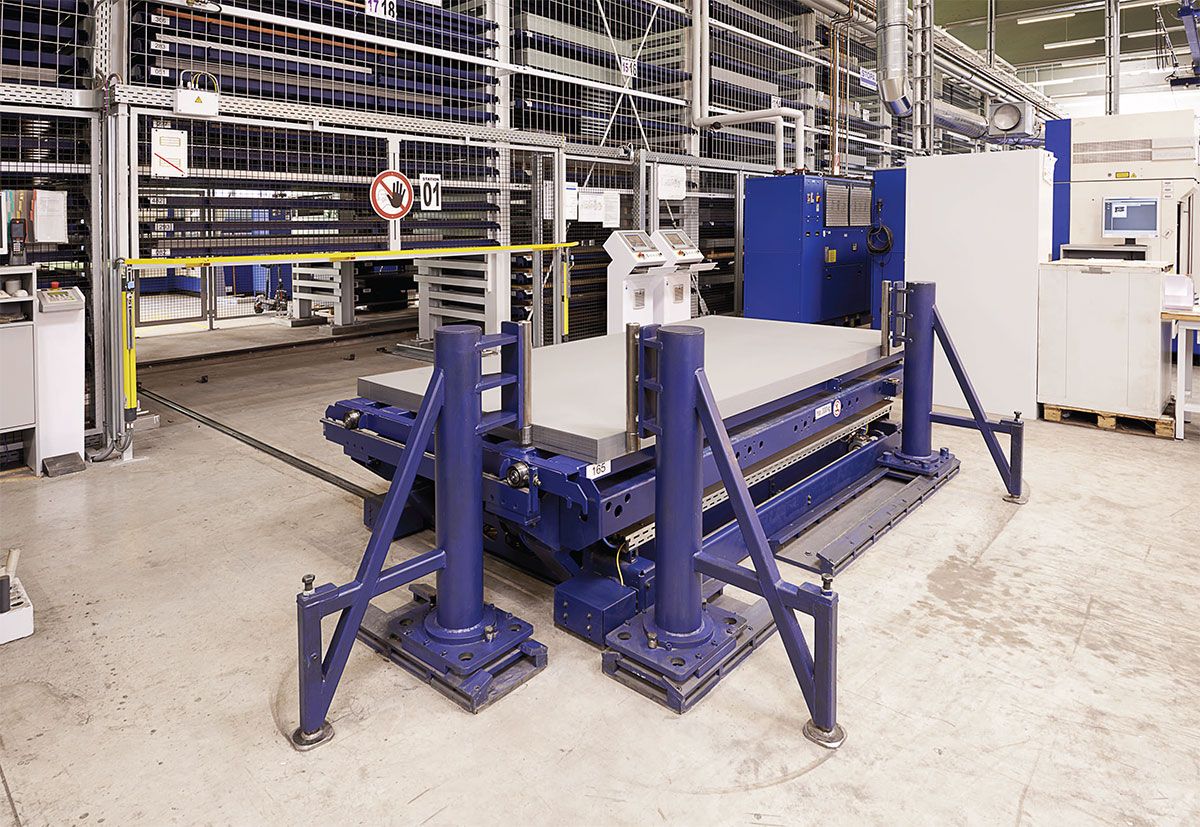
Compared to the previous forklift traffic, the use of the warehouse means that hardly any material is damaged and safety is increased at the same time
Trippacher also emphasizes the possibility of being able to accelerate the RBG variably: “We use this flexibility to prevent the material from slipping and to reduce energy consumption again. The basis for this is the reduction values that we store in the relevant article numbers.” All in all, these measures also increase process reliability. On the other hand, the system works with maximum acceleration when the material is not at risk of slipping or when the RBG is empty. In addition to these advantages, the manufacturer has reduced the overtravel dimensions on the RBG so that the automatic warehouse is more compact overall.
