Sheet-metal storage system with inner values
The STOPA COMPACT II is a new automatic sheet metal storage system on the market that, compared to its predecessor, offers more pallet spaces with the same storage volume, reduced cycle times, intelligent energy management and even greater process reliability. This is a significant added value that Rötzer Maschinenbau GmbH, for example, is benefiting from.
No matter which side you enter the factory building of Rötzer Maschinenbau GmbH in Rottenburg/Laaber from, the STOPA COMPACT II, which is around 90 meters long, 6.6 meters high and 5.6 meters wide, immediately catches the eye. However, what primarily counts are the “inner values” of the sheet metal storage system, which was developed by STOPA Anlagenbau GmbH, Achern-Gamshurst. One of these values has a particularly strong impact given the length of the storage system: the reduced upper and lower approach dimensions of the COMPACT II mean that in most cases two storage compartments are gained in each rack block compared to the previous design.
Alfred Rötzer, who runs the company together with his brother Christian, points to the patented weighing device that is integrated into the load beam of the storage and retrieval system (SRM). “Since the weighing cells are integrated into the pallet running surface, the weighing time is significantly reduced. As a result, the time for a complete storage cycle is also reduced, which means that a higher number of productive cycles per shift is possible.”
Intelligent energy management
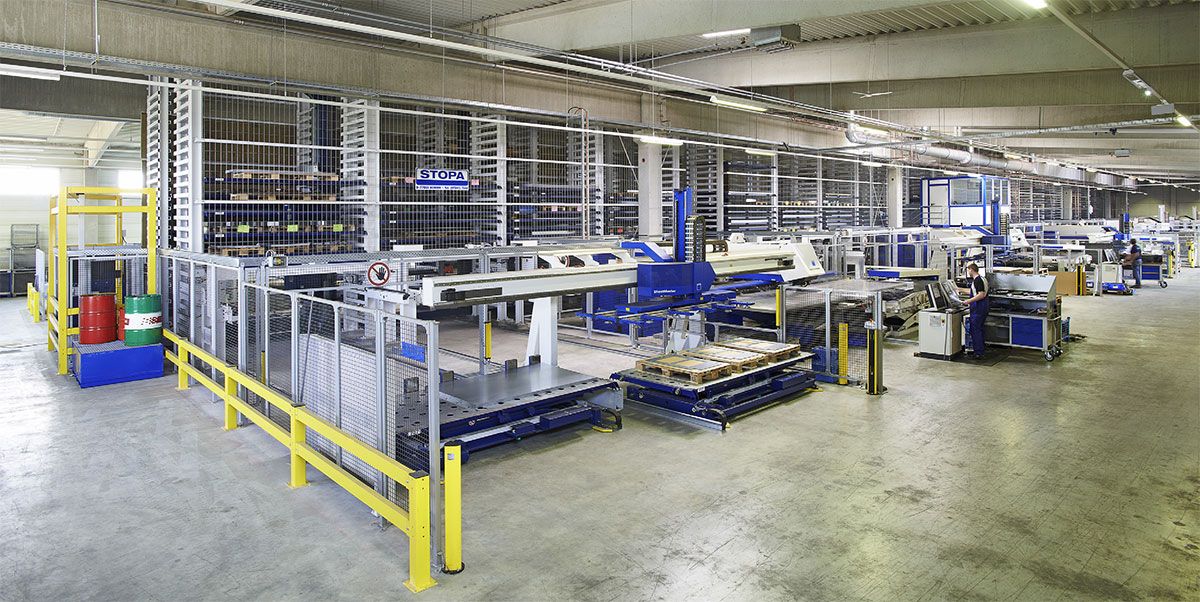
STOPA COMPACT II is a new automatic sheet metal storage system that offers significant added value compared to its predecessor.
The other advantages of the new storage system include its intelligent energy management, which helps to save up to 20% of electricity, depending on the system configuration. An ecological and economical advantage that is based on the fact that STOPA uses two powerful, lightweight gear motors instead of the heavy drive motor previously used, as well as a more compact crossbeam, thus reducing the total weight by about half a ton.
Furthermore, regenerative energy, which is generated, for example, when the traverse is lowered, can be used directly for the drive motor via an intermediate circuit coupling. This is a process that requires intelligent drive control and is particularly effective when several drives of the storage and retrieval system start and brake at the same time.
