Automatic cost reduction
Schletter Inc. in Shelby, North Carolina (USA) has invested in an automatic sheet metal and long goods storage system from STOPA. The operator benefits from short supply routes to its processing machines, unmanned shifts, a noticeable time saving and, ultimately, a sustainable reduction in intralogistics costs.
The subsidiary of the German company Schletter GmbH gained its first experience in the storage of sheet metal and long goods at its place of origin in Tucson, Arizona. There, the material was stored in cantilever racks and transported to the machines by forklift trucks. During a tour of the plant, Christoph Hackner, Vice President of Manufacturing at Schletter Inc., explains why a new concept was chosen for the plant in Shelby, North Carolina. “It was clear from the early stages of the construction planning that we wanted to invest in automated storage systems. The aim was to develop a sustainable economic strategy for handling raw materials and semi-finished parts.”
This has been achieved, as Hackner emphasizes. Machines are connected to each other via the warehouse, which acts as a conveyor system, saving time and reducing distances. The company also uses this option to run unmanned shifts or ghost shifts, as the Americans call them, at night and, above all, from Friday lunchtime to Saturday morning. In addition, it has been possible to greatly reduce forklift traffic in the building, thus creating a safe working environment and minimizing damage to the material. Ultimately, the goal of reducing intralogistics costs has been achieved.
Sheet metal storage as a supply axis
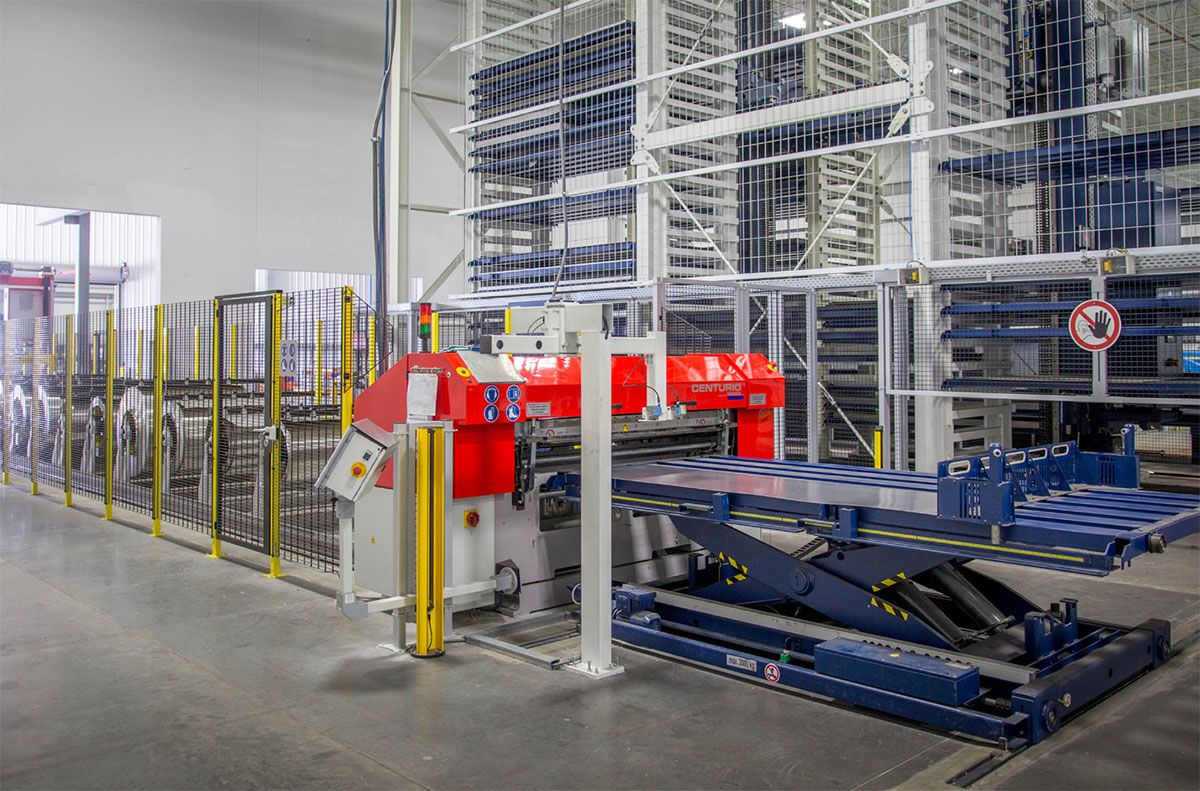
A slitting machine cuts the thin sheet metal delivered in coils and pushes the sheets onto a flat pallet, which a scissor lift table then transports into the STOPA COMPACT automatic storage system.
