The Added-Value Storage System
An automated long-bar storage system can also offer rationalization potential in addition to profiled steel. STOPA proves this at DOLL Fahrzeugbau AG. The operator achieves a high added value through decoupled processes, minimized downtimes and the resulting productivity increases.
The processes surrounding the long-bar storage system operated by DOLL are characterized by convenience and cost-effectiveness. For example, when the system automatically provides the requested material so that the employee at the goods issue station only has to lift it out of the cassette with the help of a crane and place it on the feed table of the associated circular or band saw. Dipl.-Ing., Dipl.-Wirt.-Ing. Holger Reichert head of materials management and IT at DOLL Fahrzeugbau AG, Oppenau, is observing the process. “The automatic storage of long goods directly at the point of use eliminates transport and travel times.”
More efficiency through separate processes
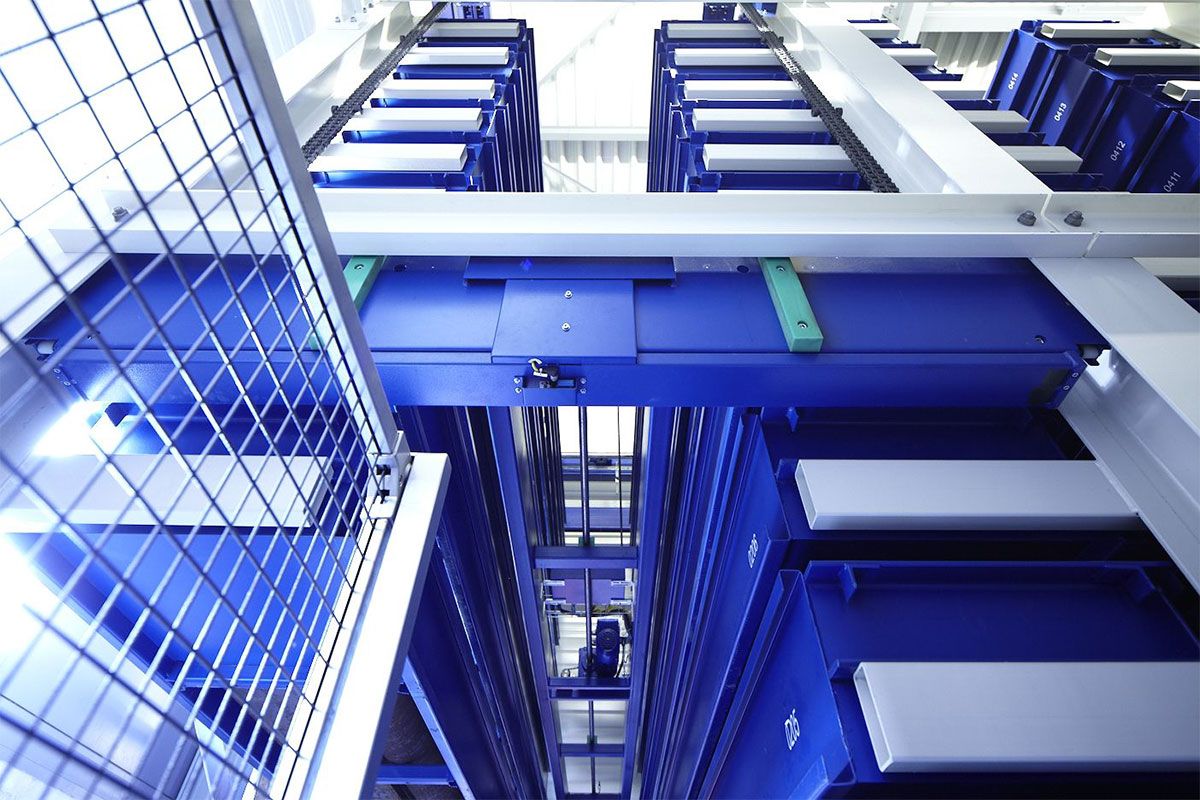
DOLL has tapped into rationalization potential through the automatic long goods storage system from STOPA
The LG B3 long-bar storage system, supplied by STOPA Anlagenbau GmbH, Achern-Gamshurst, in which round and flat steel bars, UNP profiles, rectangular and seamless tubes and other profile steel bars are stored, offers a high degree of space utilization as well as fast and random access to the material. In addition, the system relieves the warehouse and production staff. Holger Reichert’s gaze wanders from the operator who supplies the circular saw with long goods to the transport cart of the goods outgoing station, which returns to the warehouse. “The warehouse separates the processes and enables an efficient flow of materials. Since we store and retrieve independently of the processing, we can complete all tasks without waiting times. We also don’t need any intermediate buffers, we can access the steel sections in the shortest possible time and we save ourselves the effort of searching for and preparing materials. All in all, we have significantly increased our productivity.”
