More productive thanks to reduced handling
By investing in an automatic STOPA COMPACT sheet metal storage system, WaCo Gerätetechnik GmbH, a manufacturer of customized sheet metal parts, assemblies and devices, has reduced its handling costs and thus increased its productivity. This is demonstrated by the utilization of the processing machines, which has increased by up to 30 percent due to automation.
If you accompany graduate engineer Volker Wahl, co-founder and managing partner of WaCo Gerätetechnik GmbH, Dresden, and graduate engineer Dieter Bohnig, production engineer at the company, to their new STOPA COMPACT storage system, you will gain an insight into the future of their sheet metal production. “The storage system is a next step towards efficient automated production,” emphasizes Volker Wahl. “We started in this direction in 2000, when our first processing center was installed.”
WaCo made the decision to purchase the STOPA COMPACT system at the same time as it was building a new production hall. The aim was to create the conditions for the capacity expansion that is planned in the medium term. The system immediately solved the company’s space problem. This was because the pallet racks in the old production facility were not large enough to hold all the raw materials, which meant that many sheet metal packages were standing in the aisle. Furthermore, transporting the sheets to the machines and loading and unloading the systems was too time-consuming.
Significantly higher machine utilization
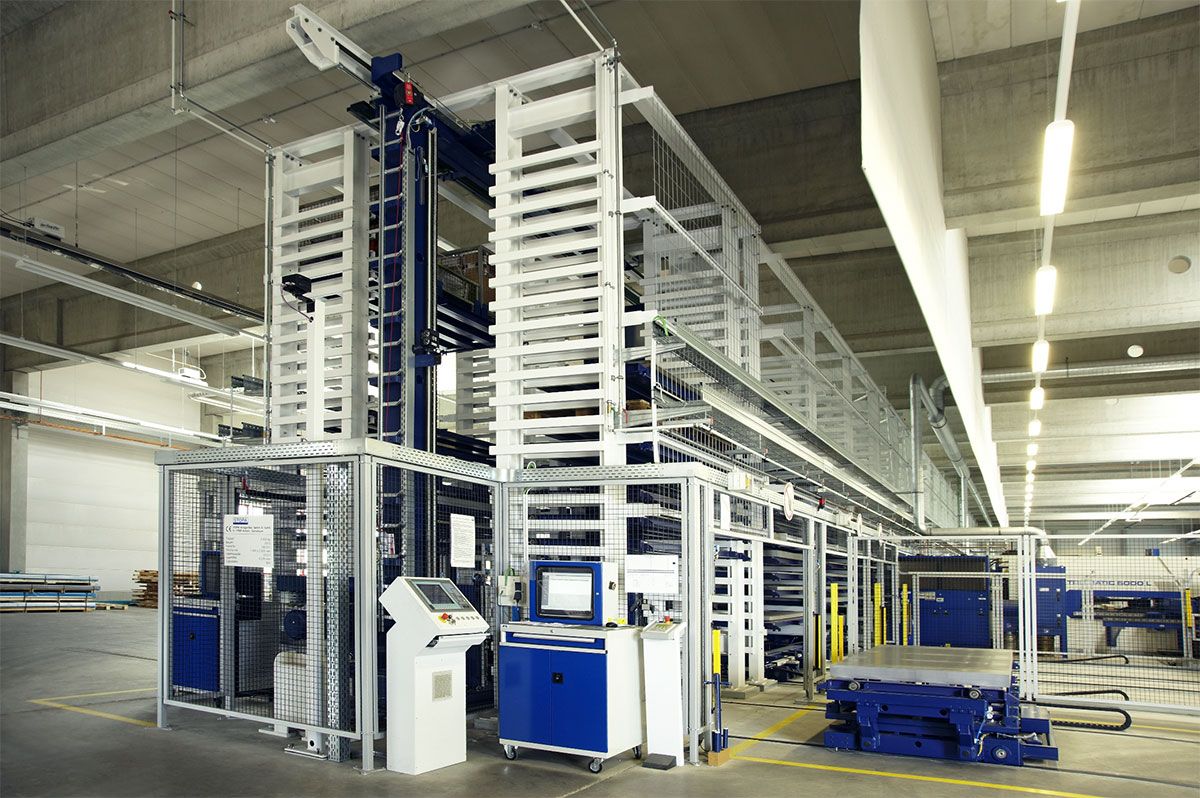
The STOPA COMPACT storage system has made transporting the sheets to the machines and loading and unloading the systems easier
Dieter Bohnig points to the machines that are automatically connected to the storage system and are currently in operation without exception. “The most important result of the conversion is our significantly increased productivity. Due to the reduced handling effort, the downtimes of our machines have been reduced by up to 30 percent, as waiting times that used to occur due to time-consuming manual ancillary activities are no longer necessary. Another advantage is the very short access times of the sheet metal storage system.”
