sheet-metal storage system with customer-specific warehouse management software
Aesculap AG, based in Tuttlingen, has invested in an automatic STOPA COMPACT sheet metal storage system with a modified warehouse management system (WMS). The software’s special features include the management of special stocks and materials subject to batch control, machine-oriented storage of certain sheet metal plates, an individual SAP-BDE-WMS interface for transferring order data to the WMS, and extensive reporting functions.
The automated warehouse went into operation at the end of 2014 in the new Innovation Factory of medical technology manufacturer Aesculap, the second-largest division under the umbrella of B. Braun Melsungen AG. Thomas Philipp, plant manager of the intelligent factory, where around 500 people work, presents the project in Tuttlingen. “We manufacture separately on two levels. The ground floor is where we manufacture aluminum and stainless steel containers, as well as storage trays for storing medical products during the sterilization process. The upper floor is where we manufacture compressed air and cable-connected motor systems for surgical procedures. When planning the Innovation Factory, in which we have invested around 50 million euros, we paid particular attention to structural and technical flexibility and energy efficiency. Thanks to the generous design of the permissible ceiling loads, we can also use machines weighing up to 26 tons on the upper floor. In addition, the production and administrative areas, which currently have usable floor space of around 14,000 and 2,800 square meters respectively, can be expanded.«
Before investing in the automatic sheet metal storage system supplied by STOPA Anlagenbau GmbH, Achern-Gamshurst, Aesculap stored the raw material separately from the production area, which meant that a great deal of logistical effort was required. “In view of this situation, we analyzed our processes, wrote a specification and drew up a comprehensive list of activities,” says Joachim Bludau, head of the sheet metal segment at the Motors & Containers plant, who discovered his enthusiasm for sheet metal forming at an early age. ”The agenda included, for example, a controlled material flow, direct access to raw materials and greatly reduced downtime. However, our main requirement was for a customer-specific orientation of the warehouse management system.”
Extensive modifications
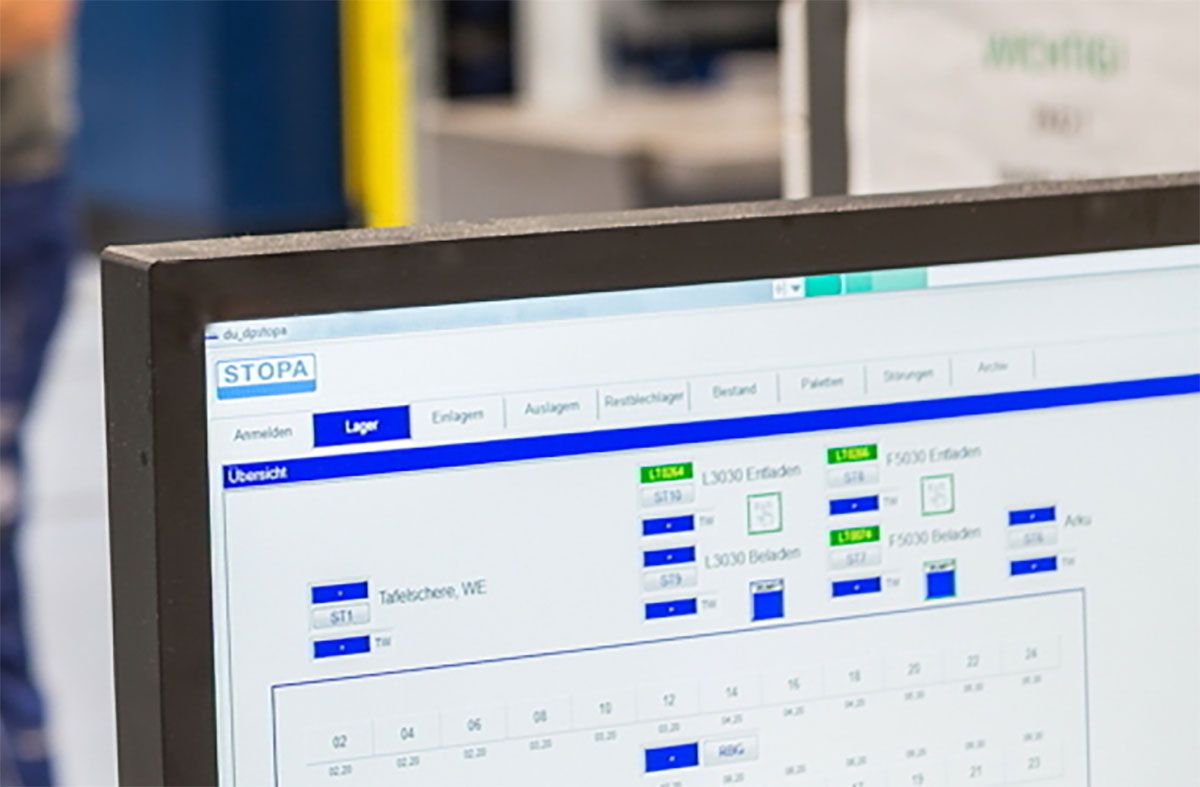
STOPA has customized the warehouse management system for Aesculap
The modifications to the STOPA WMS-Dynamic, which, among other things, manages stocks and storage locations and supplies the processing machines with material as part of its basic functions, have been very extensive. For example, WMS-Dynamic checks whether the operator has stored the relevant sheets on the pallets provided for each incoming batch of sheet metal. The system calculates the necessary quantity of raw material before the order is started. If the available material is insufficient, the order is not started at all and the employee is informed. Stock placements and removals are initiated via SAP transport orders, which the WMS then subjects to a plausibility check, including the weighed weight.