Other key decision-making criteria for DOLL included the promised and realized connection of the warehouse to its own ERP system, high availability, service life and occupational safety, as well as permanent inventory monitoring. On top of that, DOLL can dispense with sandblasting, which would be indispensable for outdoor storage. This is an advantage that further increases productivity.
The long-bar storage system, which went into operation in June 2009, stores and retrieves an average of six cassettes per hour. It replaced a stacking cradle system that required the help of a gantry crane and was only economical for material lengths of 14 to 16 meters. The alternatives to a long goods store would have been a combination of cantilever racking and side stackers or paternosters. A solution with cantilever racking would have led to a high demand for traffic area as well as a relatively low height limit and less occupational safety. And paternosters have the disadvantage that all cassettes have to be moved every time they are accessed. Furthermore, the material can only be stored and retrieved lengthways.
Holger Reichert: “We chose STOPA because the company is a full-service provider and was able to supply us with both a long-bar and a sheet metal storage system. STOPA’s geographical proximity, expertise and good references also spoke in its favor. And the fact that they respond promptly and expertly to questions, problems and change requests.”
Highlights of the solution
- Increased productivity
- Optimal use of space
- High availability
- Permanent inventory monitoring
High system availability
The long-bar storage system, which currently operates in two shifts and achieves an availability of 98 percent, is 6,895 millimeters high, 20,800 millimeters long and 7,300 millimeters wide. Its eight rack aisles provide 214 storage locations. 182 of these are designed for type 1 cassettes, which have a usable size (w x h x l) of 600 x 245 x 6,476 millimeters. STOPA has reserved 32 additional locations for type 2 cassettes, which have a larger volume with a loading height of 400 millimeters. The maximum permissible payload of 3,000 kilograms per load carrier, the possible division into four compartments and the minimum length of the bars to be stored of 2,000 millimeters are identical for both variants. 168 type 1 and 32 type 2 cassettes are currently in the system.
At the control panel of the goods-in area, which is equipped with a dead man’s switch for safety reasons, the control system shows the employee all the empty cassettes and those suitable for storage, loaded with the same material, before each storage. Once the employee has selected a cassette, the transport carriage of the goods-in station, which can be moved at the front, makes it available. The carriage is equipped with a frequency-controlled drive for smooth starts and stops. A light barrier checks whether the specified loading height is being maintained. After the operator has filled the carrier with the help of a crane and a magnet and released it, the carriage returns to the warehouse at a speed of up to 16 meters per minute.
