sheet metal storage system on two building levels
Since investing in a STOPA COMPACT II sheet metal storage system for large-format sheets, BBW Lasertechnik has benefited above all from more storage capacity and greater flexibility. Added to this is the future-oriented option of being able to supply sheet metal processing machines on two floors.
Johann Bürger, co-founder of BBW Lasertechnik GmbH, Prutting (Bavaria), who shares the management of the current family business with his son Andreas, stands in front of the sheet metal storage system supplied by STOPA Anlagenbau GmbH, Achern Gamshurst. “The system, which is around 10.8 meters high, 11 meters long and 5.6 meters wide, extends over both floors of our factory building. STOPA installed the storage system with millimetre precision between the walls, columns and the passage to the lower level, which we use to connect the first floor with the second floor intralogistically.” Andreas Bürger shows photos of the installation. “The prefabricated steel components and the storage and retrieval machine were lifted into the hall through the open roof and the opening in the upper floor using a mobile crane. We didn’t have a more economical alternative.” The managing directors expect more storage capacity and flexibility, less damage to the sheets and less time spent handling and searching for materials from the system designed for the large format. Apart from this, the company is able to connect its laser systems, which are in production, to the warehouse at any time. “Before investing in the STOPA COMPACT II, we worked with a warehouse that was designed for smaller formats,” explains Johann Bürger. “The switch to large formats has proven to be practical and up-to-date.”
Sheet metal storage with added value
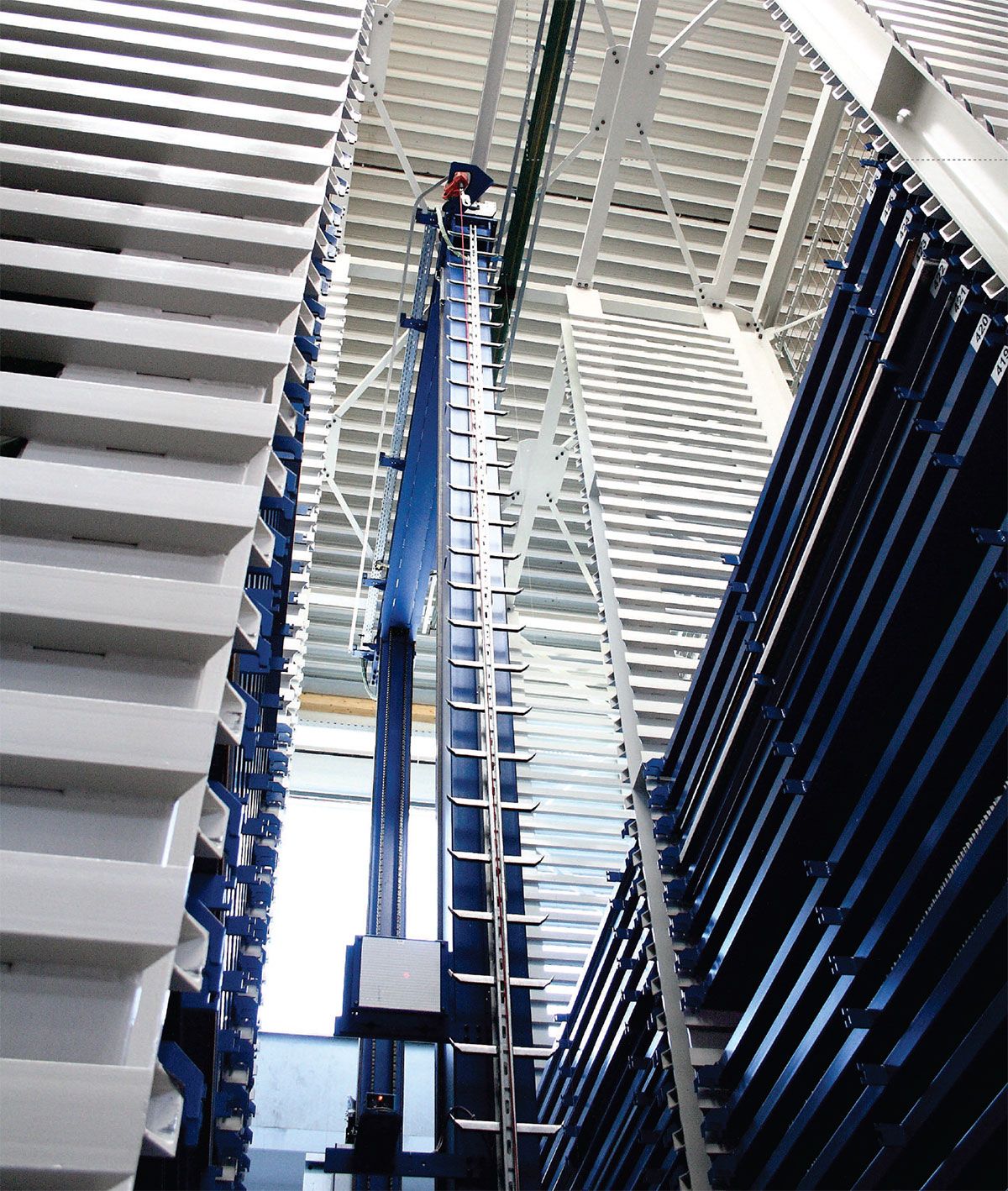
The STOPA COMPACT II sheet metal storage system connects two floors intralogistically
At BBW Lasertechnik, the STOPA COMPACT II consists of four rack blocks arranged in two rows and equipped with 208 storage locations. There are 100 flat pallets available as load carriers, each with a maximum usable area of 1,525 x 3,050 millimetres, which can be loaded with sheets weighing up to 3,000 kilograms. The key added value of this storage system includes a patented weighing device, whose weighing cells are integrated into the pallet running surface of the draw beam, and the elimination of hydraulics. This solution reduces the cycle time by around 80 percent. Added to this is intelligent energy management, based on a concept with two powerful, lightweight drive motors instead of one heavy motor, resulting in an overall weight reduction of around half a ton. In addition, the operator can make the regenerative energy of one drive available to another as motor energy.
STOPA also achieves smoother running of the system pallets by compensating for tolerances, thus increasing process reliability. An advantage that also leads to a longer service life, less downtime and lower maintenance costs.
Highlights of the solution
- more storage capacity
- greater flexibility
- high process reliability
- shorter cycle times
- intelligent energy management
- less damage
Efficient processes