In addition, STOPA offers the option of feeding the regenerative energy back into the supply network. This applies to energy that would otherwise be lost because braking resistors would convert it into heat loss. To enable energy to be fed back into the network, suitable feedback units and the approval of the network operator are required. Alfred Rötzer leafs through the order confirmation from the sheet metal storage manufacturer. “We haven’t been working with energy recovery so far. But we can have it integrated retrospectively.” However, this only makes sense once the number of stock movements reaches a certain level.
Company
Rötzer Maschinenbau: 8,000 tons of sheet metal per year
Rötzer Maschinenbau GmbH was founded in Rottenburg/Laaber in 1948. The contract manufacturer processes sheet metal in small, medium and large formats, as well as a large number of special formats. The company uses steel sheet, galvanized steel sheet and stainless steel in thicknesses of two to six millimeters. The turnover is around 8,000 tons per year. Rötzer works in two shifts. Furthermore, the punching and laser machines run unmanned at night. The company, which employs around 120 people, has its main customers within a radius of 100 kilometers in the fields of energy technology, heating technology and general mechanical engineering.
More precise positioning
One of the highlights of the RBG is its variable acceleration. Alfred Rötzer enlarges a window of the warehouse management system on an operating terminal. “We have stored a reduction value for each material so that the RBG accelerates less if necessary, the transitions when pulling are passed over more slowly and the sheets do not slip. The reduction values increase process reliability, especially when we transport galvanized oiled sheets, and also save energy. In addition, the polygon effect is minimized at the lifting gear and the influence of the rail joints is reduced during longitudinal travel. On the other hand, the system works with the highest acceleration when the material is not slipping or the RBG is empty. Apart from these advantages, STOPA has reduced the overtravel dimensions at the RBG so that the automatic warehouse is even more compact. The manufacturer uses a compact conductor rail for power transmission, which offers more reserve capacity for a later expansion of the warehouse and is easier to replace if spare parts are needed.
In addition, the system pallets in the STOPA COMPACT II run more smoothly than in the STOPA COMPACT I due to a revised concept. This makes the risk of sheets slipping even lower than before. The operator again benefits from more precise positioning and greater process reliability, as well as a longer service life thanks to minimal wear. This is based on an angled transition between the load crossbeam and the storage locations, which the pallet support rollers pass more easily and smoothly, and the elimination of the nose rollers otherwise used. In addition, the crossbeam is equipped with replaceable hardened docking pieces that provide a high degree of stability.
Everything under control
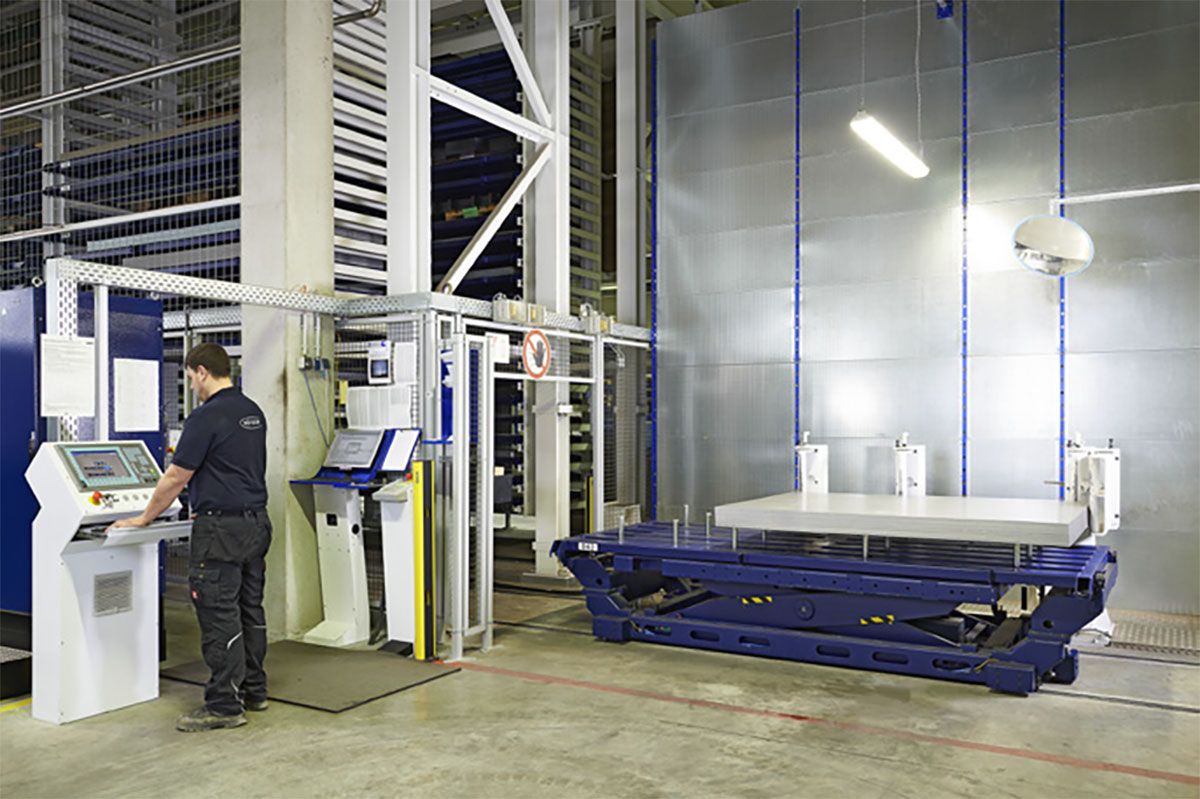
The scissor lift table at the incoming and outgoing goods station is equipped with storage stamps for incoming and outgoing goods and with pluggable stops for a coordinate corner.
