A Long Storage System for Short Distances
By investing in a 100-meter-long STOPA UNIVERSAL automatic storage system, the sheet metal processing company Schickling benefits from short distances to its laser cutting and punching machines, a closed process chain, low-manpower processes and higher productivity. In addition, it can buffer more material in stock and therefore purchase it more cheaply.
Hermann Schickling, managing director of H. Schickling GmbH Maschinenbau, Visbek, is leading the way. A push of a button on the control panel of the laser cutting machine is all it takes to trigger the processing order. “From now on, everything is automatic. The machine control system instructs the warehouse to retrieve the required sheets. The storage and retrieval unit removes the system pallet from the rack and transfers it to the transport carriage, which moves into the loading position. The loading component of the laser cutting system is waiting there to continuously supply the machine with sheet metal plates.«
Over 40 tons of material per day
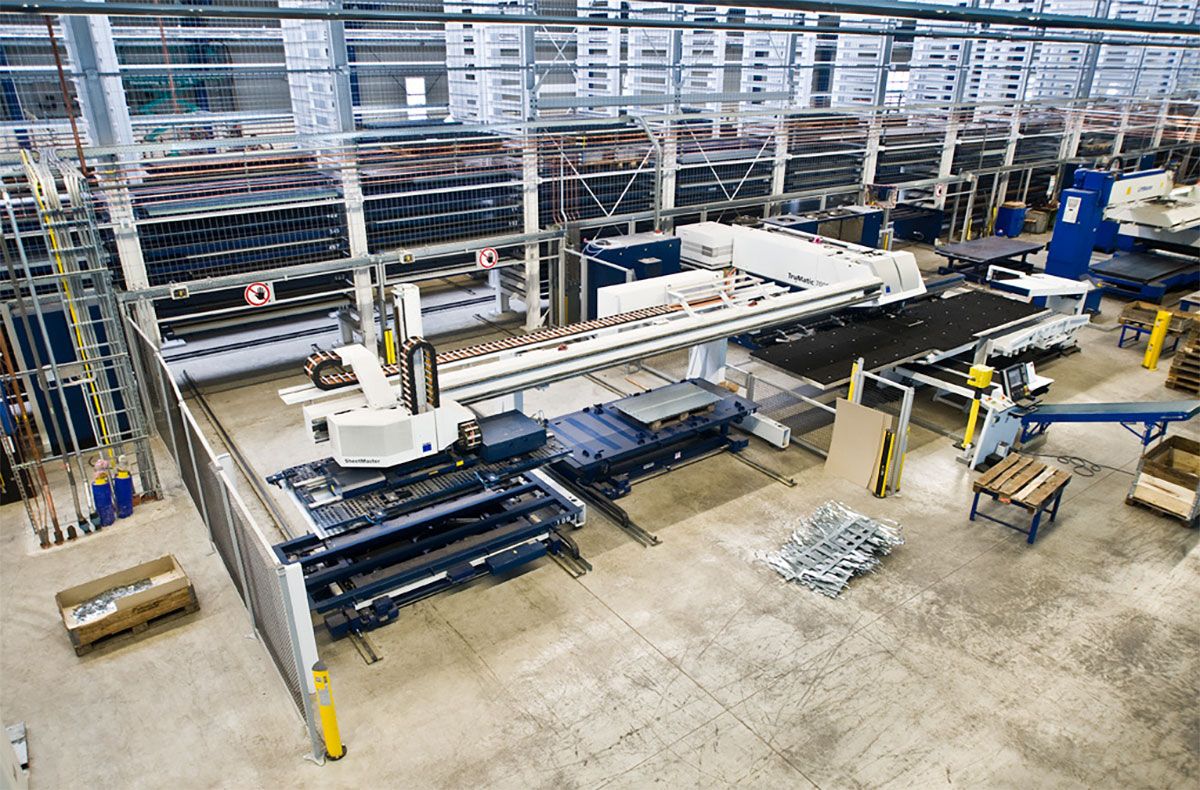
Due to the larger working area of the handling component, Schickling uses parallel loading and unloading carts at this station.