The thin sheet metal, which is delivered in the form of coils, is cut to the desired dimensions by a Krasser CENTURIO slitting machine and pushed onto a flat pallet, which is located on a scissor lift table. This table transports the sheets into the STOPA COMPACT automatic storage system, where they are picked up by the double-mast storage and retrieval machine. The operator feeds further material into the warehouse, which was launched in October 2013, at a manual storage station. The sheet metal warehouse, which is around 51.5 meters long, 8.4 meters high and 5.5 meters wide, and which, like the long goods warehouse, was supplied by STOPA Anlagenbau GmbH, Achern-Gamshurst, handles six to eight tons of steel and aluminum per shift. Designed for large and medium-sized metal sheets, with 781 pallet spaces and two loading heights, the warehouse supplies several processing machines. These include a TRUMPF TruLaser 5030 laser cutting machine. It is connected to the warehouse by a double carriage – consisting of a loading carriage and an unloading carriage in a portal design – and by an automatic handling device. The double carriage transports sheets from the warehouse to the machine and returns semi-finished products. Hackner explains: “Returning semi-finished products is routine for us because the sheet metal warehouse also acts as a supply axis to the other systems.” For example, a transport carriage transports laser-cut parts to a RAS Multibend Center, which Schletter uses for up and down swivel bending and which a robot supplies with blanks. Two TRUMPF bending machines and a RAS plate shear are also connected via transport carriages. The material is transferred to the bending machines and the plate shear manually. Bar code scanners installed at the stations, which the operators use to scan printed transport orders, make it easier to access the material required in each case. A weighing device records the weight of every incoming or outgoing item. Since the operator is also thinking about the future, he has kept an option open for expansions and planned an area for two stations to connect a TruPunch 5000 punching machine.
Hackner watches the storage and retrieval machine (SRM), which has picked up a flat pallet to be stored and is accelerating towards the storage location. “We decided on a particularly powerful stacker crane that can reach speeds of up to 150 meters per minute when traveling longitudinally.” This means that the stacker crane can cover the 51-meter-long distance between the 26 double-row storage blocks in the warehouse faster. This shortens the material supply times and thus the waiting times for employees, while at the same time increasing productivity at the stations. However, there are also cases in which it would be better to start and stop more gently. To achieve this, the operator can store lower acceleration and speed values in the article master data, thus increasing process reliability.
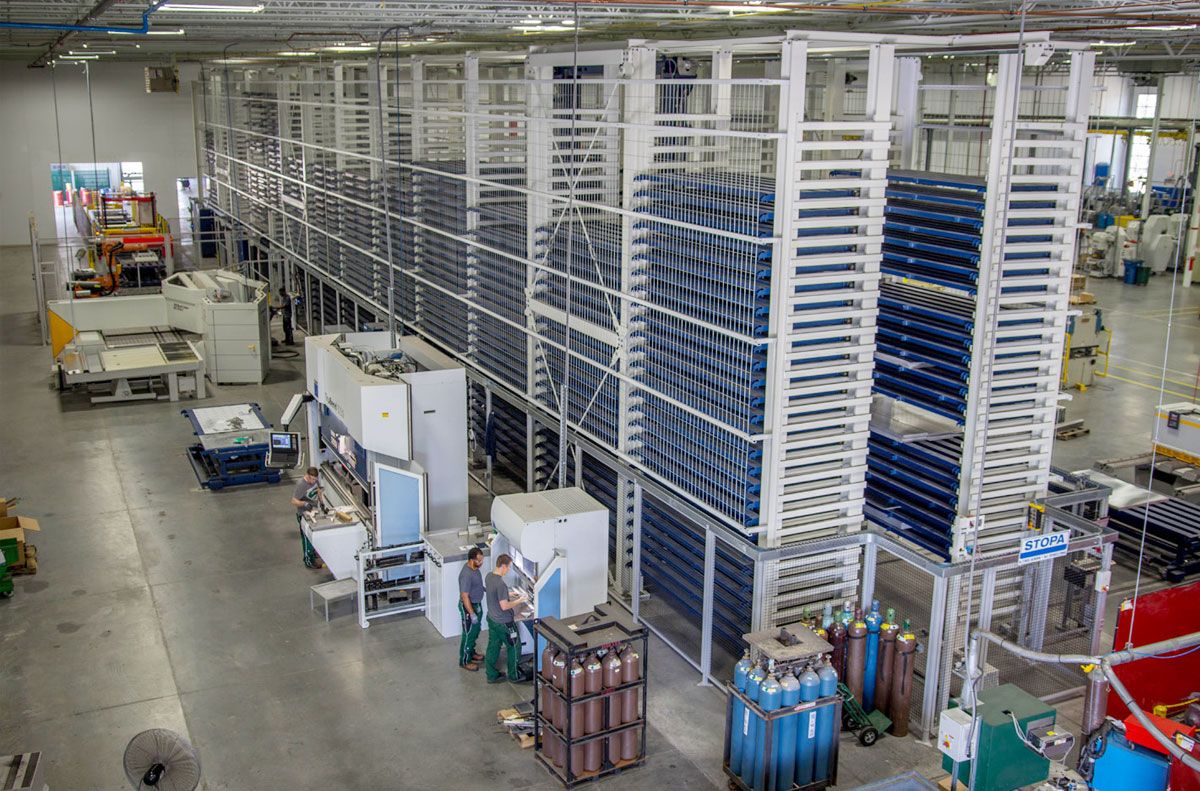
By investing in two automatic warehouses from STOPA, Schletter benefits from short supply routes to its processing machines, unmanned shifts, time savings and, ultimately, sustainably reduced intralogistics costs.
