Sheet-metal storage system in continuous operation
The POLYRACK TECH-GROUP has invested in a new punching and laser cutting center, expanded its machine park and connected it to a STOPA COMPACT sheet metal storage system. This enables the company to manufacture semi- and fully automatically. An advantage that is utilized around the clock, seven days a week.
Horst Rapp, Managing Director of POLYRACK TECH-GROUP, Straubenhardt, unfolds a drawing showing his new plant in Ettlingen near Karlsruhe. “We are setting standards in automatic sheet metal processing. The punching and laser center enables us to serve our customers and our own departments, which are responsible for the subsequent processing steps, even faster and more efficiently. “In this respect, the new plant, with its modern production methods and its automated warehouse, helps to keep our group of companies on a growth path.” The punching and laser center, which cost around three million euros to build, began operations in March 2013. The punching and laser technologies, which were previously spread across two plants, have been brought together on an area of around 5,000 square meters. The company has also invested in additional processing machines.
Edmund Gillhart is head of production technologies and warehouse technology at POLYRACK Electronic-Aufbausysteme GmbH, which operates the punching and laser center. He is standing in the tidy hall, the centerpiece of which is the automatic warehouse from STOPA Anlagenbau GmbH, Achern-Gamshurst. “There isn’t a single sheet of metal lying around here. Since the system offers space for all our materials due to its high degree of space utilization, the floor space remains free for other tasks.”
Automatic storage system as the center of sheet metal processing
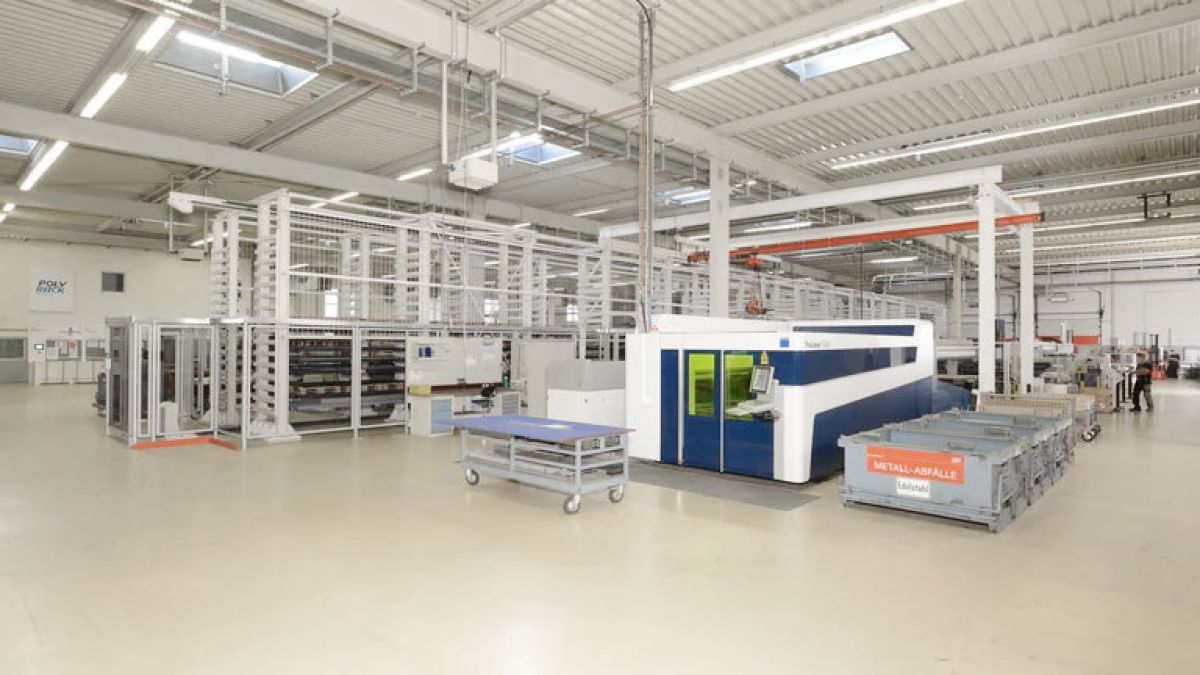
Since the STOPA COMPACT automatic storage system offers space for all of POLYRACK’s material due to its high space utilization, the floor space remains free for other tasks.