In view of the daily material handling of 40 to 45 tons, the automation solution, which went into operation in summer 2010, is already indispensable. Especially since all the sheets run through the STOPA UNIVERSAL system supplied by STOPA Anlagenbau GmbH, Achern-Gamshurst. And that five days a week, around the clock. And every Saturday until midday, and then, together with three or four machines and a small team of supervisors, until Monday morning. But the system is nowhere near its capacity limit, because the operator is currently only using just under half of the storage volume, which is designed for growth.
During the tour of the new hall, Hermann Schickling climbs up to the gallery. “From up here, you can see how the warehouse is integrated into our production and what an important role it plays there. With the high travel speed of the storage and retrieval machine of up to 150 meters per minute, the system creates the conditions for supplying all laser cutting and punching machines with material in a timely manner and for clearing them of residual sheets.”u
The company’s decision to invest in the automatic sheet metal storage system, while also purchasing additional processing machines and connecting them to the storage system together with the old systems, was made on the basis of the positive business development. “Without a central storage system, we would have had to tear apart our process chain,” emphasizes Hermann Schickling. “Now we are manufacturing more productively, flexibly and economically. Because now it is possible to store sheets back, to work with few people and to buffer larger quantities of material. An advantage that allows us to achieve lower purchase prices.” The STOPA UNIVERSAL system also limits the use of forklifts to incoming goods and to transporting finished parts. Previously, forklifts also supplied the machines and stored sheets in an old shelf, often damaging the material in the process.
Company
Schickling Maschinenbau GmbH: Perfection in metal construction
H. Schickling Maschinenbau GmbH, Visbek, was founded in 1988 and offers sheet metal processing services in the areas of laser cutting, bending, deep drawing, welding and machining. Together with its customers, the company develops the optimal and most economical variant of each part. The spectrum ranges from simple cuts to fully assembled complex assemblies made of various materials, which, if desired, can also be surface-treated. Since the sheet metal specialist has been growing steadily for years, it regularly invests in modern production processes. The steel of various grades that the Visbek-based company processes can be found, for example, in stable equipment, disposal vehicles, in storage and conveyor technology, in office furniture and heating systems, as well as in medical and laboratory technology. In addition, Schickling, which employs around 250 permanent staff and up to 30 temporary staff, manufactures high-quality stainless steel grills for leisure and garden use under its own brand name ›Edel-Design‹.
Large machine park