Exact positioning
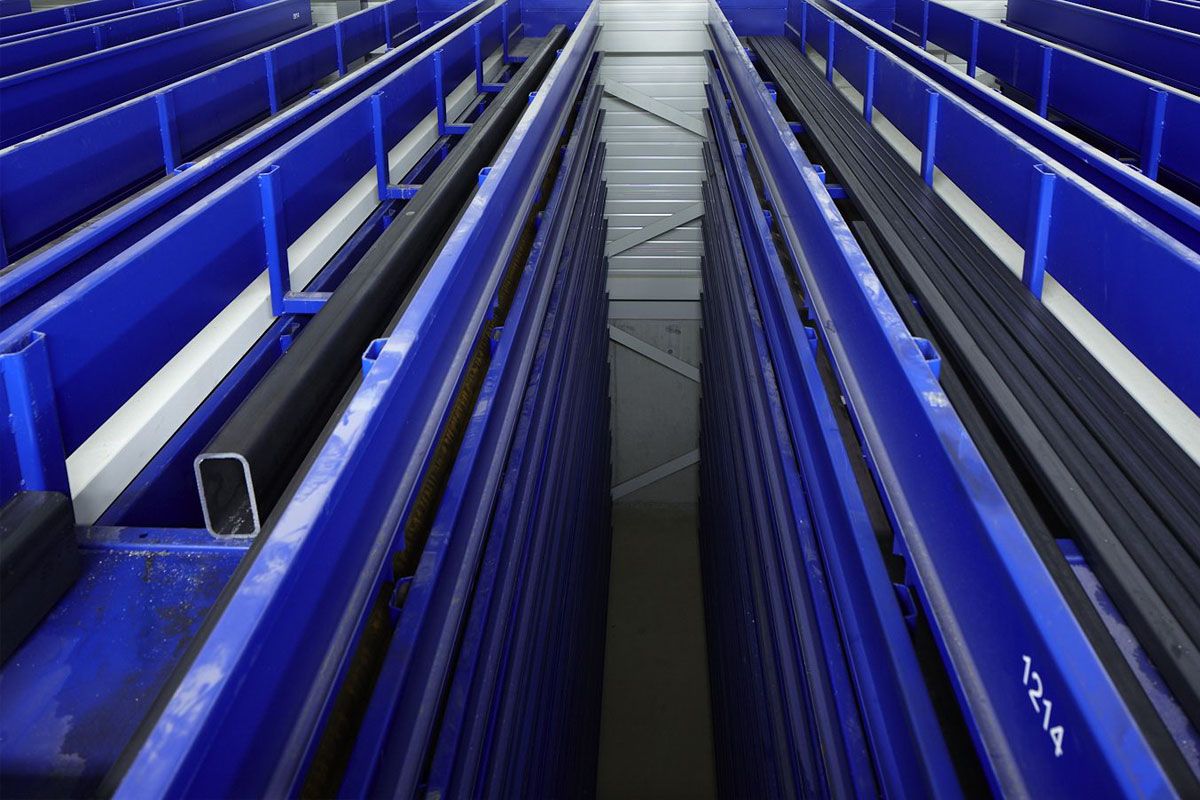
The long-goods storage system supplied by STOPA offers a high degree of space utilization as well as fast and random access
The stable and robust storage and retrieval machine uses a double-sided cassette holder for storage and retrieval, which STOPA has equipped with a frequency-controlled drive as well as a compartment occupancy and cassette seating control. A digital distance measuring system guarantees exact longitudinal positioning. A further digital distance measuring system, which works absolutely and independently of the load, ensures precise height positioning and thus makes it unnecessary to approach a reference point. Data flows contactlessly and without wear via a light barrier to the shelf operating device, which reaches speeds of up to 80 meters per minute when driving and 30 meters per minute when lifting and moving the forks.
The transport carriage of the goods issue station, which is also movable at the front, stores replenishment for the saws. Holger Reichert looks over the shoulder of the operator who is just triggering a removal order. “To retrieve a load carrier, our employee either enters the number of the desired cassette or lets the control system select the profile steel based on search criteria, which then displays all load carriers with the relevant long goods.” Material can also be transported directly from the storage to the retrieval station without having to return the cassette to its compartment first. It is also possible to order several retrievals as a list and have them processed step by step. DOLL stores the raw material again after the required quantity or length has been removed.
Communication-friendly warehouse management computer
An industrial PC with an integrated processor controls the long goods warehouse. While the PC is available for operation and displaying the system status, the processor controls the system components. An uninterruptible power supply (UPS) ensures a high level of operational reliability for the system.
The 12-inch TFT display on the ergonomic control panel allows employees to continuously monitor the status of the storage and retrieval machine in plain text and to visualize the storage rack and the storage and retrieval machine from above. The control system displays the numbers and material overviews of the cassettes that have been removed from storage. It also graphically displays the respective storage aisle. It displays free, occupied and blocked compartments. It also displays empty and full load carriers depending on their loading height. To ensure a continuous supply for the machines and their utilization, DOLL stores a minimum quantity for each profile steel, which the system automatically checks via target-actual comparisons. Holger Reichert watches the employee as he enters his commands with practiced ease. “After a training session with STOPA and a few days of practice, the operators soon got the hang of the warehouse. Especially since the menu options and functions are structured according to the storage and retrieval processes and the system can be operated intuitively.”