Apart from that, the 720 flat pallets on which RIKA stores large, medium and small format sheets in the STOPA COMPACT II with a maximum payload of 3,000 kilograms each run more smoothly than in the previous generation. This has further minimized the risk of sheets slipping. The operator benefits from more precise positioning, which is also based on redundant recording of the height of the load beam, from even greater process reliability and from a longer service life thanks to minimal wear. The load beam also works with an electronic synchronous shaft instead of the conventional mechanical one, which results in a smaller overall height and again less dead weight.
Another new feature is that the load cells of the patented weighing system are integrated into the pallet surface, which significantly reduces the weighing time and increases the number of possible productive cycles per shift.
The STOPA COMPACT II also scores points for low maintenance, which is based, among other things, on a compensating lifting chain tension, more precise lifting guide rollers and a reduced range of parts. As a result, maintenance costs and downtimes are reduced. Kohlbauer points to the clean floor of the system. “Since we also do not need any excavation hydraulics on the weighing system and thus no leaks can occur, the warehouse also works more ecologically.”
High product and delivery quality
The go-ahead for the STOPA COMPACT II, designed for different loading heights, was given at RIKA at the beginning of November 2013. Kohlbauer is standing in front of one of the system’s 20 stations. “STOPA assembled the warehouse in one step, but due to the tight schedule, it initially operated it with only one crane and connected only one TruLaser 5030 CoolLine. The remaining seven sheet metal processing machines – laser cutting systems, punch-laser and punching machines from TRUMPF – were connected from the end of November 2013 to March 2014. Since all the trades were well coordinated and the fitters were very motivated, the installation went very smoothly.«
Before deciding on the STOPA COMPACT II, which handles around 7,000 tons of sheet metal per year, RIKA had visited various sheet metal storage systems. In addition to the advantages already mentioned, Trippacher sees another point in favor of the chosen solution in view of the numerous machines connected to it. “There were no interface