Other application-specific adjustments include the management of a consignment warehouse, a separate scrap sheet metal warehouse and blocked stock, which includes all newly stored materials until they have been checked and released. The WMS also allows sheets to be stored close to the processing machine with the designation ‘preferred machine’. Furthermore, the software reserves storage areas for certain materials, provides PDC data and various lists, posts all incoming and outgoing goods and fulfills comprehensive reporting functions.
Nadine Weckenmann, as the IT project manager, was responsible for the VPN connections to the processing machines and the WMS control. She also coordinated communication between the operator’s SAP system and the production data acquisition system, as well as between the connected laser cutting systems and the WMS-Dynamic. Nadine Weckenmann emphasizes the exceptionally good cooperation during the preparation phase. “We worked together very well during the time that STOPA modified the basic warehouse management system to meet our requirements. Before the contract was awarded, our team had sounded out the market, visited reference systems and, with a common goal in mind, held workshops at STOPA and TRUMPF based on the specifications.«
Highlights of the modified WMS
The STOPA WMS-Extended, which was customized for Aesculap, offers the following additional functions to the basic functions:
- Checking that each incoming batch of sheet metal is stored correctly.
- Calculating the required quantity of raw materials before each order is started.
- Plausibility checks including the weighed weight when storing and retrieving.
- Managing a consignment store, a separate scrap sheet metal store and blocked stock, which includes all newly stored materials until they have been checked and released.
- Storage close to the processing area. Also of sheets with the marking ›preferred machine‹.
Space-saving turning devices
Two new laser cutting machines have been installed parallel to the STOPA COMPACT, and the VPN network and the RCI interfaces from the STOPA WMS-Dynamic to the TRUMPF machines have been implemented. Meanwhile, production has continued in the old buildings on existing systems in order to be able to supply customers consistently. Volker Huber, group leader in sheet metal separation with many years of extensive experience in sheet metal processing at Aesculap, ranging from punching to laser cutting, has been involved in the project. Huber will be responsible for the system as WMS administrator in the future. The processes were developed together as a team and then implemented by STOPA in the WMS. “We stored and calibrated all 410 system pallets ourselves over a period of weeks. A technician from the manufacturer was on site to support us.« STOPA had previously provided the pallets with floor plates, as Aesculap stores not only 150 different materials, but also tapes and sheet metal strips.
