Tower storage system in the pit
According to HANSA Klimasysteme, the main reason for investing in a STOPA FLEX sheet metal storage system was the prospect of being able to work without a human presence. Since the operator’s workshop is not high enough to install a tower storage system at the desired height, STOPA placed the system in a pit.
Dipl.-Ing. Arno Bunger, production manager at HANSA Ventilatoren- und Maschinenbau Neumann GmbH, Saterland, points to the roof of the factory building. “If we hadn’t lowered the foundation of the tower storage system below the level of the factory floor, the only alternative would have been to put a hood on the roof. The idea with the pit proved to be more economical.”
The air conditioning specialists did not want to compromise on the height of the sheet metal storage system supplied by STOPA Anlagenbau GmbH, Achern-Gamshurst, especially since the system has to accommodate a wide range of materials. Jens Fresemann, prefabrication, cutting department, knows the data: “We store sheets of aluminum, galvanized sheet metal and stainless steel in thicknesses of 0.8 to three millimeters in the system.”
Process-optimized production
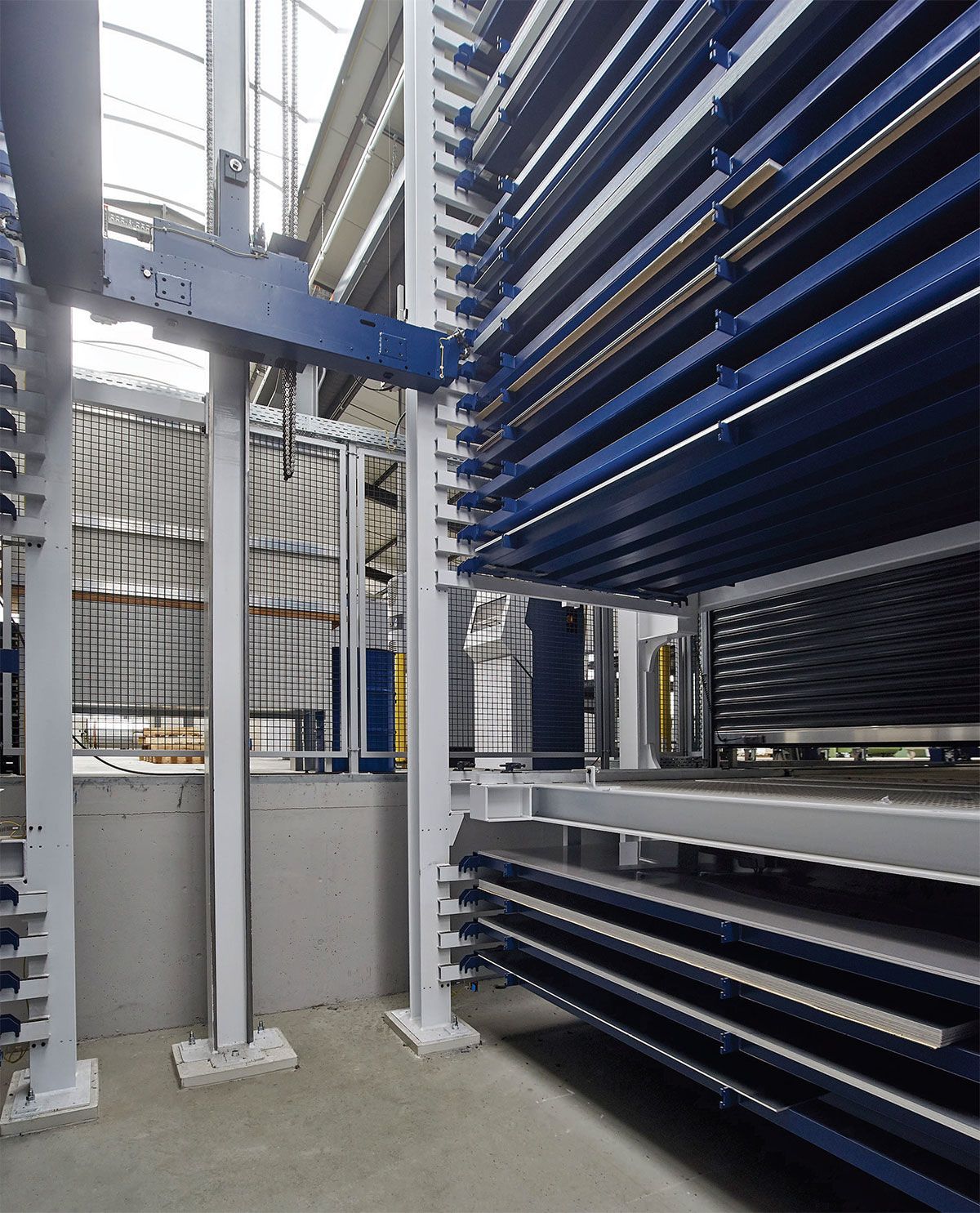
The idea of placing the storage system in a pit proved to be the most economical solution
The STOPA FLEX is one of the manufacturer’s many customized solutions. In this respect, the operator has chosen a system that continues to pursue the path of process-optimized production by automatically providing the material. The advantages also include a high degree of space utilization, faster access to the sheets and even better organization. In addition, there is less material damage because there is no longer any need for forklift traffic, for example between a cantilever rack and the sheet metal storage area.