The scissor lift table at the incoming and outgoing goods station is equipped with storage stamps for incoming and outgoing goods and with pluggable stops for a coordinate corner.
The load crossbeam also works with an electronic synchronizing shaft instead of the conventional mechanical one, which is responsible for the smaller overall height and the lower dead weight. Furthermore, the chain wear is compensated for by a spring package on the loose side, so that the chain tension is maintained for a long time.
On top of that, the crossbeam is equipped with a pre-assembled control unit -1 that ensures additional process reliability when operating with multiple loading heights.
The STOPA COMPACT II also scores points for its low maintenance requirements. This advantage is due, among other things, to the lifting chain tension that is balanced over the operating time, more precise lifting guide rollers and a reduced range of parts and components. As a result, maintenance costs and downtimes are reduced. Because no hydraulic lifting system is required, which means that there is no risk of leaks, the new sheet metal storage system is also more environmentally friendly.
Convenient human-machine interface
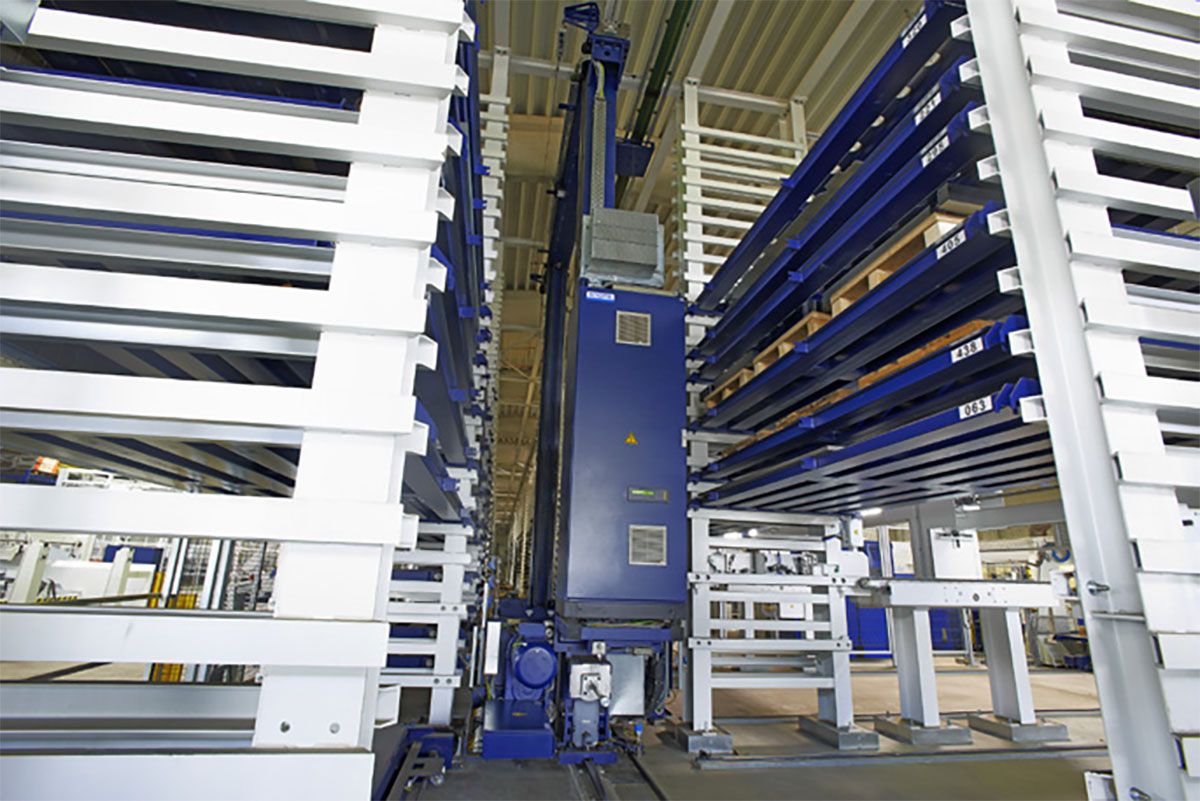
Since STOPA has reduced the total weight of the storage and retrieval system by around half a tonne by using lightweight gear motors and a more compact crossbeam, over 20 percent of electricity can be saved.