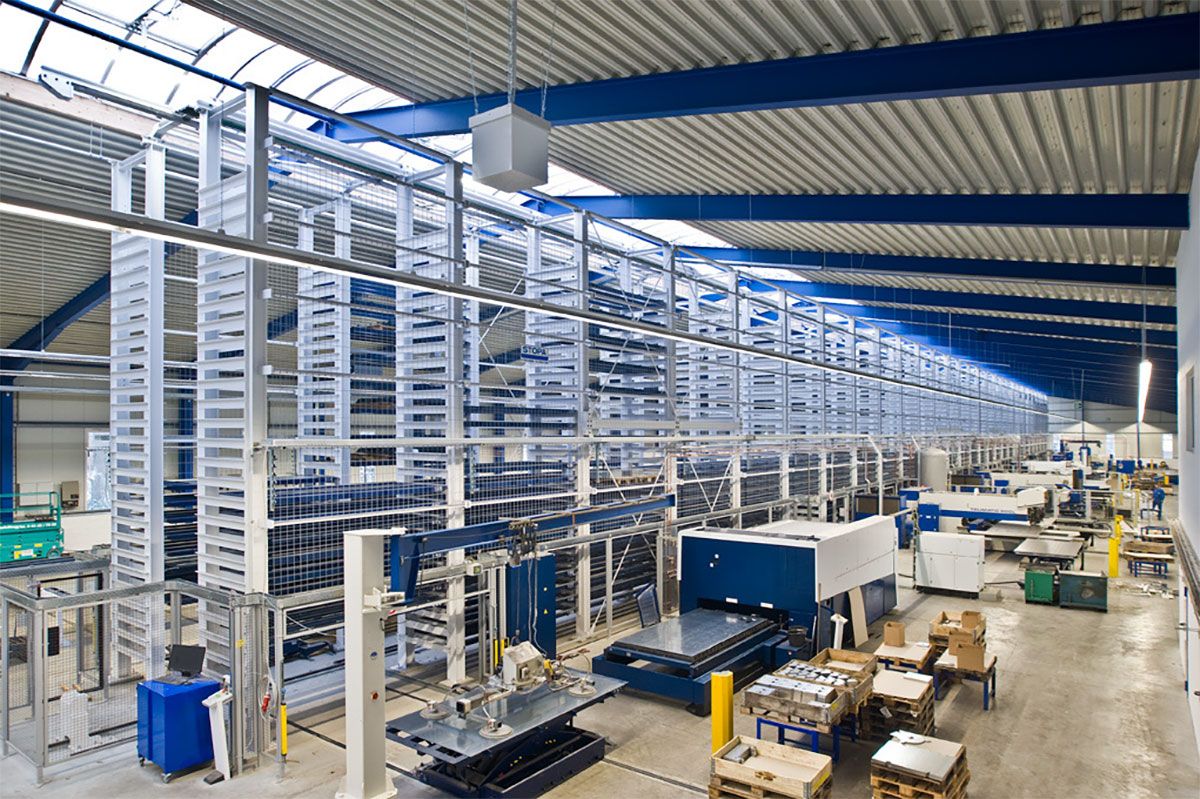
The STOPA UNIVERSAL storage system integrated into Schickling’s production process supplies all of the operator’s laser cutting and punching systems with material in line with the cycle times.
Seven flatbed laser machines and three combined laser cutting and punching systems from TRUMPF are connected to the storage system, which mainly stores galvanized sheets with thicknesses of 0.5 to 20 millimeters, via short distances and access times. Hermann Schickling stops between two stations. “Depending on the size of the work area in which the respective handling component is moving, STOPA has installed parallel loading and unloading carriages or double carriages arranged on top of each other, including contour control. The lower carriage of a double carriage station delivers material, while the upper carriage returns lasered parts to the warehouse. All transport carriages work parallel to the main time and without an operator.” Two of the stations that supply the combination machines are also equipped with a spreading magnet device on their scissor lift tables, which serve as loading carts, for safe sheet separation. The transport carts used for unloading use rotary encoders for precise positioning. In addition, the last sheet is automatically recognized at each loading station.
Hermann Schickling points to a highlight of the automation solution. “At the beginning of March 2011, we had the laser flatbed machine ›Tru-Laser 5030 fiber‹ connected directly to the warehouse via a ›LiftMaster compact‹. Part of the handling component has even been integrated into a storage block that STOPA converted for this purpose. This eliminates even the short travel distance from the warehouse to the processing machine.”
A scissor lift table also moves in the incoming and outgoing goods station. It is equipped with storage stamps and pluggable stops for a coordinate corner, which helps to align the sheets exactly. A forklift truck fetches the material from an unpacking table, which also has support stamps. Since these are movable, they can be adapted to all wooden pallets used as load carriers in truck transportation.
The automatic warehouse also has five pure outbound and return stations. Their scissor lift tables have recesses in the lower area of the front sides. Hermann Schickling asks one of his employees to insert the forks of a forklift truck into the recesses and at the same time to insert the raised fork runners into the entry opening of the Euro pallet that is lying on the system pallet of the lifting table. “It is only thanks to this solution that we can get the forklift truck close to the scissor lift table. This is essential for lifting europallets loaded with sheet metal parts from a system pallet and transporting them to the press brakes in the adjacent hall, for example.” To enable the company to make even greater use of the flexibility of the warehouse, it uses storage racks in which it stores cut and folded semi-finished products in addition to all the raw sheet metal qualities.