Employees unpack delivered sheet metal packs on the unpacking table installed on the first floor in front of the warehouse, which is designed for large formats (3,000 x 1,500 millimetres) and can be adapted to a wide variety of wooden pallets and sheet metal formats using sliding support stamps. From there, a forklift lifts the depalletized sheet metal package and places it on the goods infeed and outfeed station arranged on the long side. The scissor lift table, which is equipped with movable depositing stamps and coordinate corner stamps, allows the sheet stack to be positioned precisely on the empty system pallet. The scissor lift table is also equipped with a pneumatic trolley and pallet lock and a light barrier that monitors compliance with the maximum permissible loading height of 90 millimetres.
When the scissor lift table moves into the warehouse after being released by the operator, the robust two-mast storage and retrieval machine (SRM) pulls the pallet down and stores it. The second station installed on the first floor on the long side is used exclusively for outgoing goods. Instead of a scissor lift table, it is equipped with a fixed-height transport trolley, which has the same technical features apart from the lift. The warehouse is supplied by a TRUMPF TruLaser 5030 laser cutting system. BBW Lasertechnik does not store sheet metal or semi-finished products.
The operator works with fixed storage at a loading height and makes full use of the available space and height. The stacker crane reaches speeds of 60 meters per minute when moving and 23 meters when lifting. The telescopic pull/push device on both sides of the stacker crane reaches 20 meters per minute. Longitudinal positioning is performed using a digital distance measuring system, while height positioning is performed using an absolute and load-independent digital distance measuring system, which eliminates the need to move to a reference point. A data light barrier enables non-contact, wear-free data transfer to the stacker crane, which is supplied with power via an overhead conductor rail.
The system components are controlled via a real-time soft PLC integrated into an industrial PC. Andreas Bürger leans against the ergonomic control panel. “Operating the warehouse is simple and doesn’t require a lot of training.” The industrial PC equipped with a touch screen is built into the console, which operates the system and visualizes its status. This includes graphical representations of the warehouse and the stacker crane, permanent status displays in plain text, diagnostic functions and the logging of all messages and transport orders. The integrated raid system enables warehouse operations to continue if a hard disk fails. This increases the availability of the entire system. An uninterruptible power supply (UPS) protects against data and program losses. STOPA’s service also includes remote diagnosis of the system control via VPN. The STOPA warehouse management software “WMS-Basic 4.0” used at BBW Lasertechnik synchronizes the stock levels with the operator’s ERP system at night via a host interface. The data is managed in a database and automatically backed up daily.
