COMPACT system for sheet metal panels up to 2,500 x 6,500 millimeters
At its Nittenau plant, Krones AG produces large, high-quality sheet metal components without any joints or welds. The STOPA COMPACT automatic storage system ensures that the processing machines are always supplied with the right parts. The highlight: the storage system is designed for special sheet metal formats up to 2,500 x 6,500 millimeters. This solution helps the operator to meet its high quality standards and work more efficiently.
A decision for quality
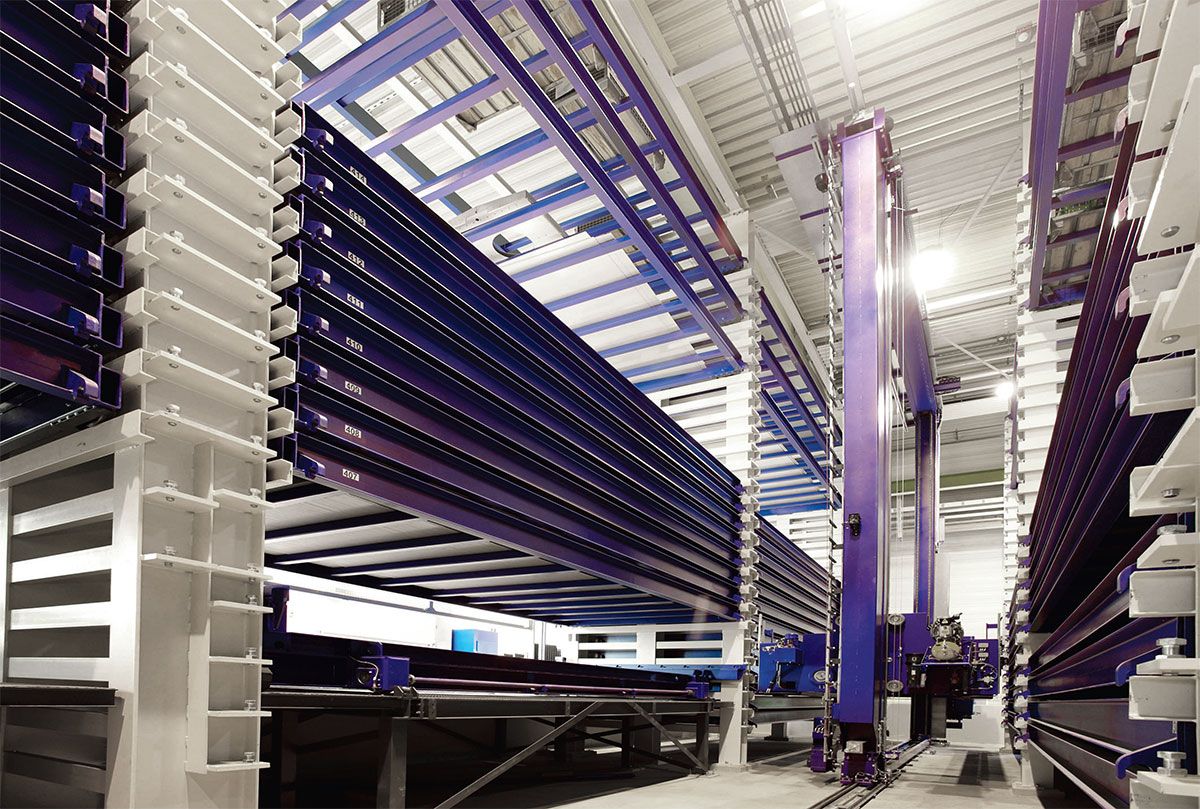
In this case, the STOPA COMPACT automatic storage system is designed for special sheet metal formats up to 2,500 x 6,500 millimeters, which enables KRONES to meet its high quality standards
The STOPA COMPACT storage system has been in operation from Monday to Friday in three shifts since January 2009. And with an availability of almost 100 percent. The storage system often supplies the machines on Saturdays as well. “Before we moved our production area to the new hall, the sheets were lying on the floor or even outside because there was a lack of space inside,” explains Heiko Bucher, head of the production team at the Krones plant in Nittenau. “Due to the large amount of space gained by the conversion, this is no longer necessary today.”
