sheet-metal storage system as an investment in the future
In order to minimize the manual effort involved in changing materials and to create more order, Busalt & Co. Blechwarenfabrik has had a STOPA COMPACT II sheet metal storage system installed next to an existing tower storage system. The system automatically supplies the connected laser cutting machines with sheets, thus enabling longer cutting times per shift.
It is clear that STOPA Anlagenbau GmbH, Achern-Gamshurst, has utilized every centimeter to install a storage system of the required height for Busalt & Co. GmbH Blechwarenfabrik, Viernheim, a warehouse of the required height. Dipl.-Wirtsch.-Ing. Peter Lamberth, managing director of the company, points to the sloping roof of the factory building, under which the system, which is around 25 meters long and 5.5 meters wide, has been installed. “STOPA has placed the warehouse in a pit, thereby expanding the available space. This enabled us to accommodate the maximum number of storage spaces we wanted. The front row of the shelf blocks is 5.7 meters high, while the rear row, in the lowest part of the hall, measures just under five meters.” The sheet metal factory, which was founded in the 1940s as the Mannheim knee plate tube factory Busalt und Co., previously worked exclusively with a TRUMPF TKL tower storage system. However, the capacity of the TKL, which had 56 storage locations, was not sufficient to supply the two laser cutting machines that were used at the time. Therefore, the company buffered its sheet metal plates in cantilever racks. Because often only two to three sheet metal parts had to be cut from one material, there were frequent material changes. This was a disadvantage that led to a lot of forklift traffic.
Minimizing manual effort
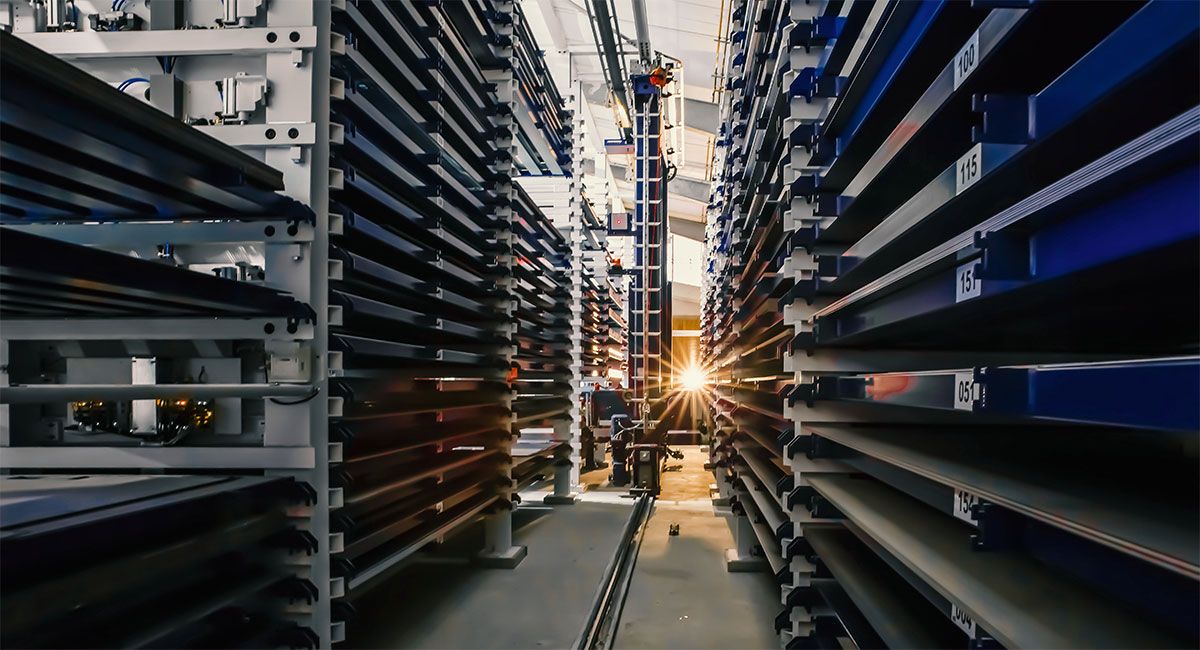
By investing in an automatic STOPA COMPACT II sheet metal storage system, Busalt has minimized the manual effort involved in changing materials and created more order.
Andreas Lamberth, junior manager at Busalt, stops in front of his new TRUMPF TruLaser 3030 laser cutting machine, which is connected to the store by a LiftMaster Store. “The interaction between the automatic store and this machine increases the benefit of the investment. Especially since we can laser during the entire work shift thanks to the automatic loading and unloading of the system. Before, this was only possible for about a third of the shift.”
