In Produktivität investiert
Durch den Einsatz eines automatischen STOPA COMPACT Blechlagers hat die CNH Industrial Belgium N.V. die Produktivität ihrer angebundenen Laserschneidanlagen und damit ihrer gesamten Blechbearbeitung nachhaltig gesteigert. Der Betreiber denkt aber schon weiter: Er möchte die Länge des Systems von derzeit rund 45 Meter fast verdreifachen und all seine Laserschneidanlagen anbinden.
Als Grund für die Automatisierung nennt der Landmaschinenhersteller der Marke New Holland, dass er in seinem Kompetenzzentrum im belgischen Zedelgem zusätzliche Kapazitäten für die Blechbearbeitung benötigt. Vor diesem Hintergrund hat er in das STOPA COMPACT und in vier Laserschneidanlagen investiert und durch die neuen Maschinen zwei alte ersetzt.
Koen Mergaert, Verantwortlicher Arbeitsvorbereitung, Blechbearbeitung und Dreherei bei CNH Industrial Belgium, stoppt beim Rundgang vor dem von der STOPA Anlagenbau GmbH, Achern-Gamshurst, gelieferten Lagersystem. »Bisher haben wir sämtliche Maschinen mithilfe eines Brückenkrans versorgt. Während wir für den Wechsel eines Blechpaketes an einer Laserschneidanlage durch den Kran eine halbe Stunde benötigt haben, sind es jetzt im automatischen Betrieb nur noch zwei Minuten. Außerdem können wir im Bereich der Automation rund um die Uhr weitestgehend mannlos arbeiten. Diese Möglichkeit nutzen wir auch samstags und sonntags jeweils über zwölf Stunden.«
Johan Vermote, Arbeitsvorbereitung Blechbearbeitung, ergänzt: »Ferner kommen wir mit weniger Leuten aus, wenn wir die neuen Maschinen beschicken. Ein Vorteil, der primär darauf beruht, dass wir die vier an das Lager angebundenen Maschinen mit Blechen versorgen, ohne den Kran einsetzen zu müssen. Für die nicht angegliederten Maschinen brauchen wir heute immer noch je Schicht zwei Kranführer. Hinzu kommt ein Bediener für zwei dieser Maschinen. Macht dieser eine Pause oder ist er anderswo beschäftigt, könnten an den betreffenden Maschinen zusätzliche Wartezeiten entstehen.«
Mehr Wirtschaftlichkeit