The highlight of the STOPA COMPACT storage system at the Nittenau plant is the usable area of the cassettes used as load carriers, which STOPA has designed for sheet metal panels in special formats of up to 2,500 x 6,500 millimeters.
Bucher points to a voluminous module that has been given its shape exclusively by laser cutting and bending. “The decision to use large sheets is a decision for more quality. We want to avoid welding and cutting joints for aesthetic reasons, but above all we want to avoid the heat that would be generated during welding distorting the products.”
In view of growing production volumes and high quality standards, investing in a sheet metal storage system was unavoidable. Against this background and because Krones uses few standard formats, there was no technical alternative to a modular storage system such as the STOPA COMPACT. As an added benefit, the operator has increased its delivery quality, as the long procurement times that are usual for special formats are no longer necessary.
Krones explains that it awarded the contract to STOPA based on the good experiences it has had with six other systems from this manufacturer: The service expertise of STOPA and the resulting high availability of the systems are to be emphasized. Just as important is the willingness to listen to special requests. Speed is not the most important thing; what is expected is a customized design of the respective warehouse. In this case, the aim is to be able to store higher parts, such as wire mesh boxes.
Warehouse supplies laser cutting machines
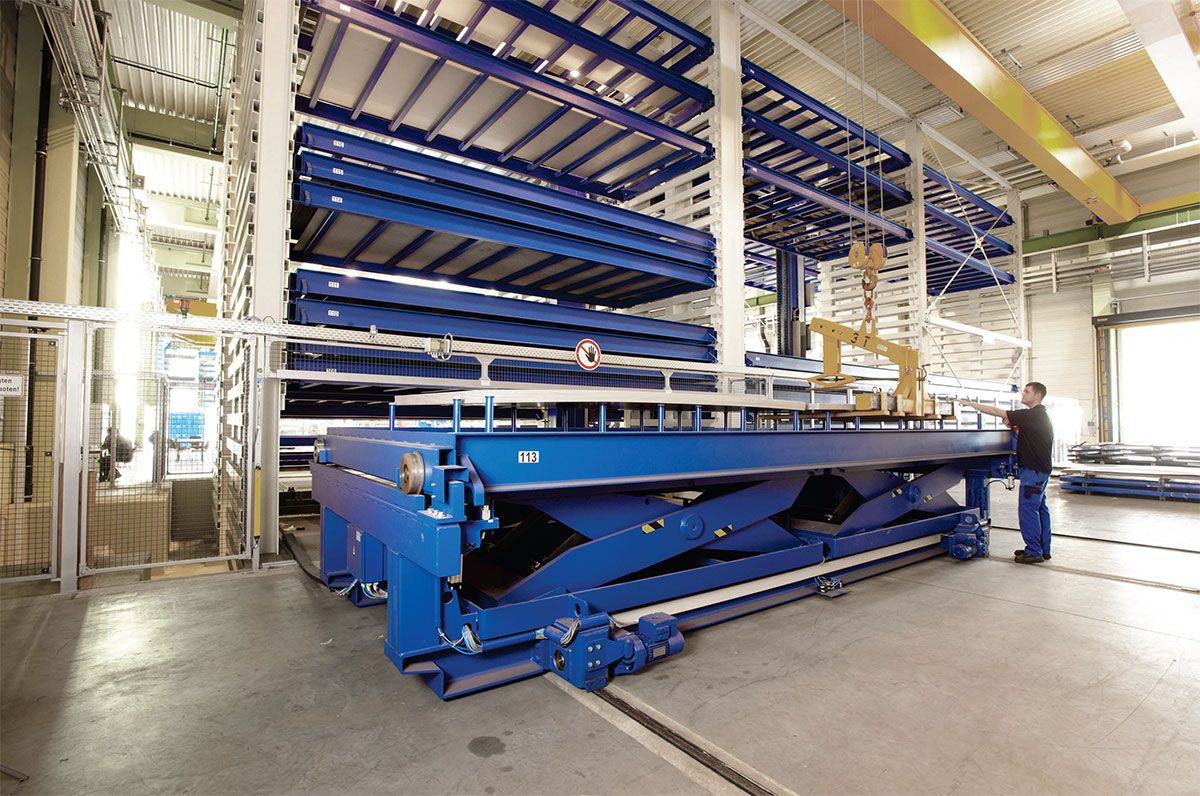
STOPA has installed the warehouse in a pit, thus lowering the floor level of the system below that of the hall and increasing the storage volume by utilizing the available hall space and height
Of the three stations of the STOPA COMPACT storage system, station 1 is used for incoming and outgoing goods for material destined for customers outside the hall. The scissor lift table of station 1, which has a maximum loading height of 510 millimeters, is equipped with storage stamps for incoming and outgoing goods. The stamps are raised above the cassette level before a forklift or crane places raw sheets on the load carrier or picks them up from there. The cassettes lock automatically on the scissor lift table. Stations 2 and 3, which store material in the hall, are each equipped with a transport carriage instead of a scissor lift table. In other respects, they correspond to station 1.