The highly available STOPA FLEX supplies a TRUMPF TruPunch 5000 punching machine with sheets and takes the punched finished parts. To be able to transport these outside the warehouse without great effort, the automatic handling device of the station places them on wooden pallets after punching, which lie on flat pallets of the system. The parts are removed on request. Bunger shows punching samples. “All sheets that have holes and edges to be punched pass through the system.” The assembly line, a folding machine and press brakes are supplied with finished parts from the tower storage system, which works with fixed storage locations.
Of the 350 to 400 tons of sheet metal that the operator handles every year, 99.9 percent pass through the system. A small number of sheet metal types that are needed in larger quantities to ensure continuous delivery capability are stored in another hall.
STOPA has equipped the system with three stations for HANSA. The incoming and outgoing goods station works with a scissor lift table equipped with deposit stamps. This is also equipped with pluggable stops for a common coordinate corner and with a stop for smaller sheets in order to be able to position them exactly and to secure the material against shifting.
The company supplies the punching machine with sheets via the double carriage station connected to the long side and stores the finished parts back. The loading carriage, a transport carriage with a fixed height that acts as a lower carriage, transports the sheets to the transfer point of the handling device that feeds the machine. The loading side automation components include the ‘last sheet detection’ function and a spreading magnet device on the transport carriage.
A special feature is the avoidance maneuver of the upper carriage, which serves as the unloading carriage and is of portal design. This carriage moves to predetermined positions with the help of an encoder, where the handling device places the finished parts. Furthermore, the upper carriage moves back as soon as a sheet is to be picked up by the lower carriage. This process facilitates quick material changes and prevents the pick-up device from colliding with the punched sheets lying on the upper carriage.
All stations are equipped with light barriers to monitor the maximum loading height and with electric roller shutters to secure the passage opening in front of the pit. In addition, STOPA has equipped the double station with a pneumatic carriage locking device and, like the scissor lift table of the incoming and outgoing goods station, with pallet locks.
Highlights of the solution
- higher storage capacity by installation in a pit
- enables process-optimized production
- ideal mix of storage capacity and space requirements
- high degree of space utilization
- fast access to sheets
- more order
Ideal mix of storage capacity and space requirements