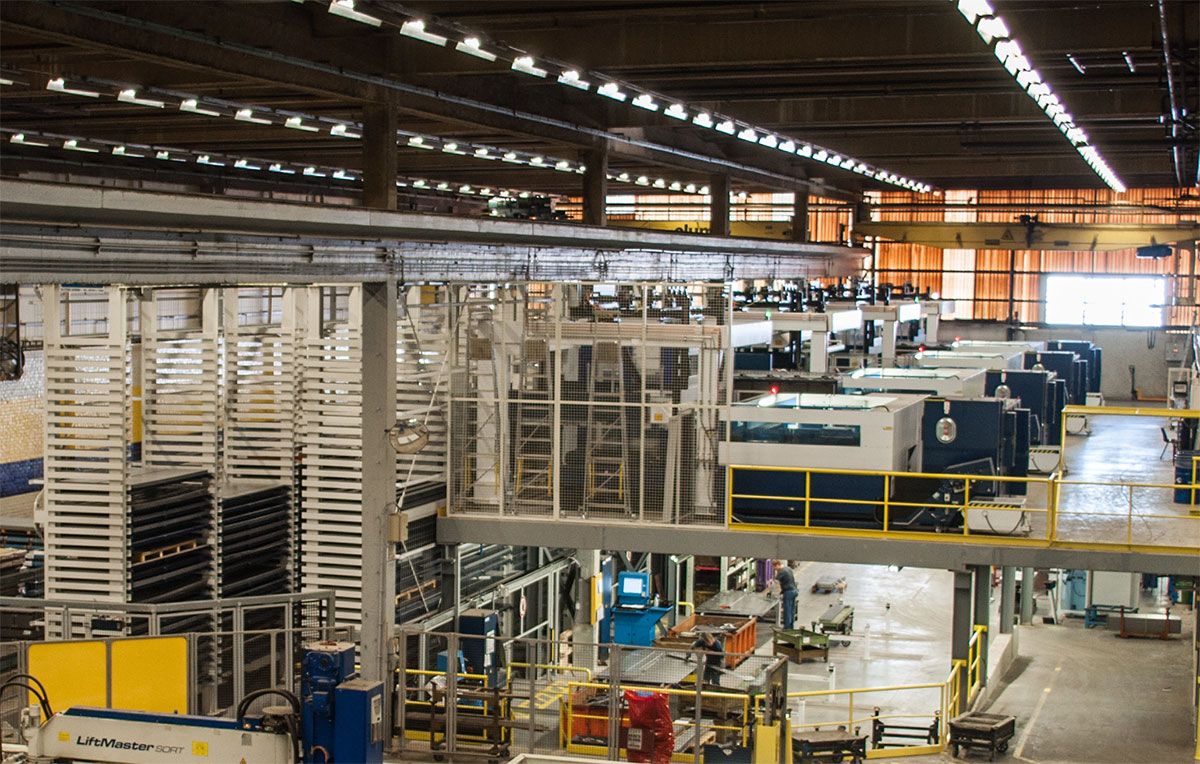
Durch den Einsatz eines automatischen STOPA COMPACT Blechlagers hat CNH Industrial Belgium die Produktivität seiner gesamten Blechbearbeitung nachhaltig gesteigert.
Früher hat der Landmaschinenhersteller, der täglich 14, in der Hochsaison 17 Mähdrescher der Marke New Holland fertigt, die Tafeln am Boden gelagert. Daher ist es oft auch erforderlich gewesen, die Blechpakete durch den Kran umzustapeln, um das gewünschte Material aufnehmen zu können. Obendrein ist es Aufgabe des Krans gewesen, nicht verarbeitete Bleche zurückzulagern. Ein Aufwand, der nach wie vor in Verbindung mit den nicht an das System angebundenen Maschinen anfällt. Abgesehen davon stellen die Kranfahrten mit Last auch ein Sicherheitsrisiko dar, zumal sie über eine bis zu 250 Meter lange Strecke führen.
Koen Mergaert blättert in einer Statistik. »Vor der Automation haben wir jährlich 50.000 Bearbeitungsstunden bei Zulieferern zugekauft. Heute vergeben wir nur noch in der Hochsaison Aufträge und bloß für 20.000 Stunden. Weil wir unseren Eigenfertigungsanteil ausgebaut haben, sinken zudem die Anzahl der Transporte und die Logistikkosten.« Wegen der höheren Produktivität verringert sich auch die Menge der komplexen Komponenten, die CNH Industrial Belgium für ihre Schwesterunternehmen von Zulieferern kaufen muss und die häufig teurer sind, als man sie weiterberechnen kann.
Johan Vermote deutet auf die Statistik. »Da wir durch das Automatiklager die Möglichkeit haben, innerhalb eines definierten Zeitraums mehr Bleche zu bearbeiten und eine größere Teilevielfalt zu produzieren, können wir die Tafeln ökonomischer schachteln und verwerten. Infolgedessen ist der Schrottanteil um ein Prozent gesunken. Bedenkt man, dass von den 20.000 Tonnen Blech, die wir im Jahr verarbeiten, 45 Prozent über das STOPA COMPACT laufen, ist das sehr viel. Und die Menge wird noch zunehmen.«
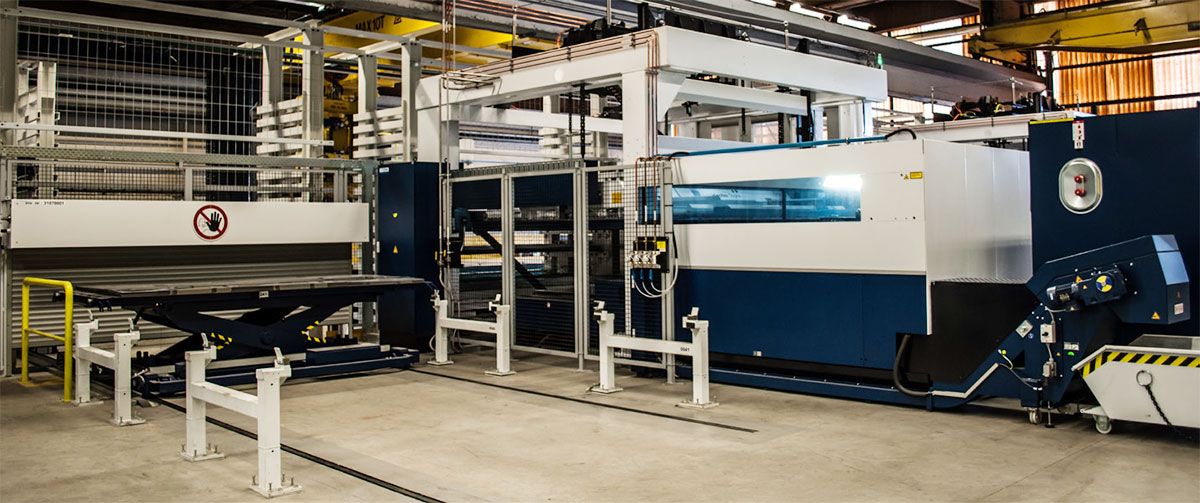
Der Scherenhubtisch der Wareneingangsstation ist mit Ablagestempeln zur Aufnahme der Blechpakete ausgestattet.