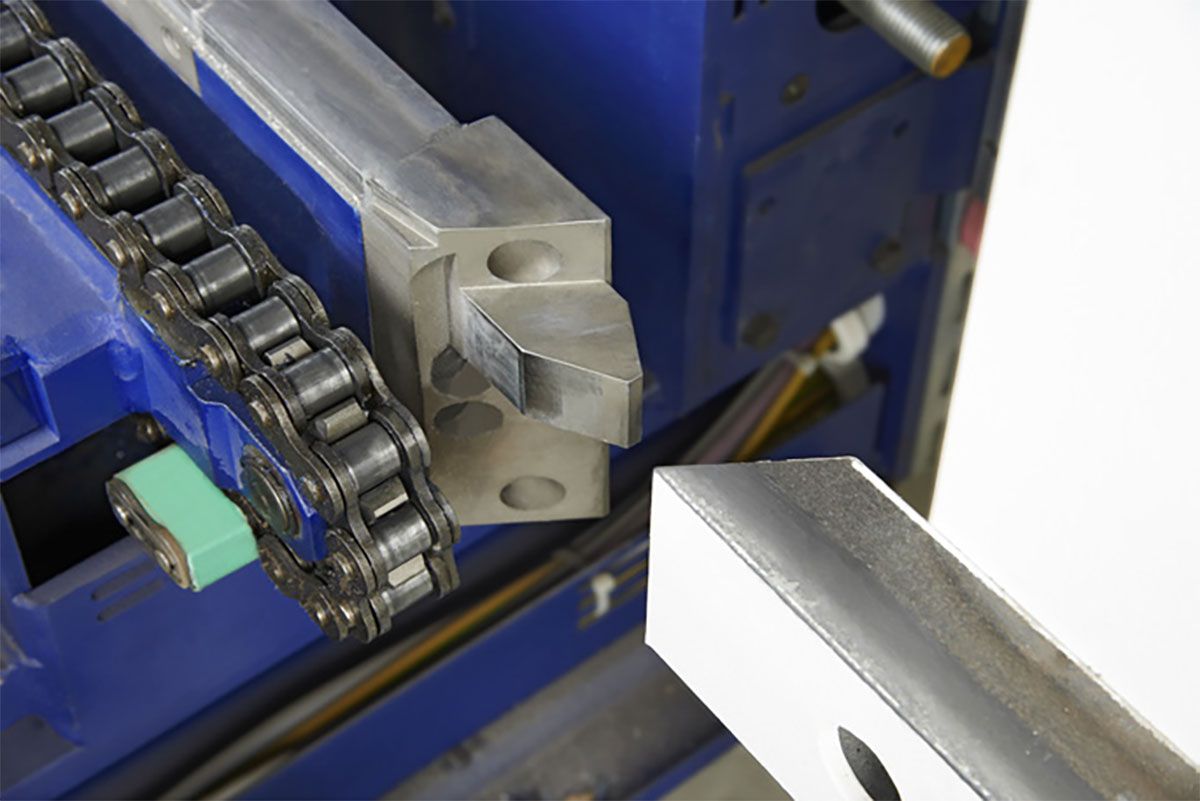
The sloping transition between the load crossbeam and the storage locations, which the pallet rollers pass more easily and smoothly, results in more precise positioning, greater process reliability and a longer service life.
At Rötzer, the STOPA COMPACT II has 23 stations, some of which the manufacturer has combined into double stations with loading and unloading trolleys. All stations are equipped with a scissor lift table, which usually has a tandem or quick-change function, and with a pneumatic centering device for the trolleys and pallets. The incoming and outgoing goods station is an exception to this, as its scissor lift table is equipped with deposit stamps for incoming and outgoing goods and with pluggable stops for a coordinate corner. The processing machines are all connected via interfaces. The loading stations have a spreading magnet device and last-sheet detection. The unloading carts use an encoder to position the processed sheets. Many of the stations are equipped with a light barrier that monitors the maximum loading height.