Company
Schletter Inc.: Specialist in solar mounting systems
Schletter Inc., founded in 2008 in Tucson, Arizona (USA), designs, develops and produces solar mounting systems made of steel and aluminum, which it sells in North and South America. Since its foundation, Schletter Inc. has manufactured photovoltaic mounting systems with a capacity of over one gigawatt. The company, which employs around 200 people, offers roof and ground mounting systems for photovoltaic systems designed for residential and commercial buildings as well as for energy suppliers. Its customers include project developers and solar installers. The company’s second production site, in addition to Tucson, is its current headquarters in Shelby, North Carolina. There alone, the company handles over 100 tons of material every day.
Schletter Inc. is an independent subsidiary of Schletter GmbH, Kirchdorf near Haag in Upper Bavaria, which operates subsidiaries in eleven countries with more than 1,300 employees worldwide. The Schletter Group has over 20 years of experience in solar mounting systems.
More production space thanks to long-bar storage
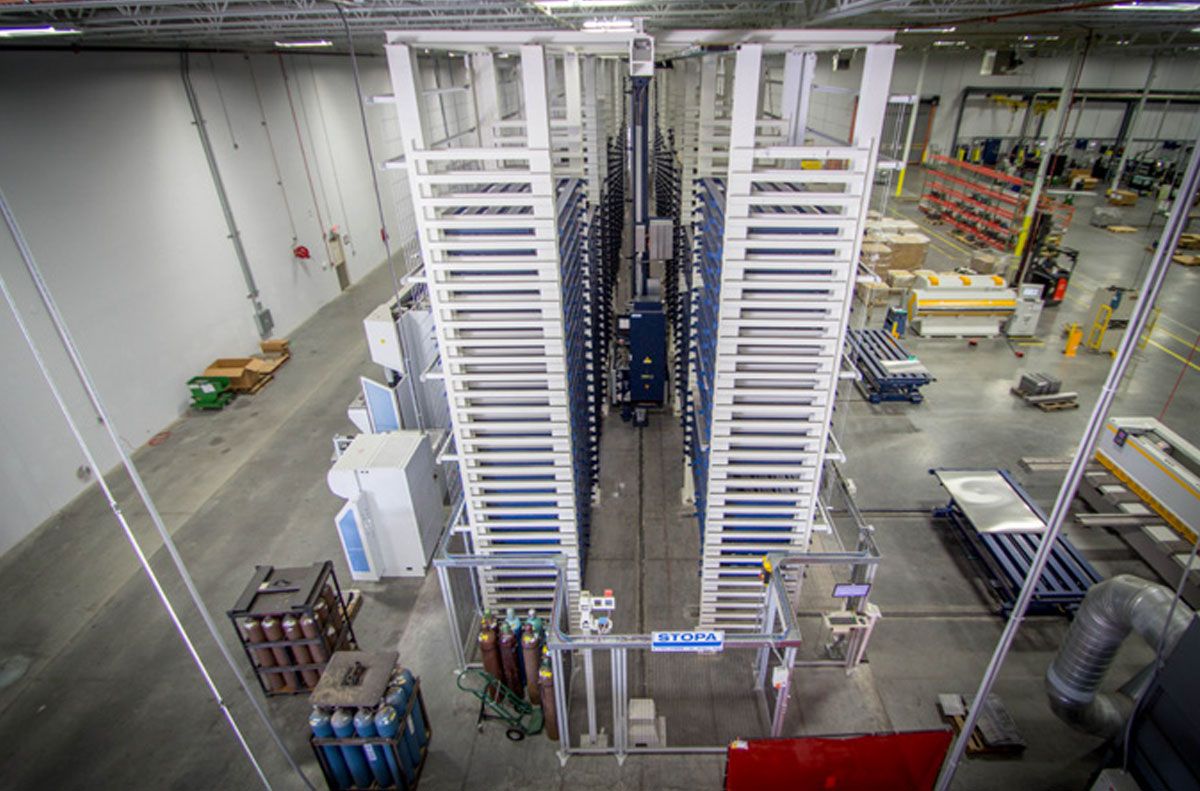
The use of a particularly powerful storage and retrieval machine shortens material provision times and thus waiting times for employees, while at the same time increasing productivity at the stations.