Unternehmen
CNH Industrial Belgium: Kompetenzzentrum für Erntemaschinen
Die CNH Industrial Belgium N.V. entwickelt bereits seit 1895 Lösungen für die Landwirtschaft. 2006 hat das Unternehmen die Strategie ‚Clean Energy Leader’ gestartet, um erneuerbare Kraftstoffe, Systeme zur Abgasreduzierung sowie eine nachhaltige Landwirtschaft zu fördern. CNH Industrial Belgium bietet Ackerbau- und Viehhaltungsbetrieben, Lohnunternehmern, Weinbaubetrieben und professionellen Grundstückpflegeunternehmen durch die Marke New Holland laut eigener Aussage die größte Auswahl an bedienungsfreundlichen Traktoren, Erntemaschinen und Ladern. Zum weltweit umfangreichsten Angebot an Landmaschinen zählen mehr als 80 Produktlinien mit über 300 Modellen. Es wird durch einen effizienten Ersatzteilund Kundendienst sowie durch maßgeschneiderte Finanzdienstleistungen ergänzt. Ein globales Händlernetz garantiert einen umfassenden Service und fachkundige Beratung.
CNH Industrial Belgium betreibt hochmoderne, global verteilte Fertigungsstätten. Vier Kompetenzzentren treiben die Entwicklung der nächsten Generation von Landmaschinen voran. Das Werk Zedelgem, Belgien, ist das Kompetenzzentrum für Erntemaschinen und zugleich Produktionsstandort. Es beschäftigt gut 2.800 Mitarbeiter. Der Stahlverbrauch liegt bei 157.000 Tonnen im Jahr. CNH Industrial Belgium stellt hier jährlich rund 3.000 Mähdrescher und 375 Häcksler her. Hinzu kommen 1.500 Vierkantballenpressen für den Weltmarkt. Dafür werden 95 Blechsorten, die beispielsweise hinsichtlich Qualität und Dicke variieren, zu etwa 20.000 verschiedenen Teilen verarbeitet. Seit Ende September 2013 ist CNH Industrial Belgium ein Tochterunternehmen der CNH Industrie N.V., die aus dem Zusammenschluss von Fiat Industrial S.p.A. und CNH Global N.V. entstanden ist.