Pioneering decision
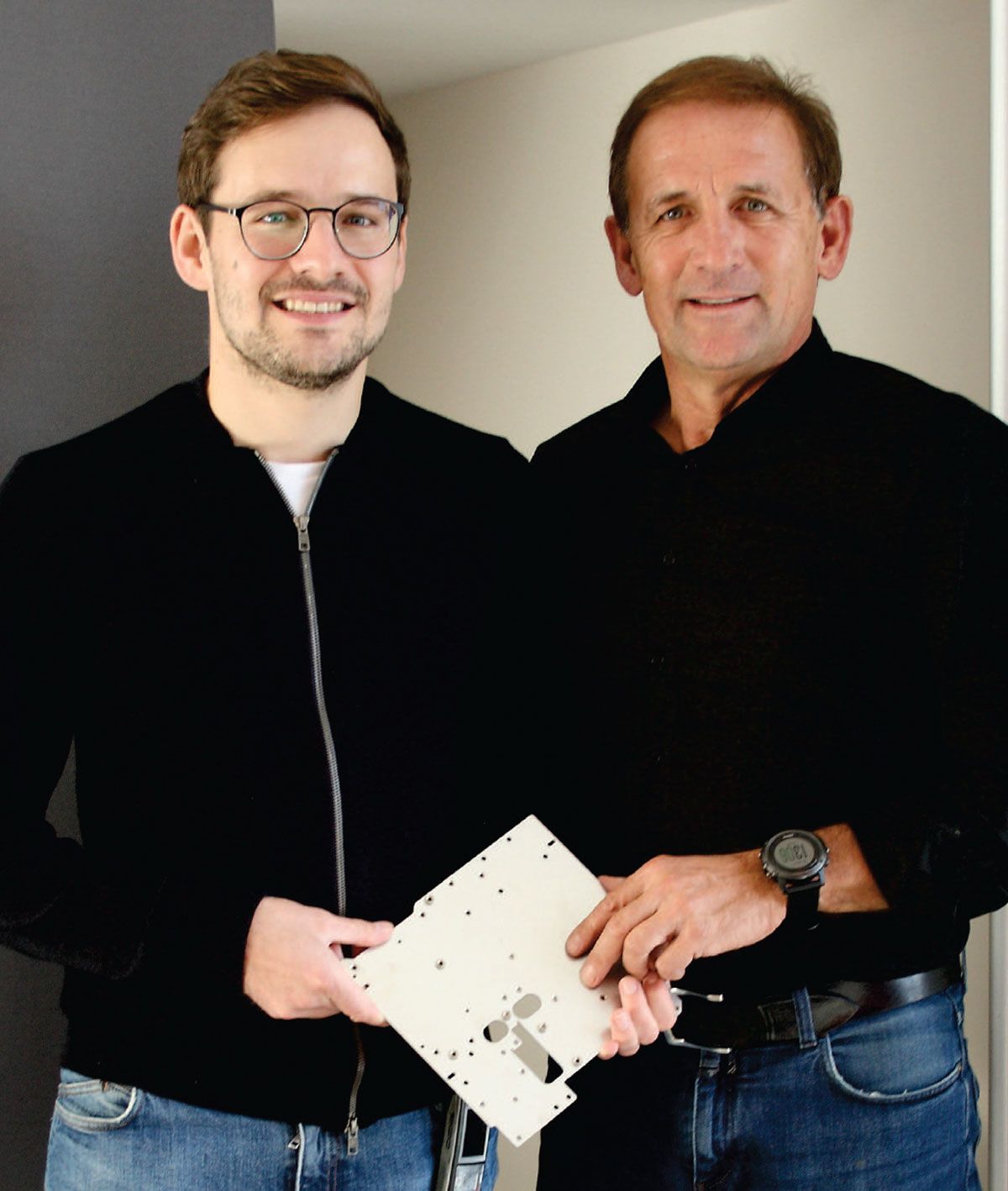
Johann (left) and Andreas Bürger (right), Managing Directors of BBW Lasertechnik GmbH, Prutting (Bavaria)
The focus of BBW Lasertechnik’s broad spectrum of laser material processing is on fine laser cutting and laser welding. Processing with ultra-short laser pulses, bending with a six-axis fence, assembly production and the complete package, which ranges from design and development to the end product, should also be emphasized.
The price-performance ratio and the supplier combination of STOPA and TRUMPF, which eliminates interface problems based on many years of experience, also contributed to the investment decision in favor of STOPA. The fact that all deadlines were met was not least due to the parallel planning of the building and warehouse. The go-ahead for the STOPA COMPACT II, which operates in two shifts with almost 100 percent availability, was given in December 2018. Johann Bürger is already thinking ahead. “As the sheet metal warehouse can be expanded at any time in the future, we are focusing on the option of integrating a third station on the upper floor of the hall and connecting additional machines.”