The STOPA COMPACT, which is 49 meters long, 4.8 meters high and 4.7 meters wide, with its 28 double-row shelf blocks, is the center of sheet metal processing. Three TRUMPF machines are currently connected, enabling the user to produce semi- and fully automatically. These are a 2D laser cutting machine TruLaser 5030 Fiber, a punch laser machine TruMatic 6000 and a punching machine TruPunch 5000. The material is transferred to the flatbed laser system manually and is also removed from there manually. The other two machines are each equipped with an automatic loading and unloading system. STOPA has already prepared stations for a further punching laser and punching machine.
In the incoming goods area, Gillhart demonstrates how POLYRACK stores the sheets. “A gantry crane lifts the sheet packages from the wooden pallets on which they are delivered and places them on the storage stamps of the scissor lift table. We align the packages with a coordinate corner that we form from pluggable stops.”
In the warehouse, which has 423 storage spaces, a double-mast stacker crane handles 210 flat pallets. These are designed for medium-sized (1,250 x 2,500 millimeters) and small-sized (1,000 x 2,000 millimeters) sheets and for materials weighing up to 2,000 kilograms. A digital distance measuring system ensures that the shelf-operating device is positioned exactly along the length. Another digital distance measuring system, which works absolutely and independently of the load, ensures precise height positioning and thus makes it unnecessary to approach a reference point. The storage and retrieval machine, which stores the flat pallets dynamically (chaotically) in free spaces in the rack block, reaches speeds of up to 100 meters per minute when moving lengthways, 23 meters when lifting and 20 meters when pulling or pushing. Light barriers monitor whether the system is adhering to the three permissible loading heights of a maximum of 130, 285 and 355 millimeters. Furthermore, an automatic loading height control prevents collisions at the storage locations above and below the selected storage location. And a weighing device integrated into the load crossbeam records the weight for each storage or retrieval. Since all components are modular, the system can be easily expanded.