Lösung auf zwei Ebenen
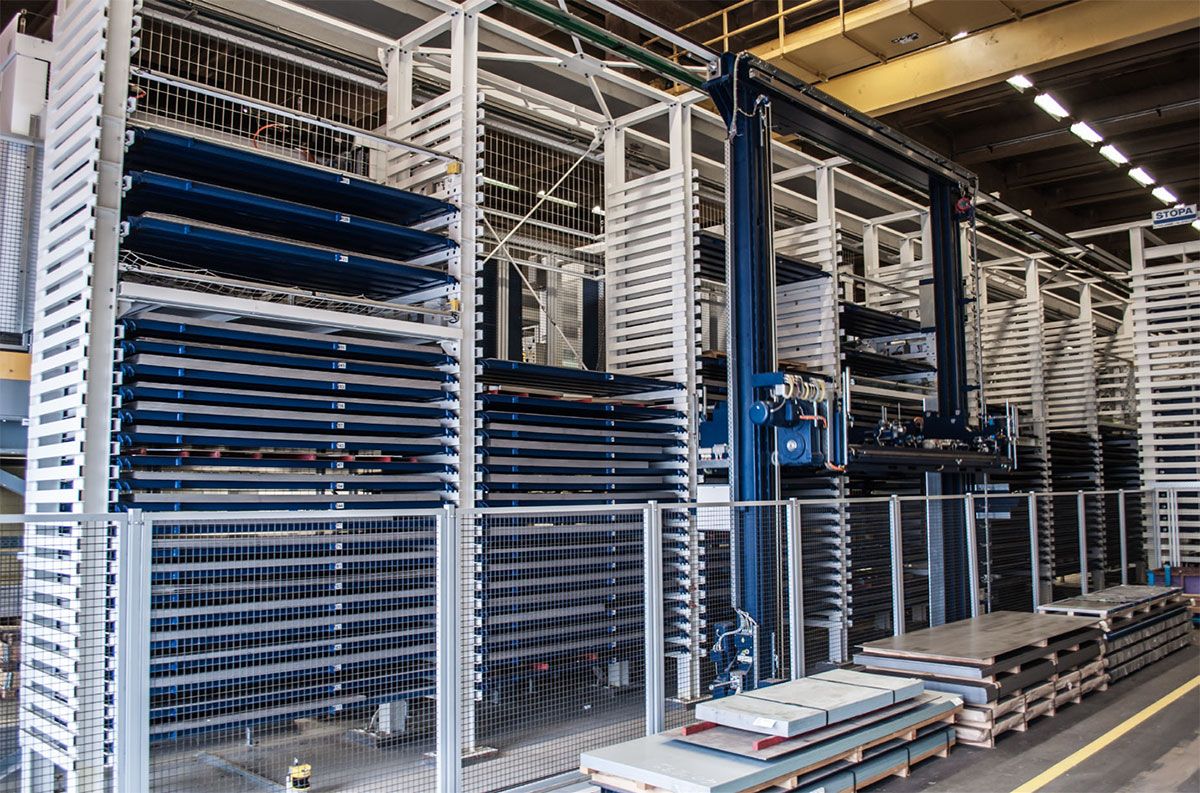
Aufgrund der Automatisierung konnte CNH Industrial Belgium den Eigenfertigungsanteil ausbauen und muss weniger Bearbeitungsstunden bei Zulieferern zukaufen.
Das Blechlager, das im April 2013 in Betrieb gegangen ist, besteht aus 18 zweireihig angeordneten Regalblöcken. Es ist acht Meter hoch und etwa 45 Meter lang und 5,5 Meter breit. Die Lagerfächer hat STOPA für Beladehöhen von 90, 275 und 315 Millimeter eingerichtet. Das robuste Zweimast-Regalbediengerät erreicht Geschwindigkeiten von 150 Meter in der Minute bei der Längsfahrt sowie 23 und 25 Meter beim Heben und Ziehen. Aufgrund der dynamischen (chaotischen) Lagerplatzverwaltung lassen sich die verwendeten Flachpaletten, die für Nutzlasten von bis zu 3.000 Kilogramm konzipiert sind, willkürlich auf die freien Plätze im Regalblock einlagern. 300 der eingesetzten Paletten sind für das Groß-, Mittel- und Kleinformat ausgelegt, 15 für das Maxi-, Groß- und Mittelformat. Die Anzahl der Lagerplätze beträgt 558, davon sind 24 für das Maxiformat vorgesehen.
Johan Vermote steigt die Treppe zu der 44 x 13 Meter großen, aus Beton hergestellten Ebene hinauf, die in der zweiten Ebene vor dem STOPA COMPACT eingezogen worden ist. »Die Anbindung der vier neuen Laserschneidanlagen auf dieser erhöhten Ebene ist eine Besonderheit. Wir benötigen die Ebene, weil der vorhandene Raum knapp ist und wir hier vier Maschinen installieren mussten.« Jede der Anlagen ist durch eine automatische Handlingeinrichtung Lift- Master Store unmittelbar an das Lager angebunden. Somit erübrigt es sich sogar, die Tafeln auf Transportwagen aus dem System herauszufahren. Von den Maschinen werden die verbleibenden Rohbleche sowie Halbfabrikate und Fertigteile in das STOPA COMPACT zurückgelagert.