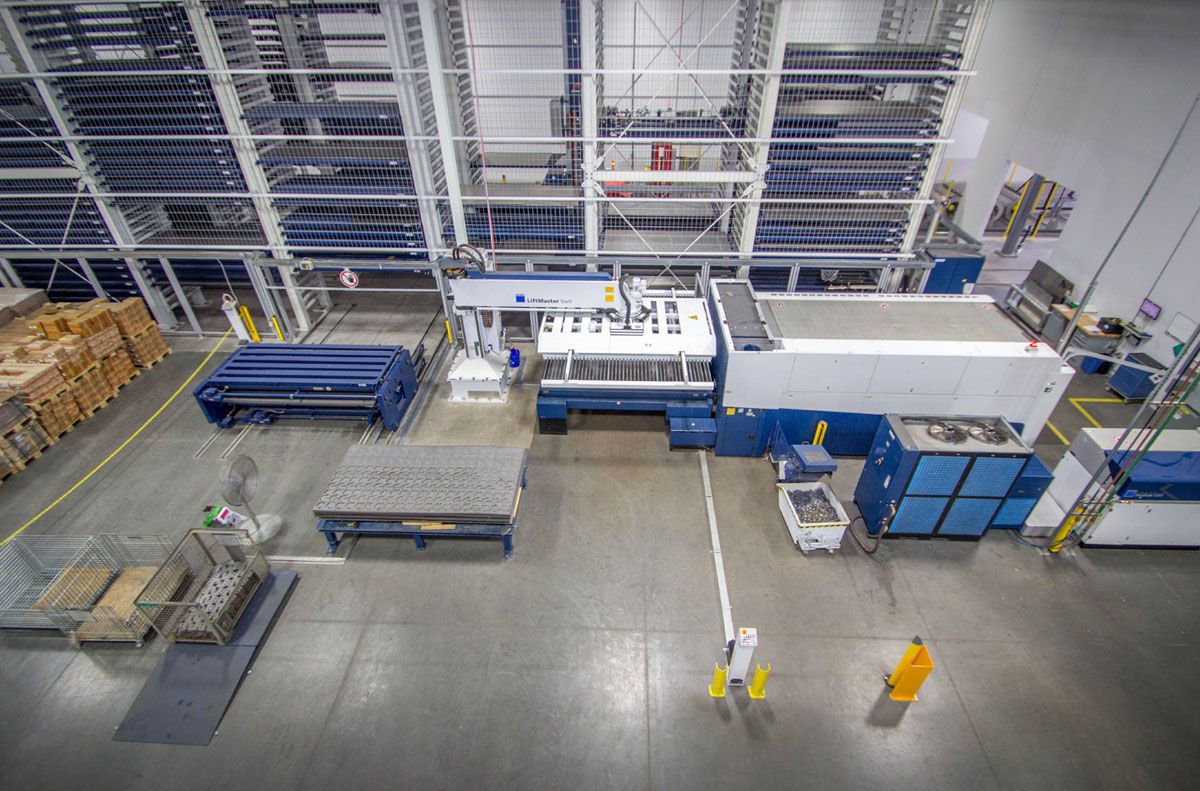
A double cart – consisting of a loading cart and an unloading cart in a portal design – transports sheets from the warehouse to a laser cutting machine and back to the semi-finished products.