In front of station 3, an employee is using a crane and a magnet to lift a tube out of a discharged cassette. He is supplying a TRUMPF LASERCELL 6005 with it. Bucher points through the protective window into the machine. “We use the flexible 3D laser center to cut and weld very large or long components. We have a TRUMPF laser flatbed machine at the opposite end of the hall for cutting standard formats. The flatbed laser also receives the sheet metal panels from the STOPA COMPACT storage system. In addition, we have set up a small intermediate storage area close to the processing area.”
In addition to the metal sheets, which range in size from 1,250 x 3,000 millimeters, the warehouse also contains components for tabletops and semi-finished products, which therefore do not take up any space on the floor. It also contains pipes, as well as round, flat and other profile steel.
Safe storage at different loading heights
The STOPA COMPACT storage system in Nittenau is 27.7 meters long, 10.2 meters wide and 10.9 meters high. It consists of six shelf blocks, each arranged in two rows of equal length. STOPA installed the storage system in a pit, thus lowering the floor level of the system below that of the hall and increasing the storage volume by utilizing the available hall space and height. The load carriers are 75 cassettes, to which STOPA has assigned fixed storage locations. They can each be loaded with material weighing up to 7,000 kilograms and divided into 14 storage locations. The operator can place cassettes with loading heights of 120 and 510 millimeters on the 144 locations of the expandable system. A third loading height is already planned. The smaller number of cassettes used compared to the number of storage locations is due to the two loading heights of the system and the fact that the locations above load carriers that are loaded higher than 120 millimeters must remain free.
The stable and robust double-mast stacker crane in the warehouse reaches speeds of 60 meters per minute when moving lengthways, 23 meters when lifting and 20 meters when pulling. It positions itself when moving via a digital distance measuring system, and when lifting and lowering via an additional digital distance measuring system that works absolutely and independently of the load, making it unnecessary to approach a reference point. A contour control system ensures safety by recognizing sheets that protrude from the side of the sheet packs. A weighing device built into the load crossbeam records the weight of each incoming or outgoing storage, then calculates the quantities and updates the inventory in this way. If the specified maximum weight is exceeded, the system does not store the cassette in question.