Automatically efficient
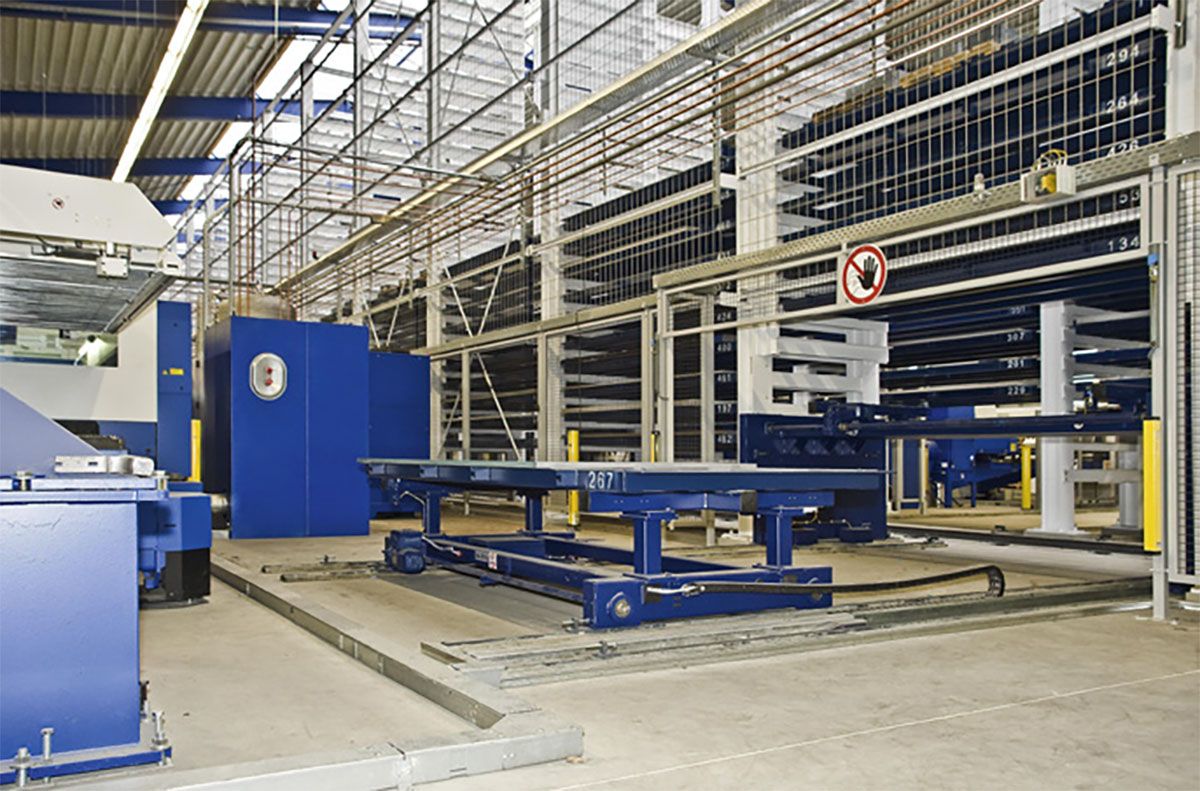
Since the handling component of this station always picks up and sets down the material in the same position, STOPA has installed space-saving double carts that move above each other for storage and retrieval.