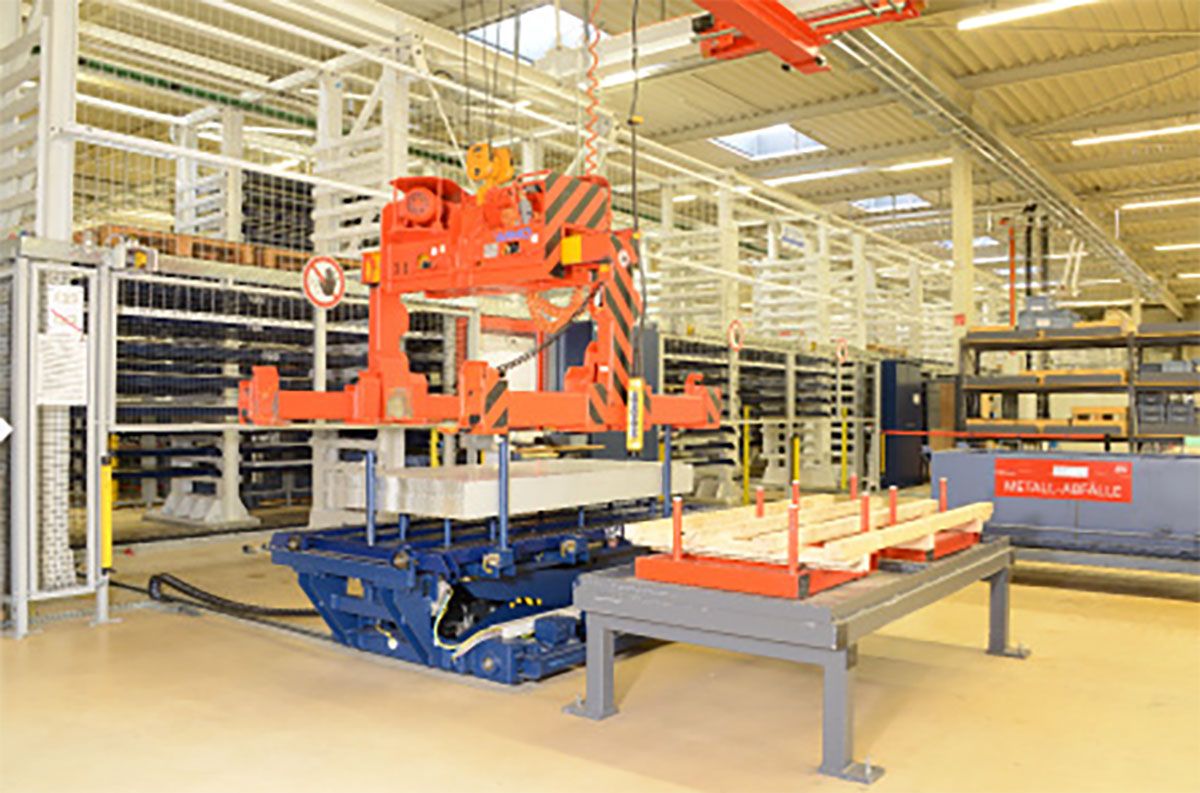
In the goods-in area, a bridge crane lifts the sheet metal packages from the wooden pallets on which they are delivered and places them on the storage stamps of the scissor lift table.
Company
POLYRACK TECH-GROUP: innovative, comprehensive product range
The history of the POLYRACK TECH-GROUP began in 1979 with the founding of POLYRACK Electronic-Aufbausysteme GmbH, which, with 210 employees, develops comprehensive solutions for electronics and is one of the leading providers of electronic packaging solutions. The owner-managed family business also includes RAPP Kunststofftechnik GmbH and RAPP Oberflächenbearbeitung GmbH, along with their foreign subsidiaries, and econ solutions GmbH, which has made a name for itself in the field of energy efficiency and rational energy use. The internationally active POLYRACK TECH-GROUP manufactures high-quality products, utilizing the economic advantages of series production. The focus is on customized products and solutions. POLYRACK employs approximately 350 people worldwide and has developed from a pure manufacturing service provider to a full-service provider whose portfolio ranges from engineering and design to the final product.
Space-saving machine connection
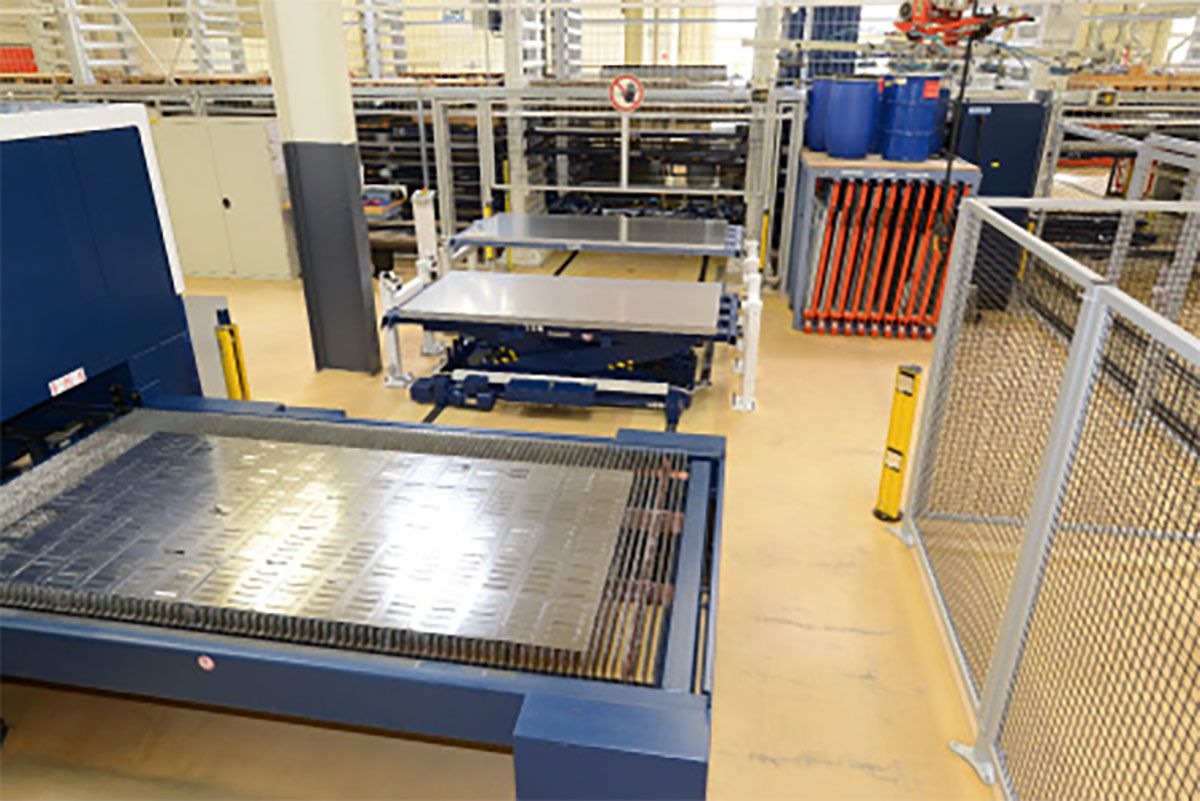
The automatic warehouse supplies the 2D laser cutting machine via a scissor lift table and two storage racks arranged one behind the other.
The 2D laser cutting machine is supplied by the warehouse via a scissor lift table and two storage racks arranged one behind the other. The scissor lift table moves under the rear rack to deposit a pallet of sheets on the front rack or to pick up an empty one. The operator uses a crane to lift the individual sheets into the system and to remove the finished parts. POLYRACK was looking for a space-saving supply and disposal concept to