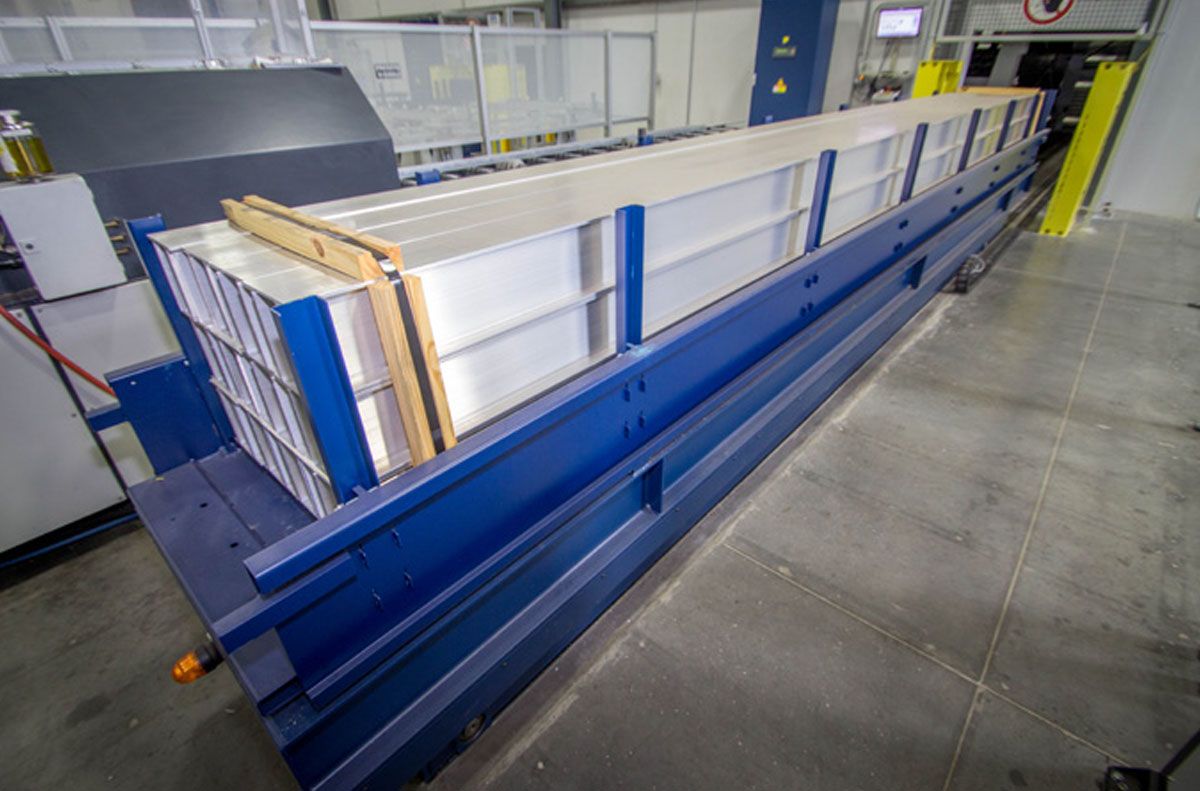
The cassettes, which are 830 x 600 x 6,626 millimeters (W x H x D) in size and designed for a maximum payload of 1,500 kilograms each, serve as load carriers.
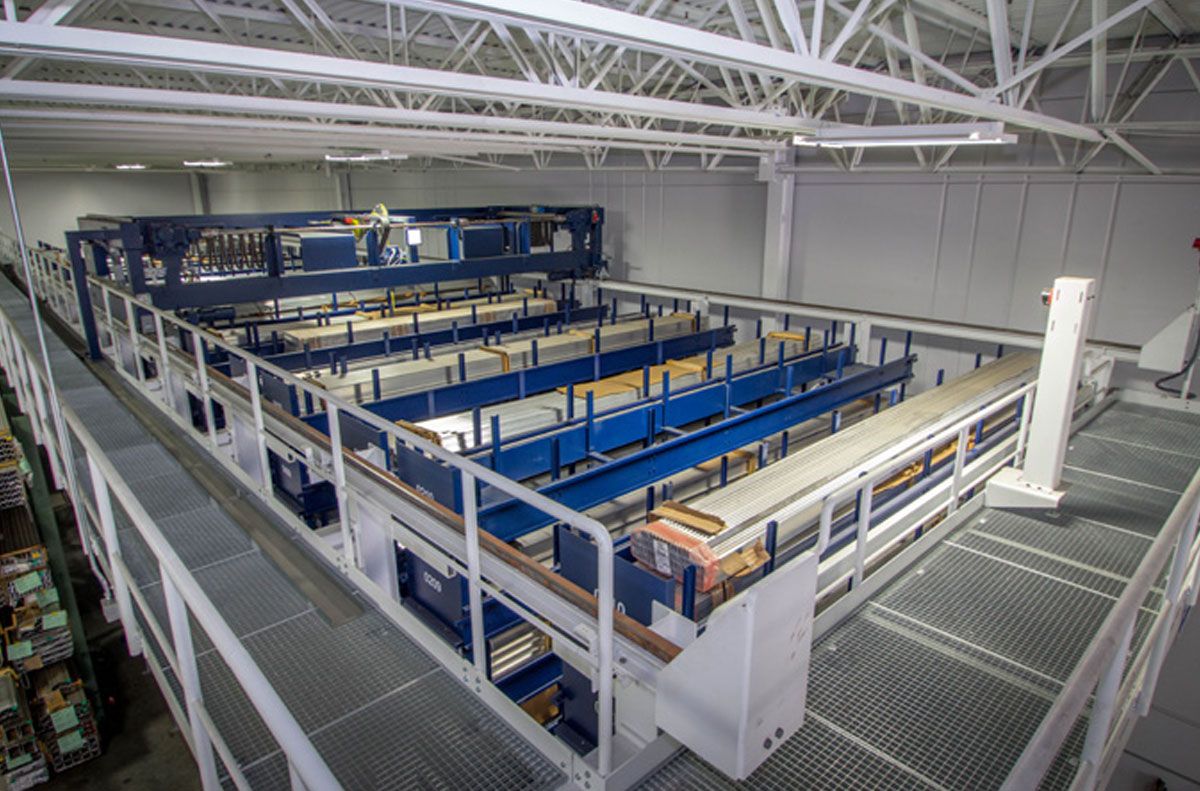
A traversing storage and retrieval machine stores and retrieves the cassettes in the twelve aisles of the long goods store.