The operator also benefits from comprehensive, up-to-date stock overviews, especially since the system control weighs every pallet that it feeds into the system. This also applies to returns. On top of that, the automatic system increases the motivation of the employees who work in production and production planning.
WaCo chose STOPA Anlagenbau GmbH, Achern-Gamshurst, as the supplier of the sheet metal storage system. A company that has the most experience in working with TRUMPF, the manufacturer of the associated processing machines. Volker Wahl stops at a station where a transport trolley is driving out a system pallet loaded with sheets. “In view of the complex connection between the machine and the storage control, it is essential that STOPA masters the interface.”
800 tons of handling capacity
WaCo stocks 140 types of sheet metal, which differ in terms of quality, thickness and material. These include steel sheets, hot-dip galvanized and electrolytically galvanized sheets, as well as aluminum, chrome-nickel, copper and brass sheets. The material thicknesses range from 0.3 to 8 millimeters, with the most common thicknesses being one to two millimeters.
The internal process begins at an unpacking table, where WaCo unloads the sheet metal packages from the pallets. The table has movable support stamps that can be adjusted to the wooden pallets used for transportation by truck. A forklift transports the packages to the incoming and outgoing goods station. Its lifting table is also equipped with support stamps and additional plug-in stops for a common coordinate corner, which the operator uses to align the sheets precisely.
“We supply four processing machines from the warehouse, which handles 1,000 tons of sheet metal every year.” Dieter Bohnig takes a punched part from a pallet. “We also supply semi-finished parts from here to our main plant for further mechanical processing.” A punching machine, a laser cutting system with automatic loading and two combined laser cutting and punching systems that are automatically loaded and unloaded are connected directly to the STOPA COMPACT. In addition, there are three outgoing goods stations, which are also used to transport sheets for deburring and straightening.
The scissor lift tables and transport trolleys that supply and remove the machines operate unmanned and in parallel with the main production time. This is an advantage that further increases productivity. The pneumatic centering of the flat pallets on the trolleys and scissor lift tables is equally automatic. And light barriers check whether the system is observing the maximum loading height in each case. In addition, STOPA has equipped the scissor lift tables serving as loading trolleys at the three stations leading to the combination machines and the laser cutting system with a spreading magnet device for safe sheet separation. Furthermore, each loading station recognizes the last sheet, and the unloading trolleys of the combination machines are equipped with rotary encoders so that the punched and laser-cut parts are deposited in the correct position.
Flexibility through four loading heights

The STOPA COMPACT automatic storage system at WaCo is around 67.5 meters long, 4.7 meters wide and 6.2 meters high
At WaCo, the STOPA COMPACT consists of 40 double-row shelf blocks that provide space for 804 storage locations. The system is around 67.5 meters long, 4.7 meters wide and 6.2 meters high. The system’s flat pallets are designed for medium-sized and small metal sheets or for materials weighing up to 3,000 kilograms. The warehouse is very flexible, with different loading heights of 130, 355, 580 and 805 millimeters, as well as 1,030 millimeters.
A shelf operating device in a stable and robust two-mast design handles the load carriers. The shelf operating device, which is equipped with a pull-and-push device and a low-wear and low-maintenance chain hoist, moves between the shelf blocks. A digital distance measuring system guarantees exact longitudinal positioning. A further digital distance measuring system, which works absolutely and independently of the load, ensures precise height positioning and consequently makes it unnecessary to approach a reference point. Data flows without contact and without wear via a light barrier to the shelf operating device. Energy is conducted through an overhead conductor rail, which also ensures low-wear and low-noise operation. To avoid collisions during storage, the storage and retrieval unit automatically checks the loading height of the storage locations above and below the selected location. In addition, STOPA has equipped the storage and retrieval unit, whose functions are reliably monitored by the control system, with a lateral contour control system to detect protruding panels. The storage and retrieval machine can travel at speeds of up to 150 meters per minute, lift up to 23 meters and pull or push up to 20 meters. The weighing unit of the load crossbeam records the weight of the pallet and the material placed on it during storage and retrieval, and can therefore also be used for efficient incoming goods inspection.