connect the two other machines to the system. Gillhart addresses the resulting challenge. “The loading and unloading stations for the punching and punching laser machines had to be built very compactly in order to be able to install three machines next to each other on one long side of the warehouse. STOPA has developed a solution in which scissor lifts supply the systems with raw sheets and transport carts in a portal design, which travel over the scissor lifts, transport finished parts into the warehouse. A special feature is the so-called evasive maneuver. Here, the gantry carriage with the disposal pallet moves back so that the handling device can remove a sheet from the supply pallet that is lying on the scissor lift table below. In addition, the gantry carriage with the disposal pallet moves to predetermined positions using a rotary encoder, where the handling device automatically places the semi-finished parts.”
The loading stations are also equipped with a last-sheet detection system and a spreading magnet device. This spreads the sheets using a magnetic field so that they can be easily separated from each other. At the unloading stations, a light barrier checks whether the system is maintaining the maximum loading height on the gantry car. At another station, the goods outbound, the operator stores material using a transport car.
The associated systems request the sheets, made of stainless steel, steel or aluminum, from the warehouse and process their orders while the operators prepare the next ones in parallel to the main time. Retrievals to an older punching and punching laser machine, which are both not directly connected to the STOPA COMPACT, are entered manually. The company transports finished parts to its other plants for mechanical finishing. The transport trolleys return sheets and semi-finished products to the system. Gillhart stops in front of a station. “The warehouse operates around the clock, seven days a week, and achieves a throughput of around 20 tons. The employees work in two shifts. The third shift runs unmanned with standby.”