The second laser cutting machine is also supplied from the automatic storage system. Since no automatic handling device is installed on this machine, the scissor lift table of the station places the flat pallets on storage racks. From there, the employees remove the sheets and transfer them to the machine. All in all, the operator, who lasers 90 percent of the sheet metal parts he produces, has minimized the manual effort required for material changes.
With the help of the STOPA COMPACT II, Busalt, whose core competence lies in the design and production of sheet metal parts, housings and system components, has also created order and thus eliminated the need to search for materials. Peter Lamberth shows samples of different sheet metal qualities. “The importance of order can be seen from our range of 250 to 300 types of sheet metal. This includes steel sheets in thicknesses from 0.1 to 25 millimeters, stainless steel up to 20 millimeters and aluminum up to 12 millimeters thick.«
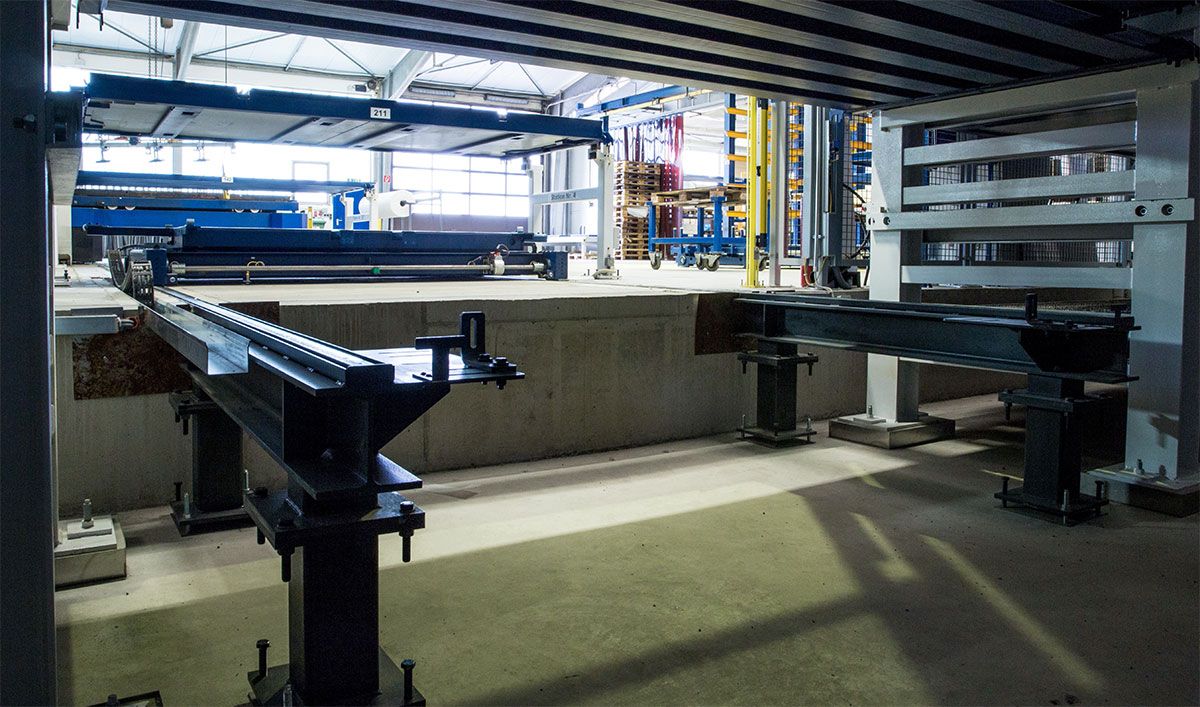
The increase in storage capacity was also the reason for installing the sheet metal storage system in a pit.
Highlights of the solution
- The STOPA COMPACT II sheet metal storage system automatically supplies the connected laser cutting machines with sheets, thus enabling longer cutting times per shift.
- Because the storage system is located in a pit, the desired maximum number of storage locations could be accommodated.
- The automatic loading and unloading of a laser cutting system means that Busalt can laser cut throughout the entire work shift.
Reliable and powerful
Compared to the previous generation, the STOPA COMPACT II offers more storage spaces at the same system height. This space gain makes it possible to increase the load of material by up to six tons. Furthermore, the automatic storage system stands for low maintenance, shorter cycle times and intelligent energy management.
The speed of the storage and retrieval machine, which can reach up to 100 meters per minute, can be adjusted to suit the application. This is how STOPA prevents the material from slipping. When unloaded, the storage and retrieval machine can travel at maximum speed. The storage and retrieval machine is also equipped for two loading heights. In addition, the storage locations above and below the selected storage location are automatically checked to avoid collisions with stored material. These advantages result in a high level of process reliability and performance.