Current stock levels in real time
A real-time soft PLC integrated into an industrial PC controls the system components of the storage system. The operator uses the industrial PC to operate and display the system status. The programmable logic controller communicates with the TRUMPF TC-Cell warehouse management computer via an interface supplied by STOPA. The software dynamically assigns the storage locations, manages the stock and sheet metal data, and thus permanently provides inventory data.
The system is operated conveniently using easy-to-understand function keys. The status of the storage and retrieval machine can be read continuously and in plain text on the 12-inch TFT display of the ergonomic control panel. In addition, the software visualizes the storage blocks and the storage and retrieval machine in a graphical representation. Dieter Bohnig asks the employee at a retrieval station to move a mesh box out. “Our team has no problems with the warehouse. The operating steps are logically structured and therefore very easy to learn.” In the event of a fault, STOPA can access the remote maintenance software PC Anywhere and the control modem to analyze and rectify the error from its own location.
Four operating modes are available for the warehouse. In online mode, a higher-level host controls the system. If you opt for automatic operation, the system processes individual orders independently as soon as the operator has entered the respective start and target coordinates. In this case, the storage system continues to function even if a fault occurs on the host. It is also possible to operate the system in a lock-free service mode, in which the employee enters the commands directly on the storage and retrieval unit, and in manual mode with active safety locks.
Investment in the future
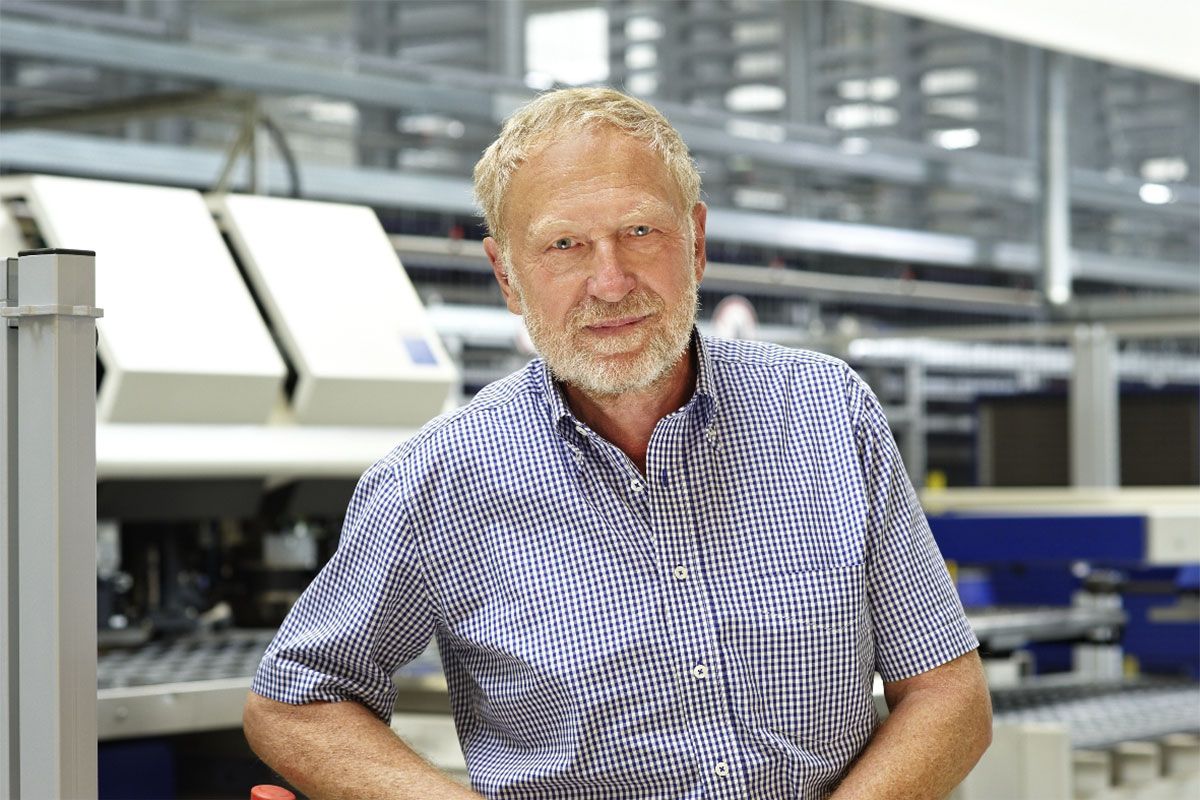
Dipl.-Ing. Dieter Bohnig, production engineer at WaCo Gerätetechnik GmbH, Dresden
WaCo has been using the STOPA COMPACT sheet metal storage system since July 2010, when it was fully commissioned after three months of installation, including the successive relocation of the four previously affiliated machines. The manufacturer then trained the relevant WaCo employees on site over three days.