Easy to use
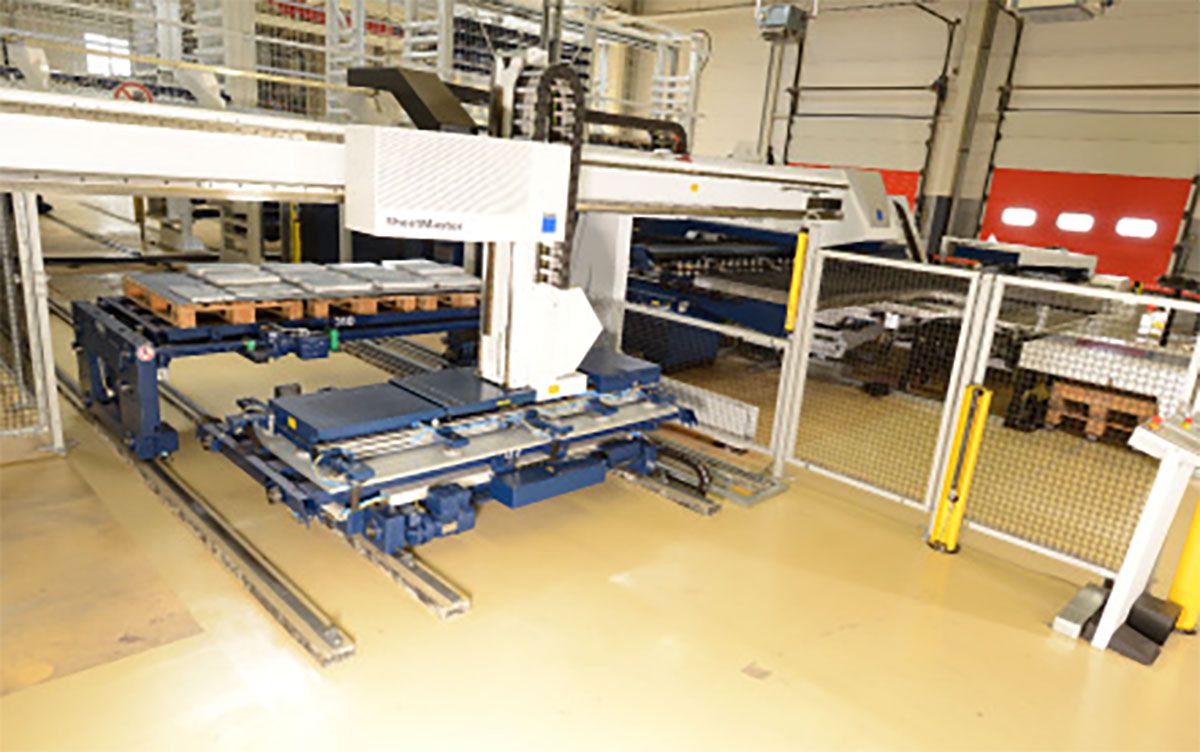
STOPA has developed a solution in which a scissor lift table supplies the punching machine with raw sheets and a transport carriage in a portal design, which travels over the scissor lift table, transports finished parts into the warehouse.
The system control consists of an industrial PC with integrated real-time soft PLC, which is installed together with a 12-inch TFT display in an ergonomic control panel. The PLC controls the system components, while the PC displays the system status. Gillhart opens a storage view on the display. “The system is very easy to operate via the PC and easy-to-understand function keys. We appreciate that we can permanently read the status of the storage and retrieval system in plain text and that the storage blocks and the storage and retrieval system can be visualized graphically.”
If a fault occurs that cannot be rectified by the POLYRACK employees, STOPA can analyze and rectify the error from its own location using the remote maintenance software PC anywhere. If a hard disk fails, the storage system continues to run with the help of the integrated RAID system, increasing the availability of the entire system. In addition, STOPA has installed an uninterruptible power supply (UPS) that switches off the panel PC in the event of a power failure. This ensures that the current investment data is backed up and that data and program losses are avoided.