Other ideas for the storage and provision of materials for the punching and laser technology area that STOPA contributed to the project include the integration and equipping of the transport trolleys used at the stations with turning devices. Without this technology, it would have been unavoidable to install the systems at right angles to the warehouse. This would have left less space for machines, so that Aesculap would have had to set up some of the systems in a second row – with the disadvantage of longer transport routes. The software solution for the sheet metal scrap storage system, in which the sheets are stored upright in a rack, is also interesting. Gerald Reischmann, production scheduler in sheet metal forming, demonstrates the benefits of the solution. “When the operator presses the touch screen, the WMS visualizes where in the warehouse a sheet of scrap metal corresponding to the order is available. In this case, the machine operator can choose between the scrap metal and a new sheet of metal from the storage system.”
A forward-looking decision
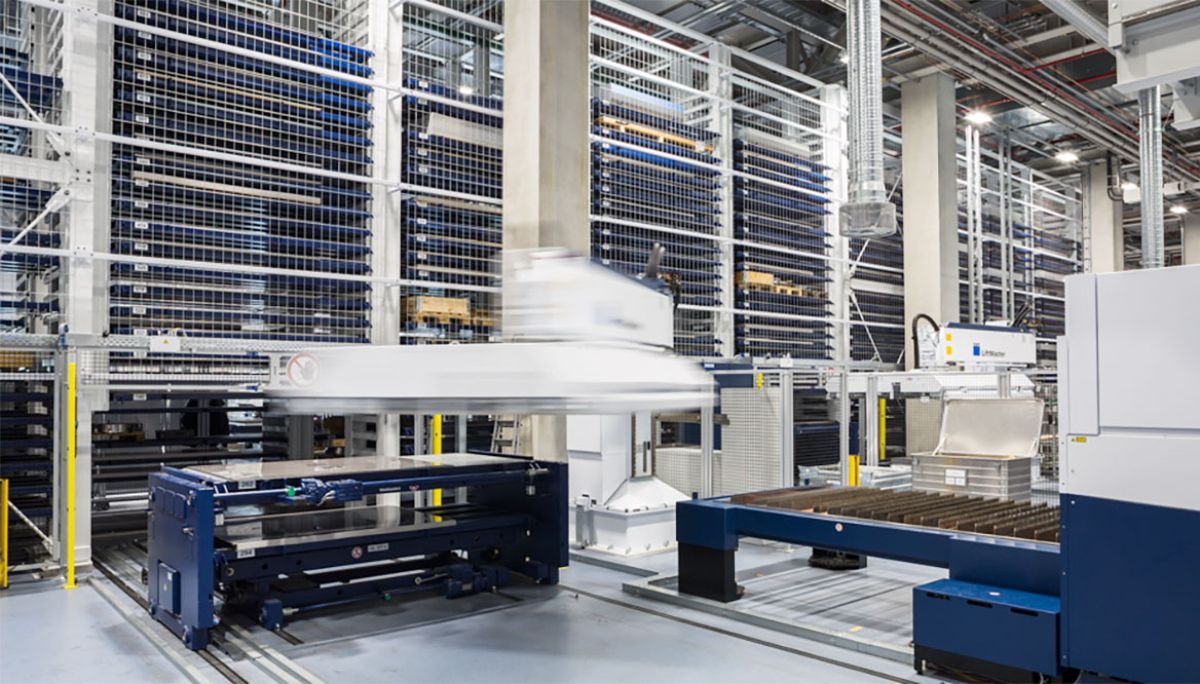
Aesculap has invested in an automated sheet metal storage system with a modified warehouse management system
The main focus of BBW Lasertechnik’s wide range of laser material processing is on laser fine cutting and laser welding. Other areas of expertise include processing with ultra-short laser pulses, bending with six-axis stops, component assembly and the entire package, from design and development to the final product.
