ECO and MONO sheet metal storage systems supply production
Precious materials wherever you look. Hans-Ulrich Maas, graduate engineer and operations manager at SCHAEFER GmbH in Sigmaringen, is showing us around the showroom. “Here, our customers will find a wide range of classic and modern design variants. We develop and manufacture everything in-house.” The product range of the company, which was founded in 1964, extends from elevator operating and display elements to buttons, panels and lift information systems, as well as access control systems, and also includes CANopen technology. Products for which the global player and technology leader processes a lot of sheet metal.
Maas goes to the production area, where STOPA Anlagenbau GmbH, Achern-Gamshurst, has installed the STOPA sheet metal storage systems. “We buffer all our sheet metal in the two towers. They are located directly next to our laser cutting and punching machine as a supply base for our production.” In addition to a STOPA MONO storage system that went into operation in 2004 and whose capacity was no longer sufficient due to increased sales, SCHAEFER invested in a STOPA ECO storage system in 2010. This means that the storage technology comes from a single source. An advantage that makes maintenance and service easier.
Compact towers
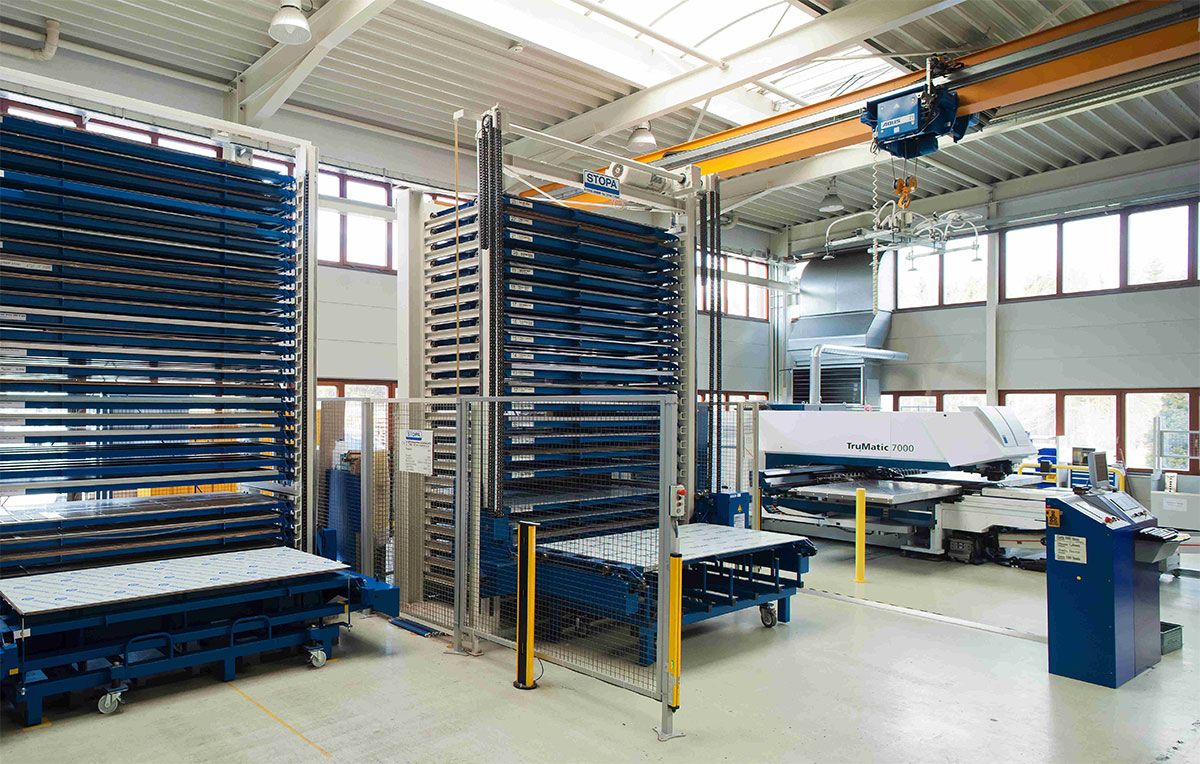
The STOPA sheet metal storage systems take up little space and are connected to the SCHAEFER laser cutting and punching system via short routes
The systems are single-sided tower storage systems with pull-out technology, in which the sheets are stored lengthwise. Flat pallets for medium-sized sheets (1,250 x 2,500 millimeters) serve as load carriers. The pallets and most types of sheet metal are assigned fixed locations.