The STOPA COMPACT II at Busalt has 270 storage locations. Of these, 180 are occupied by flat pallets on which the company stores large, medium and small format sheet metal. In addition, the operator uses four large-format laser auxiliary pallets, which he uses to cut sheets on. The laser auxiliary pallets are inserted into the recesses of specially modified load carriers. This results in a ›normal‹ loading height, so that no storage spaces had to be omitted due to higher loading.
High data security
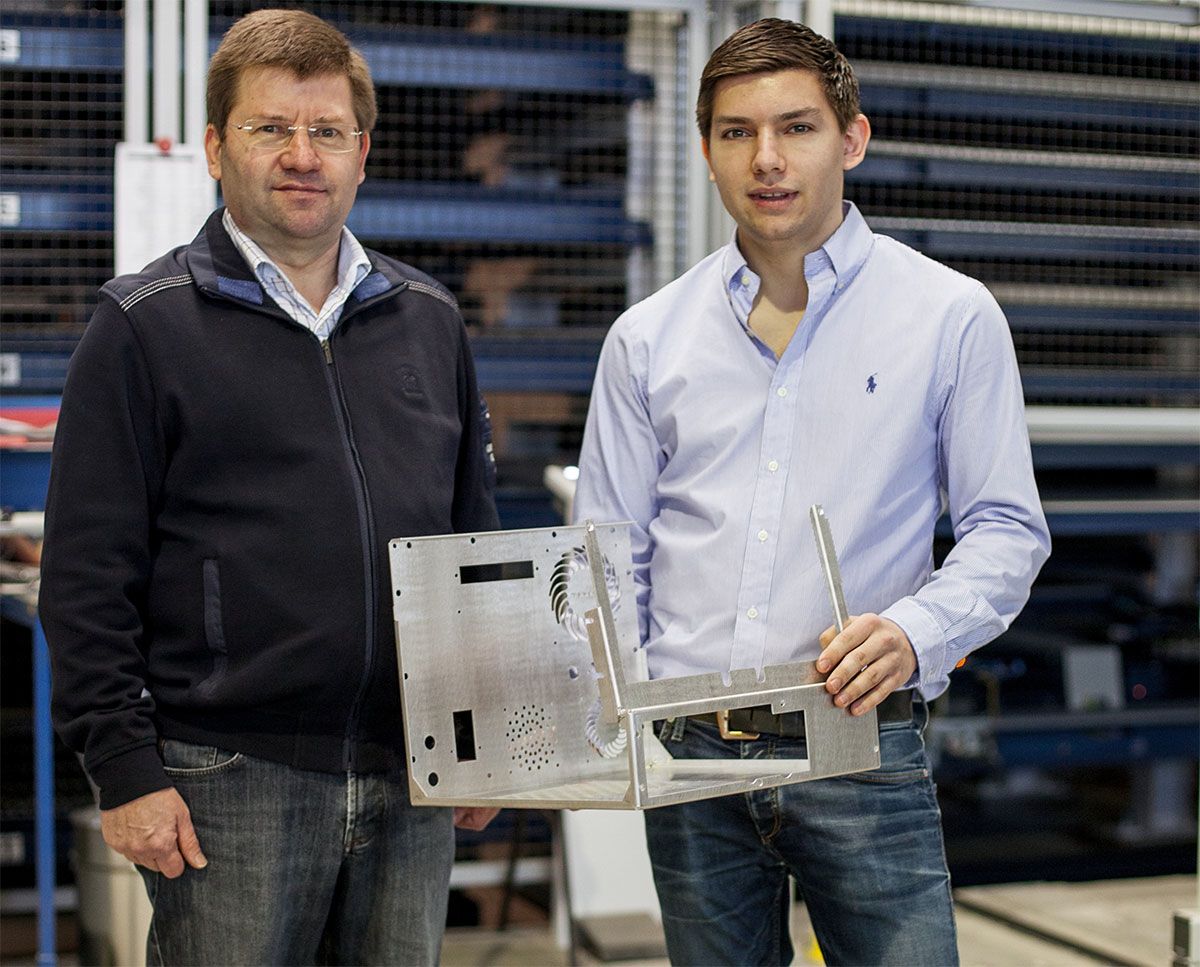
Dipl.-Wirtsch.-Ing. Peter Lamberth, managing director of the company (left), and junior manager Andreas Lamberth
Peter Lamberth looks at the 12-inch TFT display of the ergonomic control panel. “Since STOPA trained our employees for several days and accompanied them during production, they were able to operate the system right away. The display shows the status of the storage and retrieval system at all times. In addition, the storage blocks and the storage and retrieval system can be visualized graphically.”
