Meeting customer requirements with dependable processes
The expanded metal and perforated plate manufacturer MEVACO now supplies its processing machines reliably from a STOPA COMPACT automatic storage system. The sheet metal storage system enables the company to maintain its high delivery quality and continue to meet all customer requirements, despite a sharp increase in small-quantity orders.
Jochen Schott, Technical Manager at MEVACO GmbH in Schlierbach, spreads out samples of expanded metal and perforated sheets on the conference table to give an insight into the product range. “The MEVACO brand stands for reliability and a wide range of variants. Every customer receives the product they want. The parts are ready for shipment no later than four days after receipt of the order, regardless of the article and the quantity. This applies to all two-dimensional, customized parts, including special shapes.”
These are promises that, in view of a production order increase rate of around 400 percent – with order quantities of one to ten – are associated with considerable challenges. Against this background, the company first analyzed its process with the aim of maintaining its high delivery quality. In doing so, a new storage strategy emerged as the most efficient solution: away from forklift-operated shelves – towards the STOPA COMPACT automatic storage system.
Flexible movement profiles
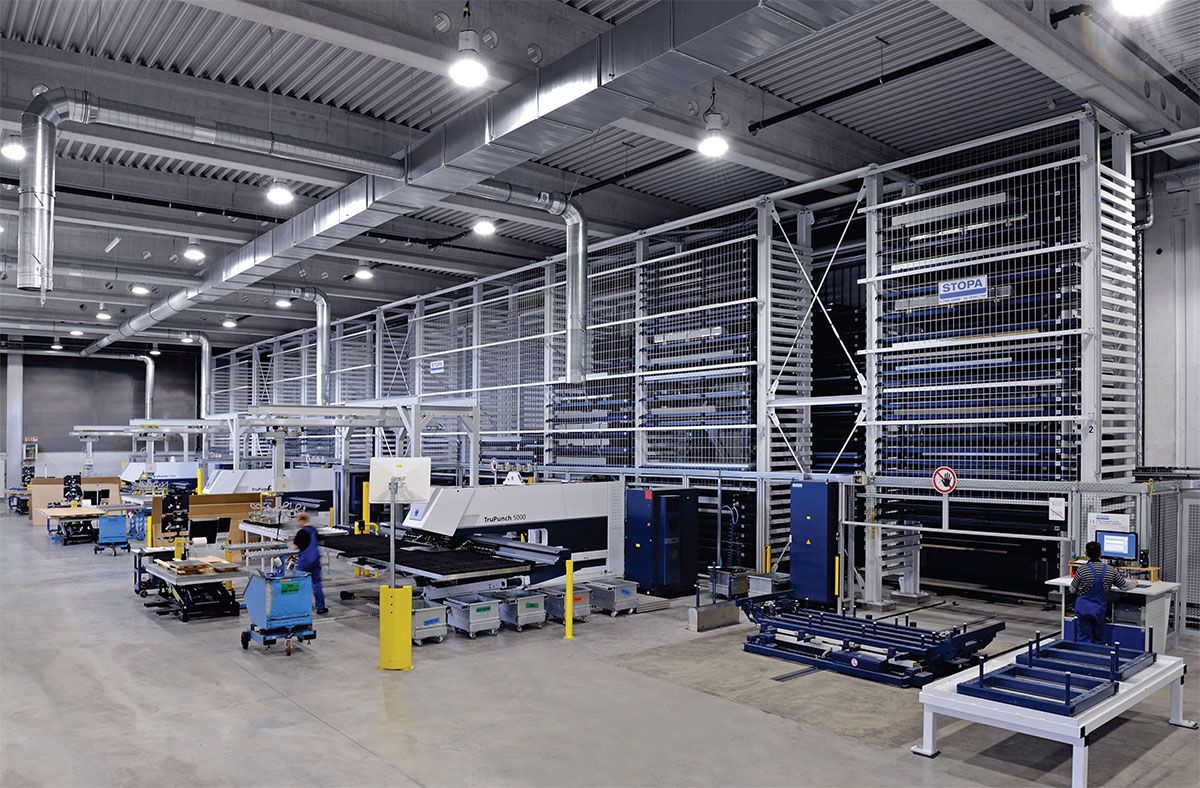
The expanded metal and perforated plate manufacturer MEVACO uses its STOPA COMPACT automatic storage system as the basis for high delivery quality
Jochen Schott calculates that the investment in the sheet metal storage system from STOPA Anlagenbau GmbH, Achern-Gamshurst, also makes economic sense. “Since the system was put into operation at the beginning of September 2012, we have been working much more productively and thus more economically. Many non-productive times have been eliminated, for example the search effort and about 23,000 forklift trips per year. Before, we had to transport sheets to the machines about 14,000 times a year and then transport the remaining sheets back again. Based on the process optimization achieved, we expect the warehouse to pay for itself in six years. This calculation takes into account the reduced manual labor as well as the elimination of machine downtime, which results from the fact that the systems are now directly connected to the warehouse.”