The system control communicates with the warehouse management computer, which manages the stocks and material data and allows a quick overview of the stock through its permanent inventory. However, the warehouse management software is not only responsible for the long goods warehouse, but also for the sheet metal warehouse that STOPA has installed in the same hall. The company’s services also include the interface between the warehouse management computer and the operator’s ERP system. Should a fault occur, STOPA uses the remote maintenance software PC Anywhere and the control system’s modem to analyze and rectify the error from its own location.
Convincing cost-effectiveness
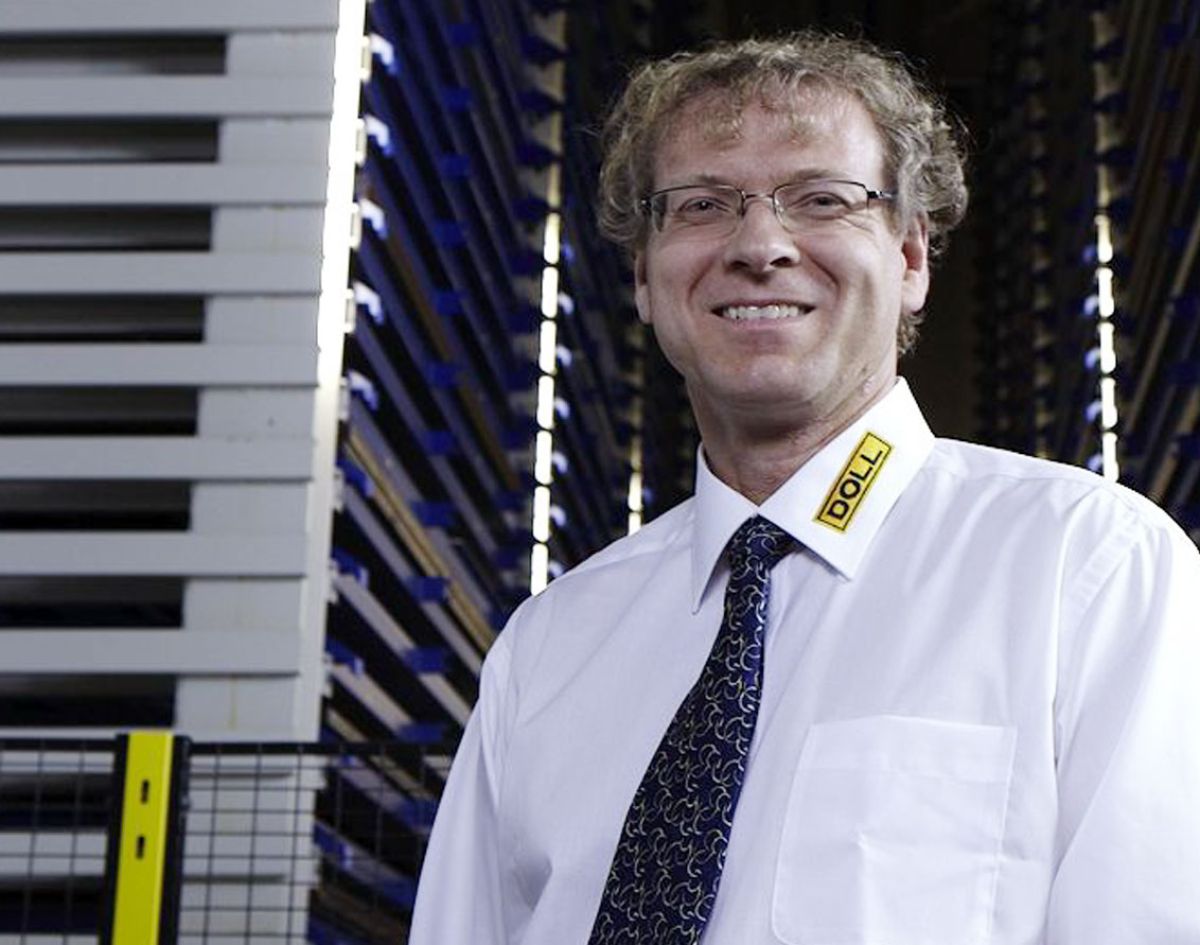
Dipl.-Ing., Dipl.-Wirt.-Ing. Holger Reichert, Head of Materials Management and IT at DOLL
The STOPA long-bar storage system is a very economical solution because it achieves a significantly longer service life than the associated machines. When entering the fully enclosed storage system, another important point becomes apparent: since the steel profiles are stored in a space-saving manner in a small area, DOLL requires considerably less space for the same amount of material. Capacity could also be increased by introducing an unmanned third shift. Furthermore, with an identical number of personnel, a long-bar storage system can be used to operate more machines and the storage system itself. And all this with a higher level of occupational safety.