A real-time soft PLC integrated into an industrial PC controls the system components. The software communicates with the TRUMPF TruTops Fab Module Storage, which displays the material stocks and controls the material flow. The industrial PC operates the system and visualizes its statuses. The manufacturer has implemented a RAID system to ensure that the storage system can continue to operate even if a hard disk fails. An uninterruptible power supply (UPS) protects against data and program losses, and the STOPA Tele-Presence Portal forms the basis for remote diagnostics and troubleshooting.
A future-proof solution
Andreas Lamberth is monitoring the processes on the STOPA COMPACT II, which was launched in mid-2015. “The decision in favor of such a solution was predetermined by the desired level of automation. In view of our experience with the TKL, which runs with high availability, we also decided on STOPA when selecting the large-scale storage system.” Another factor in favor of STOPA was that no interface problems between the storage system and the processing machines were to be expected. This is an important point, especially since the company works unmanned with automatic material changes on Friday evenings.
Peter Lamberth leans back in a relaxed manner at the main control panel of the STOPA COMPACT II. “Everything works wonderfully. The automatic storage system is future-proof, because there is space for almost 50 more pallets and an additional machine can be connected. In addition, three-shift operation is possible. On top of that, we can continue to use our old tower storage system.”
Author: Jürgen Warmbol
Sales Contact Person
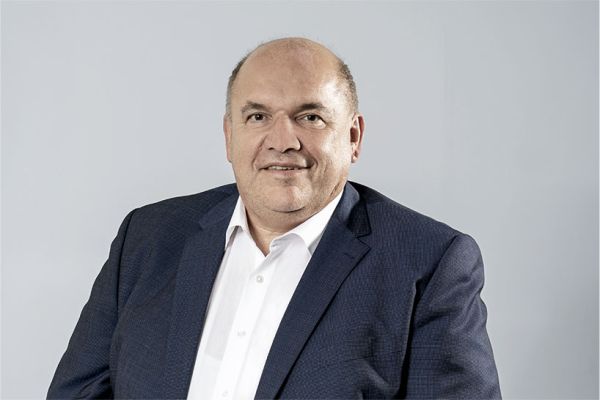
Holger Dehmelt
Sales Engineer Warehouse Technology
STOPA Anlagenbau GmbH
Industriestr. 12
77855 Achern-Gamshurst
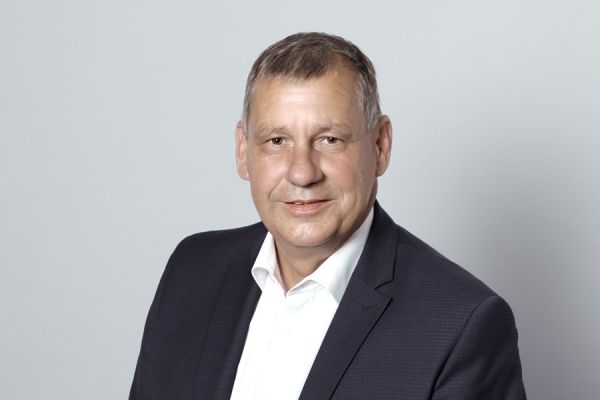
Rolf Eckhardt
Sales Engineer Warehouse Technology
STOPA Anlagenbau GmbH
Industriestr. 12
77855 Achern-Gamshurst
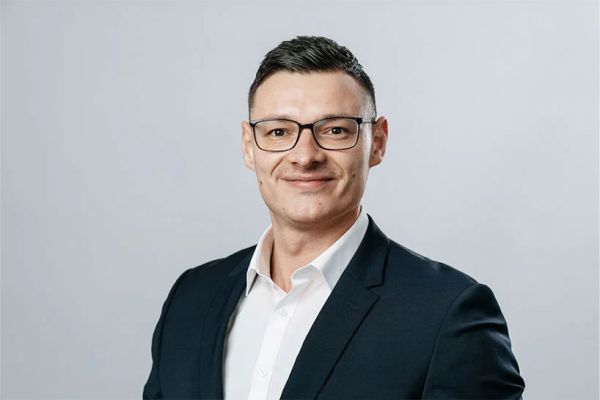
Andreas Pahl
Sales Engineer Warehouse Technology
STOPA Anlagenbau GmbH
Industriestr. 12
77855 Achern-Gamshurst