The list of TRUMPF processing machines used includes two combined punching and laser cutting machines, a TruMatic 7000 and a TruMatic 600L, as well as two punching machines, TruPunch 5000, each connected to a SheetMaster that automatically loads and unloads them. Alfred Rötzer interrupts the tour at another station where the STOPA COMPACT II delivers sheets to a TruBend 5170 bending machine. “A BendMaster is working here. The bending robot takes the sheets from the pallet, moves to the machine on a linear unit and bends the sheets there according to the program. The BendMaster makes it possible to supply the bending machine with lasered or punched semi-finished parts from the warehouse during the main production time. Since this solution has proven itself, we are already planning to invest in a second BendMaster for another station.”
A real-time soft PLC integrated into an industrial PC controls the system components of the sheet metal storage system and communicates with the TRUMPF warehouse management computer via an interface, which the machines use to request material. The computer also uses the interface to send the reduction values to the PLC, which the RBG uses to accelerate less. The operator uses the industrial PC to operate the system and to display the system status.
Alfred Rötzer stops in front of the ergonomically designed control panel, into which the industrial PC with its 12-inch TFT display is built. “Our employees were able to operate the warehouse after a very short training period.” STOPA has created a user-friendly human-machine interface by providing permanent status displays of the RBG in plain text and by graphically visualizing the storage blocks and the RBG. If a fault should occur, the manufacturer can analyze and rectify the error from his own location via modem.