problems between STOPA and TRUMPF. We would not have expected that from a different combination of suppliers. It is equally positive that we can meet all deadlines with the help of the storage system. This means that our customers not only buy a high-quality product, but also a corresponding quality of delivery. «
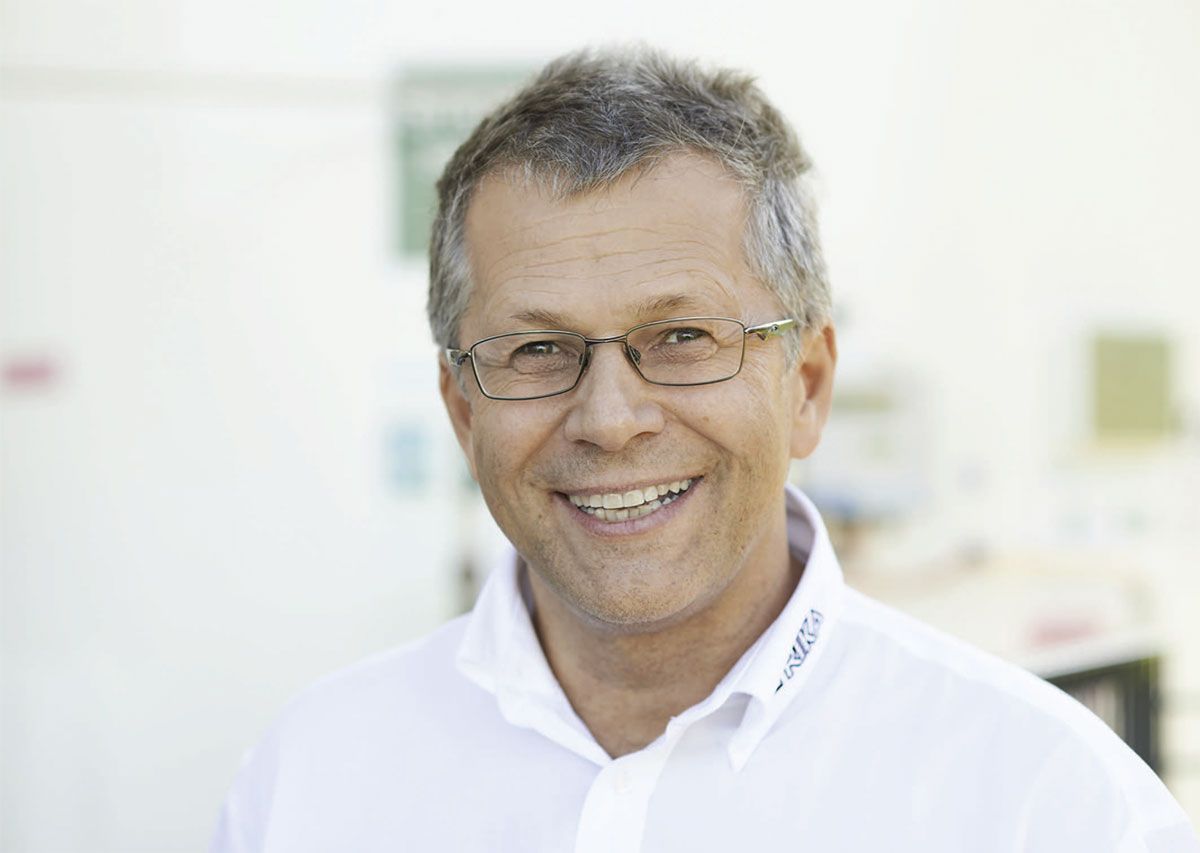
Reinhard Trippacher, Purchasing Manager at RIKA, emphasizes that the solution with two AS/R machines was chosen mainly because of the almost doubled performance and the reliability
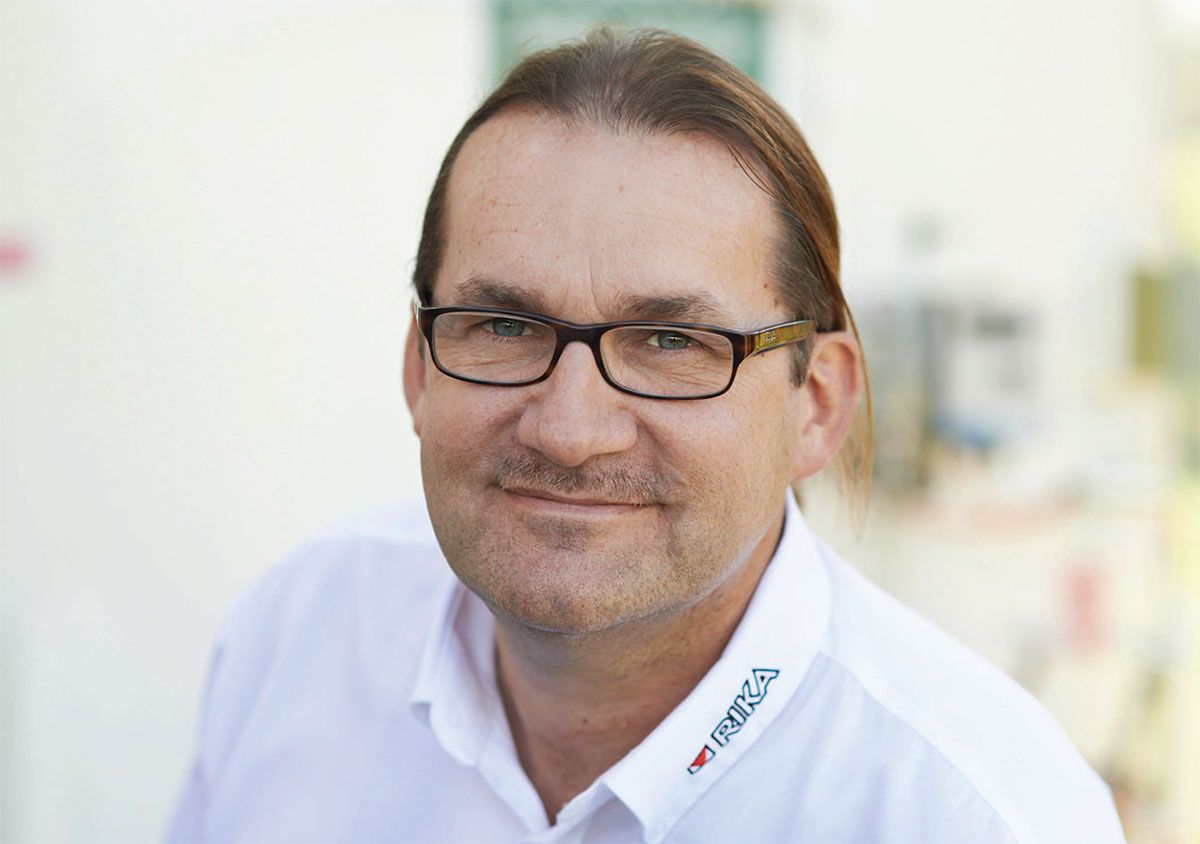
Heinz Kohlbauer, Cutting Manager at RIKA, emphasizes the time savings during setup that the automated warehouse brings
Author: Jürgen Warmbol
Sales Contact Person
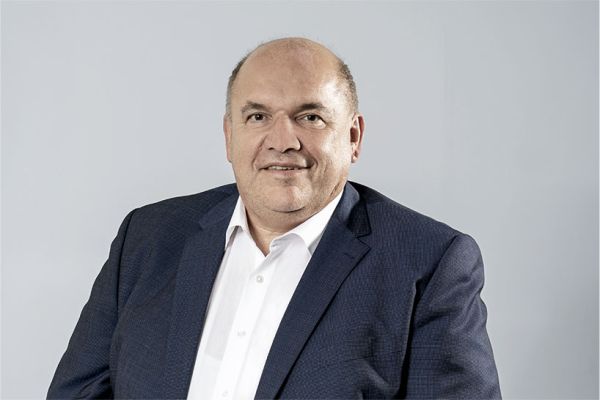
Holger Dehmelt
Sales Engineer Warehouse Technology
STOPA Anlagenbau GmbH
Industriestr. 12
77855 Achern-Gamshurst
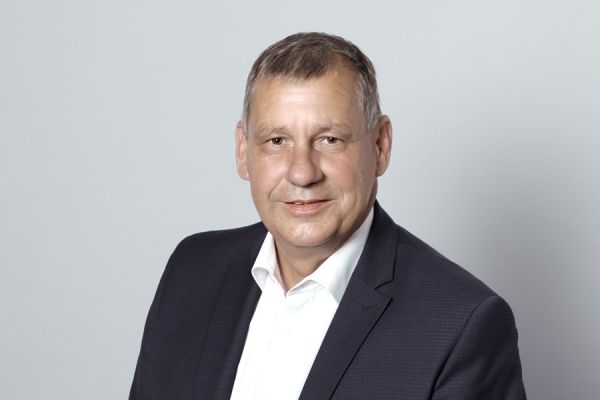
Rolf Eckhardt
Sales Engineer Warehouse Technology
STOPA Anlagenbau GmbH
Industriestr. 12
77855 Achern-Gamshurst
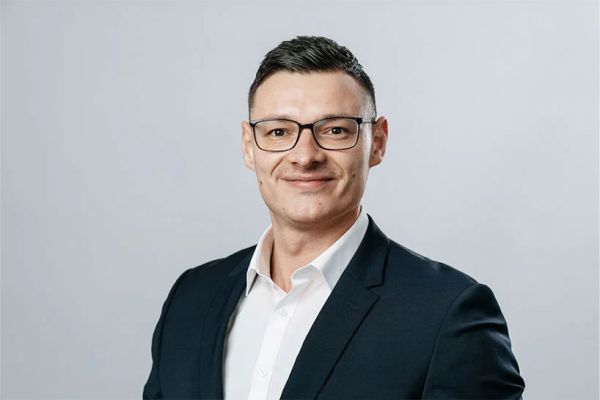
Andreas Pahl
Sales Engineer Warehouse Technology
STOPA Anlagenbau GmbH
Industriestr. 12
77855 Achern-Gamshurst