Furthermore, the DOLL system enables the entire order processing to be planned more easily and precisely. Better parts quality also contributes to the cost-effectiveness of the warehouse. This results from more careful material handling, which is based on the elimination of forklifts in production, as well as the elimination of contamination. An additional economic advantage is provided by throughput times that are reduced by around 50 percent.
Author: Jürgen Warmbol
Sales Contact Person
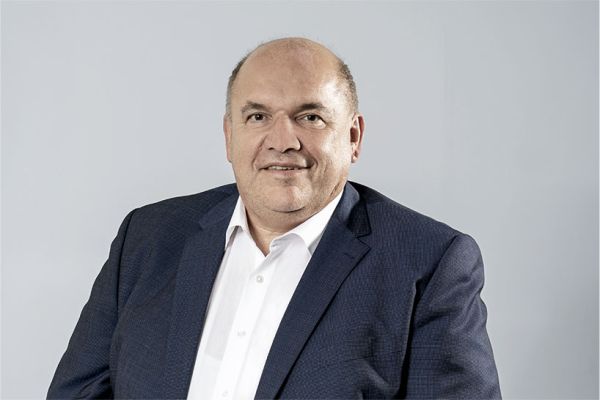
Holger Dehmelt
Sales Engineer Warehouse Technology
STOPA Anlagenbau GmbH
Industriestr. 12
77855 Achern-Gamshurst
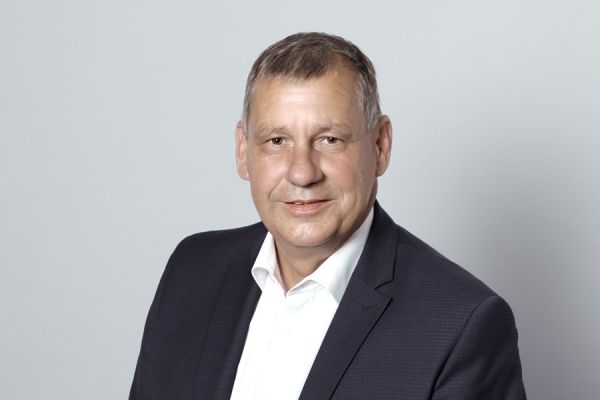
Rolf Eckhardt
Sales Engineer Warehouse Technology
STOPA Anlagenbau GmbH
Industriestr. 12
77855 Achern-Gamshurst
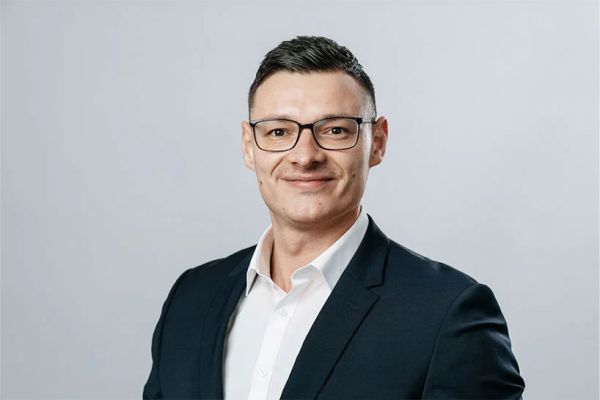
Andreas Pahl
Sales Engineer Warehouse Technology
STOPA Anlagenbau GmbH
Industriestr. 12
77855 Achern-Gamshurst