Volker Wahl looks out of a rear window of the hall at an undeveloped part of his property. “The STOPA COMPACT storage system is an investment in the future. On the one hand, because it has sustainably increased our productivity, and on the other hand, because it can be flexibly extended.” In addition to the required property, the foundation for a longer sheet metal storage system is already in place throughout the hall, which can be expanded into the still vacant area. There is also space for WaCo to add additional and larger machines and stations. The flexibility of the system is also evident in the operating times. The last of the three daily shifts is to be unmanned in the future. WaCo is gaining experience in this area on weekends, when the company already manufactures automatically.
Author: Jürgen Warmbol
Sales Contact Person
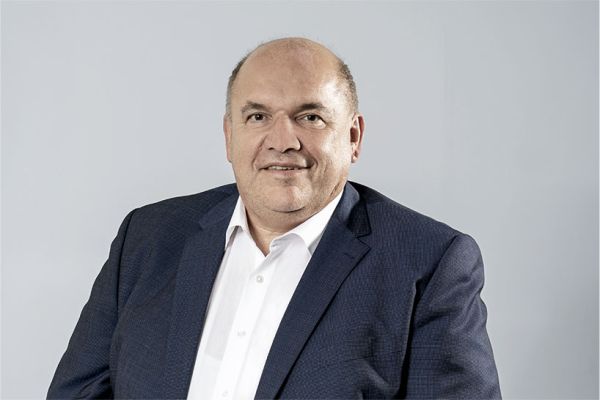
Holger Dehmelt
Sales Engineer Warehouse Technology
STOPA Anlagenbau GmbH
Industriestr. 12
77855 Achern-Gamshurst
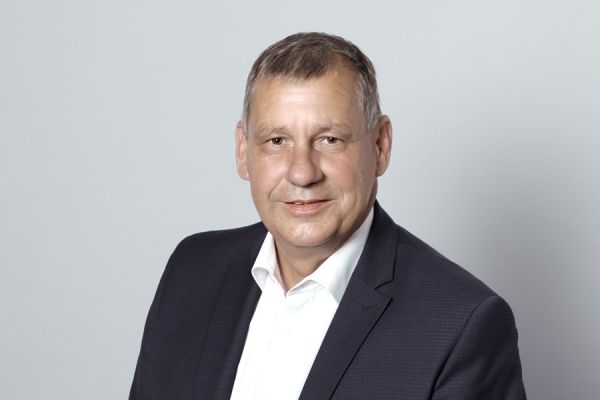
Rolf Eckhardt
Sales Engineer Warehouse Technology
STOPA Anlagenbau GmbH
Industriestr. 12
77855 Achern-Gamshurst
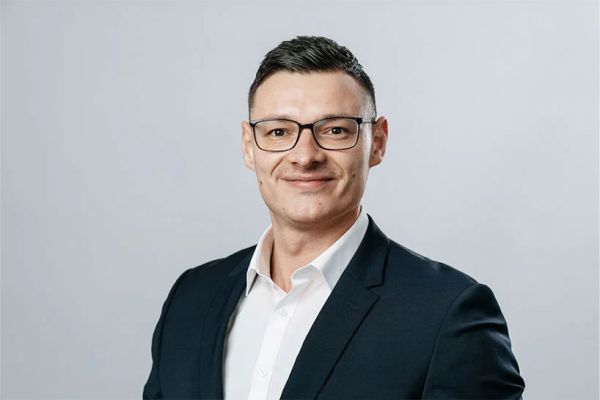
Andreas Pahl
Sales Engineer Warehouse Technology
STOPA Anlagenbau GmbH
Industriestr. 12
77855 Achern-Gamshurst