Storage System at the centre of sheet metal processing
By investing in a STOPA ECO tower storage system, Winkhaus, a manufacturer of building hardware, has increased the safety of handling sheet metal and thus its efficiency. Other advantages include space-saving storage, the ability to access raw sheets quickly, less material damage and more organization.
Dipl.-Ing. Uwe Birwe, Head of Industrial Engineering at Aug. Winkhaus GmbH & Co. KG, Telgte, stands in front of the tower storage system, which is around six and a half meters high, four meters long and three meters wide. “We only process medium-sized metal sheets that cover our product range. That’s why we don’t need a storage system for large-format metal sheets, which we wouldn’t have considered anyway, not least because of the limited space available. “ The installation of the compact tower storage system alone, which had to be installed with millimeter precision in the available space, was a challenge. In this respect, the STOPA ECO, developed by STOPA Anlagenbau GmbH, Achern-Gamshurst, meets all the expectations that Winkhaus, as a leading provider of high-quality window technology, door locking and access organization, had for the investment.
Optimal packing density
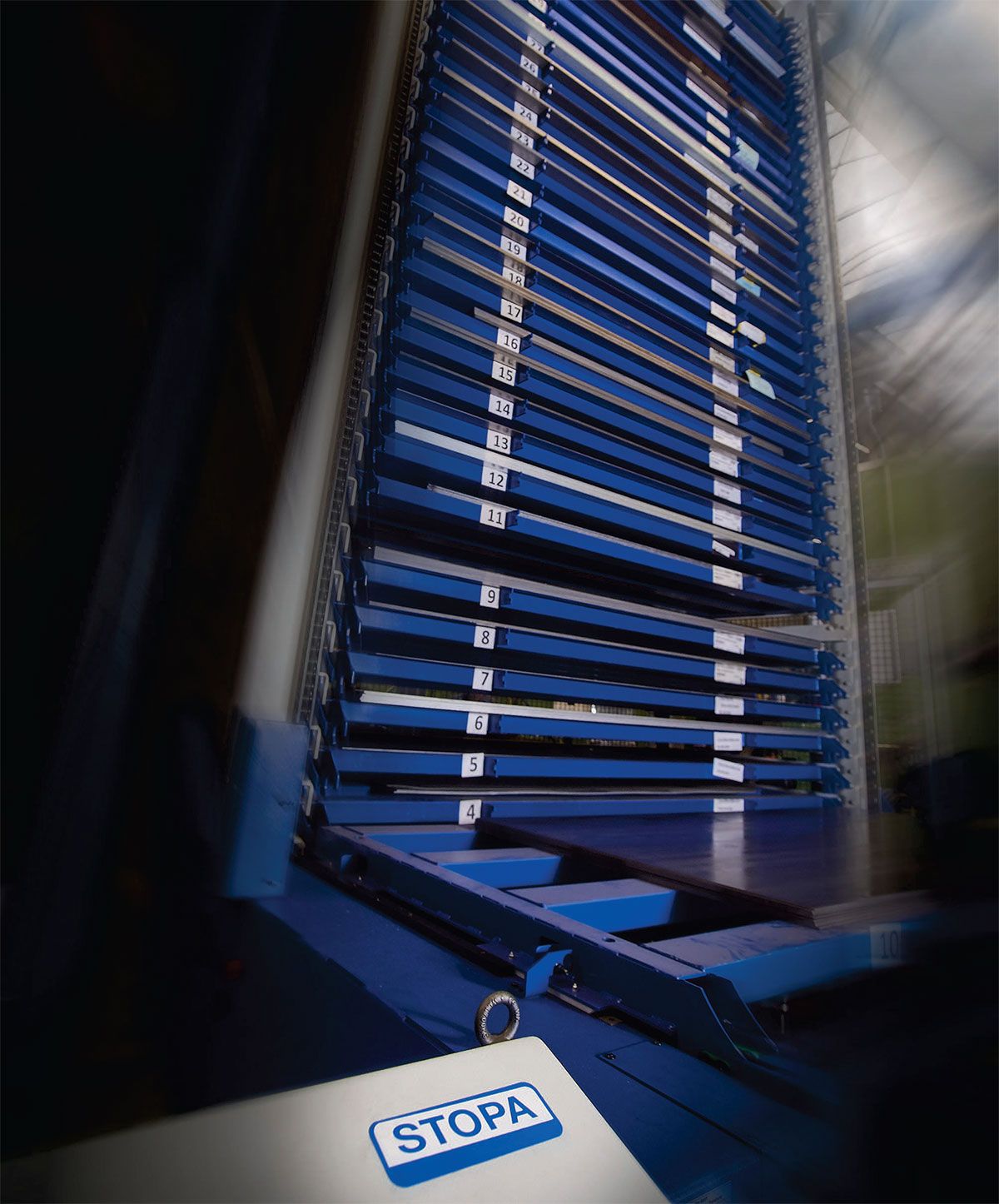
Since Winkhaus processes around 160 tons of sheet metal every year, the investment in the storage system is a forward-looking step
Birwe walks across the small area taken up by the storage system. “We benefit from a high degree of space utilization, minimized material damage and quick access to raw sheets. In addition, there is a significantly reduced search effort, based on more order, and a short-term return on investment.” The most important thing, as Birwe emphasizes, is the safety that the STOPA ECO stands for. This is helped by the fact that the sheets can be stored, picked up and delivered in a defined manner. Since all the types of sheet metal used, in thicknesses of between half a millimeter and eight millimeters, for example stainless steel, aluminum or