Just as MEVACO responds flexibly to customer requests, the movements of the STOPA COMPACT can be adapted to the material to be stored and retrieved. Jochen Schott leafs through the warehouse documentation. “We can store movement profiles for all sheets in the master data of the warehouse management software. This enables us to achieve greater process reliability with slippery material on the one hand, and short cycle times when supplying the processing machines by utilizing the special dynamics of the warehouse on the other.” The two-mast storage and retrieval machine (SRM) handles its travel orders either with high or low acceleration or speed values, depending on the respective specification. The maximum longitudinal travel speed of 150 meters per minute is required, for example, for empty trips. The operator relies on gentler handling, especially for galvanized and slippery material.
Highlights of the solution
- Increased productivity
- greater cost-effectiveness
- high space utilization
- process optimization
interface easily adapted
The STOPA COMPACT, which offers optimal space utilization, consists of 20 double-row shelf blocks at MEVACO. The system, which is over 7.5 meters high, almost 49 meters long and 5.5 meters wide, contains small, medium and large format sheets in 654 storage locations. Flat pallets, which can be loaded with material weighing up to 3,000 kilograms, serve as load carriers. A real-time soft PLC integrated into an industrial PC controls the system components of the warehouse, which operates in three shifts at the expanded metal and perforated sheet manufacturer and with an availability of almost 100 percent.
Forklift trucks lift the sheet metal packages from the delivery trucks and place them on an unpacking table and later on the scissor lift table of the incoming and outgoing goods station, which is equipped with storage stamps. “We book the incoming goods via the warehouse management system developed by STOPA in our own ERP system.” Jochen Schott simulates a booking process. “STOPA has adapted its warehouse management system so that the relevant employees only have to familiarize themselves with one user interface. STOPA has also easily adapted the interface to our system.”