In the STOPA LG-B1.5 long-goods store, which went into operation in August 2013 and handles five to six tons of material per shift, Schletter mainly stores aluminum extruded profiles. The load carriers are 222 cassettes, each measuring 830 x 600 x 6,626 millimeters (W x H x D), which are designed for a maximum payload of 1,500 kilograms each. A stacker crane stores the cassettes in and out of the twelve aisles of the system. The storage system, which is around 8.5 meters high, 34.5 meters long including the maintenance bridge and 7.3 meters wide, supplies the connected saws, which Schletter operates manually, automatically and semi-automatically, via four retrieval stations. The long-goods storage system is also equipped with a storage station. Hackner unfolds a drawing. “Since the system is installed near the goods receipt and the saws, we have short distances to the machines. However, the main advantage of the long-bar storage system is that the sawmill has considerably more production space available due to the space-saving storage of the profiles, and we are able to provide our employees with convenient material handling.”
The requested profiles are transported directly to the saws by the stations in automatic mode, monitored by scanners. As a result, the operators save time, which they can use for machine loading and thus for productivity increases. Additional time savings are achieved by pre-storage locations at the retrieval stations, which the system uses to minimize the cycle times of the material supply.
STOPA has also solved the issue of returning material to storage in the sawmill. This is an important point, as it is often necessary to return a half-open bundle to storage. This is especially the case when the extruded profiles come from the extrusion plant in larger bundles and are not always processed immediately in this quantity. When returning material to storage, the weighing equipment at the stations makes it easier to record the stock.
Data exchange via SAP-certified interface
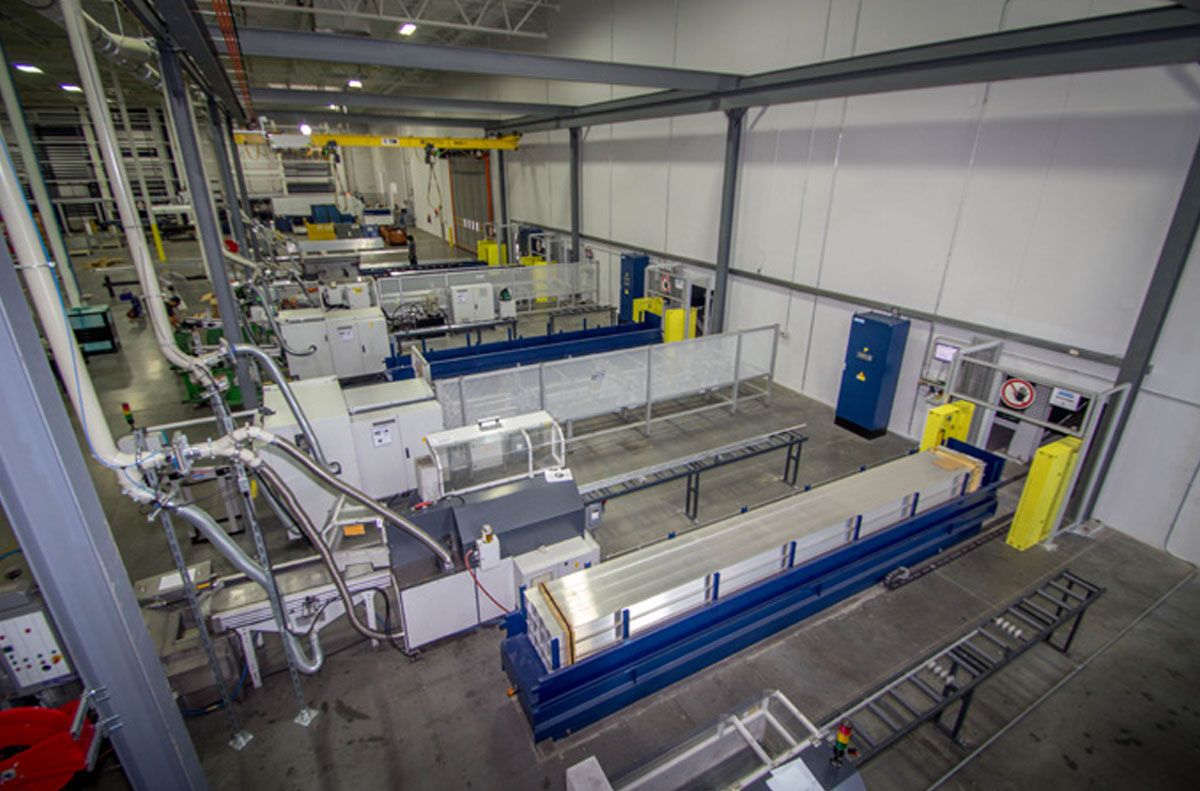
The long goods storage system supplies the connected saws via four short-distance retrieval stations.
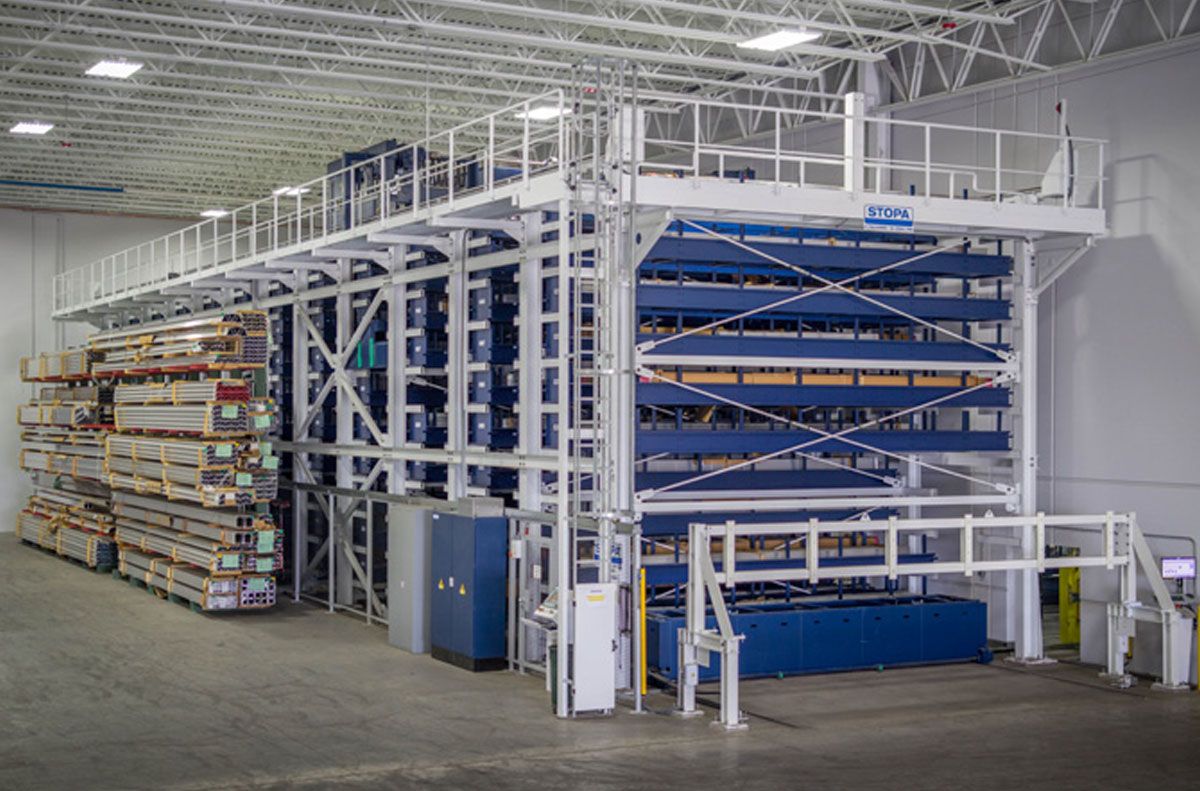
The main advantage of the long goods storage system is that the sawmill has considerably more production space available due to the space-saving storage of the profiles.