high-strength steels, are buffered in the tower storage, it is no longer necessary to store sheets on their edges. The family business, which was founded in 1854, has replaced floor stacking and a manually operated drawer rack, in which sheets were stored up to two meters high, with the tower storage system. According to Birwe, half the space is now required and the employees have been relieved of physical strain.
The tower storage system, which operates reliably in three shifts six days a week with an availability of almost 100 percent, started operation at the beginning of December 2018. Birwe points to the rack block, which is equipped with longitudinal connections and diagonal reinforcements in the frame as well as with a rear push-through protection. “We decided on fixed-position storage and a fixed height grid of 60 millimeters. Because this solution matches the order quantities of our sheets, we achieve an optimal packing density.” If a height grid of 200 millimeters is required, for example to be able to load higher goods or pallets in front, the rack block could be retrofitted with a double loading height.
Highlights of the solution
- High level of safety when handling sheet metal
- High degree of space utilization
- Fast access to raw sheet metal
- Significantly reduced search effort
- Minimized material damage
- Short-term return on investment
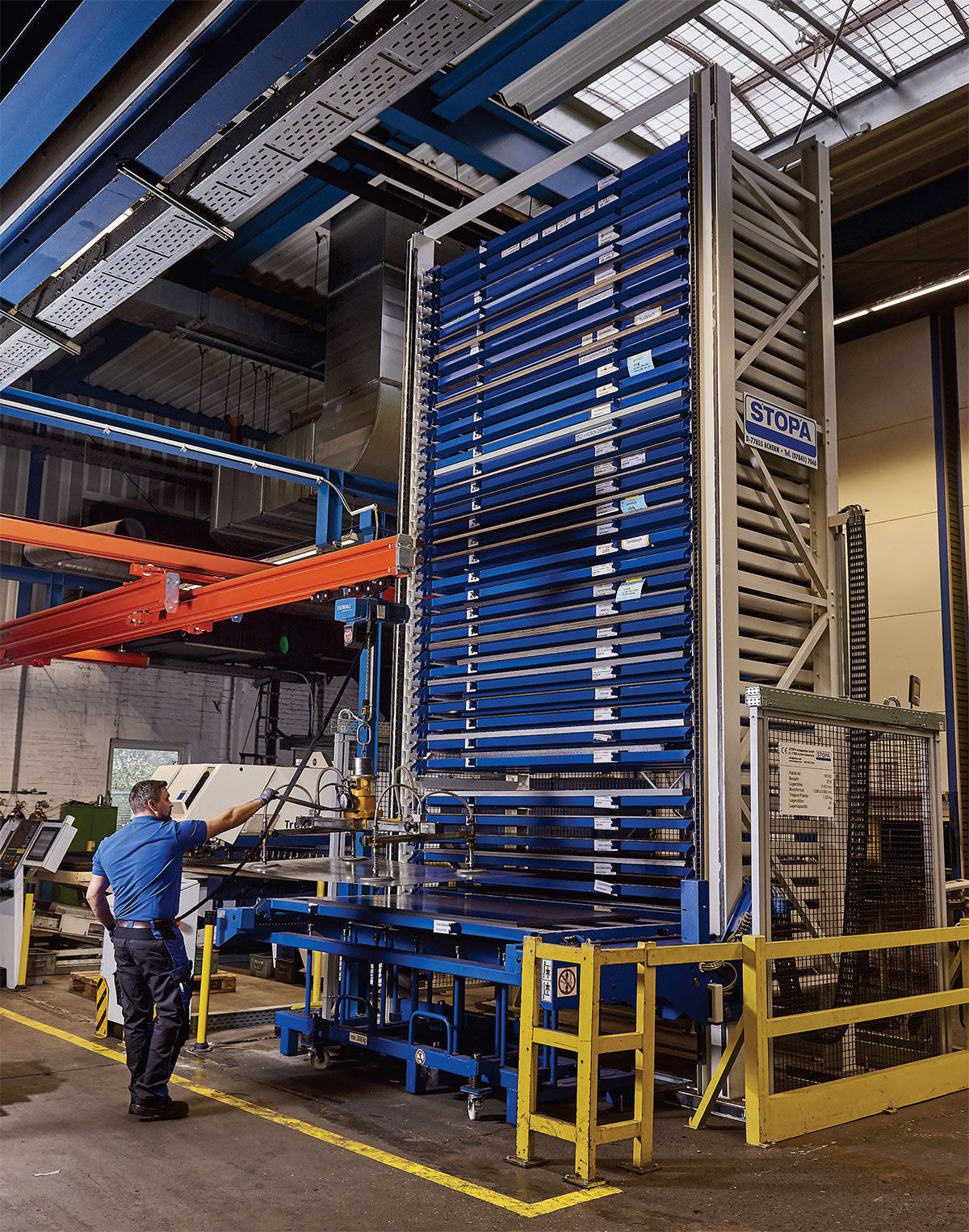
The operator lowers the system pallet from the tower and lifts the sheet metal panels ergonomically with the crane
Ergonomic and safe processes
Forklift trucks supply the STOPA ECO with delivered sheet metal packages, which they place on the fixed storage stamps of the storage platform. Before this, Alex Gutjahr, the warehouse operator, enters the number of a compartment at the central system terminal to request an empty system pallet from it.