Die gelaserten Komponenten lagert das System über zwei Stationen in den Bereich von drei neuen Abkantpressen aus, die unterhalb der zweiten Ebene montiert sind. Mitarbeiter nehmen die Teile von den Flachpaletten, die auf Scherenhubtischen liegen, und legen sie auf Trolleys oder in Kästen. Restbleche werfen sie in Container. An diesen Abkantpressen kann der Betreiber, wie auch an den Laserschneidanlagen, kleinere Losgrößen günstiger herstellen, da er mehr inhouse produziert. Infolgedessen sinken die Bestände an Halbfertigteilen und die damit verbundene Kapitalbindung.
Komponenten, die nicht für die Abkantpressen bestimmt sind, transportiert CNH Industrial Belgium zum Tiefdrücken oder Tiefziehen. Fertigteile gehen zu 70 Prozent in die Schweißerei, 20 Prozent entfallen auf Zulieferungen für andere Werke und der Rest läuft über die Lackierung oder direkt in die Montage.
Die Systemsteuerung – bestehend aus einem Industrie-PC mit integrierter Realtime-Soft-SPS, der in ein ergonomisches Bedienpult eingebaut ist – kommuniziert via Schnittstelle mit dem TRUMPF TruTops Fab Module Storage. Diese Software steuert den gesamten Materialfluss der Produktion und verwaltet alle