The production planning system of the operator initiates stock removals to the connected systems – three TRUMPF TruPunch 5000 punching machines and one stretching machine. This is part of the ERP system and communicates with the warehouse management system. Since the warehouse is equipped with tandem stations, the RBG can store a flat pallet of material while the associated machines are still processing sheets from another pallet. The planned investment in another machine has already been taken into account in the current warehouse configuration.
Parts production from sheet metal plates and coils
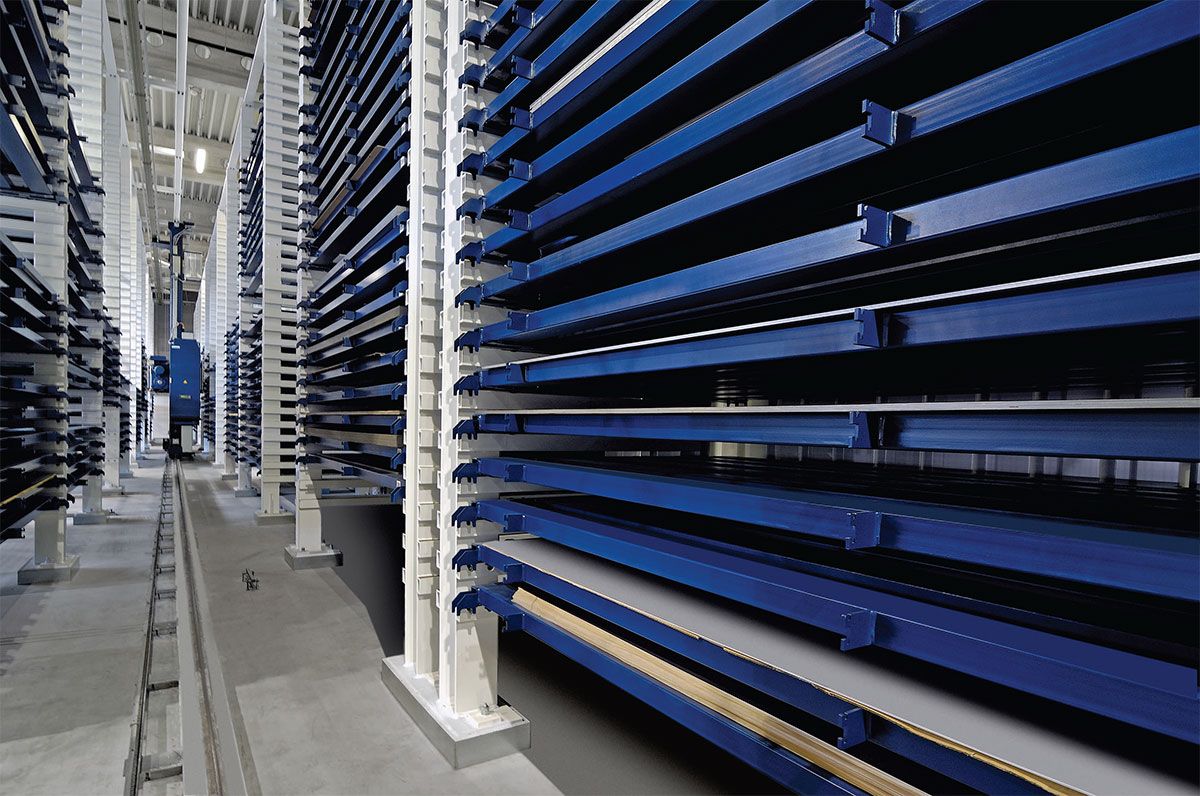
The movements of the STOPA COMPACT sheet metal warehouse can be flexibly adapted to the material to be stored and retrieved
MEVACO does not automatically transfer the metal sheets to the machines. Jochen Schott stops his tour at a station where a metal sheet is hanging on a vacuum crossbeam. “We lift the sheets with the help of a crossbeam and spray them with punching oil from below. This way, we prevent greater wear of the punching tools.” The company does not store any finished or semi-finished parts, only residual pallets with raw sheets. The material is weighed on the RBG and the stock is updated accordingly in the warehouse management system.
MEVACO produces expanded metals on an expansion machine. If a customer requires a smaller quantity, the desired expanded pattern is produced from sheet metal plates that the STOPA COMPACT removes from a scissor lift table. The platform of the latter can be rotated by 180 degrees so that the flat pallet can be aligned so that the operator has a short distance to the stretching machine when manually transferring the sheets. The employee shows an alternative to individual sheets by unwinding a coil from a mandrel to the stretching machine. Jochen Schott explains: “Although the material in this case does not come from the sheet metal store, the system is still integrated into the process. The warehouse control system allows a pallet to be moved out for this process, on which a roller conveyor is installed.” In this way, the strip that is unwound from the coil is pulled over the roller conveyor so that it does not sag. This is an advantage that makes it much easier to thread the strip into the machine because no tensile forces occur.