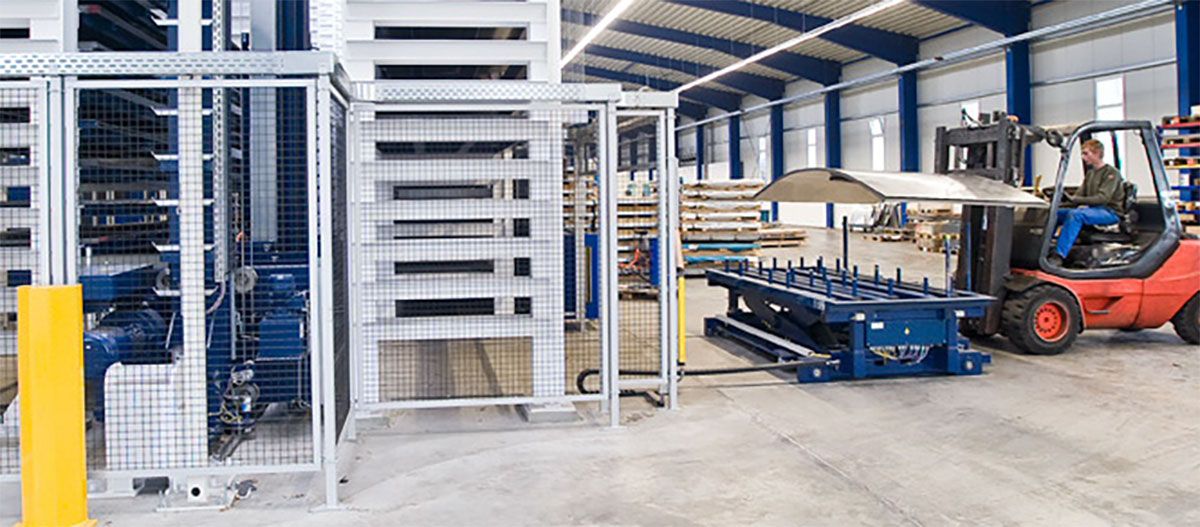
The scissor lift table of the incoming and outgoing goods station is equipped with storage stamps and pluggable stops for a coordinate corner, which helps to align the sheets exactly.
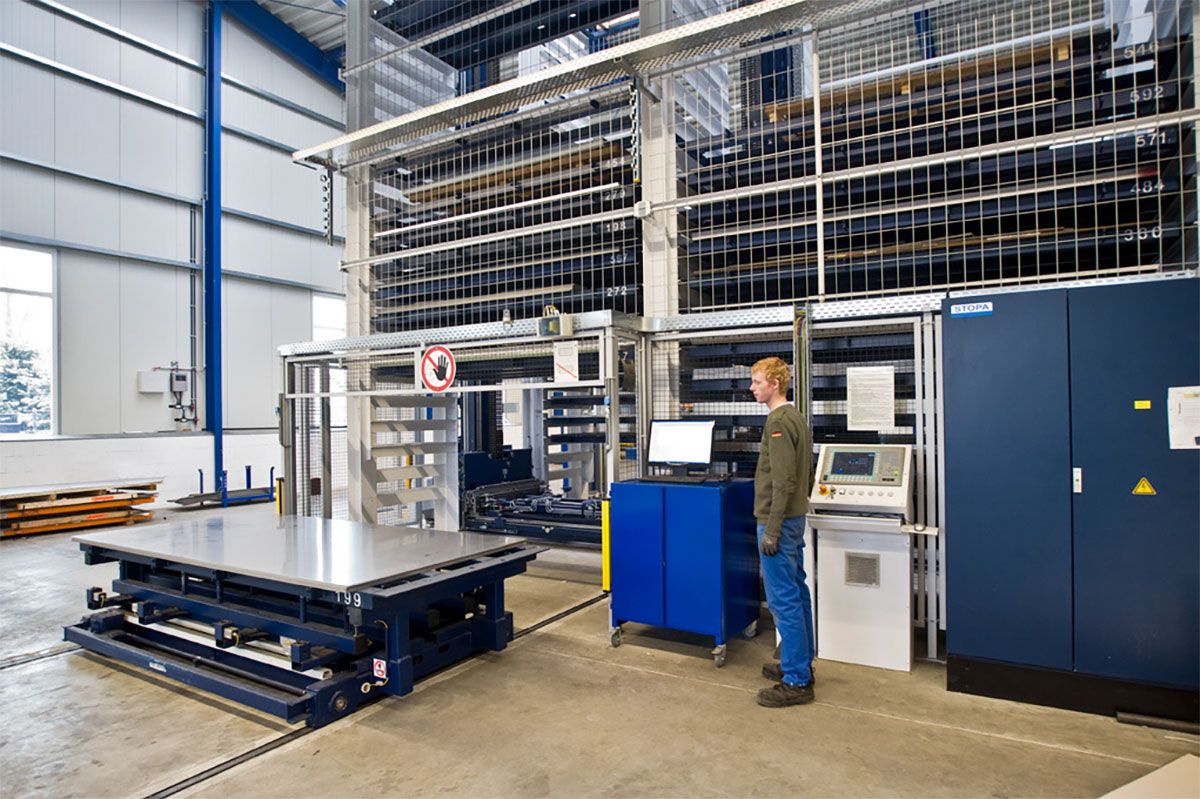
A Schickling employee has entered the command to store the delivered sheets into the system control.