The control system communicates with the TRUMPF TruTops Fab module Storage via an interface. This software manages all stocks, including semi-finished parts, and controls the entire material flow of the production process. This includes the supply of raw materials and the removal of the manufactured parts.
Well-proven automatic storage system
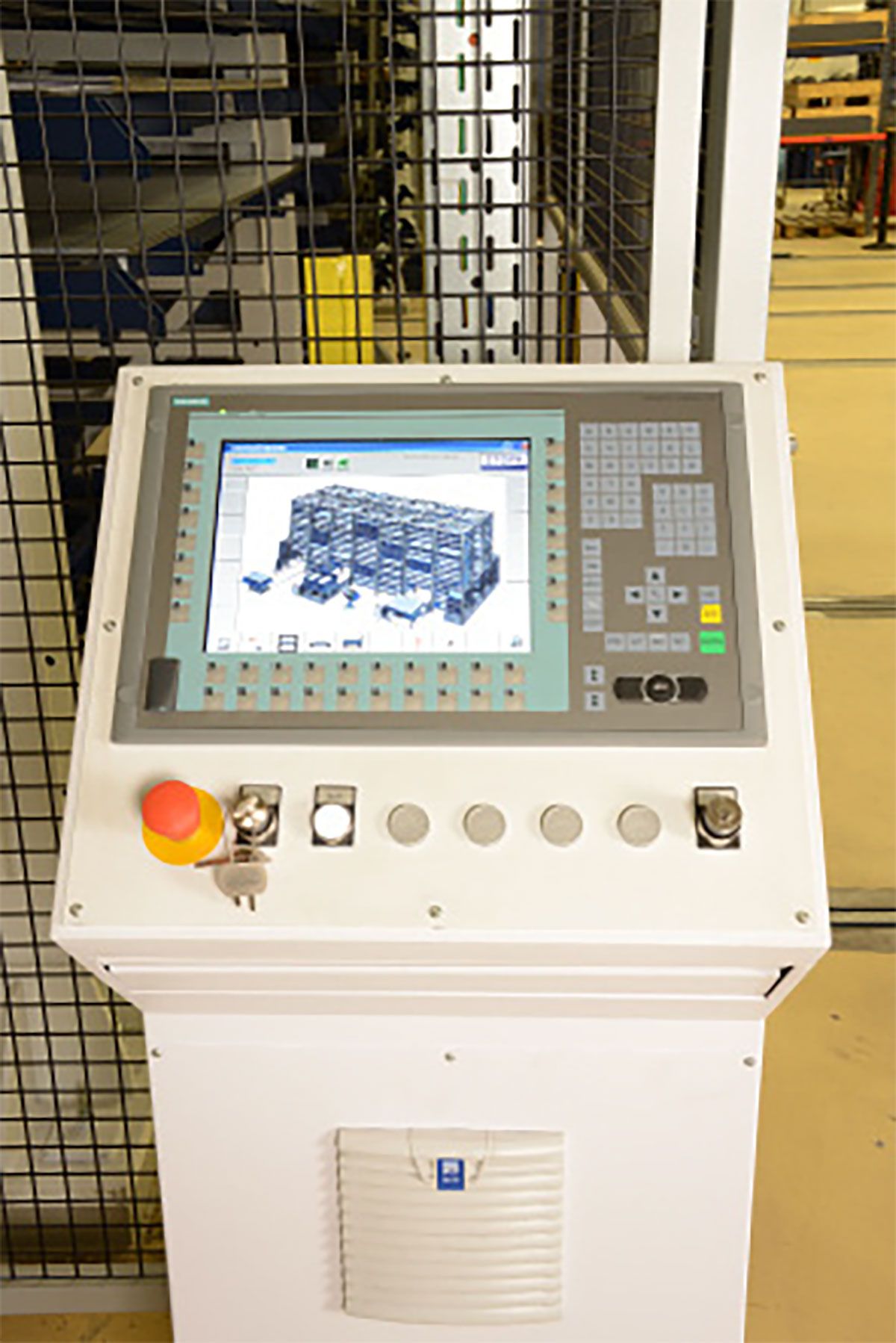
The system control consists of an industrial PC with integrated real-time soft PLC, which is installed in an ergonomic control panel together with a 12-inch TFT display.