MEVACO processes around 90,000 metal sheets per year via the warehouse. For each production order, the technical management calculates which production process – sheet or coil – is more cost-effective based on the manufacturing cost calculation. The company combines orders that are planned for coil production if this is possible within the very narrow time frame that results from the promised short delivery times.
Harmonious customer-supplier relationship
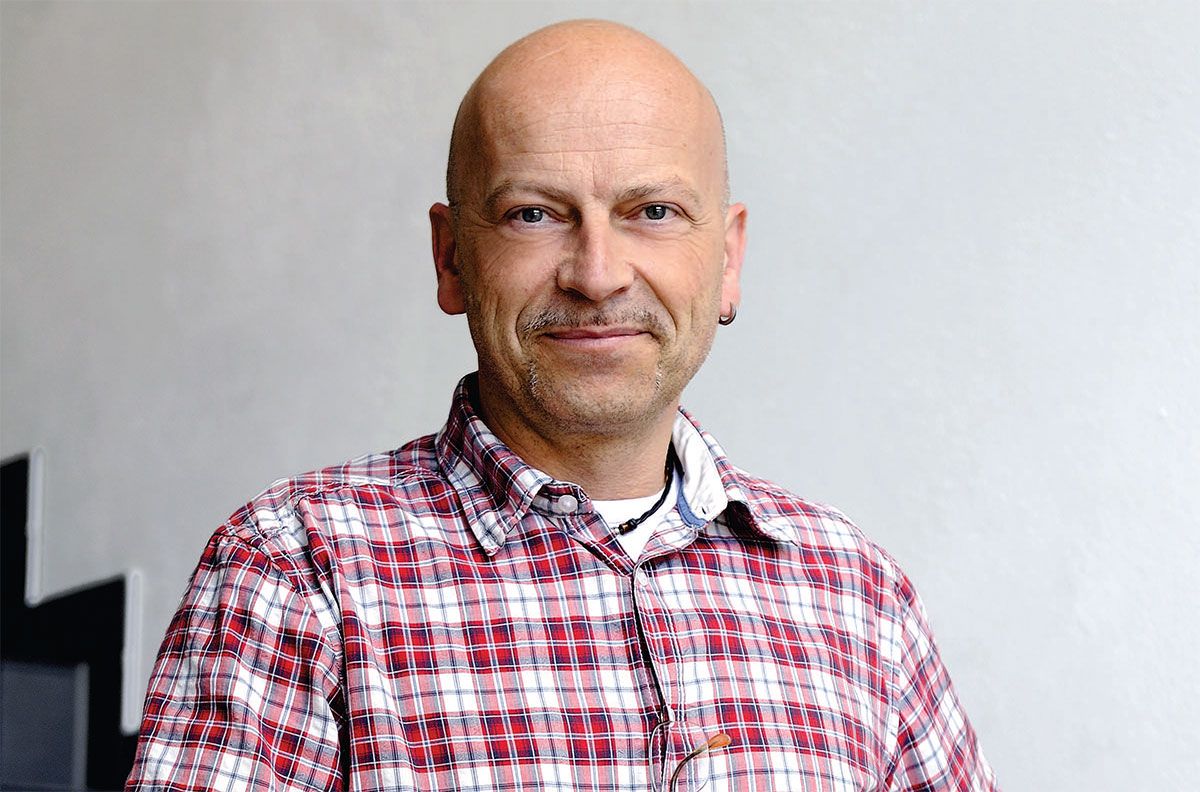
Jochen Schott, Technical Director of MEVACO GmbH
Before deciding on the automated warehouse, MEVACO also asked an Italian and another German manufacturer. Jochen Schott puts a layout of the warehouse on the table. “We decided on STOPA because all agreements were kept.” He taps his finger on the drawing. “For example, the layouts were presented on time. In addition, the sales and marketing manager Ralf Gerber, our contact at STOPA, comes across as authentic. This is important, because a customer-supplier relationship has to be right from the start, especially since we are committing ourselves for the long term with this investment. It is not just the price that is decisive, but also a high level of flexibility in the cooperation. At STOPA, this is the case, as we already noticed in the planning phase when we had change requests regarding the machine connection.”
Author: Jürgen Warmbol
Sales Contact Person
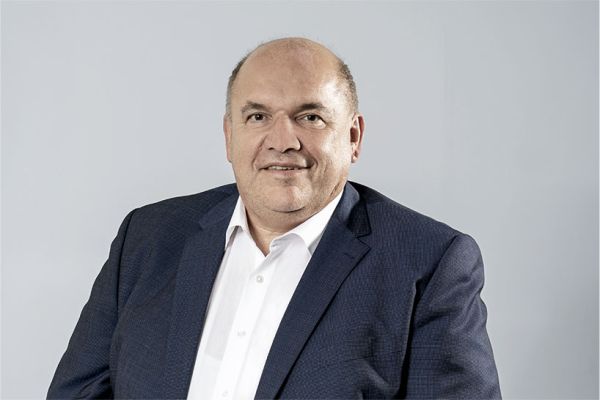
Holger Dehmelt
Sales Engineer Warehouse Technology
STOPA Anlagenbau GmbH
Industriestr. 12
77855 Achern-Gamshurst
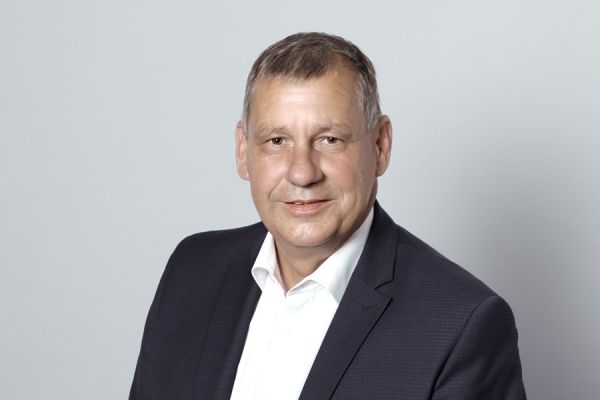
Rolf Eckhardt
Sales Engineer Warehouse Technology
STOPA Anlagenbau GmbH
Industriestr. 12
77855 Achern-Gamshurst
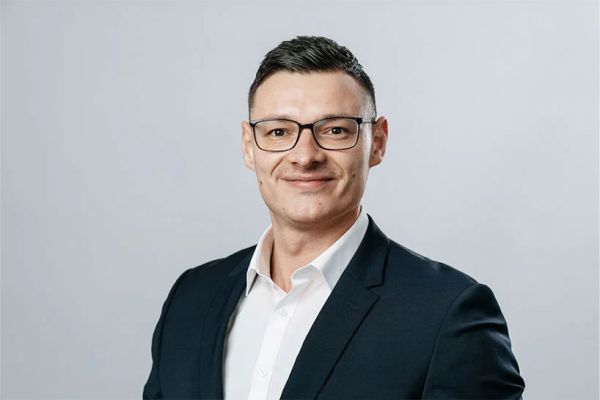
Andreas Pahl
Sales Engineer Warehouse Technology
STOPA Anlagenbau GmbH
Industriestr. 12
77855 Achern-Gamshurst