The system control for the sheet metal storage system consists of an industrial PC with an integrated slot PLC, while the long-bar storage system has an integrated soft PLC. Both warehouses are connected to the operator’s ERP system, which was supplied by SAP. Data exchange regarding warehouse stocks and material requirements for work orders is carried out via an SAP-certified IDoc interface. This is a proprietary transport protocol that is used to map the warehouse management in the SAP system. The ERP system always keeps the master data and the complete inventories up to date. The company also plans production orders in the SAP system, which sends them as transport orders to the STOPA warehouse management systems (WMS).
The LVS of the sheet metal warehouse dynamically (chaotically) allocates the materials to the storage locations, manages the tare weights of the pallets, processes manually initiated storage and retrieval orders, controls and monitors transport orders and performs diagnostic functions.
Once the profiles that were stored in a long goods cassette have been completely processed, the cassette is returned to an empty cassette pool. The operator then requests a new cassette for the new material and posts the goods receipt to it. The WMS manages the profiles and the standardized cassettes.
Hackner is leaning against the control panel of the sheet metal storage system, which is easy to operate via its graphical user interface. “Before making our decision, we looked at three alternatives. We ultimately chose STOPA because of the price, the high availability, which is 99 percent as promised, and the service that STOPA also offers in the USA. STOPA’s experience and close cooperation with TRUMPF and RAS contributed to the success of the project. We expect the payback period to be five years.”
Author: Jürgen Warmbol
Sales Contact Person
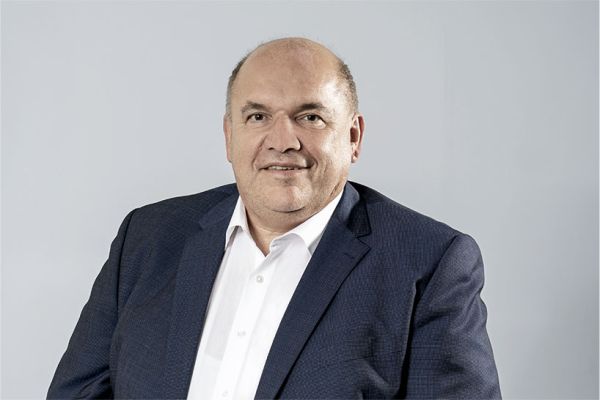
Holger Dehmelt
Sales Engineer Warehouse Technology
STOPA Anlagenbau GmbH
Industriestr. 12
77855 Achern-Gamshurst
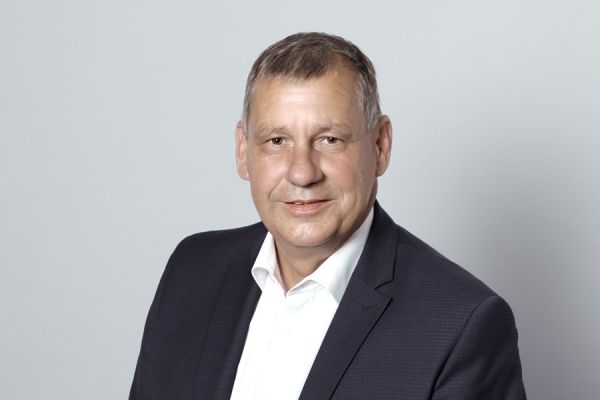
Rolf Eckhardt
Sales Engineer Warehouse Technology
STOPA Anlagenbau GmbH
Industriestr. 12
77855 Achern-Gamshurst
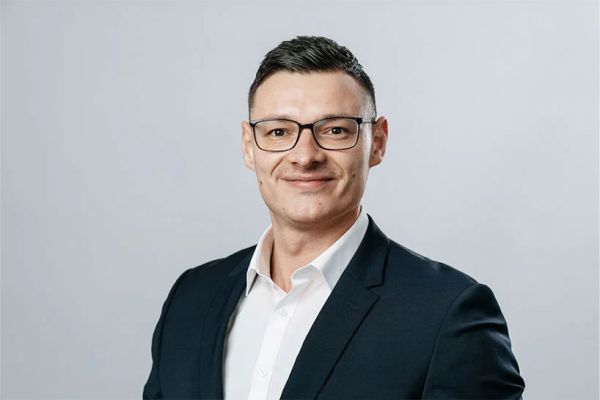
Andreas Pahl
Sales Engineer Warehouse Technology
STOPA Anlagenbau GmbH
Industriestr. 12
77855 Achern-Gamshurst