Lagerbestände. Die Schneidaufträge, Schachtelungen und Programme werden aus der Arbeitsvorbereitung mit sämtlichen Informationen, wie Blechdicke und Material, via Intranet an die Laserschneidanlagen übertragen. Die Maschinen fordern die Tafeln daraufhin aus dem Lager an und arbeiten die Aufträge ab, während die Bediener hauptzeitparallel die nächsten vorbereiten. Außerdem kann das Regalbediengerät, basierend auf den Auftragsdaten, Paletten mit den benötigten Blechen vorausschauend und somit zeitsparend vorab in die Nähe der betreffenden Maschinen umlagern.
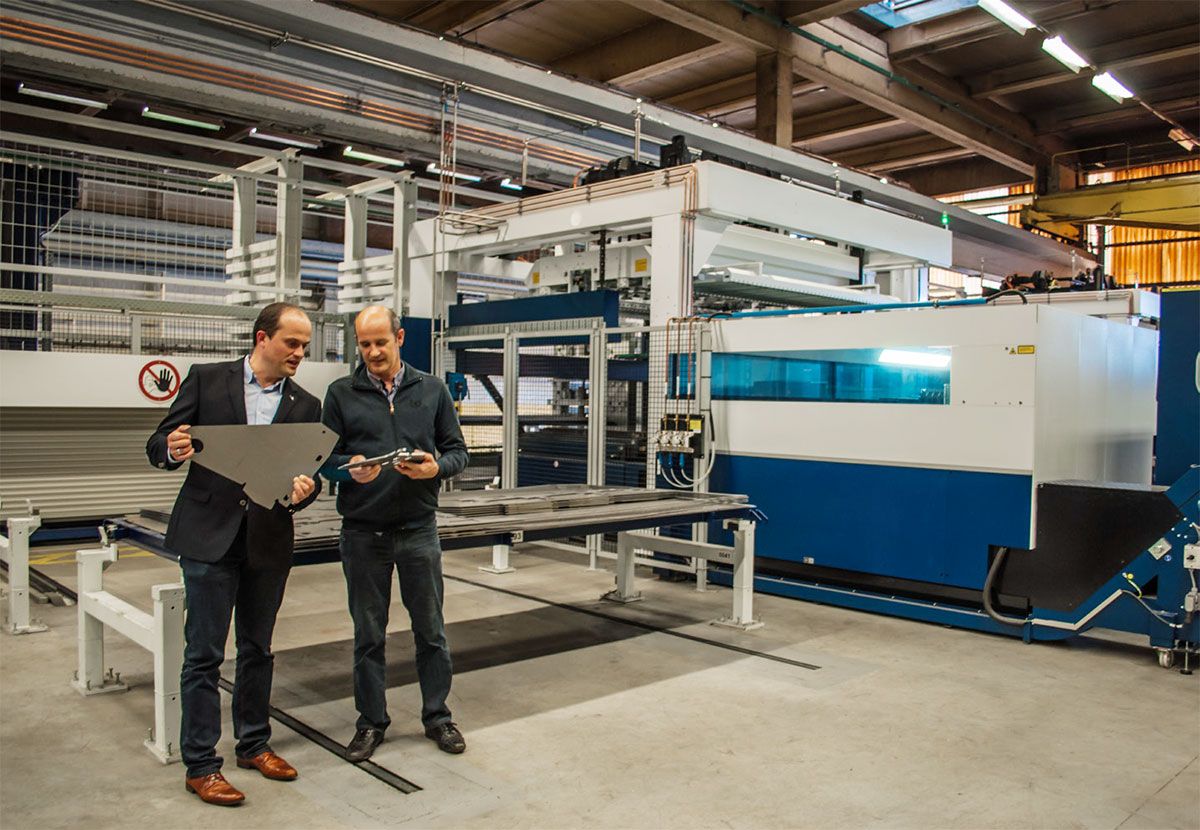
Koen Mergaert, Verantwortlicher Arbeitsvorbereitung, Blechbearbeitung und Dreherei (rechts), sowie Johan Vermote, Arbeitsvorbereitung Blechbearbeitung bei CNH Industrial Belgium.
Autor: Jürgen Warmbol
Vertrieb Ansprechpartner
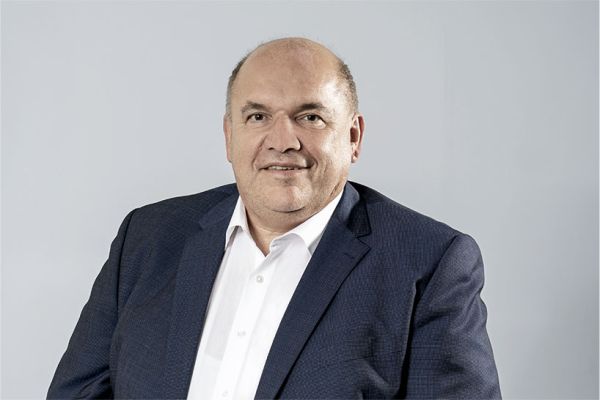
Holger Dehmelt
STOPA Anlagenbau GmbH
Industriestr. 12
77855 Achern-Gamshurst
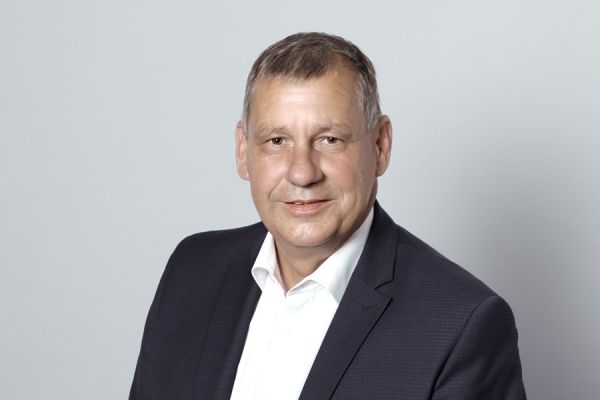
Rolf Eckhardt
STOPA Anlagenbau GmbH
Industriestr. 12
77855 Achern-Gamshurst
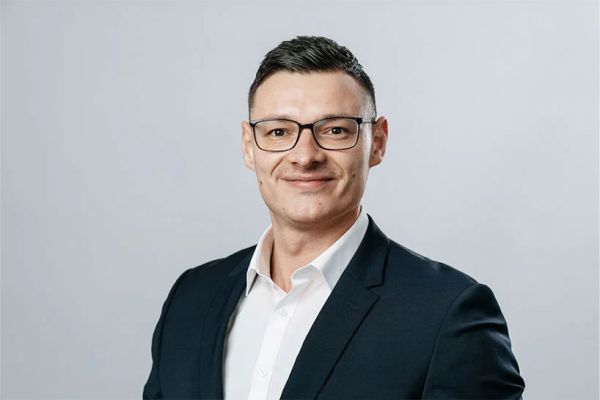
Andreas Pahl
STOPA Anlagenbau GmbH
Industriestr. 12
77855 Achern-Gamshurst