Interface between PLC and ERP system
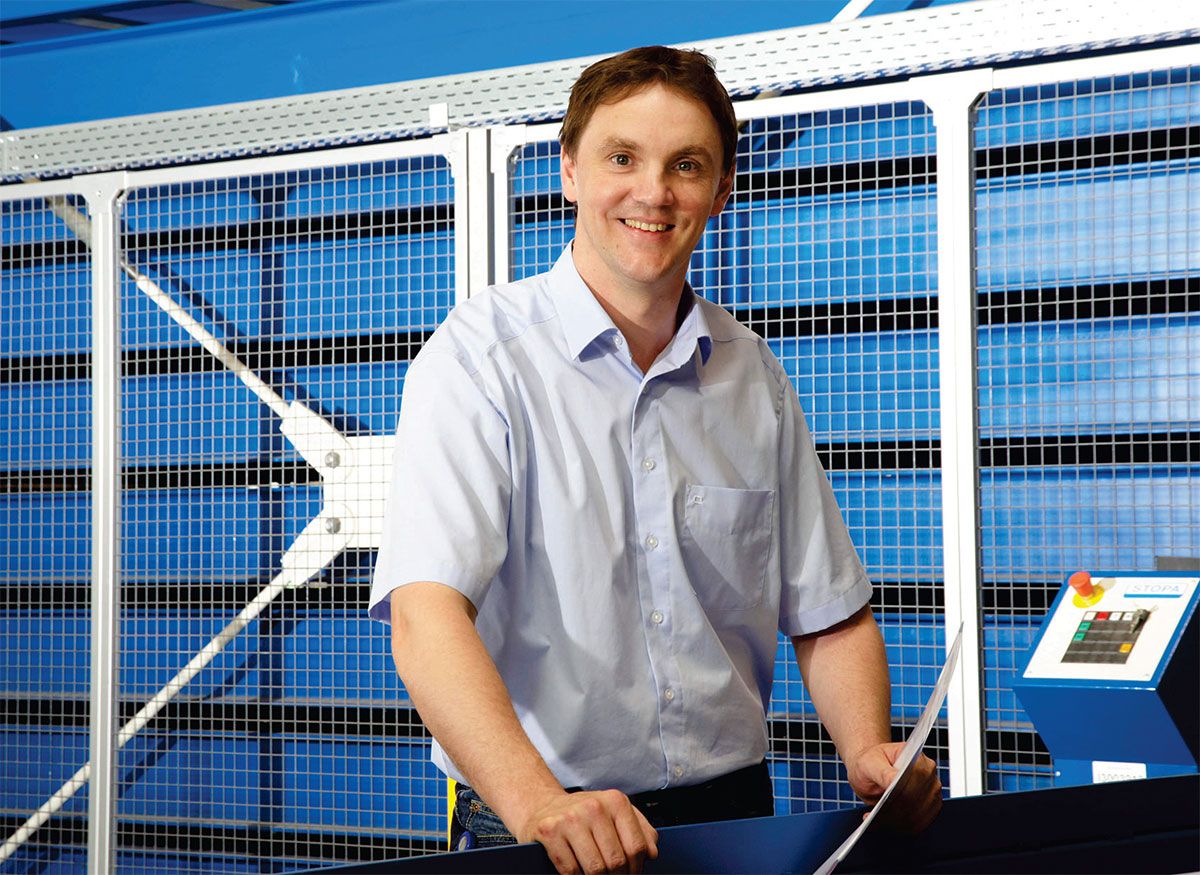
Heiko Bucher, Head of the Production Team at the KRONES plant in Nittenau
A real-time soft PLC controls the system components of the STOPA COMPACT storage system. The programmable logic controller is integrated into an industrial PC. Krones uses the PC to operate and display the system statuses. The system controller communicates with a warehouse management computer. Its software manages the stocks and the sheet metal data and, thanks to a permanent inventory, provides an up-to-date overview of the stock at all times. Bucher emphasizes another point: “To ensure that this data is also available to our SAP ERP system, an interface has been set up between the real-time soft PLC and the ERP system for synchronization.” The status of the storage and retrieval machine can be read continuously and in plain text on the 12-inch TFT display of the ergonomic control panel. At the touch of a button, the storage blocks and the storage and retrieval machine appear on the display in graphic form.