The price-performance ratio and the combination of suppliers STOPA and TRUMPF, which excludes interface problems due to many years of experience, also contributed to the decision to invest in STOPA. The fact that all deadlines were met was not least due to the parallel planning of the building and the warehouse. The STOPA COMPACT II, which operates in two shifts with almost 100 percent availability, was launched in December 2018. Johann Bürger is already thinking ahead. “Since the sheet metal storage system can be expanded at any time in line with future requirements, we are focusing on the option of integrating a third station on the upper floor of the hall and connecting additional machines.”
Constructively and physically from a single source
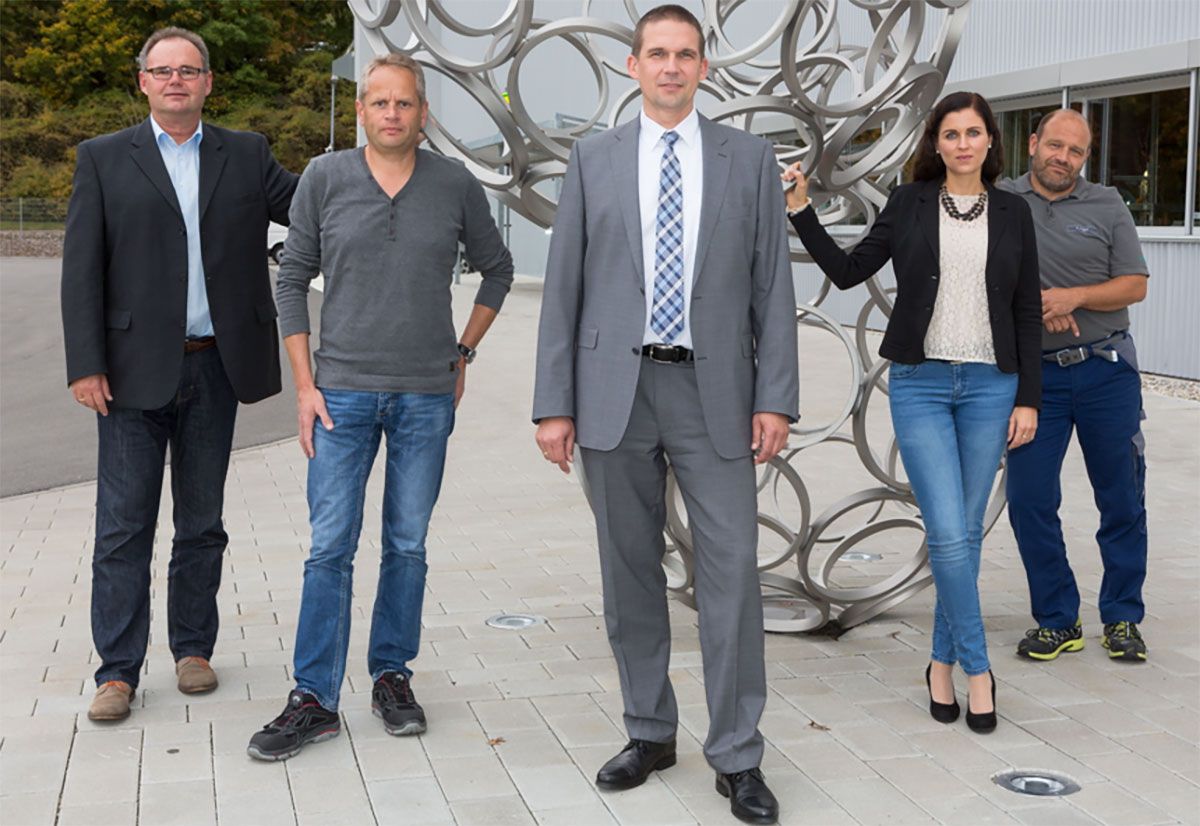
Thomas Philipp, plant manager of the Aesculap Innovation Factory (center), is proud of his team, which includes (from left to right) Joachim Bludau, segment manager for sheet metal at the Motors & Containers plant, Gerald Reischmann, production scheduler for sheet metal forming, Nadine Weckenmann, IT project manager, and Volker Huber, group manager for sheet metal separation
Aesculap had many reasons for deciding to install the 42-meter-long, 8-meter-high, 4.7-meter-wide automated warehouse with 685 storage locations. In addition to the advantages already mentioned, these include the option of retrieving goods according to the FIFO principle, a high level of user-friendliness and occupational safety, a permanent inventory, stock reporting and synchronization with the SAP system, and ultimately a high level of cost-effectiveness. In addition, an SAP-BDE-WMS interface, which transfers data from the production plan to the machines and the WMS, ensures reliable communication between the SAP system and the STOPA WMS-Dynamic. In the supplier combination STOPA/TRUMPF, there are also no interface problems due to many years of experience. In addition, it has been possible to link several machines, some with automatic air blast and suction technology, lubrication and punching laser technology. Bludau emphasizes that STOPA has built and developed the warehouse completely on its own. In addition to its high level of expertise, STOPA guarantees a fast and long-term supply of spare parts. Joachim Bludau mentions another success factor in the project: “STOPA has kept all its agreements and has also taken on topics that have arisen subsequently.”