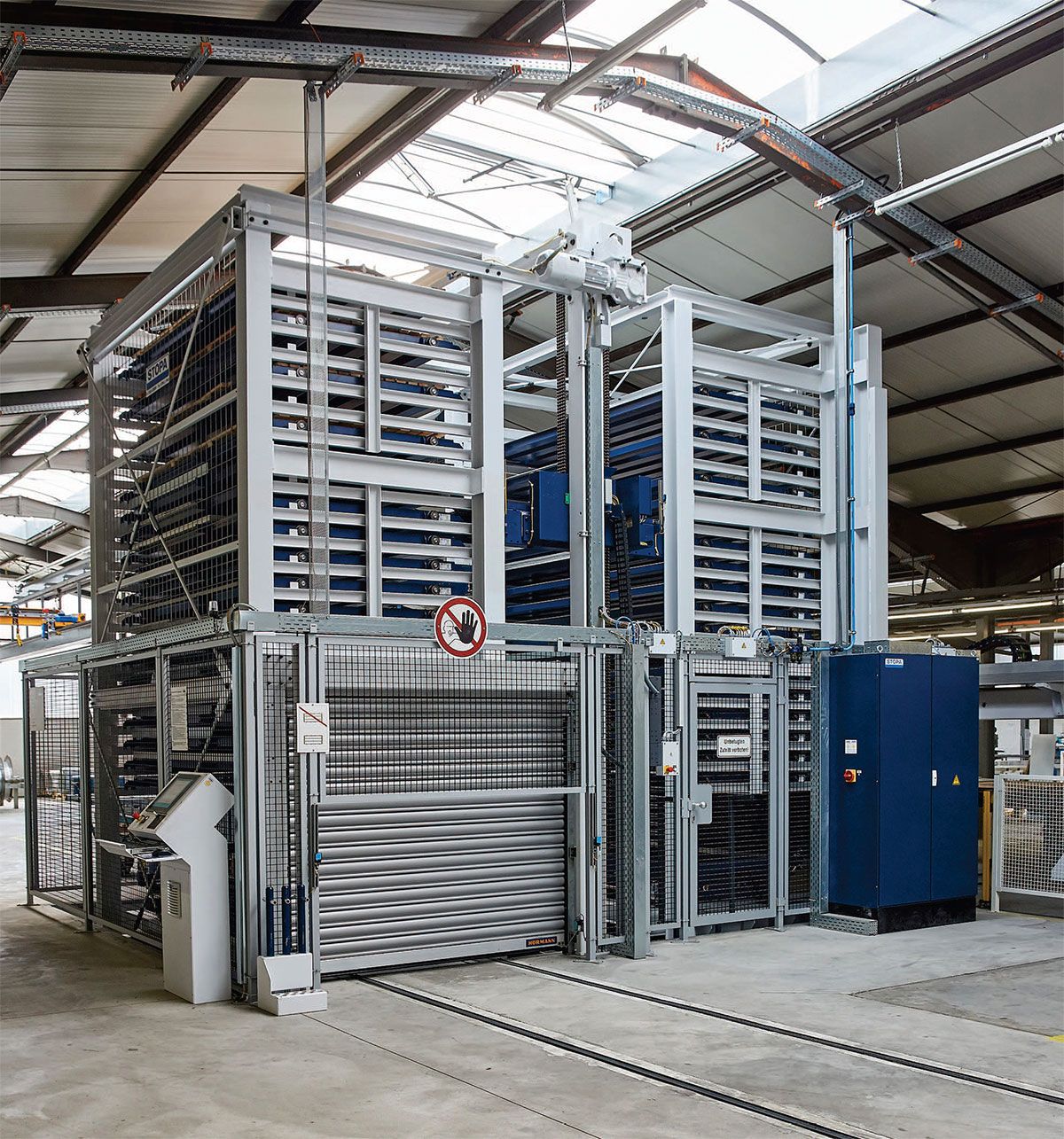
The STOPA FLEX is one of the many customized solutions from the manufacturer
The seven-meter-high, 5.37-meter-long and 6.9-meter-wide tower storage system at HANSA has over 44 flat pallets with a usable area of up to 1,525 x 3,050 millimeters and a permissible payload of up to 3,000 kilograms each. The company, which was founded in 1971 and employs 155 people, uses it to store large and medium-sized metal sheets.
The stable and robust double-mast storage and retrieval machine positions itself at height using an absolute, load-independent digital distance measuring system, which makes it unnecessary to approach a reference point. It can reach speeds of up to twelve meters per minute when lifting and six meters per minute when pulling. The inclined pallet supports prevent the stored load carriers from slipping.
The compact design of the warehouse means that the operator benefits from an ideal mix of storage capacity and space requirements. The loading heights of the storage locations can be varied so that the height of the system can be optimally utilized. The sheets that pass through the warehouse are installed in air conditioning systems that HANSA supplies to customers in Europe and the USA. These include museums, schools, sports halls, swimming pools, data centers, hospitals and industrial companies.
“An alternative to the STOPA FLEX would have been to buy just a punching machine and continue to supply it with forklifts.” Bunger waves this idea aside. “It wouldn’t have been worth it. The tower storage system allows us to work unmanned. At the end of the shift, the sheet metal storage system and the machine automatically process up to eight programmed orders.”
Storage and retrieval with just a few clicks
To prevent the handling device from coming into contact with punched sheets when picking up raw sheets, the upper carriage moves out of the way
The system components are controlled by a real-time soft PLC integrated into an industrial PC. The PC, which is equipped with a 12-inch TFT display, operates the system and visualizes its status. This includes graphical representations of the warehouse and the storage and retrieval machine, a permanent status display in plain text, diagnostic functions, an operating hours counter and the logging of all messages and travel orders.
A warehouse management system that communicates with the machine via an interface set up by STOPA manages the stocks. In addition, the software controls the flow of material, offers inventory management and makes it possible to trigger travel commands and material requests directly at the machine. Bunger observes the interaction between the tower storage system and the punching machine. “The direct interface between the storage system and the punching machine was one of the reasons for the investment.”