The sheet metal storage system is already the third automatic storage system from STOPA in which POLYRACK has invested since 1994. Rapp shows photos of the systems. “When the contract was awarded, we chose this supplier again because its storage technology has proven itself. We are also very satisfied with the new STOPA COMPACT. This is demonstrated by the high degree of space utilization, the high throughput, the option of connecting the processing machines directly, and one hundred percent availability.”
Author: Jürgen Warmbol
Sales Contact Person
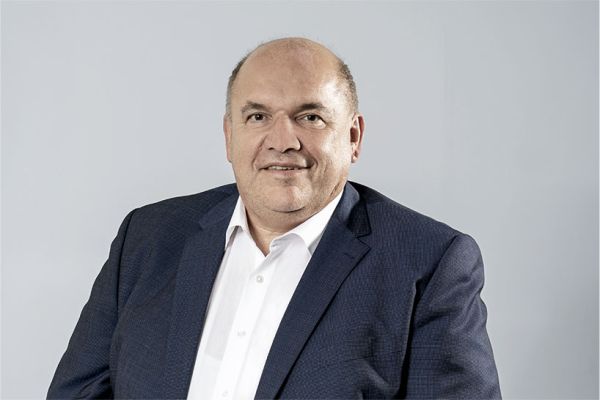
Holger Dehmelt
Sales Engineer Warehouse Technology
STOPA Anlagenbau GmbH
Industriestr. 12
77855 Achern-Gamshurst
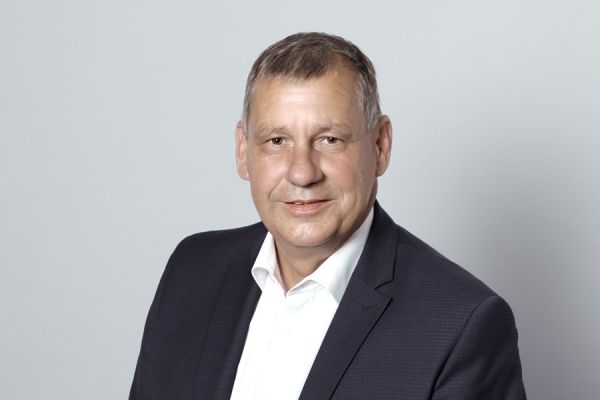
Rolf Eckhardt
Sales Engineer Warehouse Technology
STOPA Anlagenbau GmbH
Industriestr. 12
77855 Achern-Gamshurst
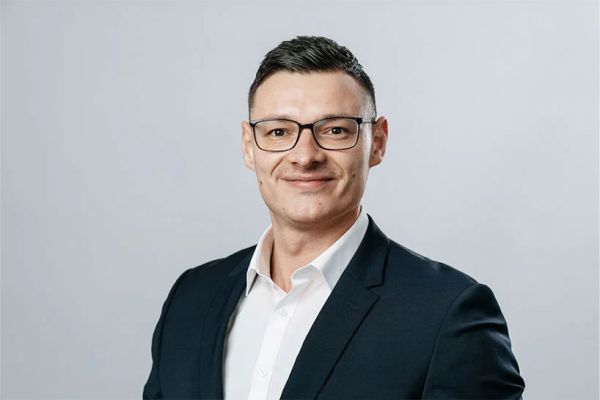
Andreas Pahl
Sales Engineer Warehouse Technology
STOPA Anlagenbau GmbH
Industriestr. 12
77855 Achern-Gamshurst