A question of cost-effectiveness
The STOPA COMPACT is a very economical solution because the sheet metal storage system achieves a significantly longer service life than the associated machines. The system also promises cost-effectiveness in view of possible productivity increases. These are based on faster material provision to the processing machines and, consequently, on their continuous utilization. Capacity can also be increased by an unmanned third shift. In addition, the space requirement is significantly lower for the same amount of material, since the storage system utilizes the entire height of the hall. Furthermore, with an identical number of personnel, a STOPA COMPACT storage system can be used to operate more machines and the storage system at the same time. Better part quality also contributes to the cost-effectiveness of the storage system. Another argument in favor of the system’s economy is the approximately 50 percent reduction in throughput times.
Author: Jürgen Warmbol
Sales Contact Person
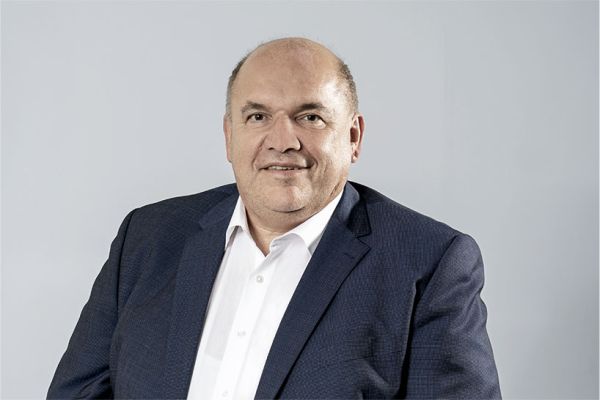
Holger Dehmelt
Sales Engineer Warehouse Technology
STOPA Anlagenbau GmbH
Industriestr. 12
77855 Achern-Gamshurst
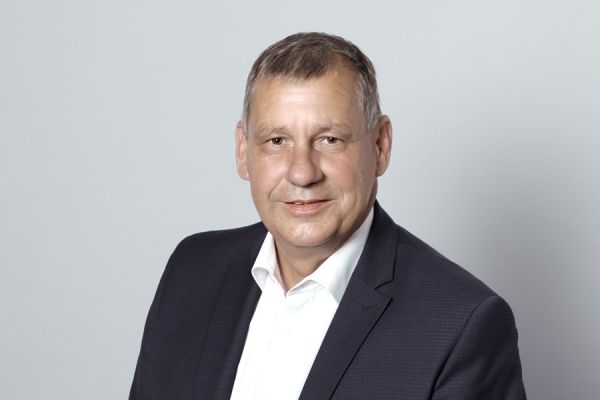
Rolf Eckhardt
Sales Engineer Warehouse Technology
STOPA Anlagenbau GmbH
Industriestr. 12
77855 Achern-Gamshurst
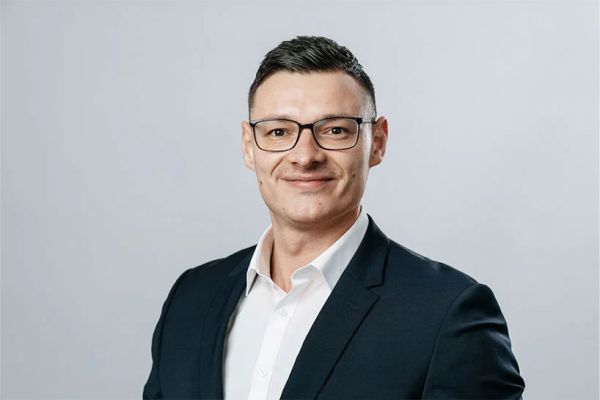
Andreas Pahl
Sales Engineer Warehouse Technology
STOPA Anlagenbau GmbH
Industriestr. 12
77855 Achern-Gamshurst