The STOPA UNIVERSAL storage system is 107.5 meters long, 9.5 meters high and 5.2 meters wide. It has 1,464 storage locations in 56 rack blocks, which are arranged in two rows along a rack aisle. On the upper level, material can be stored up to four times the loading height. Currently, 480 flat pallets with a surface area of 1,525 x 3,050 millimeters are in the system. The load carriers are loaded with large and medium-sized sheets up to the full payload of 3,000 kilograms. If the operator returns sheets or semi-finished products to the warehouse that are not securely positioned on at least two pallet longitudinal profiles, or if he stores mesh boxes, he must place perforated floor plates on the system pallets.
The stable and robust double-mast storage and retrieval machine stores and retrieves with a fork that can be telescoped on both sides. A digital distance measuring system guarantees exact longitudinal positioning. A further digital distance measuring system, which works absolutely and independently of the load, makes it possible to position precisely in height without having to approach a reference point. Data flows contact-free and wear-free via light barrier to the shelf operating device. STOPA also ensures low-wear and low-noise operation by supplying the energy via an overhead conductor rail. A weighing device integrated into the load beam also records the weight when the sheets are stored or retrieved. And a contour check is carried out by the system before retrieval to ensure that the sheets do not protrude over the edge of the pallet.
At Schickling, the STOPA UNIVERSAL storage system is designed for maximum loading heights of 130, 410 and 970 millimeters. For safety reasons, the sheet metal processing company has the storage locations above and below a selected storage location monitored by an automatic collision control system to ensure that they are not occupied. The system stores items in free locations dynamically or randomly, with the exception of wire mesh boxes, which are only stored on the upper level. When retrieving items, the control system uses a light barrier to ensure that the permissible loading height of the respective transport cart or scissor lift table is not exceeded.
A real-time soft PLC controls the system components of the storage system. The operator uses the industrial PC integrated into the programmable logic controller to operate and display the system statuses. The system control communicates with the warehouse management computer via an interface supplied by STOPA. The software manages the stocks and the sheet metal data and allows a permanent inventory to be carried out at any time, providing an insight into the current stocks. The system is operated conveniently using easy-to-understand function keys. An employee demonstrates how the status of the shelf operating device can be read continuously and in plain text on the 12-inch TFT display of the ergonomic control panel and how the software graphically visualizes the storage blocks and the shelf operating device. Should a fault occur, STOPA can access the remote maintenance software PC Anywhere and the control modem to analyze and rectify the error from their own location.