WMS-TOWER 4.0 with a broad program package
The long goods warehouse is equipped with the STOPA warehouse management software “WMS-TOWER 4.0“, which has all the functions required to operate a high-bay warehouse as a fixed location warehouse. The data is managed by a Microsoft SQL Server Express database. A teleservice is available as part of the warranty, which includes diagnostics and recommendations for rectifying faults. It includes remote diagnosis of the system control via the STOPA Tele-Presence portal. Thanks to the WMS, the STOPA LG-E long goods warehouse, which went into operation at Lehnhoff Hartstahl in August 2020, offers a wide range of functions that can be adapted to the desired requirements. “Not yet installed, but planned and prepared, is the data flow between the long goods warehouse and our ERP system as well as the systems to be supplied,” emphasizes Spengler. “This means that inventory data can be exchanged and transport orders can be placed that contain optional accompanying information for material tracking. In this respect, we benefit from seamless documentation of the stored goods.” As the software generates the orders automatically, some of the manual entries are no longer necessary. This is an advantage in terms of the reliability of the inventories, which are managed as total and partial inventories. STOPA has also integrated plausible, intuitive user guidance into the graphical program interface and hidden program parts that are not required. The access rights of individual users can also be restricted to defined areas of merchandise management.
The operation of the long goods warehouse, which offers almost 100 percent availability and works in two shifts, proves to be user-friendly thanks to clear graphical user interfaces. Regardless of whether full or partial withdrawals and additions or transfers are involved.
Author: Jürgen Warmbol
Sales Contact Person
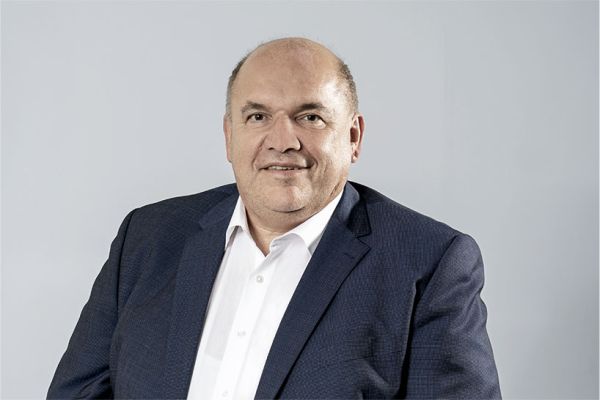
Holger Dehmelt
Sales Engineer Warehouse Technology
STOPA Anlagenbau GmbH
Industriestr. 12
77855 Achern-Gamshurst
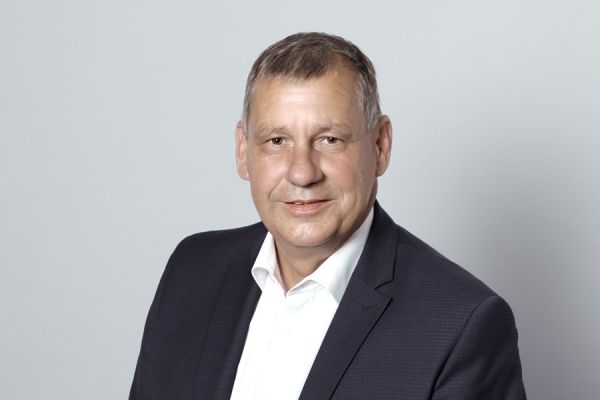
Rolf Eckhardt
Sales Engineer Warehouse Technology
STOPA Anlagenbau GmbH
Industriestr. 12
77855 Achern-Gamshurst
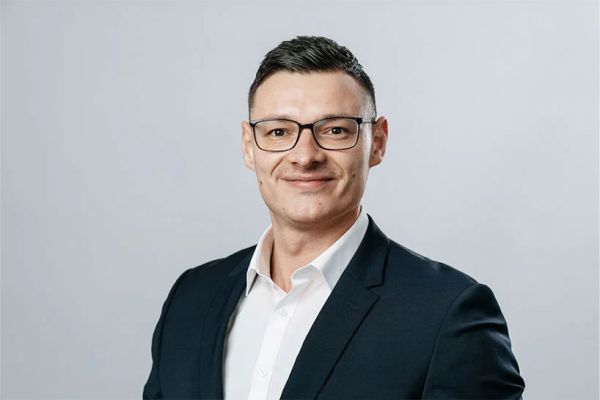
Andreas Pahl
Sales Engineer Warehouse Technology
STOPA Anlagenbau GmbH
Industriestr. 12
77855 Achern-Gamshurst