The control system then automatically moves the selected pallet from its storage location to the stationary lifting or load beam of the tower storage system. This lowers the load carrier between the stamps of the platform so that the plates can be taken over as soon as the forklift has deposited them. During the subsequent storage process, a light barrier checks whether the maximum loading height is being adhered to. Gutjahr himself also benefits from the solution. “The clearly structured control panel simplifies interaction with the warehouse.”
The company, which employs around 2,200 people worldwide, supplies two TRUMPF punch laser machines of the TruMatic 6000 and 7000 models from the sheet metal warehouse. The operator initiates the removal by entering the compartment number of the pallet to be stored and pressing the confirmation button until the removal position is reached. The requested sheets are removed from the pallet using a crane, which is located on the low-wear and low-maintenance load beam. The beam, which is equipped with a pull and push device, is monitored for safe operation and can reach speeds of eight meters per minute when lifting and four meters per minute when pulling. To ensure that the different types of sheet metal are distributed in the storage tower in line with daily requirements, 40 storage compartments and system pallets are available. The load carriers are designed for payloads of up to 1,200 kilograms. STOPA has also equipped them with limiting plates and a self-supporting frame construction with longitudinal beams and sliding rails.
When a new delivery is due, the operator is forced to select a load carrier that already contains sheets of metal. First, the operator removes the system pallet from the tower and lifts the existing sheets off the pallet using the crane. He then places the newly delivered material on the pallet and stacks the older sheets on top of it.
To return the load carrier to its compartment, the operator presses the OK button again. Winkhaus stores both raw and residual sheets. To enable the crossbeam, whose height is measured by an absolute and load-independent digital measuring system, to reach the two lowest storage compartments, the empty rack in front of it can be moved.