Economic solution
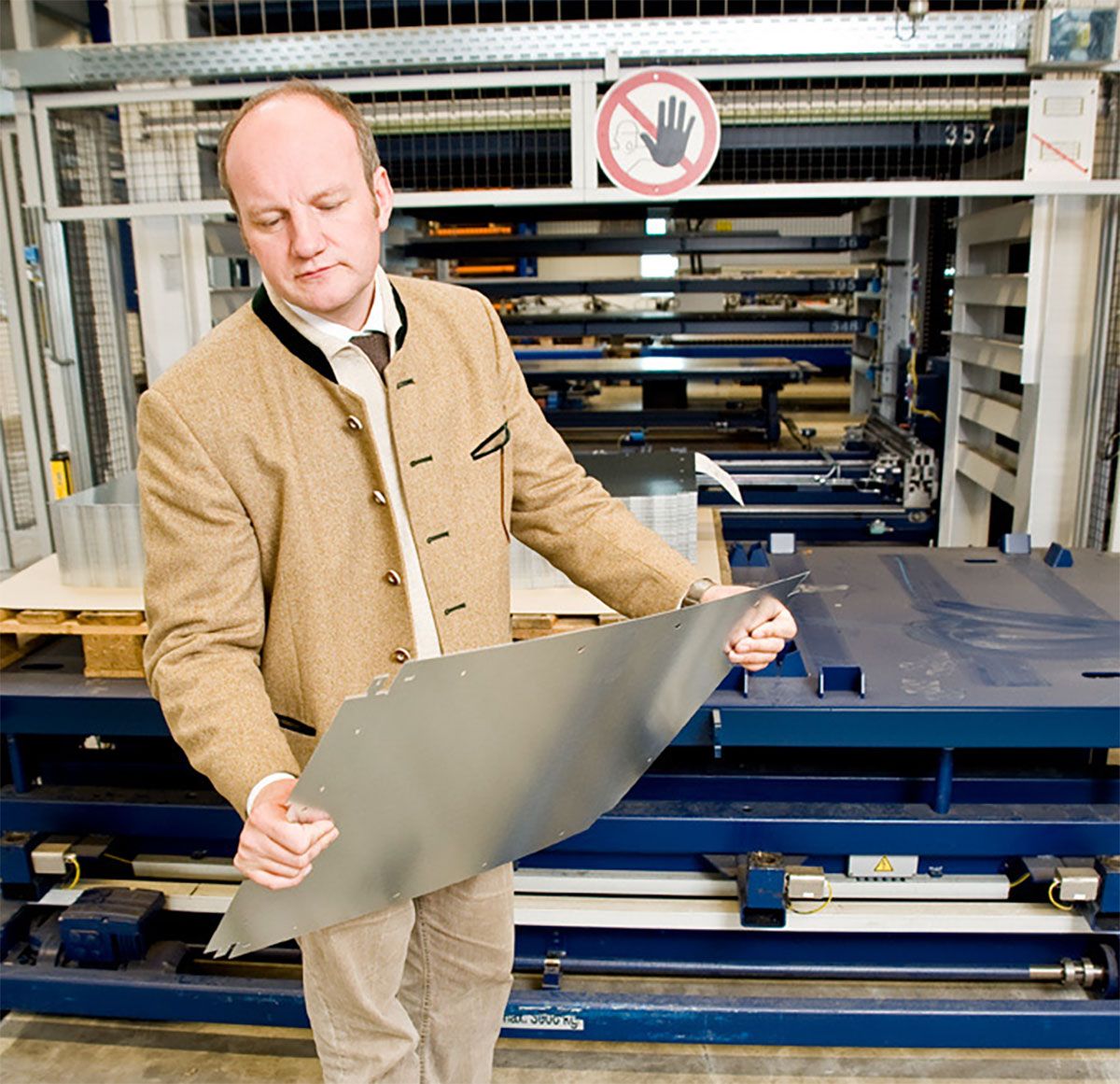
“Without a central warehouse, we would have had to break up our process chain,” emphasizes Hermann Schickling, while examining the quality of a sheet metal part.
The STOPA UNIVERSAL system is a very economical solution simply because the sheet metal storage system achieves a significantly longer service life than the associated processing machines. The system also promises cost-effectiveness in view of the faster material provision and the resulting continuous utilization of the system. In addition, Schickling is able to increase his capacity by operating with fewer staff. Apart from that, he can operate more machines and the storage system at the same time with the same number of staff.