The integrated RAID system allows the warehouse to continue operating even if a hard disk fails, thus increasing the availability of the entire system. If there is a power failure, the uninterruptible power supply (UPS) automatically switches off the PC. As part of the warranty, STOPA provides a teleservice that includes diagnostics and a recommendation for troubleshooting. Bunger holds an offer in his hand. “After the warranty expires, we will conclude a maintenance contract.”
Fresemann is standing at the ergonomic control panel. “After a short training and production support by STOPA, we were able to operate the storage system. How easy this is can be seen from the fact that pallets can be stored and retrieved with just a few clicks on the keyboard.”
A big step towards
automation
Before investing in the tower storage system, HANSA had been working with a 25-year-old punch nibbling system that had to be loaded manually. In this context, the STOPA FLEX, which went into operation at the beginning of May 2016, was a big step forward. Bunger is satisfied. “Our expectations have been fully met. Another factor in favor of STOPA was that this company was the only one that had already implemented storage systems in combination with TRUMPF machines in practice, which made coordination much easier. The investment also allows us to benefit from personnel savings and higher dimensional accuracy. In addition, the time spent searching for sheets is eliminated. Apart from that, it is possible to increase sales without having to hire additional personnel. The employees that we save in this area are employed elsewhere in production. The most important investment criterion was, to emphasize it again, that the tower storage system and thus also the punching machine can work without an operator.”
Author: Jürgen Warmbol
Sales Contact Person
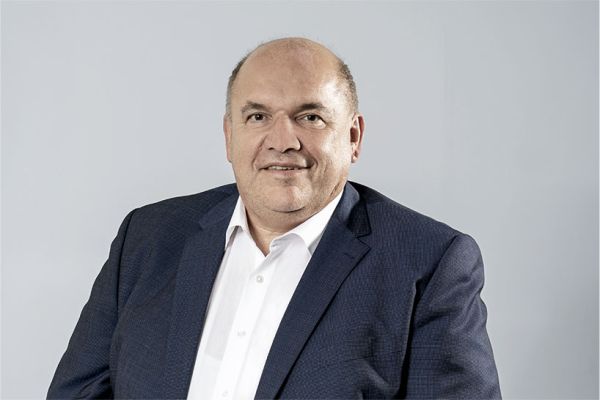
Holger Dehmelt
Sales Engineer Warehouse Technology
STOPA Anlagenbau GmbH
Industriestr. 12
77855 Achern-Gamshurst
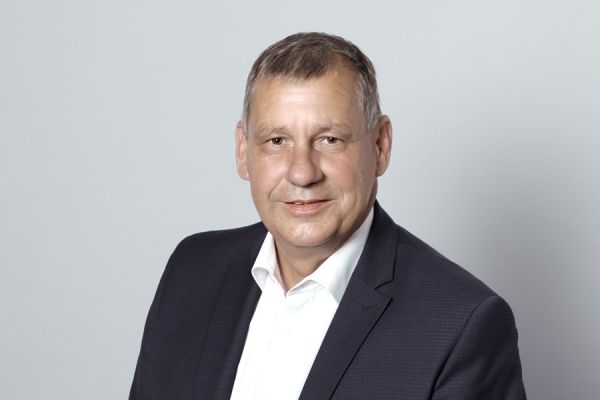
Rolf Eckhardt
Sales Engineer Warehouse Technology
STOPA Anlagenbau GmbH
Industriestr. 12
77855 Achern-Gamshurst
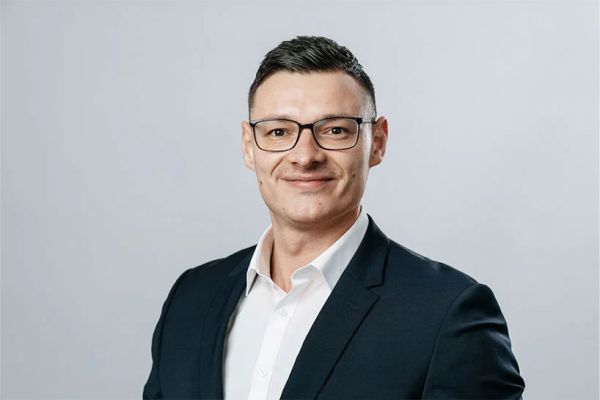
Andreas Pahl
Sales Engineer Warehouse Technology
STOPA Anlagenbau GmbH
Industriestr. 12
77855 Achern-Gamshurst