Much more economical
In the past, the company used to book its warehouse accesses manually and store the boards in cantilever racks. Alfred Rötzer shows photos from that time. “We often had to search for material. In addition, our employees sometimes fed the wrong sheet metal qualities to the machines. The large amount of time required and the damage caused by forklift traffic were also a disadvantage.”
The decisive factor in the decision to invest in the automatic sheet metal storage system was its high level of cost-effectiveness, emphasizes Alfred Rötzer. Apart from that, there was a desire for constant stock monitoring. The availability of the storage system, which went into operation in the fall of 2011, is close to 100 percent. All in all, the STOPA COMPACT II, with its comprehensive added value, represents a future-oriented solution in sheet metal storage technology.
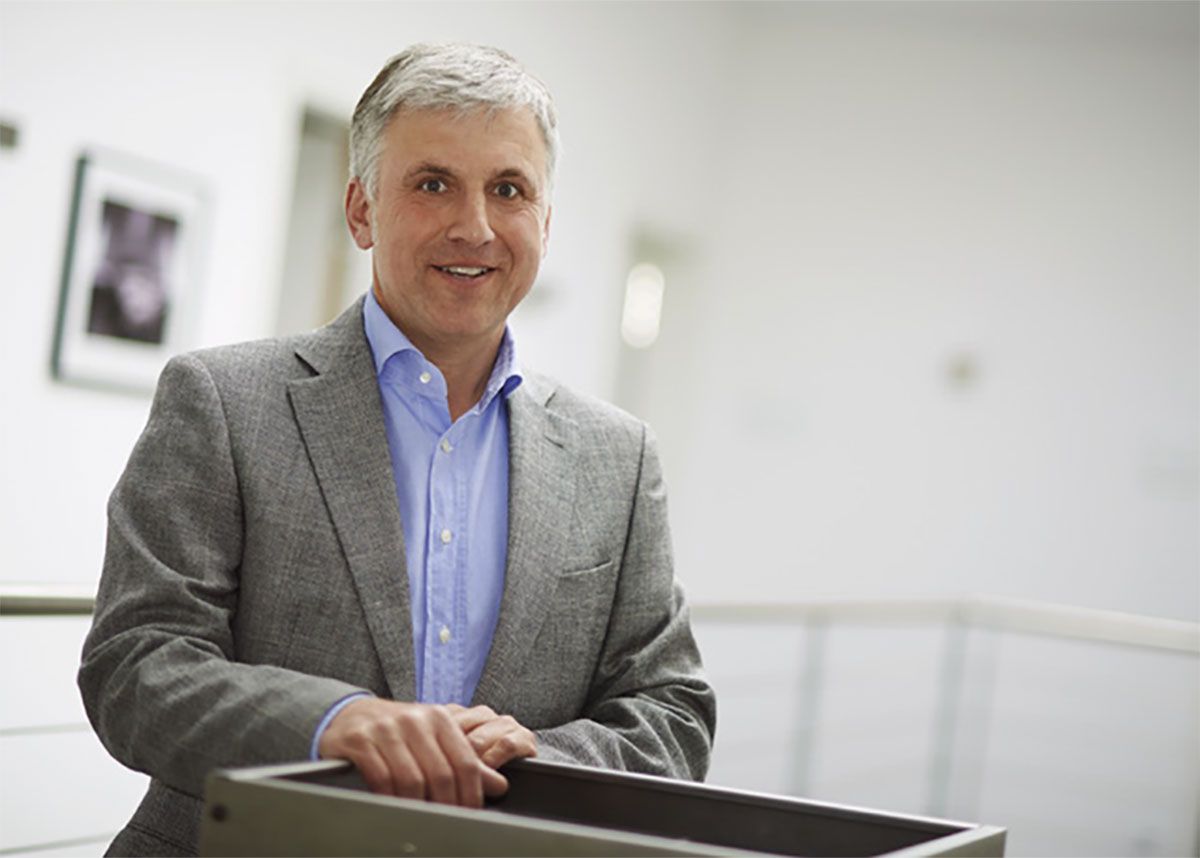
Alfred Rötzer, who runs the company together with his brother Christian, invested in the automatic sheet metal storage system because of its high cost-effectiveness.
Author: Jürgen Warmbol
Sales Contact Person
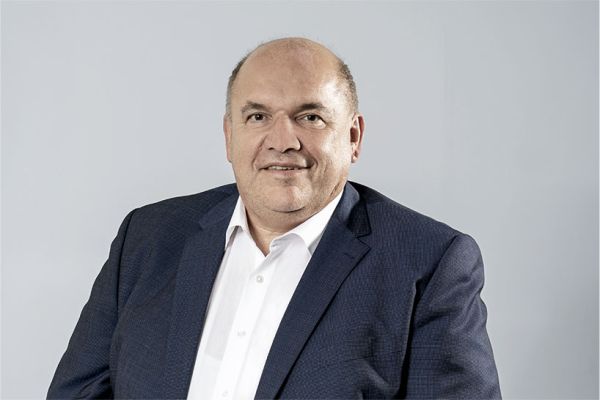
Holger Dehmelt
Sales Engineer Warehouse Technology
STOPA Anlagenbau GmbH
Industriestr. 12
77855 Achern-Gamshurst
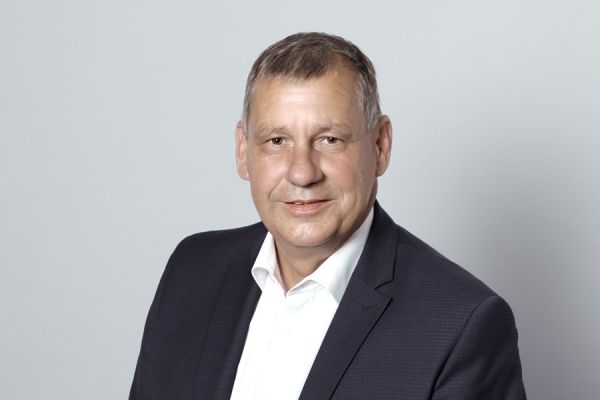
Rolf Eckhardt
Sales Engineer Warehouse Technology
STOPA Anlagenbau GmbH
Industriestr. 12
77855 Achern-Gamshurst
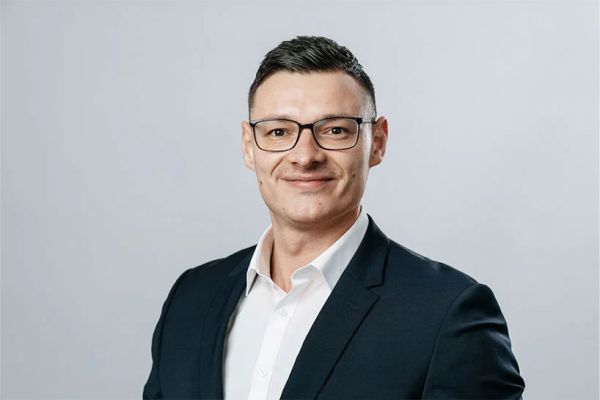
Andreas Pahl
Sales Engineer Warehouse Technology
STOPA Anlagenbau GmbH
Industriestr. 12
77855 Achern-Gamshurst