Thanks to their compact design, the sheet metal storage systems achieve a high degree of space utilization in a small area and therefore only take up a small area in the production process. Since the STOPA ECO rack block is also equipped with a double height grid, the packing density can be optimized even further and higher goods can be stored. These are significant advantages compared to storage on the floor or in cantilever racks. The STOPA MONO, which is around 4.8 meters high, four meters long and a good three meters wide, offers space for 23 storage locations. The system’s easy-to-handle flat pallets are designed for payloads of up to 1,000 kilograms. The STOPA ECO has similar values. It is 4.7 meters high, 2.85 meters long, 3.6 meters wide and has 28 spaces. The maximum payload in this case is 1,200 kilograms. Light barriers check whether the loading heights of 70 or 60 millimeters are being adhered to.
Both towers work with a low-maintenance, stable and robust two-mast load traverse that is stored and retrieved by a pull/push device. A load-independent position measuring system ensures the highest positioning accuracy. To keep the flat pallets of the STOPA MONO in position on their inclined supports, they are equipped with self-supporting support rollers mounted on the front side. To enable the load cross beams or pallets to pick up the sheets, the operator first places the sheets on storage platforms that are equipped with storage stamps at a fixed height. The storage platforms can be moved on rollers to access the lowest locations.
The systems are operated via central control panels, on whose LCD displays all input steps and error messages appear in plain text. Once the employee has entered the storage location number and confirmed it by pressing a button, the STOPA ECO automatically processes the relevant order. In contrast, the control system of the STOPA MONO can store up to ten individual orders, which this system also processes automatically. After confirmed withdrawals, the storage control systems return the pallets to storage.