The STOPA ECO tower storage system is equipped with a compact control system or programmable logic controller, including an LCD display and touchscreen user interface. If an error occurs, it is displayed as a text message. The warehouse is managed via the operator’s SAP system, which primarily supplies customers in Western Europe, including Poland. These include builders, window manufacturers, door manufacturers, locksmiths, building element and building hardware dealers, and architects.
“We do not use the online operation offered by STOPA, which makes it possible to automatically process an order list with up to ten transport orders,” says Birwe. “Our orders are too small for that. In most cases, we only need one sheet.”
A forward-looking decision
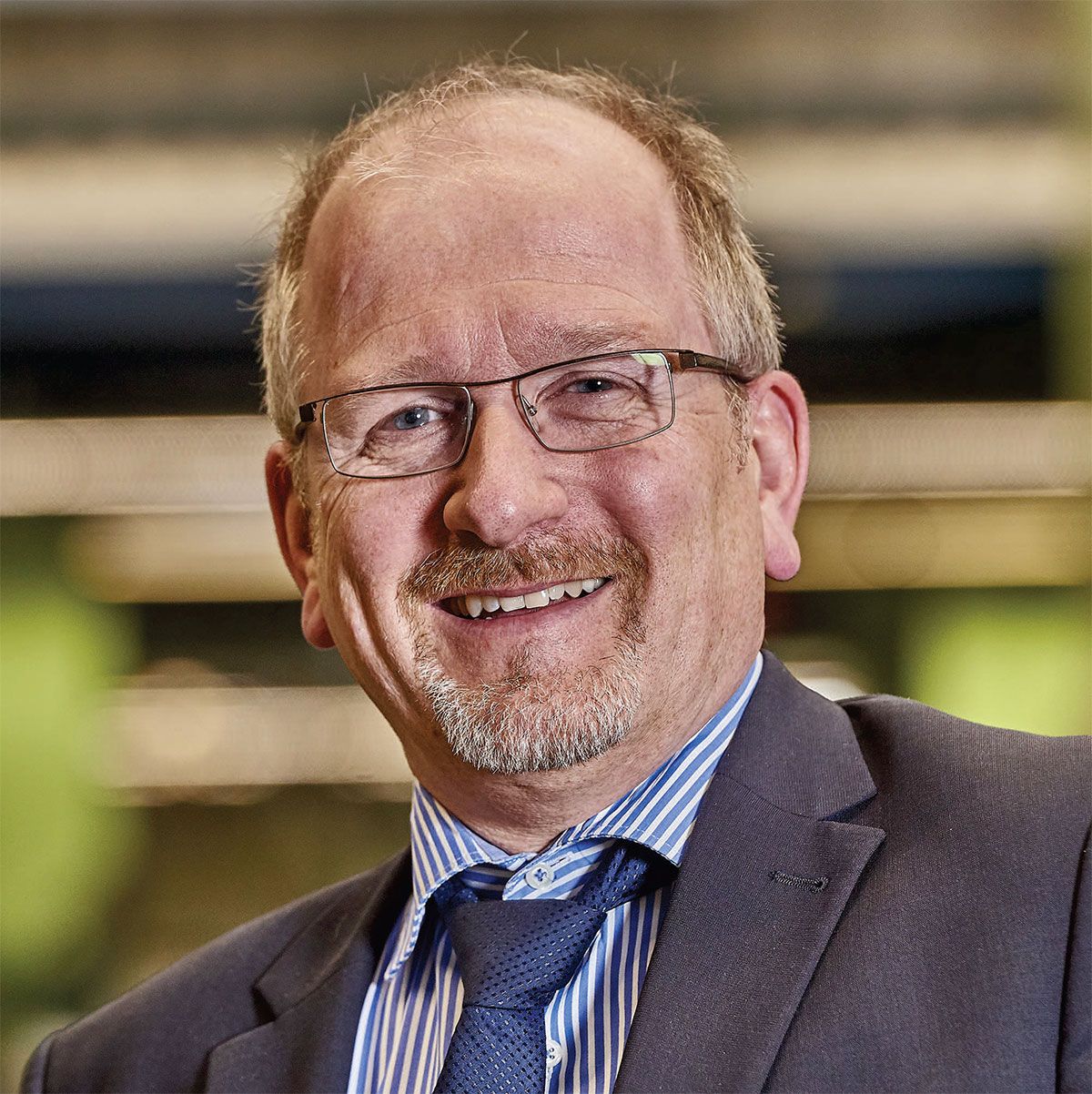
Dipl.-Ing. Uwe Birwe, Head of Industrial Engineering at Aug. Winkhaus GmbH & Co. KG, Telgte
Since around 160 tons of the approximately 30,000 tons of steel that Winkhaus processes annually are sheet metal, the investment in the storage system can be seen as a forward-looking step. Birwe points to a stack of trade journals. “We analyzed the market and informed ourselves about the systems of other manufacturers. The STOPA tower storage system meets our requirements in terms of height, compactness, ease of maintenance and price-performance ratio. Another positive aspect is that, unlike alternative suppliers, STOPA’s medium format of 1,250 x 2,500 millimeters is standard. “ In addition, the sheet metal storage system’s modular concept makes it an affordable entry point for the automatic storage of flat materials.