Furthermore, the system enables the operator to plan processing times and the entire order processing more easily and more accurately. The improved quality of the parts, which results from the gentler sheet metal handling, also contributes to the cost-effectiveness of the storage system. The approximately 50 percent shorter throughput times provide a further economic advantage. Manual ancillary activities, such as material search and provision, are no longer necessary due to the optimized organizational processes. What’s more, the modular STOPA UNIVERSAL system is expandable. A forward-looking concept that allows the warehouse to be adapted to new production environments. In addition, automation results in greater occupational safety. There is also a significantly lower space requirement for the same amount of material, as the warehouse uses the entire height of the hall.
The STOPA UNIVERSAL system at Schickling also scores extra points in terms of cost-effectiveness thanks to the brackets on its steel structure. This is a special solution that allows the sheet metal worker to lay his supply lines quickly and conveniently. You can see how satisfied Hermann Schickling is. “But in addition to the economic aspects, it is also important to me that we can continue to employ our entire team. That was one of our goals. Especially since we have invested in the automated warehouse not least because of our continued growth.«
Sales Contact Person
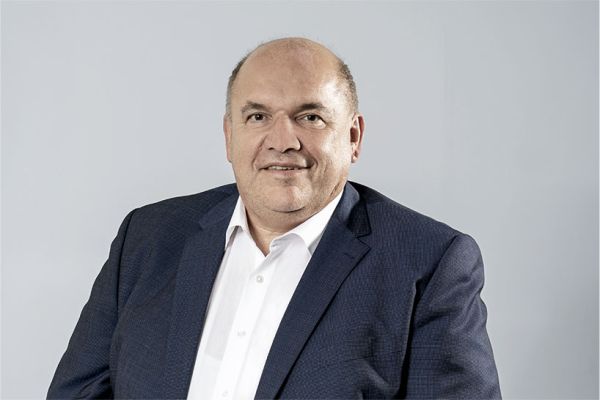
Holger Dehmelt
Sales Engineer Warehouse Technology
STOPA Anlagenbau GmbH
Industriestr. 12
77855 Achern-Gamshurst
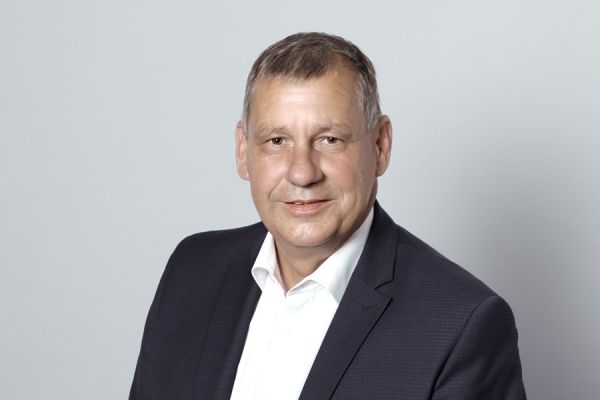
Rolf Eckhardt
Sales Engineer Warehouse Technology
STOPA Anlagenbau GmbH
Industriestr. 12
77855 Achern-Gamshurst
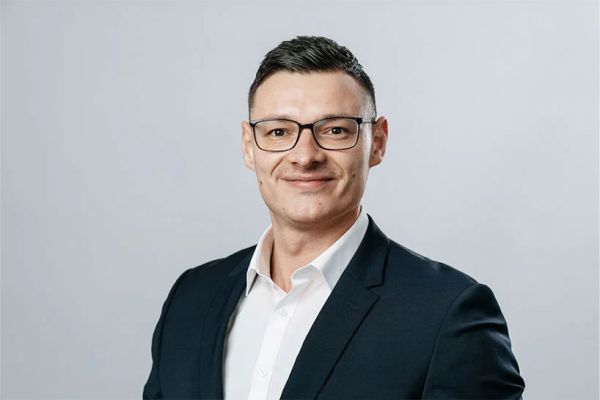
Andreas Pahl
Sales Engineer Warehouse Technology
STOPA Anlagenbau GmbH
Industriestr. 12
77855 Achern-Gamshurst