SCHAEFER operates the warehouses in two shifts. “In 2011, the turnover of the towers was 120 tons of sheet metal,” emphasizes Maas. “In terms of material, we only use medium-sized sheets, the majority of which are V2A steel in thicknesses of 0.8 to 3 millimeters and in various types of grinding.”
Fast and flexible processes
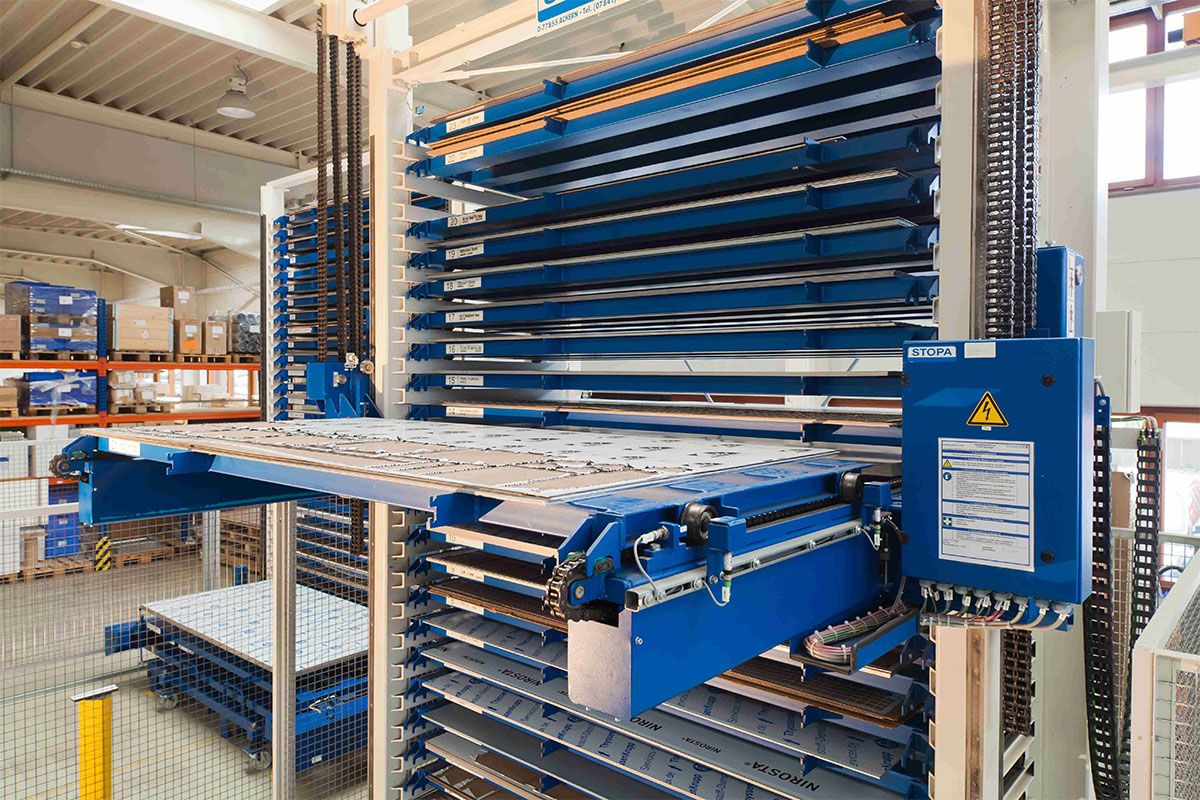
Both storage towers work with a low-maintenance, stable and robust two-mast load traverse that is moved in and out of storage by a pull/push device
Forklift trucks transport the delivered sheet metal packages to the STOPA ECO and place them on the storage stamps of the storage platform. After the system operator has given the go-ahead, the load traverse lifts the flat pallet in front of it to pick up the sheet metal package from the stamps and automatically moves it to its compartment. Maas: “If necessary, we store new material by packing it on pallets with the same type of sheet metal. We work according to the FIFO principle and place the new sheets under the existing ones. This is because the laser-compatible protective film on the sheets has a limited shelf life.«
The employee at the STOPA MONO uses a bridge crane and a vacuum suction gripper to take a sheet from the flat pallet that has been driven out of the warehouse and transfers it to the adjacent TRUMPF laser cutting and punching machine. “We supply the machine from the STOPA MONO, especially since this warehouse is closer to the system and we save time as a result,” explains Maas. “The STOPA ECO therefore mainly buffers supplies for the STOPA MONO, which we relocate as required.” In addition to saving time, a high level of flexibility is required. That is why SCHAEFER also demands almost 100% availability of the sheet metal storage system, which is additionally ensured by regular maintenance.
Author: Jürgen Warmbol
Sales Contact Person
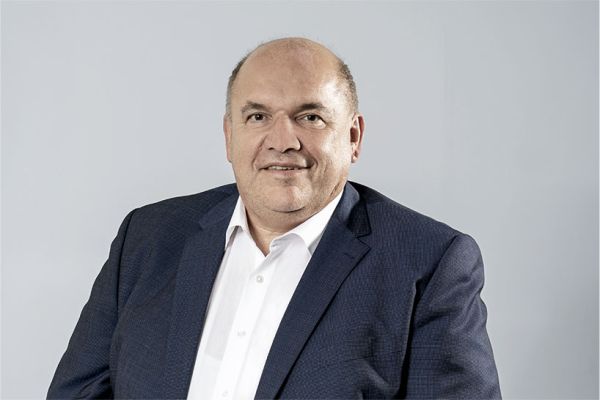
Holger Dehmelt
Sales Engineer Warehouse Technology
STOPA Anlagenbau GmbH
Industriestr. 12
77855 Achern-Gamshurst
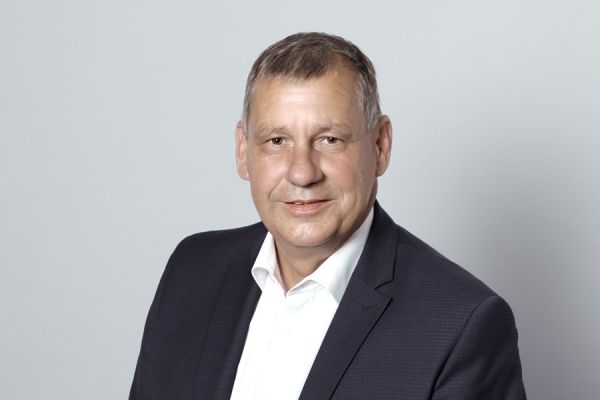
Rolf Eckhardt
Sales Engineer Warehouse Technology
STOPA Anlagenbau GmbH
Industriestr. 12
77855 Achern-Gamshurst
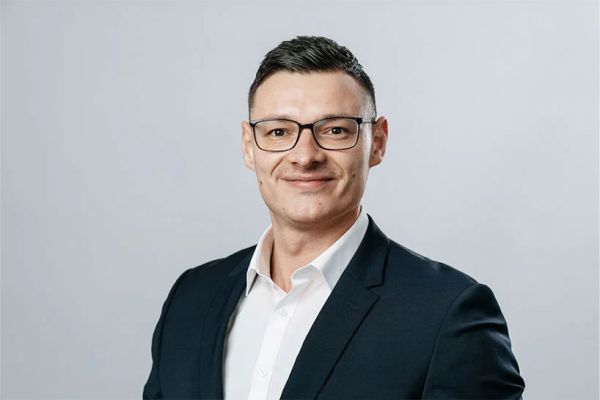
Andreas Pahl
Sales Engineer Warehouse Technology
STOPA Anlagenbau GmbH
Industriestr. 12
77855 Achern-Gamshurst