Author: Jürgen Warmbol
Sales Contact Person
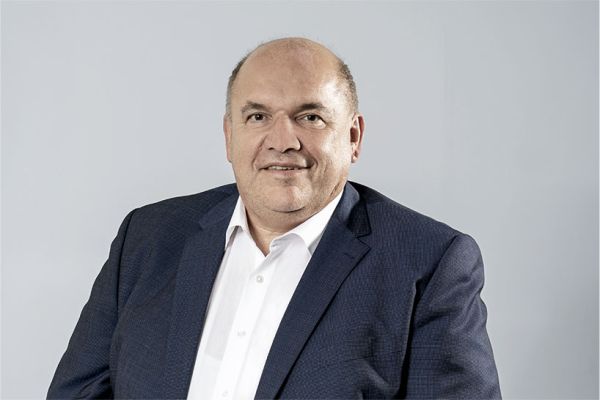
Holger Dehmelt
Sales Engineer Warehouse Technology
STOPA Anlagenbau GmbH
Industriestr. 12
77855 Achern-Gamshurst
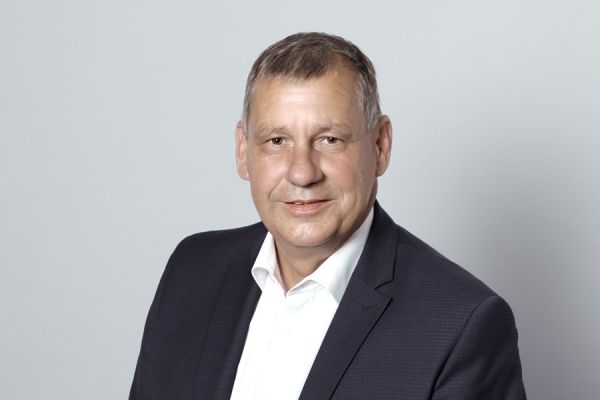
Rolf Eckhardt
Sales Engineer Warehouse Technology
STOPA Anlagenbau GmbH
Industriestr. 12
77855 Achern-Gamshurst
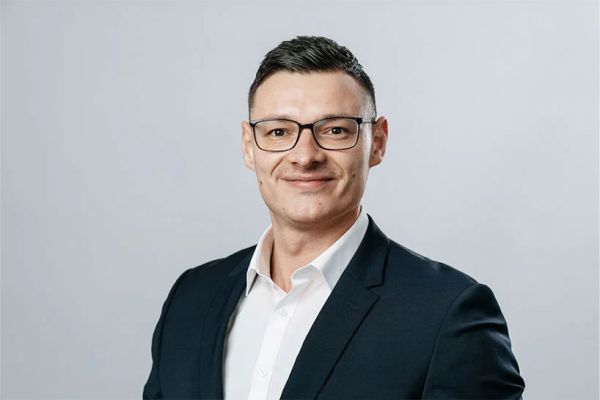
Andreas Pahl
Sales Engineer Warehouse Technology
STOPA Anlagenbau GmbH
Industriestr. 12
77855 Achern-Gamshurst