Author: Jürgen Warmbol
Sales Contact Person
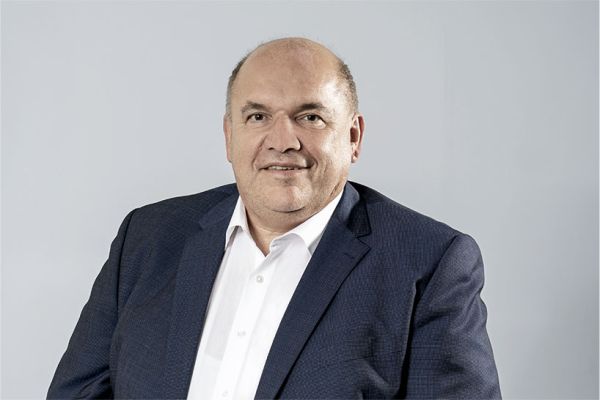
Holger Dehmelt
Sales Engineer Warehouse Technology
STOPA Anlagenbau GmbH
Industriestr. 12
77855 Achern-Gamshurst
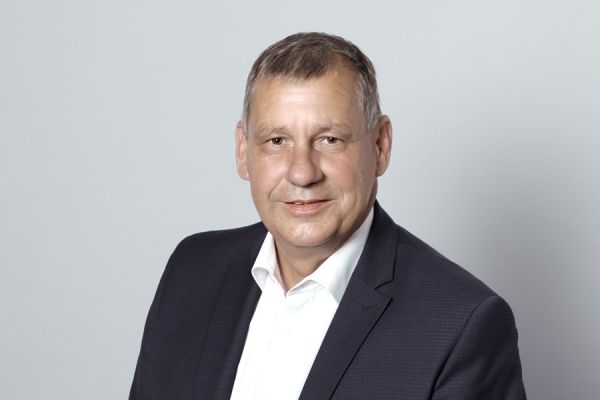
Rolf Eckhardt
Sales Engineer Warehouse Technology
STOPA Anlagenbau GmbH
Industriestr. 12
77855 Achern-Gamshurst
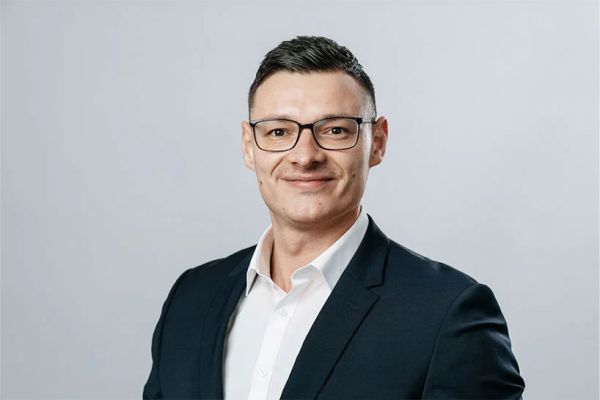
Andreas Pahl
Sales Engineer Warehouse Technology
STOPA Anlagenbau GmbH
Industriestr. 12
77855 Achern-Gamshurst